- お役立ち記事
- Practical examples of alternative procurement strategies for times of supply shortage that purchasing personnel should keep in mind
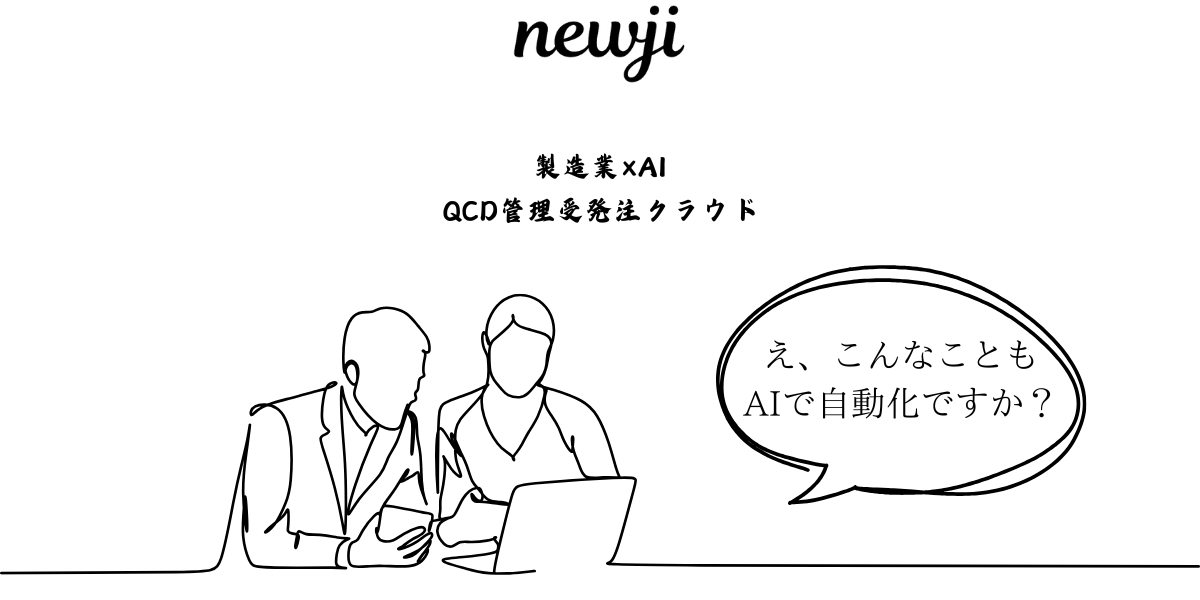
Practical examples of alternative procurement strategies for times of supply shortage that purchasing personnel should keep in mind
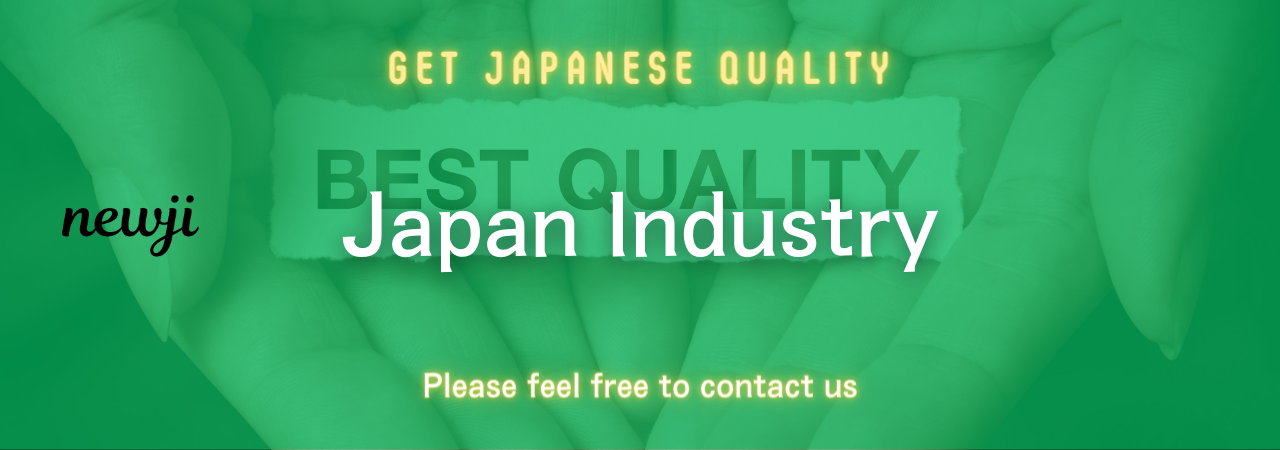
When supply shortages hit, purchasing personnel often find themselves in a bind, needing to ensure their organization continues to function smoothly.
Understanding and implementing alternative procurement strategies can be crucial during these times.
Let’s explore some practical examples that can help ease the strain of shortages and keep operations running efficiently.
目次
Diversifying Suppliers
One of the most effective strategies during supply shortages is diversifying suppliers.
Relying heavily on a single supplier can become a significant risk if that supplier cannot meet demand.
