- お役立ち記事
- Practical example of multiple procurement in the manufacturing industry promoted by the purchasing department
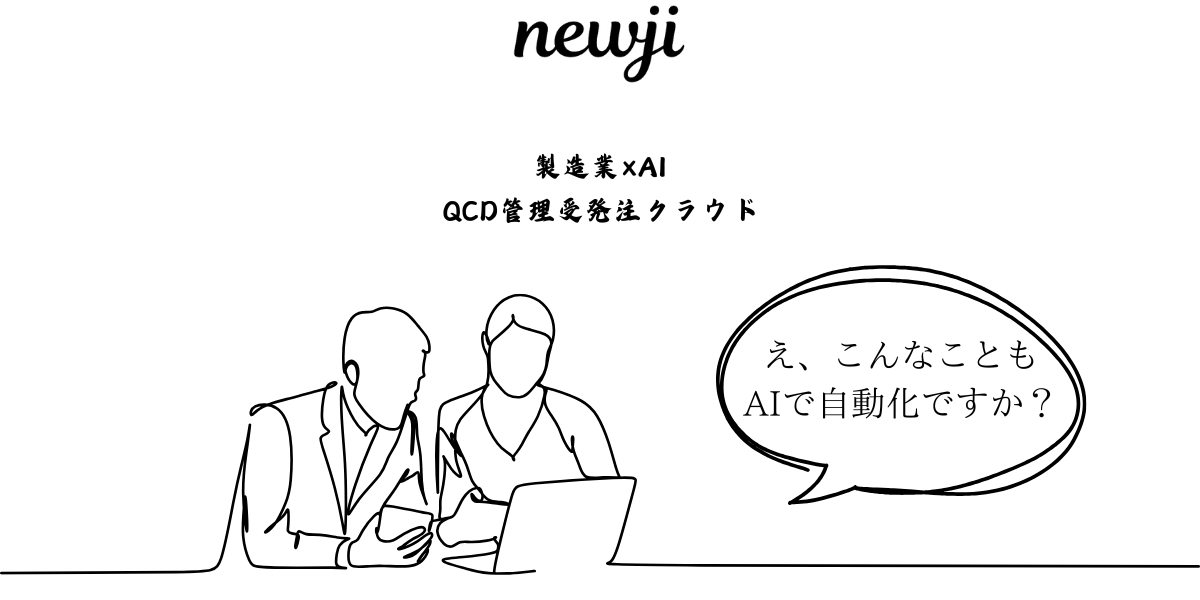
Practical example of multiple procurement in the manufacturing industry promoted by the purchasing department
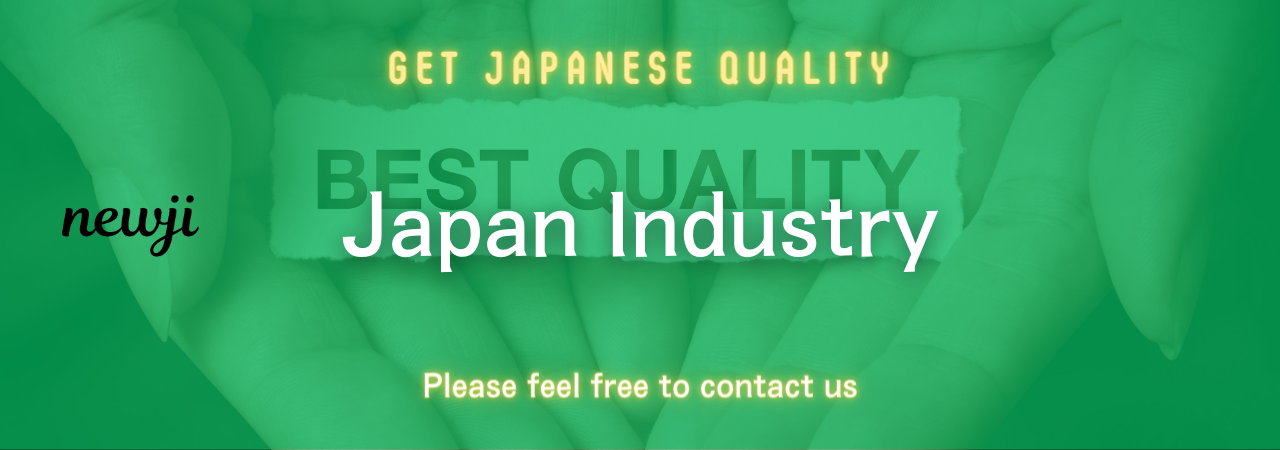
目次
Understanding Multiple Procurement in Manufacturing
In today’s dynamic manufacturing industry, the concept of multiple procurement is gaining traction.
The purchasing department plays a pivotal role in implementing this strategy to ensure efficiency, cost-effectiveness, and agility in the production process.
But what exactly is multiple procurement, and why is it so important?
What is Multiple Procurement?
Multiple procurement, also known as multi-sourcing, involves sourcing the same type of product or raw material from multiple suppliers instead of relying solely on a single supplier.
This approach diversifies the supply chain and mitigates risks associated with supply disruptions.
