- お役立ち記事
- Practical guidelines for essential APQP processes for quality control departments
月間76,176名の
製造業ご担当者様が閲覧しています*
*2025年3月31日現在のGoogle Analyticsのデータより
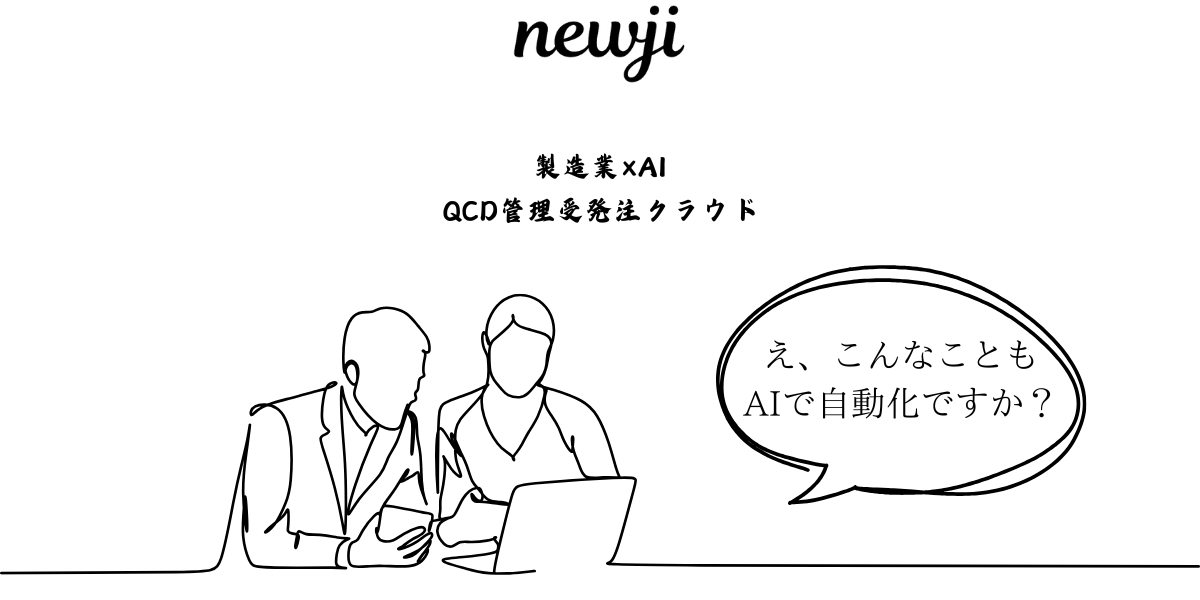
Practical guidelines for essential APQP processes for quality control departments
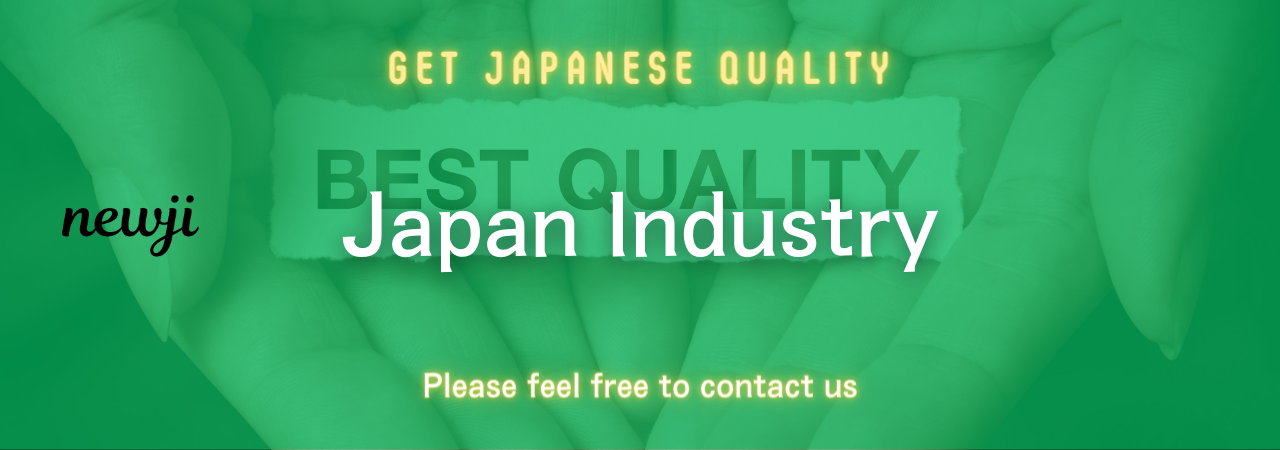
目次
Understanding APQP: An Overview
Advanced Product Quality Planning (APQP) is a vital framework utilized in the automotive industry to ensure the delivery of high-quality products.
Introduced by the Automotive Industry Action Group (AIAG), APQP provides a structured approach for quality planning during product development.
This methodology is not just confined to automotive manufacturing, as it is beneficial across various sectors where quality is paramount.
The main goal of APQP is to facilitate communication and collaboration between different departments, ensuring that quality is built into the product design and manufacturing processes.
It helps organizations to identify potential failures, optimize processes, and enhance product reliability.
APQP is structured into five phases, each with specific deliverables and objectives aimed at improving product quality and customer satisfaction.
The Five Phases of APQP
1. Plan and Define Program
The first phase involves planning and defining the program.
