- お役立ち記事
- Practical know-how for effective on-site improvement and problem solving in production management
Practical know-how for effective on-site improvement and problem solving in production management
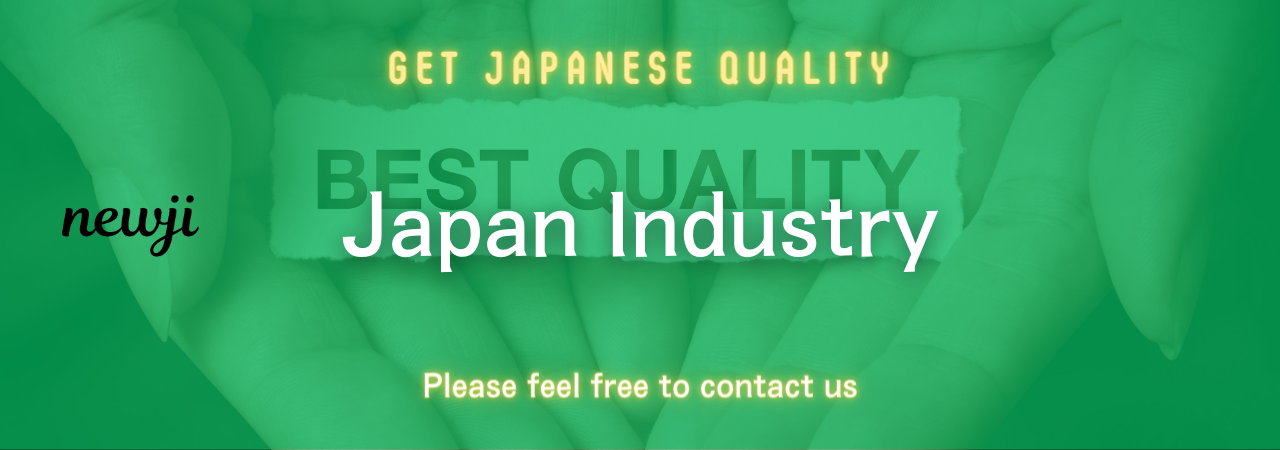
目次
Understanding On-Site Improvement in Production Management
On-site improvement, also known as “Gemba Kaizen” in Japanese, plays a crucial role in enhancing production management within any manufacturing setup.
The term “Gemba” translates to “the real place” in Japanese, referring to the actual location where work is done.
In the context of production, it means the factory floor or the site where value is created.
Focusing on the Gemba helps management identify issues at their source, fostering significant improvements that are vital for efficient production.
Importance of On-Site Improvement
On-site improvement involves taking a hands-on approach to identifying problems, streamlining processes, and implementing changes directly on the production floor.
It’s essential because theoretical knowledge alone rarely uncovers the nuances and inefficiencies present in everyday operations.
Addressing issues on-site ensures that solutions are practical, relevant, and immediately applicable.
This approach results in rapid problem solving, boosting productivity and reducing waste.
Key Strategies for Effective Problem Solving
To capitalize on the benefits of on-site improvements, adopting specific strategies is vital.
These strategies guide teams in identifying problems, analyzing root causes, and implementing effective solutions.
Kaizen Philosophy
Kaizen, meaning “change for better,” emphasizes continuous improvement.
Implementing Kaizen involves all levels of employees, encouraging a culture where every small improvement contributes to overall efficiency.
It’s about fostering an environment where ideas for improvement are welcomed and tested, making production processes smoother over time.
Root Cause Analysis
Root cause analysis is a method used to identify the origin of a problem, allowing teams to address the underlying issues rather than symptoms.
Tools such as the Five Whys and Fishbone diagrams assist in getting to the root cause, enabling effective solutions to be crafted based on real insights.
Utilizing Lean Principles
Lean principles focus on reducing waste and maximizing value.
By identifying waste in its various forms—be it time, materials, or labor—lean practices ensure every step in the production process adds value.
On-site improvements informed by Lean methodologies often lead to streamlined operations and enhanced efficiency.
Encouraging Employee Involvement
When employees who work directly with manufacturing processes are involved in on-site improvements, it leads to more actionable insights.