By establishing relationships with multiple vendors, businesses can pivot quickly and find alternatives when one supplier faces challenges.
Local Suppliers
Turning to local suppliers can often be a viable option as transport and logistics issues may cause delays with international suppliers.
Local vendors can sometimes provide quicker turnaround times and reduce the impact of global disruptions.
Multiple Suppliers
Choosing multiple suppliers for the same product can help mitigate risk.
This means that if one supplier defaults or faces a shortage, others can step in to fill the gap.
Maintaining relationships with several suppliers can ensure consistent supply and better negotiation leverage.
Building Strategic Partnerships
Forming strategic partnerships with key suppliers can be beneficial for both parties.
Partnerships foster cooperation and communication, encouraging suppliers to prioritize your orders during shortages.
Long-term Contracts
Entering long-term contracts with suppliers can secure stable pricing and supply.
These agreements often include clauses that prioritize your orders during shortages, ensuring you get the needed resources.
Collaborative Forecasting
Work closely with suppliers to project future demand and collaboratively plan inventory needs.
This helps suppliers prepare and allocate resources to meet your requirements, reducing the impact of sudden shortages.
Implementing Just-in-Time Inventory
Just-in-Time (JIT) inventory systems focus on reducing waste and increasing efficiency.
While traditionally used to reduce costs, JIT can be adapted to navigate supply shortages by closely aligning inventory levels with current demand.
Demand Forecasting
Accurate demand forecasting is critical in a JIT system.
Using data analytics to predict trends can help adjust procurement strategies proactively.
This timely information allows you to adjust orders and inventory levels in anticipation of shortages, reducing their impact.
Buffer Stock
While JIT minimizes excess inventory, maintaining a small buffer stock of critical items can act as a cushion during shortages.
This safety stock ensures operations continue smoothly until the regular supply resumes.
Revamping Inventory Management
Optimizing inventory management during supply shortages helps in maintaining balance.
It involves smart strategies to control stock levels and reduce dependence on external supplies.
ABC Analysis
Categorize inventory into three categories: A (high-value), B (moderate value), and C (low-value).
Focus efforts on A items to ensure their availability, as having these items in stock is vital to business operations.
By prioritizing high-value items, businesses can minimize the impact of shortages on their most critical resources.
Flexible Stock Policies
Adjust inventory policies to be more flexible in response to changing market conditions.
This could include altering reorder points, lead times, and minimum order quantities to accommodate variability in supply.
Utilizing Technology Solutions
Leveraging technology can streamline procurement processes and make them more resilient to supply chain disruptions.
AI and Machine Learning
AI and machine learning can improve demand forecasting and supply chain management by identifying patterns and predicting potential shortages before they occur.
These technologies provide insights that enable businesses to make proactive procurement decisions.
Supplier Relationship Management Software
Using software to manage supplier relationships offers a centralized platform for communication and collaboration.
It provides real-time updates on supplier status and helps identify potential issues early.
This ensures purchasing personnel can act swiftly and effectively during shortages.
Exploring Alternative Materials
Exploring alternative materials during supply shortages can maintain production and quality standards.
This approach requires flexibility and creativity in sourcing.
Research and Development (R&D)
Investing in R&D to discover alternative materials or components can be beneficial.
This allows the business to switch materials without compromising product quality or performance if original materials become scarce.
Quality Assurance
Ensure any alternative materials meet the company’s quality standards.
Working closely with quality assurance teams ensures that product integrity remains uncompromised even amidst shortages.
Conclusion
Developing a robust procurement strategy is essential for navigating supply shortages effectively.
By diversifying suppliers, building strategic partnerships, implementing JIT, optimizing inventory management, leveraging technology, and exploring alternative materials, purchasing personnel can mitigate the risks associated with supply disruptions.
These strategies ensure a steady flow of resources, keeping businesses operational and competitive even during challenging times.
資料ダウンロード
QCD調達購買管理クラウド「newji」は、調達購買部門で必要なQCD管理全てを備えた、現場特化型兼クラウド型の今世紀最高の購買管理システムとなります。
ユーザー登録
調達購買業務の効率化だけでなく、システムを導入することで、コスト削減や製品・資材のステータス可視化のほか、属人化していた購買情報の共有化による内部不正防止や統制にも役立ちます。
NEWJI DX
製造業に特化したデジタルトランスフォーメーション(DX)の実現を目指す請負開発型のコンサルティングサービスです。AI、iPaaS、および先端の技術を駆使して、製造プロセスの効率化、業務効率化、チームワーク強化、コスト削減、品質向上を実現します。このサービスは、製造業の課題を深く理解し、それに対する最適なデジタルソリューションを提供することで、企業が持続的な成長とイノベーションを達成できるようサポートします。
オンライン講座
製造業、主に購買・調達部門にお勤めの方々に向けた情報を配信しております。
新任の方やベテランの方、管理職を対象とした幅広いコンテンツをご用意しております。
お問い合わせ
コストダウンが利益に直結する術だと理解していても、なかなか前に進めることができない状況。そんな時は、newjiのコストダウン自動化機能で大きく利益貢献しよう!
(Β版非公開)