By having multiple suppliers, companies can maintain continuity in production even if one supplier faces issues.
Benefits of Multiple Procurement
There are several benefits to adopting a multiple procurement strategy in the manufacturing industry:
1. **Risk Mitigation:** By diversifying the supplier base, manufacturing companies can reduce the risk of supply chain disruptions due to unforeseen events like natural disasters or political instabilities affecting a single supplier.
2. **Cost Efficiency:** Competition among suppliers can drive down material costs.
By evaluating quotes and negotiating terms with different vendors, companies can secure better pricing and terms.
3. **Quality Assurance:** With multiple suppliers, companies can ensure a consistent supply of materials that meet their quality standards.
If one supplier fails to deliver quality products, other suppliers can fill the gap.
4. **Flexibility and Scalability:** Multiple procurement allows for greater flexibility in scaling production up or down.
Manufacturers can adjust supplies based on demand without being constrained by the capacity of a single supplier.
5. **Innovation and Development:** Working with several suppliers can expose companies to innovative practices and new technologies, fostering product development and improvement.
Implementing Multiple Procurement
For the purchasing department to successfully implement a multiple procurement strategy, certain steps and considerations are crucial.
Supplier Selection and Evaluation
The first step is selecting suitable suppliers.
This involves evaluating potential suppliers based on a criteria matrix that includes cost, quality, reliability, and capacity.
Regular audits and assessments help in ensuring that supplier standards align with company requirements.
Building Strong Supplier Relationships
Once suppliers are selected, nurturing strong relationships is essential.
Effective communication, good negotiations, and mutual understanding bolster trust and cooperation.
It leads to better coordination and problem-solving when challenges arise.
Forecasting and Demand Planning
Successful multiple procurement relies on accurate forecasting and demand planning.
Purchasing departments must analyze market trends, customer demands, and production schedules to adjust procurement activities accordingly.
This proactive approach minimizes waste and maximizes cost-efficiency.
Technology and Data Analytics
Leveraging technology and data analytics is vital.
Implementing procurement management software can streamline processes, track order histories, and analyze supplier performance.
Data-driven insights support decision-making and enable continuous improvement.
Case Study: A Practical Example
To better understand how multiple procurement works in practice, consider the case of a mid-sized automotive parts manufacturer.
Due to increasing demand, the company experienced a bottleneck in production, stemming from their sole reliance on a single supplier for a critical component.
The purchasing department initiated a multiple procurement strategy, reaching out to several potential suppliers.
After a rigorous evaluation, three new suppliers were brought on board.
This diversification resulted not only in a more stable supply chain but also in a 10% reduction in component costs due to competitive pricing.
Moreover, when one supplier faced a temporary shutdown, the other suppliers mitigated the impact, ensuring uninterrupted production.
Challenges and Considerations
Although multiple procurement presents numerous advantages, it does come with challenges.
Complex Supplier Management
Managing multiple suppliers can become complex and resource-intensive.
It requires well-designed systems and processes to effectively coordinate deliveries, quality checks, and payments.
Potential for Increased Costs
While cost savings are a potential benefit, there are instances where multiple procurement can lead to increased overhead costs due to smaller batch orders from individual suppliers and higher logistical costs.
Balancing Supply and Demand
Maintaining the right balance between supply and demand can be tricky.
Overestimating needs may lead to excess inventory, while underestimating can cause stockouts.
Conclusion
In conclusion, multiple procurement is a potent strategy for the manufacturing industry, offering risk mitigation, cost efficiency, and enhanced quality assurance.
When executed effectively, it can provide a competitive edge in today’s fast-paced market.
However, it demands careful planning, continuous monitoring, and effective supplier relationship management.
As the industry continues to evolve, the purchasing department’s ability to adapt and optimize procurement strategies will be crucial for maintaining business success.
資料ダウンロード
QCD調達購買管理クラウド「newji」は、調達購買部門で必要なQCD管理全てを備えた、現場特化型兼クラウド型の今世紀最高の購買管理システムとなります。
ユーザー登録
調達購買業務の効率化だけでなく、システムを導入することで、コスト削減や製品・資材のステータス可視化のほか、属人化していた購買情報の共有化による内部不正防止や統制にも役立ちます。
NEWJI DX
製造業に特化したデジタルトランスフォーメーション(DX)の実現を目指す請負開発型のコンサルティングサービスです。AI、iPaaS、および先端の技術を駆使して、製造プロセスの効率化、業務効率化、チームワーク強化、コスト削減、品質向上を実現します。このサービスは、製造業の課題を深く理解し、それに対する最適なデジタルソリューションを提供することで、企業が持続的な成長とイノベーションを達成できるようサポートします。
オンライン講座
製造業、主に購買・調達部門にお勤めの方々に向けた情報を配信しております。
新任の方やベテランの方、管理職を対象とした幅広いコンテンツをご用意しております。
お問い合わせ
コストダウンが利益に直結する術だと理解していても、なかなか前に進めることができない状況。そんな時は、newjiのコストダウン自動化機能で大きく利益貢献しよう!
(Β版非公開)