- お役立ち記事
- Practical example of resolving labor shortages using IoT devices in factories
月間76,176名の
製造業ご担当者様が閲覧しています*
*2025年3月31日現在のGoogle Analyticsのデータより
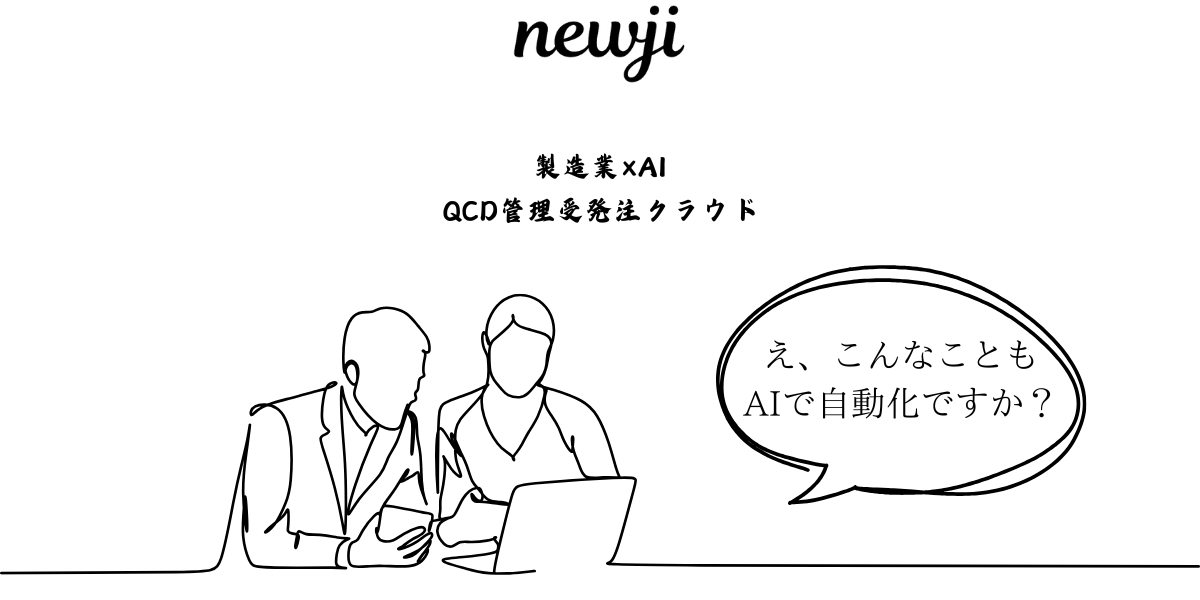
Practical example of resolving labor shortages using IoT devices in factories
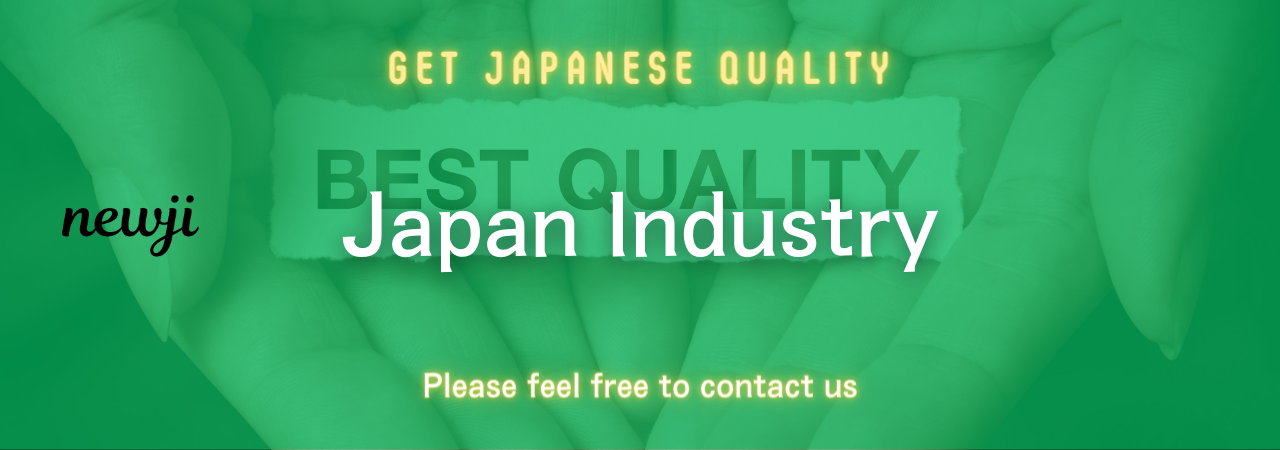
目次
Understanding the Labor Shortage in Factories
Labor shortages have become a significant issue for many industries worldwide, including manufacturing.
Factors such as an aging workforce, declining birth rates in certain regions, and the increasing complexity of modern manufacturing processes have contributed to this shortage.
Additionally, younger generations may prefer pursuing careers in other sectors, further exacerbating the issue.
As a result, manufacturers are facing challenges in maintaining operational efficiency and productivity.
To address these challenges, factories are turning to technology, specifically Internet of Things (IoT) devices, as a viable solution to fill the gaps left by workforce shortages.
IoT Devices: A Solution to Labor Shortages
IoT devices are revolutionizing the way factories operate by providing innovative solutions to labor shortages.