At this stage, a cross-functional team is formed to gather customer requirements and expectations.
This phase focuses on understanding the customer needs, product design goals, project scope, and preliminary process design.
Key deliverables include project feasibility studies, benchmarking data, and preliminary timelines.
Effective communication and strong teamwork are critical during this phase to ensure that all customer requirements are well-understood and documented.
This foundation sets the path for the successful implementation of the subsequent phases.
2. Product Design and Development
In the second phase, the focus shifts to product design and development.
This is where concepts turn into actual designs through the integration of engineering principles and customer inputs.
Design FMEA (Failure Mode and Effects Analysis) is often conducted at this stage to identify potential design failures and their impact on product performance.
Documentation, such as design specifications and technical drawings, are refined during this phase.
Prototyping and testing play a crucial role here to validate the design and ensure it meets customer needs.
Feedback loops are essential to address any issues and refine the product design accordingly.
3. Process Design and Development
Once the product design is solidified, the third phase involves designing the process that will produce the product.
Process FMEA is performed to identify potential process failures and implement preventive measures.
The emphasis is on developing a capable production process that guarantees quality while optimizing efficiency.
This phase includes activities such as process mapping, tool design, and equipment selection.
Control plans and work instructions are developed to provide clear guidelines for the production team.
The ultimate goal is to create a stable process that consistently delivers high-quality products.
4. Product and Process Validation
In the fourth phase, validation of the product and process is performed.
This involves conducting trials in production settings to ensure that the product and process can consistently meet customer requirements.
Key activities include production trial runs, capability studies, and final verification tests.
During this phase, the product is subjected to rigorous testing to confirm that it performs according to specifications.
The process is also scrutinized to check for stability and capability.
This phase culminates in a production part approval process (PPAP), which certifies that the product meets all customer and regulatory requirements.
5. Launch, Feedback, Assessment, and Corrective Action
The final phase of APQP involves launching the product into mass production while continuously gathering feedback for improvement.
Feedback from production and post-production assessments is vital in identifying areas for enhancement.
Any deviations from expected outcomes are analyzed, and corrective actions are implemented to prevent recurrence.
This phase emphasizes continuous improvement through regular assessments and feedback loops.
The objective is to fine-tune both the product and the process to maintain high quality even as production scales.
APQP in Quality Control Departments
Quality control departments play a crucial role in implementing APQP guidelines.
Their primary responsibility is to ensure that quality is maintained throughout the entire product lifecycle.
Incorporating APQP processes helps quality control teams to systematically evaluate every aspect of product development and manufacturing.
This holistic approach minimizes defects, reduces costs, and improves customer satisfaction.
The use of standardized tools such as FMEA, control plans, and process flows within the APQP framework enables quality control teams to effectively manage risks and improve product quality.
Early identification of potential issues allows for proactive measures, reducing the likelihood of costly rework or recalls.
Benefits of Implementing APQP
Adopting APQP practices in quality control departments offers several advantages:
1. Enhanced Product Quality
By integrating customer requirements throughout the development process, APQP ensures that the final product meets or exceeds expectations.
The structured approach to risk management and process optimization results in superior product quality.
2. Improved Communication and Collaboration
APQP fosters collaboration among different departments by establishing clear communication channels and shared objectives.
This minimizes misunderstandings and ensures that everyone is aligned towards a common goal.
3. Reduced Time to Market
A well-defined APQP process helps streamline product development cycles, enabling faster time to market.
With early spotting of potential issues, rework is minimized, and production processes are more efficient.
4. Cost Savings
By reducing defects and optimizing processes, organizations can achieve significant cost savings.
APQP minimizes waste, prevents costly recalls, and improves resource utilization.
Conclusion
Advanced Product Quality Planning is an essential tool in any quality control department’s toolkit.
By adhering to APQP guidelines, companies can elevate their product quality, improve time to market, and enhance customer satisfaction.
Through diligent planning, design, validation, and continuous improvement, APQP helps in building robust processes that deliver consistent and reliable products.
It sets a standard for excellence that positions organizations for long-term success in competitive markets.
資料ダウンロード
QCD管理受発注クラウド「newji」は、受発注部門で必要なQCD管理全てを備えた、現場特化型兼クラウド型の今世紀最高の受発注管理システムとなります。
ユーザー登録
受発注業務の効率化だけでなく、システムを導入することで、コスト削減や製品・資材のステータス可視化のほか、属人化していた受発注情報の共有化による内部不正防止や統制にも役立ちます。
NEWJI DX
製造業に特化したデジタルトランスフォーメーション(DX)の実現を目指す請負開発型のコンサルティングサービスです。AI、iPaaS、および先端の技術を駆使して、製造プロセスの効率化、業務効率化、チームワーク強化、コスト削減、品質向上を実現します。このサービスは、製造業の課題を深く理解し、それに対する最適なデジタルソリューションを提供することで、企業が持続的な成長とイノベーションを達成できるようサポートします。
製造業ニュース解説
製造業、主に購買・調達部門にお勤めの方々に向けた情報を配信しております。
新任の方やベテランの方、管理職を対象とした幅広いコンテンツをご用意しております。
お問い合わせ
コストダウンが利益に直結する術だと理解していても、なかなか前に進めることができない状況。そんな時は、newjiのコストダウン自動化機能で大きく利益貢献しよう!
(β版非公開)