- お役立ち記事
- Practical examples for the purchasing department to minimize procurement risks
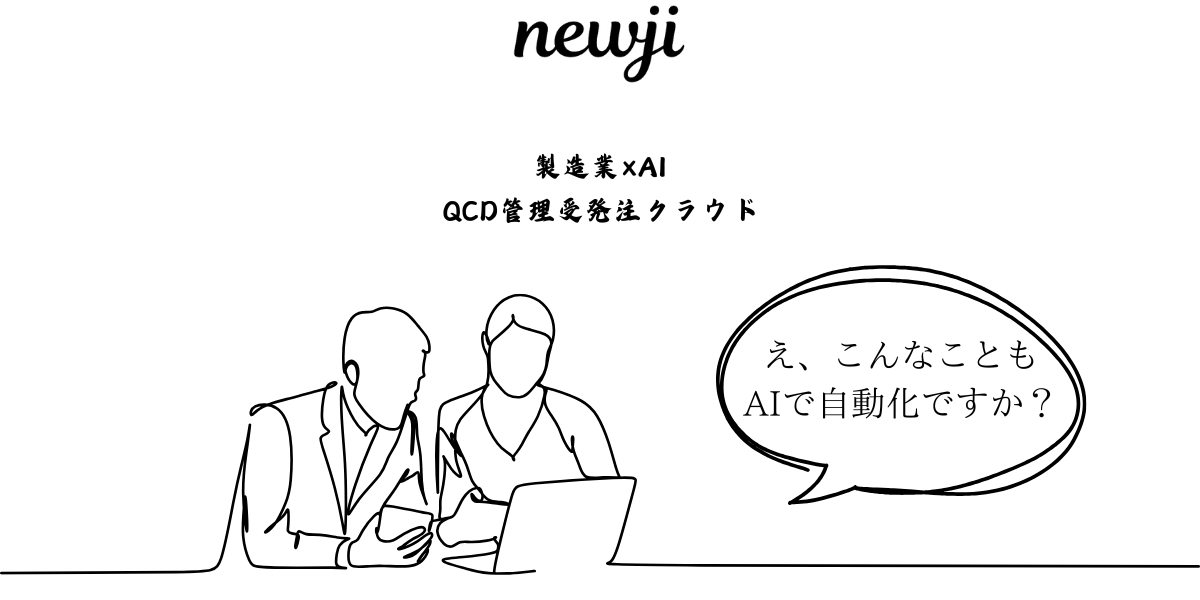
Practical examples for the purchasing department to minimize procurement risks
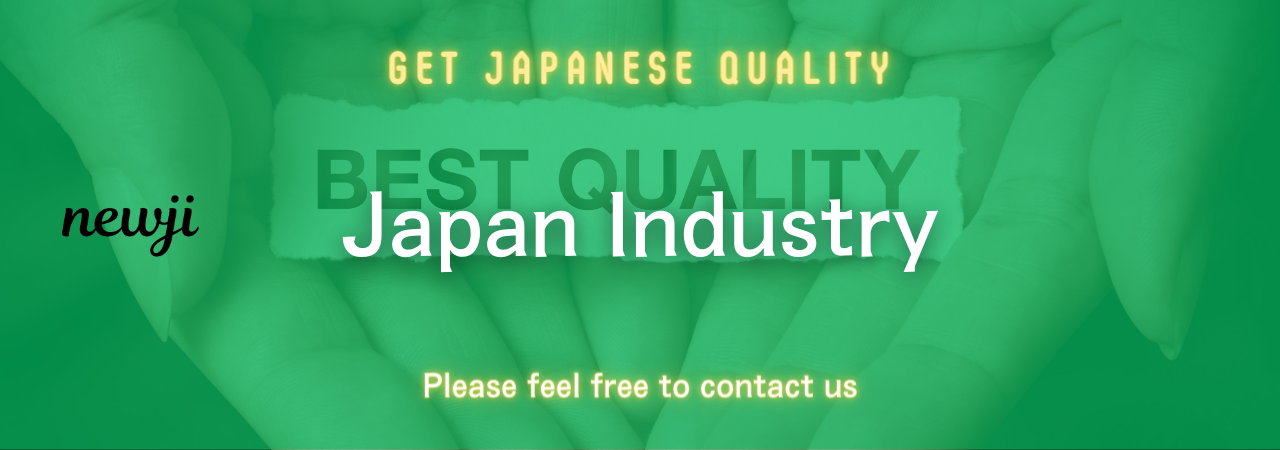
目次
Understanding Procurement Risks
Procurement is a crucial function for any organization as it involves acquiring goods, services, or works from external sources.
However, this process often comes with its own set of challenges and risks.
These risks can impact the cost, quality, and delivery of procured items and services, potentially leading to business disruptions.
Procurement risks can arise from various sources, such as market volatility, supplier reliability, legal issues, and natural disasters.
It’s essential for the purchasing department to identify these risks and devise strategies to minimize them.
By doing so, businesses can ensure a smooth procurement process, ultimately saving time and resources.
Identifying Potential Risks
Before tackling procurement risks, the purchasing department must first identify them.
Common risks include supply chain disruptions, price fluctuations, quality issues, and compliance problems.
