- お役立ち記事
- Practical examples of new energy-saving technologies that produce results in factory operations
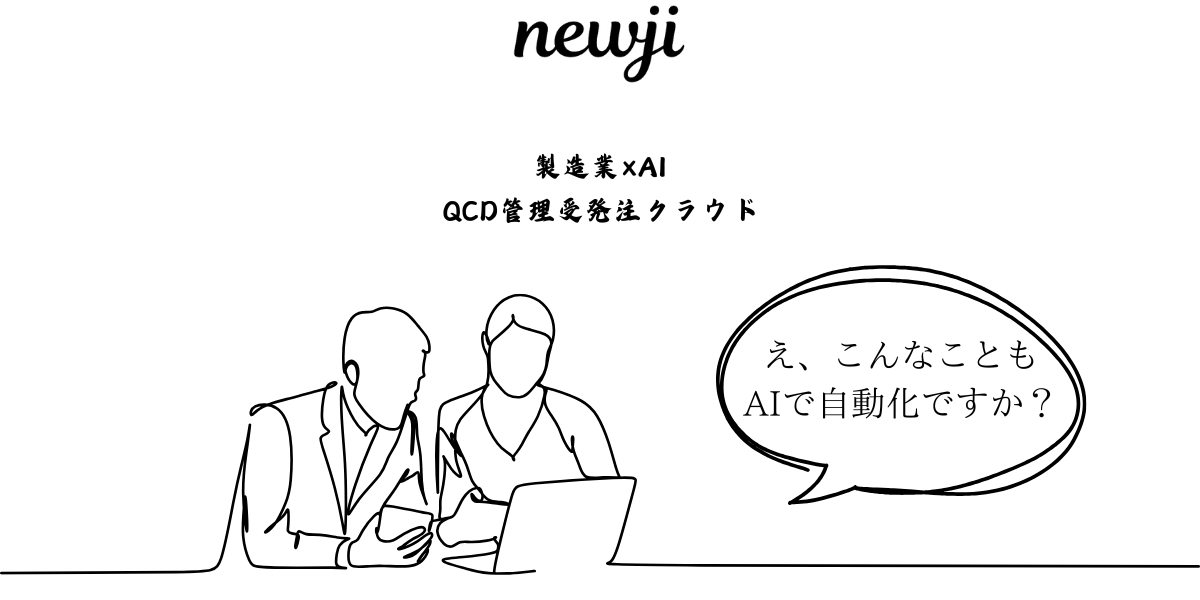
Practical examples of new energy-saving technologies that produce results in factory operations
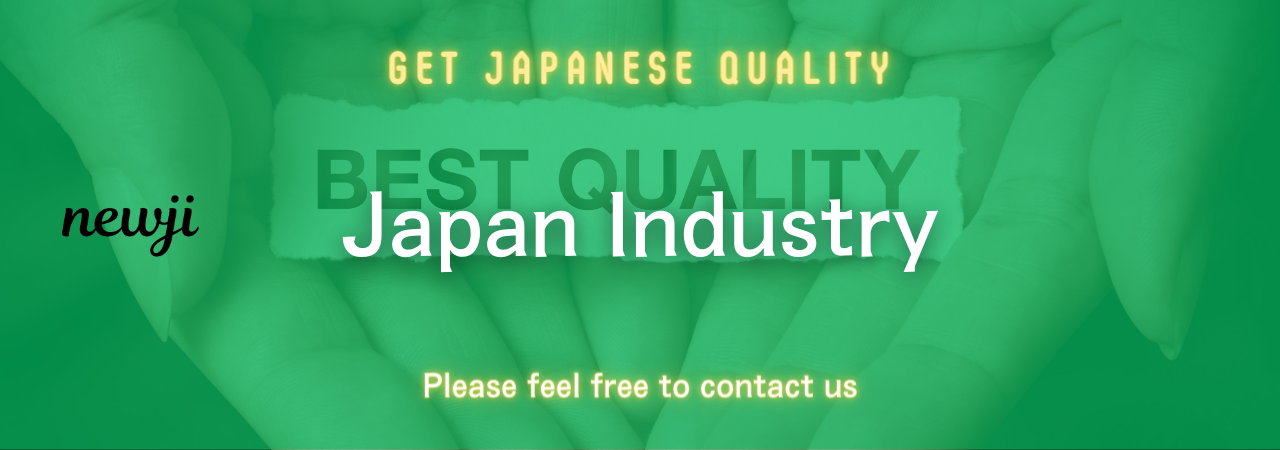
目次
Introduction to Energy-Saving Technologies in Factories
In today’s rapidly industrializing world, energy conservation has become more essential than ever.
As factories strive to optimize their operations, they are increasingly turning to cutting-edge technologies that promise to deliver significant energy savings.
By implementing these innovations, factories not only reduce their operational costs but also contribute to a healthier environment.
This article explores practical examples of new energy-saving technologies currently making waves in the manufacturing sector.
Smart Lighting Systems
One of the simplest yet most effective ways for factories to save energy is through the implementation of smart lighting systems.