These devices can automate tasks, monitor equipment and processes, and provide valuable data insights that enhance decision-making.
By integrating IoT technology into their operations, factories can optimize their workforce and improve overall efficiency.
Automating Tasks
One of the most practical applications of IoT devices in factories is the automation of routine and repetitive tasks.
Robots and automated systems can be employed to handle tasks such as assembly line work, packaging, and quality control.
These systems are equipped with sensors and IoT connectivity, allowing them to work alongside human workers or independently, depending on the complexity of the task.
By automating these tasks, factories can reduce the need for a large workforce, enabling them to operate efficiently despite labor shortages.
Monitoring Equipment and Processes
IoT devices are also instrumental in monitoring equipment and processes within a factory.
Sensors can be installed on machinery to track performance metrics such as temperature, vibration, and energy consumption.
These devices provide real-time data that can be used to predict when maintenance is needed, reducing downtime and avoiding costly repairs.
By ensuring that machines are operating efficiently, factories can maximize output with fewer human resources.
Data-Driven Decision Making
With the vast amounts of data generated by IoT devices, factories can harness this information to make informed decisions.
Advanced analytics tools can be used to interpret data, identify trends, and optimize processes.
For instance, IoT data can help detect bottlenecks in production lines or forecast future labor needs.
By leveraging data insights, factory managers can allocate resources more effectively and adapt to changes in demand, mitigating the impact of labor shortages.
Case Studies: Successful Implementation of IoT in Factories
Several factories have successfully implemented IoT solutions to address labor shortages, demonstrating the practical benefits of this technology.
Case Study 1: Automotive Manufacturing
An automotive manufacturer in Europe faced a severe labor shortage due to an aging workforce and high employee turnover.
The company implemented IoT technologies to automate various production processes, such as welding and painting.
By using collaborative robots, commonly known as cobots, they were able to maintain high efficiency on the assembly line.
The IoT implementation also included predictive maintenance systems that reduced equipment downtime.
As a result, the company saw a 30% increase in productivity and a significant reduction in labor costs.
Case Study 2: Food Processing Industry
A food processing factory in the United States struggled to find sufficient workers for its packaging and sorting departments.
The factory adopted IoT-enabled sorting machines equipped with advanced sensors and cameras.
These machines could quickly and accurately sort products by size, color, and quality, tasks previously done by human workers.
The transition to IoT technology allowed the factory to maintain production levels with a smaller workforce, effectively addressing the labor shortage.
Case Study 3: Electronics Manufacturing
An Asian electronics manufacturer faced challenges in hiring skilled technicians for quality control inspections.
The company turned to IoT-based inspection systems that use artificial intelligence and machine learning algorithms to detect defects in electronic components.
These systems provided real-time feedback and reduced the reliance on human inspectors.
The implementation resulted in improved inspection accuracy and a faster production line, solving the labor shortage problem.
Challenges and Considerations
Despite the benefits, implementing IoT solutions in factories comes with its own set of challenges.
Cost
The initial investment required to install IoT devices and infrastructure can be significant.
Factories need to consider the cost of purchasing, installing, and maintaining these technologies.
However, the long-term savings from increased efficiency and reduced labor costs can justify the initial expenditure.
Training and Integration
Integrating IoT technologies into existing factory processes may require additional training for employees.
Workers need to be familiar with the new systems and how to interact with them effectively.
Providing adequate training ensures a smooth transition and maximizes the benefits of the IoT investment.
Data Security
With the increased connectivity of IoT devices, data security becomes a critical concern.
Factories must implement robust cybersecurity measures to protect sensitive data and prevent unauthorized access.
Ensuring data privacy and security is essential for maintaining trust with customers and stakeholders.
Conclusion
IoT devices offer practical solutions for factories facing labor shortages.
Through automation, real-time monitoring, and data-driven insights, IoT technology can optimize operations and enhance productivity.
While there are challenges to consider, the successful implementation of IoT in various industries demonstrates its potential to transform manufacturing processes.
As technology continues to evolve, factories that embrace IoT solutions will be better equipped to navigate labor shortages and remain competitive in the global market.
資料ダウンロード
QCD管理受発注クラウド「newji」は、受発注部門で必要なQCD管理全てを備えた、現場特化型兼クラウド型の今世紀最高の受発注管理システムとなります。
ユーザー登録
受発注業務の効率化だけでなく、システムを導入することで、コスト削減や製品・資材のステータス可視化のほか、属人化していた受発注情報の共有化による内部不正防止や統制にも役立ちます。
NEWJI DX
製造業に特化したデジタルトランスフォーメーション(DX)の実現を目指す請負開発型のコンサルティングサービスです。AI、iPaaS、および先端の技術を駆使して、製造プロセスの効率化、業務効率化、チームワーク強化、コスト削減、品質向上を実現します。このサービスは、製造業の課題を深く理解し、それに対する最適なデジタルソリューションを提供することで、企業が持続的な成長とイノベーションを達成できるようサポートします。
製造業ニュース解説
製造業、主に購買・調達部門にお勤めの方々に向けた情報を配信しております。
新任の方やベテランの方、管理職を対象とした幅広いコンテンツをご用意しております。
お問い合わせ
コストダウンが利益に直結する術だと理解していても、なかなか前に進めることができない状況。そんな時は、newjiのコストダウン自動化機能で大きく利益貢献しよう!
(β版非公開)