- お役立ち記事
- Practical exercise in electronic device thermal design using thermofluid engineering and MBD
月間76,176名の
製造業ご担当者様が閲覧しています*
*2025年3月31日現在のGoogle Analyticsのデータより
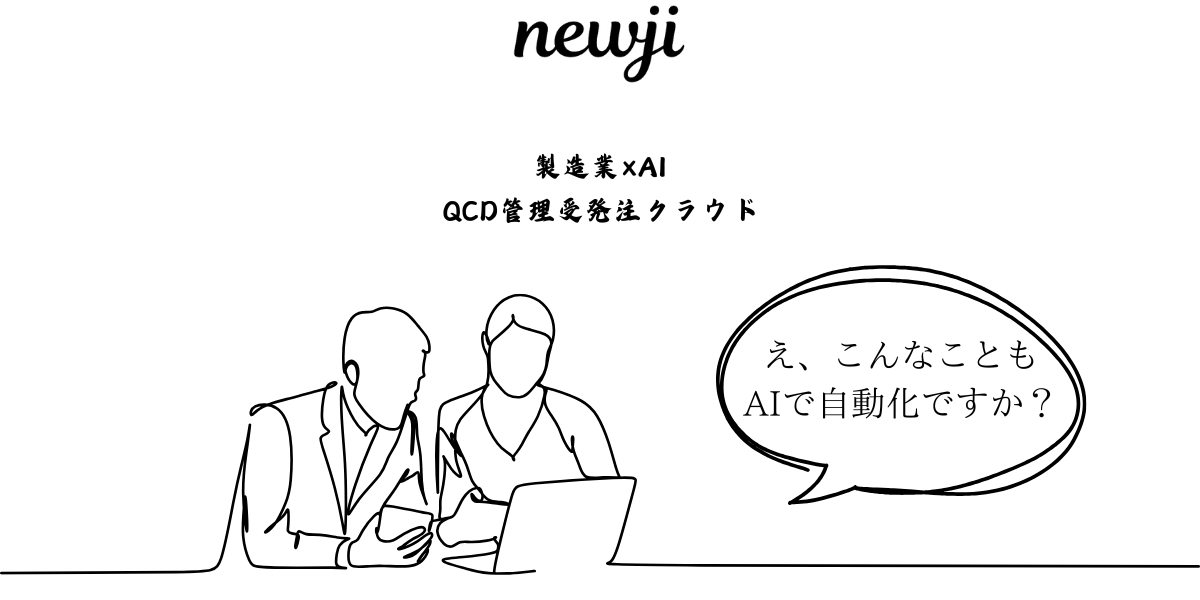
Practical exercise in electronic device thermal design using thermofluid engineering and MBD
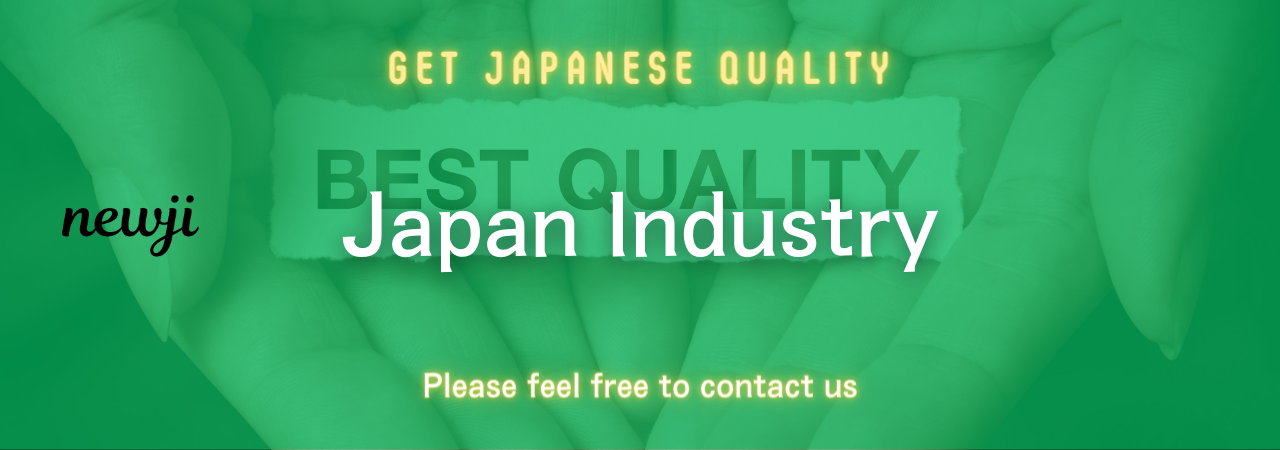
Understanding Thermal Design in Electronic Devices
In the rapidly advancing world of technology, electronic devices are becoming more powerful and compact.
