- お役立ち記事
- Practical know-how course on how to effectively proceed with FMEA/DRBFM and measures to prevent quality problems.
月間77,185名の
製造業ご担当者様が閲覧しています*
*2025年2月28日現在のGoogle Analyticsのデータより
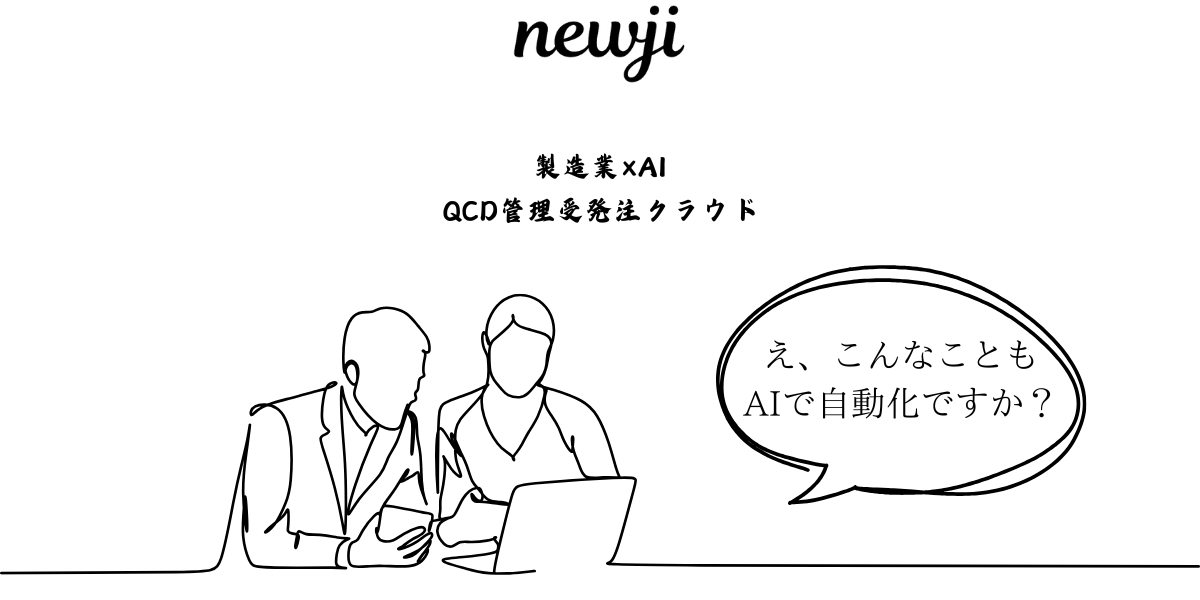
Practical know-how course on how to effectively proceed with FMEA/DRBFM and measures to prevent quality problems.
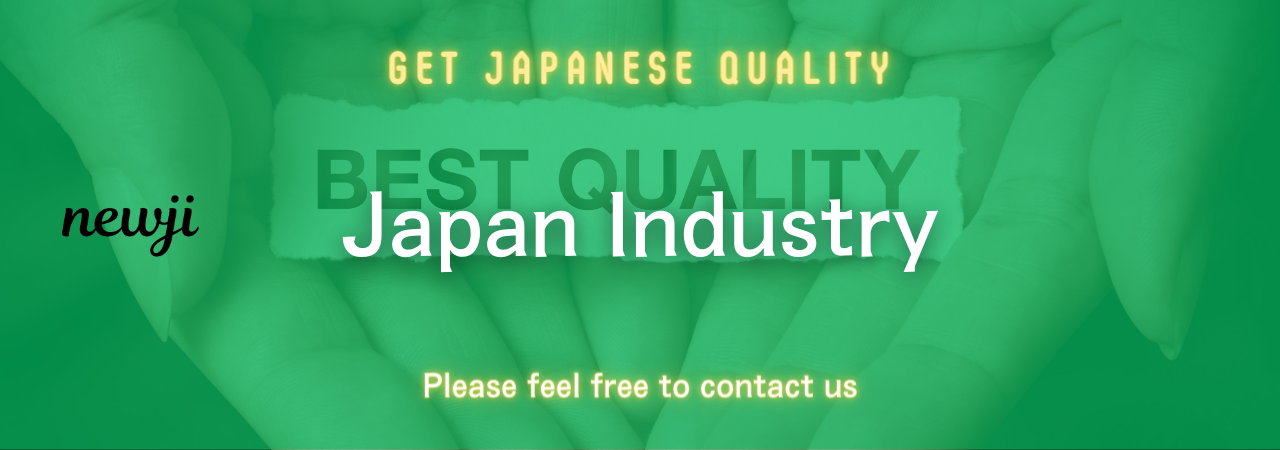
目次
Understanding FMEA and DRBFM
Failure Modes and Effects Analysis (FMEA) and Design Review Based on Failure Modes (DRBFM) are systematic processes used to identify potential failures in design and manufacturing processes.
These methodologies aim to proactively identify and mitigate risks to improve product quality and reliability.
Both are integral to maintaining high standards and preventing quality issues before they arise.
While FMEA focuses on identifying and evaluating potential failure modes in a system, DRBFM emphasizes reviewing design changes to spotlight areas of concern.
Understanding these processes can significantly enhance your product development cycle by ensuring better design efficiency and safety.
The Importance of FMEA
FMEA is a step-by-step approach that helps predict potential points of failure within a given system.
