- お役立ち記事
- Practical examples and results of lead time reduction proposed by the purchasing department
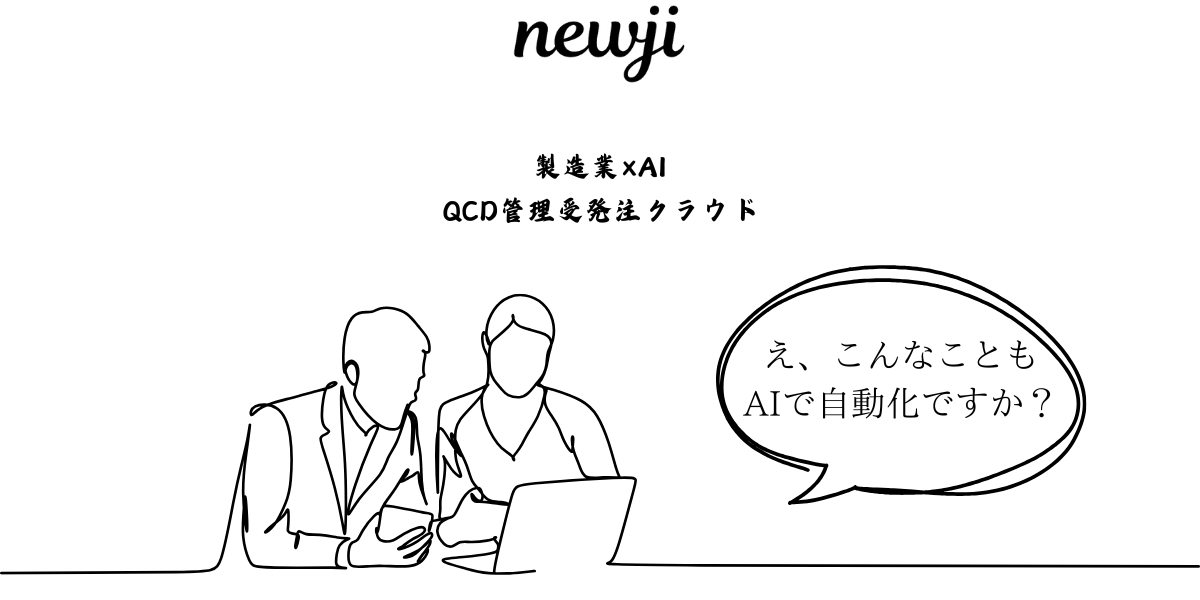
Practical examples and results of lead time reduction proposed by the purchasing department
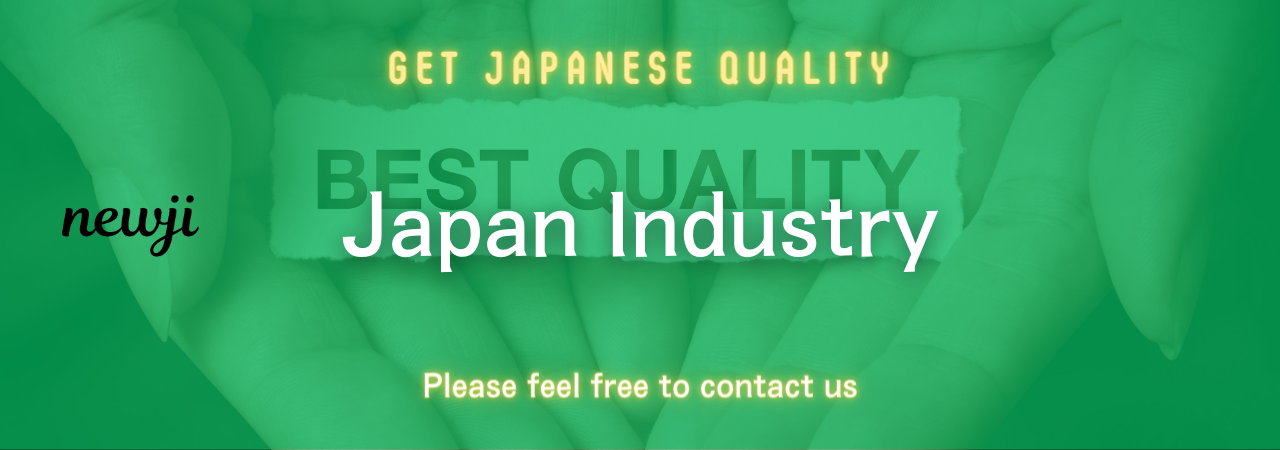
目次
Understanding Lead Time Reduction
Lead time refers to the amount of time it takes for a process, from initiation to completion, in a supply chain.
In the context of a purchasing department, lead time covers the period from ordering materials to receiving them and making them available for manufacturing or other activities.
Reducing lead time can significantly improve operational efficiency, decrease costs, and enhance customer satisfaction by speeding up delivery times.
Purchasing departments play a crucial role in reducing lead times, as they can influence the entire supply chain process.
By optimizing procurement strategies, they ensure that materials and products are ordered, processed, and delivered in a timely manner.
Through innovative strategies, purchasing teams can help businesses operate more smoothly and responsibly.