To effectively pinpoint these risks, companies can conduct thorough market research and analyze historical data.
Regularly communicating with suppliers also provides valuable insights into potential challenges.
Supply chain disruptions can occur due to natural disasters, political instability, or supplier bankruptcy.
Price fluctuations are often influenced by changes in market demand, raw material costs, or currency variations.
Quality issues may arise if suppliers fail to meet the agreed-upon standards.
Lastly, compliance problems can result from not adhering to industry regulations or contract terms.
Strategies to Mitigate Procurement Risks
Once potential risks are identified, the next step is to devise strategies to mitigate them.
Here are some practical examples that purchasing departments can implement to minimize procurement risks effectively:
1. Diversifying Suppliers
Relying on a single supplier can be risky, especially if they face disruptions.
To minimize this risk, businesses can diversify their supplier base by working with multiple vendors.
This strategy ensures that if one supplier fails, others can fill the gap, reducing the risk of supply chain interruptions.
2. Building Strong Supplier Relationships
Strong relationships with suppliers can significantly mitigate procurement risks.
By fostering open communication and collaboration, companies can quickly address potential issues.
Regular meetings and performance reviews with suppliers help maintain transparency and ensure all parties meet their obligations.
3. Implementing Vendor Management Systems
Vendor management systems (VMS) are powerful tools that help streamline the procurement process.
These systems track supplier performance, manage contracts, and provide analytics for informed decision-making.
By using a VMS, purchasing departments can monitor potential risks and develop appropriate strategies to address them.
4. Negotiating Flexible Contracts
Flexible contracts offer protection against unforeseen circumstances, such as market fluctuations or supply chain disruptions.
By including clauses for renegotiation, businesses can adapt to changing conditions without suffering significant losses.
This flexibility also allows companies to switch suppliers if necessary without facing legal challenges.
5. Conducting Risk Assessments
Regular risk assessments help the purchasing department stay ahead of potential issues.
By evaluating supplier performance, market conditions, and internal processes, companies can identify emerging risks and develop proactive measures to mitigate them.
This approach ensures that procurement risks are continuously monitored and managed.
6. Insuring Against Risks
Insurance is another effective tool for mitigating procurement risks.
Policies can cover various risks, such as property damage, liability, or business interruptions.
By insuring against these risks, companies can minimize financial losses and safeguard their operations.
7. Establishing Contingency Plans
Contingency plans are essential for dealing with unexpected events that may disrupt the procurement process.
These plans outline alternative strategies and actions to take in response to specific risks.
By having contingency plans in place, companies can quickly adapt to changing conditions and minimize disruptions.
Ensuring Sustainable Procurement Practices
Mitigating procurement risks goes hand in hand with sustainable procurement practices.
By focusing on sustainability, companies can not only minimize risks but also promote environmental and social responsibility.
1. Evaluating Supplier Sustainability
When selecting suppliers, businesses should evaluate their sustainability practices.
Employing eco-friendly and socially responsible vendors reduces the risk of non-compliance with environmental regulations.
It also ensures that sourced products or services align with the company’s values and goals.
2. Promoting Ethical Sourcing
Ethical sourcing involves prioritizing suppliers that adhere to fair labor practices and uphold human rights.
By engaging with suppliers committed to ethical sourcing, companies can minimize legal and reputational risks while promoting a positive brand image.
3. Reducing Waste and Emissions
Minimizing waste and emissions is essential for sustainable procurement.
Companies can work with suppliers to develop eco-friendly packaging, reduce waste throughout the supply chain, and track emissions levels.
This effort not only reduces risks but also supports sustainability objectives.
Conclusion
To minimize procurement risks effectively, purchasing departments must adopt a proactive and strategic approach.
By identifying potential risks, implementing practical strategies, and embracing sustainable practices, companies can significantly mitigate procurement risks.
This ensures that the procurement process remains smooth, efficient, and aligned with organizational goals.
資料ダウンロード
QCD調達購買管理クラウド「newji」は、調達購買部門で必要なQCD管理全てを備えた、現場特化型兼クラウド型の今世紀最高の購買管理システムとなります。
ユーザー登録
調達購買業務の効率化だけでなく、システムを導入することで、コスト削減や製品・資材のステータス可視化のほか、属人化していた購買情報の共有化による内部不正防止や統制にも役立ちます。
NEWJI DX
製造業に特化したデジタルトランスフォーメーション(DX)の実現を目指す請負開発型のコンサルティングサービスです。AI、iPaaS、および先端の技術を駆使して、製造プロセスの効率化、業務効率化、チームワーク強化、コスト削減、品質向上を実現します。このサービスは、製造業の課題を深く理解し、それに対する最適なデジタルソリューションを提供することで、企業が持続的な成長とイノベーションを達成できるようサポートします。
オンライン講座
製造業、主に購買・調達部門にお勤めの方々に向けた情報を配信しております。
新任の方やベテランの方、管理職を対象とした幅広いコンテンツをご用意しております。
お問い合わせ
コストダウンが利益に直結する術だと理解していても、なかなか前に進めることができない状況。そんな時は、newjiのコストダウン自動化機能で大きく利益貢献しよう!
(Β版非公開)