- お役立ち記事
- Practical Guide to Improving Product Quality in Spinning
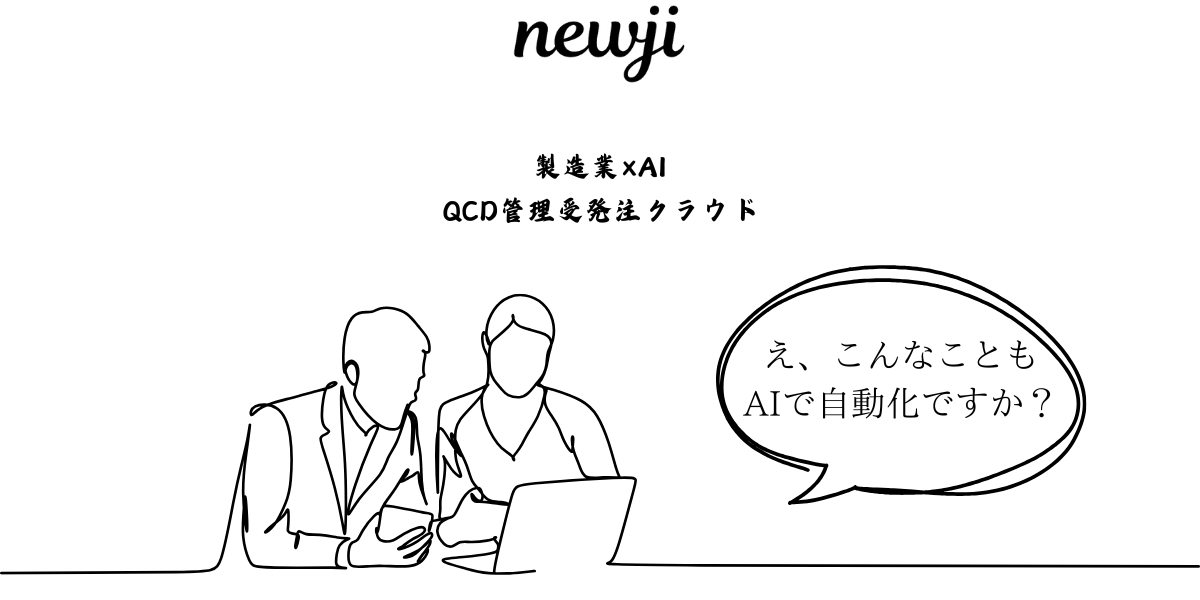
Practical Guide to Improving Product Quality in Spinning
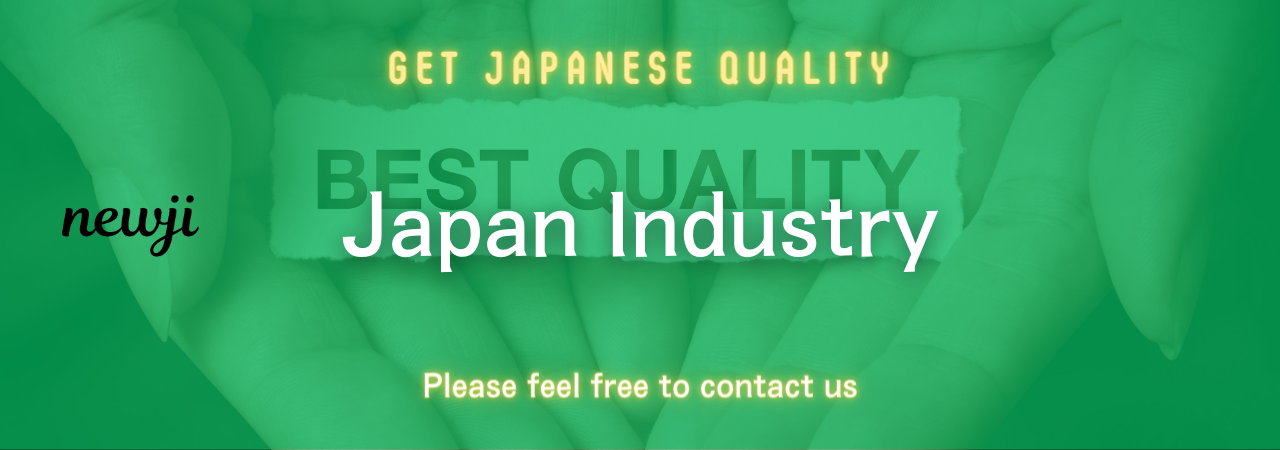
Improving the quality of products in spinning requires a strategic approach that revolves around meticulous planning, precise execution, and constant evaluation.