This trend poses significant challenges for engineers, as these devices generate more heat while having less space to dissipate it.
Effective thermal design is crucial to ensure the operational reliability and longevity of electronic components.
The Importance of Thermal Management
Without proper thermal management, electronic devices can overheat, leading to malfunctions or permanent damage.
Overheating can degrade the performance of a device and may even pose safety risks.
Thus, engineers must implement efficient thermal solutions to manage heat production in electronic devices.
What is Thermofluid Engineering?
Thermofluid engineering is an interdisciplinary field that combines principles of thermodynamics, fluid mechanics, and heat transfer to solve complex thermal management problems.
By utilizing thermofluid engineering, engineers can design effective cooling systems that control the temperature of electronic devices.
This process involves the analysis and optimization of various cooling methods such as conduction, convection, and radiation.
Model-Based Design (MBD) in Thermal Design
Model-based design (MBD) is a sophisticated approach that uses simulations to create virtual models of electronic components and systems.
This enables engineers to predict how a device will behave under different thermal conditions.
MBD allows for the evaluation and optimization of thermal designs before physical prototypes are built.
This approach reduces time and costs in the development process and helps engineers identify potential issues early.
Practical Exercise in Thermal Design
To better understand the principles of thermal design using thermofluid engineering and MBD, let’s explore a practical exercise.
Imagine designing a cooling system for a high-performance laptop.
Step 1: Collecting Data
The first step is to identify the thermal characteristics of the laptop’s components.
This involves collecting data on the power consumption, size, and heat dissipation requirements of the processor, graphics card, and other key components.
Step 2: Simulating the Thermal Model
Using model-based design tools, create a virtual model of the laptop.
In this simulation, input the data collected in the first step and set the parameters to test different thermal scenarios.
The simulation will analyze how heat is distributed across the device and the efficiency of various cooling strategies.
Step 3: Selecting Cooling Methods
Based on the simulation results, choose the most effective cooling method for each component.
Common cooling techniques include heat sinks, fans, liquid cooling, and thermoelectric devices.
Each method has its advantages and limitations, so the choice will depend on factors like size, cost, and performance requirements.
Step 4: Optimizing the Design
After selecting the cooling methods, optimize the design for efficiency and effectiveness.
Modify the virtual model to incorporate the selected cooling solutions and simulate the thermal performance.
Adjust the design as needed to ensure that all components operate within safe temperature limits.
Step 5: Testing and Validation
Once the design is optimized, build a physical prototype and test it under real-world conditions.
Measure the temperature distribution across the device and compare it with the simulation results.
This step validates the accuracy of the model-based design and identifies any discrepancies that may need further refinement.
Challenges and Considerations
Thermal design is complex and involves several challenges.
Engineers must consider material properties, component placement, and environmental conditions.
Additionally, the design must account for any physical constraints and comply with industry standards.
It is important to remember that no single cooling solution fits all scenarios.
Each electronic device has unique requirements, and the thermal management strategy must be tailored accordingly.
Future Trends in Thermal Design
As technology continues to evolve, the demand for efficient thermal management solutions increases.
Emerging trends include the use of advanced materials like graphene for improved heat dissipation, and the integration of artificial intelligence in thermal control systems.
These innovations promise to enhance the performance and reliability of electronic devices.
Conclusion
Thermal design plays a critical role in the electronics industry.
By applying principles of thermofluid engineering and utilizing model-based design, engineers can create effective cooling solutions that extend the lifespan and performance of electronic devices.
A thorough understanding of these concepts and practices is essential for developing efficient thermal management systems in the face of ongoing technological advancements.
資料ダウンロード
QCD管理受発注クラウド「newji」は、受発注部門で必要なQCD管理全てを備えた、現場特化型兼クラウド型の今世紀最高の受発注管理システムとなります。
ユーザー登録
受発注業務の効率化だけでなく、システムを導入することで、コスト削減や製品・資材のステータス可視化のほか、属人化していた受発注情報の共有化による内部不正防止や統制にも役立ちます。
NEWJI DX
製造業に特化したデジタルトランスフォーメーション(DX)の実現を目指す請負開発型のコンサルティングサービスです。AI、iPaaS、および先端の技術を駆使して、製造プロセスの効率化、業務効率化、チームワーク強化、コスト削減、品質向上を実現します。このサービスは、製造業の課題を深く理解し、それに対する最適なデジタルソリューションを提供することで、企業が持続的な成長とイノベーションを達成できるようサポートします。
製造業ニュース解説
製造業、主に購買・調達部門にお勤めの方々に向けた情報を配信しております。
新任の方やベテランの方、管理職を対象とした幅広いコンテンツをご用意しております。
お問い合わせ
コストダウンが利益に直結する術だと理解していても、なかなか前に進めることができない状況。そんな時は、newjiのコストダウン自動化機能で大きく利益貢献しよう!
(β版非公開)