Traditional lighting systems consume a considerable amount of electricity, making them an obvious target for upgrading.
Smart lighting technologies use energy-efficient LED bulbs and integrate with sensors to automatically adjust lighting based on occupancy and natural light availability.
Factories adopting these systems witness a remarkable reduction in energy consumption related to lighting, often seeing savings of up to 70%.
Energy-Efficient Heating, Ventilation, and Air Conditioning (HVAC) Systems
HVAC systems significantly contribute to a factory’s energy use.
Replacing outdated HVAC units with energy-efficient models can lead to substantial savings.
New HVAC systems incorporate advanced sensors and controls that adjust temperatures in different zones based on real-time data and usage.
Additionally, integrating smart thermostats allows for remote monitoring and adjustments, ensuring optimal operation without excessive energy use.
Furthermore, the use of geothermal heat pumps taps into the earth’s stable temperature, providing heating and cooling with minimal energy input.
Variable Frequency Drives (VFDs)
Many factory operations involve machinery that operates continuously at a fixed speed.
This often leads to energy wastage when machines run at full capacity regardless of the demand.
Variable frequency drives (VFDs) address this issue by regulating the speed and torque of electric motors, ensuring that they operate efficiently according to the specific needs at any given time.
By optimizing motor performance, VFDs can reduce energy consumption by 30% or more.
Case Study: Optimizing Motor Use
A textile manufacturing plant recently implemented VFD technology across all its motor-driven equipment.
By doing so, they not only cut their energy usage by a third but also extended the lifespan of their machinery due to reduced wear and tear.
Advanced Energy Management Systems (EMS)
Energy management systems are sophisticated software solutions that provide factories with a comprehensive view of their energy consumption.
These systems collect data from various points in the manufacturing process, analyze it, and identify areas of inefficiency.
By offering real-time insights and actionable recommendations, EMS enable factories to make informed decisions and implement energy-saving measures.
Industrial Internet of Things (IIoT)
The rise of the Industrial Internet of Things (IIoT) has radically transformed energy conservation in factories.
Through a network of interconnected devices and sensors, IIoT allows for precise monitoring and control over industrial processes.
For example, predictive maintenance powered by IIoT prevents energy wastage by ensuring equipment runs at peak efficiency.
Sensors detect anomalies and signal when maintenance is needed before a breakdown occurs, thus maintaining optimal energy usage.
IIoT in Action: Reducing Energy Costs
An electronics manufacturing facility leveraged IIoT technology to monitor its production lines.
By analyzing the data collected, the factory identified energy bottlenecks and optimized production scheduling, leading to a 20% reduction in energy costs.
Renewable Energy Integration
Incorporating renewable energy sources is a powerful way for factories to reduce their dependence on traditional energy grids and cut back on costs.
Solar photovoltaic (PV) installations and wind turbines can provide factories with clean energy to power their operations.
Furthermore, energy storage solutions such as batteries are becoming increasingly affordable and efficient, allowing factories to store excess energy generated during peak times and use it when needed.
Example of Renewable Energy Use
A food processing plant installed solar panels on its facility’s roof.
This initiative now covers more than 25% of the plant’s energy needs, showcasing not only a commitment to sustainability but also a smart financial investment.
Conclusion
The deployment of energy-saving technologies in factory operations is not just a trend but a necessity.
With the global push towards sustainability and environmental responsibility, factories have a vital role to play in reducing energy consumption and emissions.
By adopting smart lighting systems, energy-efficient HVAC, VFDs, advanced EMS, IIoT, and renewable energy solutions, factories can achieve meaningful reductions in energy use.
The cumulative impact of these technologies not only assures financial benefits but also a positive contribution to environmental conservation.
As more factories embrace these innovations, the world inches closer to a more sustainable future.
資料ダウンロード
QCD調達購買管理クラウド「newji」は、調達購買部門で必要なQCD管理全てを備えた、現場特化型兼クラウド型の今世紀最高の購買管理システムとなります。
ユーザー登録
調達購買業務の効率化だけでなく、システムを導入することで、コスト削減や製品・資材のステータス可視化のほか、属人化していた購買情報の共有化による内部不正防止や統制にも役立ちます。
NEWJI DX
製造業に特化したデジタルトランスフォーメーション(DX)の実現を目指す請負開発型のコンサルティングサービスです。AI、iPaaS、および先端の技術を駆使して、製造プロセスの効率化、業務効率化、チームワーク強化、コスト削減、品質向上を実現します。このサービスは、製造業の課題を深く理解し、それに対する最適なデジタルソリューションを提供することで、企業が持続的な成長とイノベーションを達成できるようサポートします。
オンライン講座
製造業、主に購買・調達部門にお勤めの方々に向けた情報を配信しております。
新任の方やベテランの方、管理職を対象とした幅広いコンテンツをご用意しております。
お問い合わせ
コストダウンが利益に直結する術だと理解していても、なかなか前に進めることができない状況。そんな時は、newjiのコストダウン自動化機能で大きく利益貢献しよう!
(Β版非公開)