- お役立ち記事
- Practical know-how on failure analysis technology and reliability evaluation methods for power semiconductor products
月間76,176名の
製造業ご担当者様が閲覧しています*
*2025年3月31日現在のGoogle Analyticsのデータより
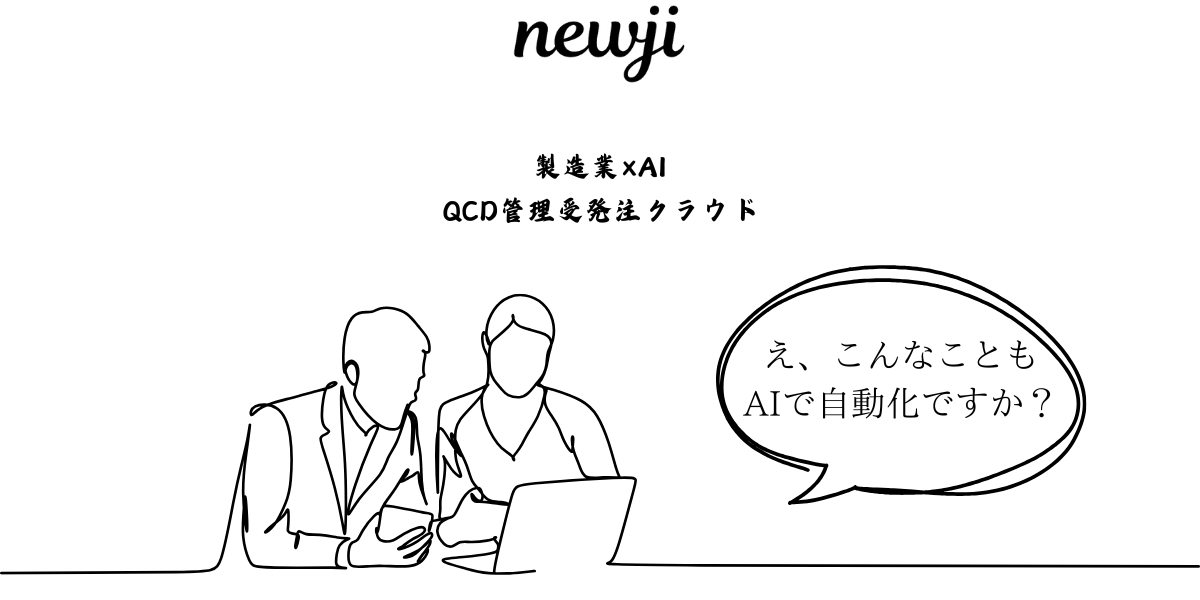
Practical know-how on failure analysis technology and reliability evaluation methods for power semiconductor products
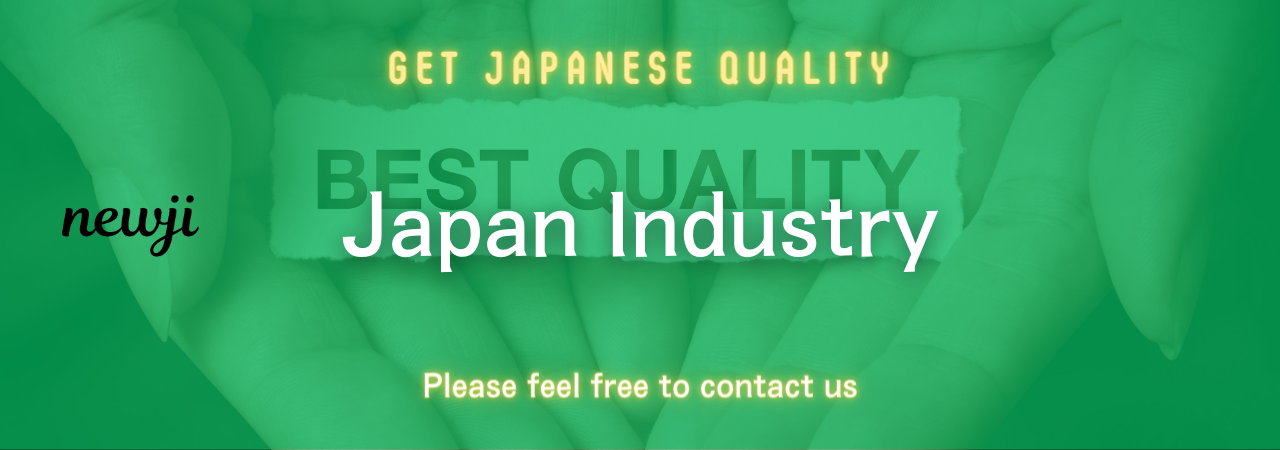
目次
Understanding Power Semiconductor Products
Power semiconductor products are crucial components in modern electronics, providing essential functionality for the conversion and control of electrical power.
These components are used in a wide array of applications, from consumer electronics to industrial equipment, and play a significant role in enhancing energy efficiency.
However, like all electronic components, power semiconductors can fail due to various reasons, making failure analysis technology and reliability evaluation methods vital for ensuring their longevity and performance.