Strategies for Reducing Lead Time
Several practical strategies can be implemented by purchasing departments to reduce lead times effectively.
1. Supplier Relationship Management
Building strong relationships with suppliers is a key factor in reducing lead time.
Good communication and trust can lead to quicker responses from suppliers and better negotiation opportunities for urgent orders.
Additionally, collaborating closely with suppliers can help anticipate potential delays and address them proactively.
2. Implementing Just-In-Time (JIT) Inventory
Just-In-Time (JIT) inventory is a strategy where materials are ordered and received on an as-needed basis rather than stockpiling them.
This approach can significantly reduce the time materials spend in storage, thus decreasing the overall lead time.
Purchasing departments managing JIT must ensure reliable supplier performance and an efficient, streamlined ordering process.
3. Electronic Data Interchange (EDI)
The use of Electronic Data Interchange (EDI) can help reduce lead time by automating the purchasing process.
This system facilitates real-time communication between buyers and suppliers, allowing for quick order processing and minimization of human errors associated with manual entry.
EDI can reduce paperwork, accelerate information exchange, and ultimately shorten lead times.
4. Strategic Sourcing
By focusing on strategic sourcing, purchasing departments identify suppliers who provide the best combination of cost, quality, and reliability.
Strategic sourcing involves evaluating suppliers beyond just price, considering factors such as lead time, service quality, and flexibility.
This approach ensures that the chosen suppliers can meet all the company’s needs efficiently.
5. Demand Forecasting
Accurate demand forecasting is vital in reducing lead time.
It involves predicting future customer demand to pre-emptively order and stock materials.
By having a clear picture of future needs, purchasing departments can minimize the waiting time between realizing a need for a product and actually receiving it.
Advanced forecasting tools can help create more accurate predictions and better inventory management.
6. Standardizing Components
Standardizing components or materials is an efficient way to reduce lead times.
This involves using common parts and materials across different products, reducing variation and complexity.
Standardized components simplify the purchasing process, allow bulk ordering, and decrease supplier lead times, contributing to faster production cycles.
Results of Lead Time Reduction
The successful implementation of lead time reduction strategies can lead to significant positive outcomes for businesses.
1. Improved Customer Satisfaction
With reduced lead time, businesses can deliver products to customers more quickly and reliably.
Customers value prompt service, and faster delivery can set a company apart from its competitors, enhancing customer satisfaction and loyalty.
2. Increased Operational Efficiency
Lead time reduction can streamline production processes, eliminate bottlenecks, and improve overall operational efficiency.
This leads to better use of resources, less waste, and the ability to respond quickly to market changes.
3. Cost Savings
Reducing lead time often results in cost savings.
Companies can reduce inventory-carrying costs by holding less stock and minimizing obsolescence.
Additionally, efficient processes reduce the necessity for overtime and can decrease labor costs.
4. Enhanced Flexibility
With shorter lead times, businesses gain greater flexibility to adapt to changes in market demand and customer preferences.
They can quickly adjust their production schedules, launch new products, or modify existing ones based on market trends.
5. Strengthened Supplier Relationships
Maintaining clear communication and cooperation with suppliers, a focus in lead time reduction, leads to solid relationships.
Reliable partnerships can provide quicker responses, improve service levels, and offer support during peak demand periods.
Conclusion
The purchasing department’s role in reducing lead times cannot be underestimated.
By adopting strategies such as enhancing supplier relationships, implementing JIT inventory systems, and leveraging technology, companies can achieve significant results.
Improved efficiency, customer satisfaction, cost savings, and increased market responsiveness are among the many rewards.
Lead time reduction should be a strategic goal for organizations aiming to enhance their competitive edge in today’s fast-paced business environment.
By continuing to explore and invest in best practices, companies can ensure their supply chains are more efficient and effective, ready to meet the challenges of an ever-changing market landscape.
資料ダウンロード
QCD調達購買管理クラウド「newji」は、調達購買部門で必要なQCD管理全てを備えた、現場特化型兼クラウド型の今世紀最高の購買管理システムとなります。
ユーザー登録
調達購買業務の効率化だけでなく、システムを導入することで、コスト削減や製品・資材のステータス可視化のほか、属人化していた購買情報の共有化による内部不正防止や統制にも役立ちます。
NEWJI DX
製造業に特化したデジタルトランスフォーメーション(DX)の実現を目指す請負開発型のコンサルティングサービスです。AI、iPaaS、および先端の技術を駆使して、製造プロセスの効率化、業務効率化、チームワーク強化、コスト削減、品質向上を実現します。このサービスは、製造業の課題を深く理解し、それに対する最適なデジタルソリューションを提供することで、企業が持続的な成長とイノベーションを達成できるようサポートします。
オンライン講座
製造業、主に購買・調達部門にお勤めの方々に向けた情報を配信しております。
新任の方やベテランの方、管理職を対象とした幅広いコンテンツをご用意しております。
お問い合わせ
コストダウンが利益に直結する術だと理解していても、なかなか前に進めることができない状況。そんな時は、newjiのコストダウン自動化機能で大きく利益貢献しよう!
(Β版非公開)