Spinning, being a fundamental process in the textile industry, encompasses the conversion of fibers into yarn.
Ensuring high product quality in spinning not only enhances the end-product but also optimizes the entire production cycle, reducing waste and boosting efficiency.
目次
Understanding the Basics of Spinning
Spinning involves several intricate steps starting from fiber selection to yarn winding.
Each step plays a critical role in determining the final quality of the yarn.
High-quality fiber selection is a prerequisite.
Fibers should be clean, of appropriate length, and have uniform thickness.
Impurities in fibers can lead to weak yarn, resulting in defects in the fabric.
Examine factors like fiber strength, length, fineness, and cleanliness.
This crucial first step sets the foundation for the remaining process.
Optimizing the Spinning Process
Blending
Blending is the process of mixing different fibers to achieve uniform properties throughout the yarn.
Proper blending ensures consistent quality in terms of strength, color, and texture.
Mechanized blending, controlled by technological tools, provides better results compared to manual blending.
Regular checks on blending ratios maintain consistency.
Incorporating automation into the blending process can significantly enhance the uniformity and quality of the spun yarn.
Carding
Carding is another critical stage where fibers are disentangled, cleaned, and interlaced to form a continuous web or sliver.
The efficiency of the carding machine directly impacts the quality of the yarn.
Periodic maintenance of carding machines and replacing the carding clothing when necessary can prevent defects.
Monitoring the speed and tension of the carding machine helps in producing a finer sliver.
Detecting and removing impurities during carding reduces imperfections in yarn.
Drawing
Drawing elongates and increases the uniformity of the sliver.
Drawing frames should be set to optimal speed and tension.
Appropriate drafting roll materials can limit contamination and sliver breakage.
Regular cleaning of drawing frames minimizes the chances of contamination.
Adjusting the draft ratio according to fiber type ensures a balanced yarn quality.
Roving
Roving prepares slivers into roving, a finer and slightly twisted strand suitable for spinning.
Proper control over twist and tension during roving prevents weak spots in yarn.
Regular inspection of roving frames ensures consistent performance.
Using high-quality roving belts and gears can effectively reduce breakage.
Ensuring lubrication of roving machinery can enhance performance and prevent malfunctions.
Spinning
Finally, spinning frames convert roving into yarn with controlled twist and tension.
Maintaining spindle speeds within recommended limits ensures consistent yarn quality.
Regular maintenance of spindles, rollers, and rings prevents undesired variability.
Monitoring the environmental conditions like humidity and temperature can prevent yarn defects caused by fluctuating conditions.
Incorporating advanced spinning technologies can further refine the quality of the finished yarn.
Quality Control and Inspection
In-process Inspections
Conducting in-process inspections at various stages helps in early detection and rectification of defects.
Regular analysis of intermediate products like sliver, roving, and unfinished yarn identifies potential issues.
Utilizing high-precision instruments for inspection ensures accurate detection of defects.
Training personnel to identify and address common issues during the process can minimize defects.
Post-production Quality Checks
After spinning, the yarn should undergo rigorous quality checks for parameters like evenness, strength, and appearance.
Automated quality check systems reduce human error and enhance accuracy.