These employees often have intimate knowledge of the challenges faced during operations and can offer realistic solutions that management might overlook.
Encouraging their input creates a sense of ownership and accountability, further enhancing problem-solving efficiency.
Implementing On-Site Improvements
Effectively implementing on-site improvements requires a structured approach to apply the identified problem-solving strategies.
Step 1: Observation
The first step involves closely observing the work process on-site to pinpoint areas of inefficiency or waste.
This means spending time on the factory floor, watching how employees carry out tasks, and identifying bottlenecks or repeated errors.
Step 2: Data Collection
Data collection helps quantify the problem and track progress.
This includes logging production rates, downtimes, error frequencies, and resource utilization.
Having reliable data provides a baseline against which the success of any improvement efforts can be measured.
Step 3: Collaboration and Feedback
Engaging with employees across different levels for feedback provides a comprehensive view of the issues.
Considering input from machine operators, line managers, and engineers ensures that all aspects of a problem are explored.
Collaboration fosters trust and helps build strategies based on a collective understanding of the challenges.
Step 4: Plan and Test Improvements
Once the problem is understood, planning an improvement strategy is essential.
This might involve rearranging workflows, upgrading machinery, or providing additional training.
Testing these improvements on a small scale allows teams to tweak them before full implementation.
Step 5: Implementation and Monitoring
After successful testing, the full-scale implementation of new processes or tools takes place.
Ongoing monitoring is crucial to ensure the improvements deliver the intended benefits and identify any adjustments needed for optimum results.
Regular reviews and feedback loops help maintain a cycle of continuous improvement.
Challenges and Solutions in On-Site Improvement
Despite its clear benefits, on-site improvement faces several challenges.
Understanding and addressing these can significantly enhance problem-solving efforts.
Resistance to Change
Employees may resist changes due to fear of the unknown or habits formed over years.
Clear communication about the benefits and involving them early in the process can mitigate this resistance.
Training and acknowledging their concerns helps reassure and motivate the workforce.
Limited Resources
Resource constraints, whether time, budget, or manpower, can hinder improvement efforts.
Prioritizing solutions with the highest potential impact and starting small can help overcome these limitations.
Regularly revisiting resource allocation can also optimize use.
Inconsistent Improvement Efforts
Inconsistency in improvement efforts leads to erratic results.
Establishing a culture of continuous improvement and making it part of the organizational ethos ensures sustained focus.
Documenting processes and tracking progress also aids in maintaining consistency.
Conclusion
On-site improvement and practical problem solving are integral to effective production management.
By focusing on areas where value is created, involving employees, and utilizing strategic tools such as Kaizen and Lean principles, organizations can significantly bolster their operational efficiency.
Overcoming challenges requires structured implementation, open communication, and an unwavering commitment to continuous improvement.
Ultimately, these efforts culminate in a more responsive, efficient, and productive production environment.
資料ダウンロード
QCD調達購買管理クラウド「newji」は、調達購買部門で必要なQCD管理全てを備えた、現場特化型兼クラウド型の今世紀最高の購買管理システムとなります。
ユーザー登録
調達購買業務の効率化だけでなく、システムを導入することで、コスト削減や製品・資材のステータス可視化のほか、属人化していた購買情報の共有化による内部不正防止や統制にも役立ちます。
NEWJI DX
製造業に特化したデジタルトランスフォーメーション(DX)の実現を目指す請負開発型のコンサルティングサービスです。AI、iPaaS、および先端の技術を駆使して、製造プロセスの効率化、業務効率化、チームワーク強化、コスト削減、品質向上を実現します。このサービスは、製造業の課題を深く理解し、それに対する最適なデジタルソリューションを提供することで、企業が持続的な成長とイノベーションを達成できるようサポートします。
オンライン講座
製造業、主に購買・調達部門にお勤めの方々に向けた情報を配信しております。
新任の方やベテランの方、管理職を対象とした幅広いコンテンツをご用意しております。
お問い合わせ
コストダウンが利益に直結する術だと理解していても、なかなか前に進めることができない状況。そんな時は、newjiのコストダウン自動化機能で大きく利益貢献しよう!
(Β版非公開)