By analyzing various components and their interactions, teams can prevent defects and enhance overall product performance.
The key lies in being able to thoroughly recognize and address weaknesses before they can manifest as real-world problems.
Conducting a successful FMEA requires a deep understanding of the system being analyzed.
This necessitates involving cross-functional teams who bring diverse perspectives and knowledge bases to identify all possible failure modes.
When carried out effectively, FMEA lays the groundwork for superior product design and more reliable performance.
Steps to Implement FMEA
1. **Assemble a Team:** Gather a group of individuals with diverse expertise pertinent to the project.
This includes design engineers, quality assurance specialists, and manufacturing personnel.
2. **Define the Scope:** Clearly outline the boundaries of the analysis to ensure focus and relevancy in findings.
3. **Identify Failure Modes:** List all potential failures that could occur with each component or process in your system.
Consider what could go wrong and why.
4. **Evaluate Risk:** Prioritize the failure modes based on their severity, occurrence, and detectability.
Assign a risk priority number (RPN) to guide which issues demand immediate attention.
5. **Develop Action Plans:** Design countermeasures for the highest risk areas.
These should aim to eliminate or control the causes of potential failures.
6. **Implement Solutions:** Integrate the recommended actions into the design or process.
7. **Monitor Results:** Once modifications are enacted, continuously review outcomes to ensure the efficacy of the solutions and make adjustments if necessary.
Understanding DRBFM
DRBFM is particularly useful when modifications or design changes are introduced to a product.
This method prioritizes in-depth reviews of these modifications to preclude unintended consequences that could lead to failures.
It is a preventive approach that complements FMEA by ensuring design alterations don’t compromise the product’s integrity.
Key Steps in Applying DRBFM
1. **Identify Changes:** Recognize additions or alterations in the design that could impact current performance.
2. **Formulate the Base Design:** Establish a baseline design to provide a point of comparison and clarity in identifying shifts and the reasons driving changes.
3. **Discuss Changes:** Engage in detailed discussions about how alterations may introduce new risks and create weaknesses.
4. **Investigate Likely Outcomes:** Examine the potential effects that the design changes could manifest across the entire product lifecycle.
5. **Develop Solutions:** Propose countermeasures to address the identified risks.
Ensure these solutions are feasible and align with the design objectives.
6. **Conduct Validation Testing:** Validate the effectiveness of changes through testing and simulations to confirm the absence of risks.
Preventing Quality Problems
The main goal of FMEA and DRBFM methodologies is to prevent quality problems before they happen.
Implementing these strategies enables teams to maintain high standards of quality by pinpointing and addressing issues early in the development process.
These tools are not limited to just identifying and fixing flaws.
They also facilitate collaboration between departments, encouraging a culture of quality within organizations.
Both methodologies support a cyclical process of improvement that leads to better product outcomes.
Benefits of Proactive Quality Management
– **Cost Reduction:** By identifying potential issues beforehand, companies can avoid costly recalls or customer dissatisfaction.
– **Enhanced Safety:** Preg, nizing potential risks and implementing effective solutions minimizes safety-related incidents.
– **Customer Satisfaction:** Maintaining high-quality standards leads to improved customer loyalty and brand reputation.
– **Continuous Improvement:** Fostering a culture of continuous improvement and learning within the organization enhances innovation.
Challenges and Considerations
Although FMEA and DRBFM can greatly improve processes and product quality, there are challenges that organizations may face:
– **Resource Intensive:** Both methods require considerable time and resources, particularly in complex systems.
Allocating these resources might be challenging, but it is crucial for effective outcomes.
– **Maintaining Objectivity:** Keeping an unbiased view during evaluations is essential.
It can be tempting to overlook small design flaws, but maintaining thoroughness is key to preventing future issues.
– **Interdepartmental Cooperation:** Necessity for collaboration across departments may encounter resistance or miscommunication, which can hinder the process.
Conclusion
Utilizing FMEA and DRBFM as part of your process ensures that potential issues are identified and addressed before they impact the end product.
Integrating these methodologies leads to higher-quality outcomes, improved safety, and satisfied customers.
Despite their challenges, the proactive nature of these tools provides a significant return on investment through enhanced reliability and performance.
資料ダウンロード
QCD管理受発注クラウド「newji」は、受発注部門で必要なQCD管理全てを備えた、現場特化型兼クラウド型の今世紀最高の受発注管理システムとなります。
ユーザー登録
受発注業務の効率化だけでなく、システムを導入することで、コスト削減や製品・資材のステータス可視化のほか、属人化していた受発注情報の共有化による内部不正防止や統制にも役立ちます。
NEWJI DX
製造業に特化したデジタルトランスフォーメーション(DX)の実現を目指す請負開発型のコンサルティングサービスです。AI、iPaaS、および先端の技術を駆使して、製造プロセスの効率化、業務効率化、チームワーク強化、コスト削減、品質向上を実現します。このサービスは、製造業の課題を深く理解し、それに対する最適なデジタルソリューションを提供することで、企業が持続的な成長とイノベーションを達成できるようサポートします。
製造業ニュース解説
製造業、主に購買・調達部門にお勤めの方々に向けた情報を配信しております。
新任の方やベテランの方、管理職を対象とした幅広いコンテンツをご用意しております。
お問い合わせ
コストダウンが利益に直結する術だと理解していても、なかなか前に進めることができない状況。そんな時は、newjiのコストダウン自動化機能で大きく利益貢献しよう!
(β版非公開)