Random sampling and rigorous testing of yarn batches can provide insights into overall product quality.
Corrective measures post-inspection can help avoid recurrence of identified defects.
Integrating quality management systems can streamline the inspection procedures and enhance overall productivity.
Technological Advancements and Innovations
To keep up with competitive markets, leveraging technological advancements is crucial.
Automation
The use of automation in spinning processes enhances precision and reduces human-induced errors.
Implementing automated systems for blending, carding, and drawing optimizes production consistency.
Automation can streamline the entire production process, making it efficient and less prone to faults.
AI and Machine Learning
Incorporating AI and machine learning in the spinning process can predict and rectify defects before they propagate.
Machine learning algorithms can analyze vast data from spinning processes to identify patterns and potential faults.
Predictive maintenance supported by AI can ensure timely intervention, preventing machinery downtimes.
AI can assist in maintaining optimal environmental conditions, thus preventing yarn inconsistencies.
Internet of Things (IoT)
IoT-driven monitoring systems continuously track machine performance and product quality.
Real-time data from IoT sensors helps in timely decisions to adjust process parameters.
These systems provide comprehensive insights into production, facilitating informed decisions that enhance product quality.
IoT integration enhances transparency across the production line, ensuring consistent monitoring.
Continuous Improvement and Training
A dynamic approach towards continuous improvement ensures sustained product quality.
Regular Training Programs
Keeping the workforce updated with the latest techniques and technologies is vital.
Conduct regular training sessions for machine operators, quality inspectors, and maintenance personnel.
Workshops and demonstrations can enhance the practical understanding of advancements in spinning technology.
Feedback Mechanisms
Implementing robust feedback mechanisms can provide real-time insights from the production floor.
Encourage open communication where workers can report potential issues and suggest improvements.
Analyzing feedback helps in understanding recurring problems and developing long-term solutions.
Lean Manufacturing Principles
Adopting lean manufacturing principles can significantly improve efficiency and product quality.
Principles like eliminating waste, continuous improvement (Kaizen), and maintaining quality through Total Quality Management (TQM) foster a culture of excellence.
Regular Kaizen events and continuous improvement programs can keep quality enhancement efforts on track.
Enduring commitment to lean principles ensures a sustained focus on quality and operational efficiency.
Improving product quality in spinning demands a strategic, comprehensive approach encompassing every step from fiber selection to final inspection.
An unwavering focus on optimization, continuous improvement, and embracing technological advancement lays the foundation for superior yarn and fabric quality.
Achieving excellence in spinning quality not only boosts customer satisfaction but also solidifies a company’s competitive edge in the textile market.
資料ダウンロード
QCD調達購買管理クラウド「newji」は、調達購買部門で必要なQCD管理全てを備えた、現場特化型兼クラウド型の今世紀最高の購買管理システムとなります。
ユーザー登録
調達購買業務の効率化だけでなく、システムを導入することで、コスト削減や製品・資材のステータス可視化のほか、属人化していた購買情報の共有化による内部不正防止や統制にも役立ちます。
NEWJI DX
製造業に特化したデジタルトランスフォーメーション(DX)の実現を目指す請負開発型のコンサルティングサービスです。AI、iPaaS、および先端の技術を駆使して、製造プロセスの効率化、業務効率化、チームワーク強化、コスト削減、品質向上を実現します。このサービスは、製造業の課題を深く理解し、それに対する最適なデジタルソリューションを提供することで、企業が持続的な成長とイノベーションを達成できるようサポートします。
オンライン講座
製造業、主に購買・調達部門にお勤めの方々に向けた情報を配信しております。
新任の方やベテランの方、管理職を対象とした幅広いコンテンツをご用意しております。
お問い合わせ
コストダウンが利益に直結する術だと理解していても、なかなか前に進めることができない状況。そんな時は、newjiのコストダウン自動化機能で大きく利益貢献しよう!
(Β版非公開)