The Importance of Failure Analysis in Power Semiconductors
Failure analysis in power semiconductors is a systematic process to identify the root cause of component failures.
Understanding these failures is indispensable for manufacturers to improve product designs and ensure reliability.
It involves a series of technical evaluations that may include visual inspections, electrical testing, and advanced analytical techniques such as scanning electron microscopy (SEM) and energy dispersive X-ray spectroscopy (EDX).
By analyzing failures, engineers can determine whether they stem from manufacturing defects, design flaws, or operational stresses.
Common Causes of Failure
Failures in power semiconductors generally arise from several common causes.
Manufacturing defects, such as improper dopant levels or contamination, can result in early-life failures.
Electrical overstress and electrostatic discharge are also significant contributors, often occurring during handling or due to inadequate protective measures.
Thermal issues, such as overheating from poor thermal design or inadequate heat dissipation, are other typical culprits behind semiconductor failure.
Finally, mechanical stresses, including vibrations and shock, can also lead to long-term reliability issues.
Reliability Evaluation Methods
Ensuring the reliability of power semiconductor products requires comprehensive evaluation methods.
These methods simulate real-world conditions to anticipate product performance over time.
Accelerated Life Testing
Accelerated life testing (ALT) is a crucial tool for evaluating the reliability of power semiconductors.
This method involves subjecting products to elevated stress conditions, such as higher temperatures or voltages, to induce failures within a shorter time frame.
By analyzing the failure modes and mechanisms identified during ALT, manufacturers can predict the product’s lifespan under normal operating conditions.
Bournout Testing
Burnout testing is another reliability evaluation method used, particularly for assessing a semiconductor’s robustness against thermal and electrical stresses.
During burnout testing, the power semiconductors are operated under extreme electrical conditions until they fail.
This helps to understand the maximum limits the device can handle and provides insights into its thermal and electrical handling capabilities.
Thermal Cycling and Vibration Testing
Thermal cycling tests evaluate how power semiconductor products react to temperature fluctuations, mimicking real-world cycles of heating and cooling.
This is vital for determining the material’s endurance against thermal fatigue.
Vibration testing, on the other hand, assesses the mechanical integrity of components under simulated operational vibrations.
Both tests are vital in understanding how these components will perform in dynamic environments, such as automotive or industrial applications.
Technological Advancements in Failure Analysis
Recent advancements in technology have significantly improved the ability to analyze failures in power semiconductors.
Non-Destructive Testing
Non-destructive testing techniques, such as infrared thermography and X-ray tomography, provide valuable insights without damaging the components.
These methods are ideal for initial investigations, allowing engineers to assess internal structures and identify potential defects before proceeding to more invasive techniques.
Advanced Microscopy
Advanced microscopic techniques have become indispensable in failure analysis.
Scanning electron microscopy (SEM) and focused ion beam (FIB) microscopy provide detailed images of semiconductor surfaces and cross-sections.
These techniques allow engineers to examine microscopic failures that are not visible to the naked eye, aiding in pinpointing the exact failure sites and mechanisms.
Data Analytics and AI
Data analytics and artificial intelligence (AI) are revolutionizing the approach to failure analysis and reliability assessment.
Machine learning algorithms can process vast amounts of data from different testing scenarios, identifying patterns and predictive markers of failure.
AI-driven analytics enhances the predictive accuracy of failure analysis and enables manufacturers to make data-driven decisions for designing more reliable semiconductor products.
Enhancing Reliability through Design Improvements
While failure analysis and testing are critical, their insights are most valuable when they lead to tangible improvements in design.
Material Selection
Choosing the right materials is fundamental to enhancing the reliability of power semiconductor products.
Materials that demonstrate superior thermal and mechanical properties can significantly reduce the risk of failure due to thermal fatigue or mechanical stress.
Advanced Packaging Techniques
Innovative packaging techniques, such as chip-on-board and flip-chip designs, can improve heat dissipation and reduce thermal resistance, mitigating common failure modes associated with overheating.
By optimizing package design, manufacturers can enhance both the thermal and the structural robustness of semiconductors.
Conclusion
Failure analysis and reliability evaluation are integral to the development of power semiconductor products.
By understanding the causes of failure and employing robust evaluation methods, manufacturers can design more reliable and enduring products.
Incorporating advanced technologies and methodologies in the failure analysis process ensures that the power semiconductor products not only meet current performance standards but also exceed them, positioning them as reliable components in an increasingly energy-demanding world.
資料ダウンロード
QCD管理受発注クラウド「newji」は、受発注部門で必要なQCD管理全てを備えた、現場特化型兼クラウド型の今世紀最高の受発注管理システムとなります。
ユーザー登録
受発注業務の効率化だけでなく、システムを導入することで、コスト削減や製品・資材のステータス可視化のほか、属人化していた受発注情報の共有化による内部不正防止や統制にも役立ちます。
NEWJI DX
製造業に特化したデジタルトランスフォーメーション(DX)の実現を目指す請負開発型のコンサルティングサービスです。AI、iPaaS、および先端の技術を駆使して、製造プロセスの効率化、業務効率化、チームワーク強化、コスト削減、品質向上を実現します。このサービスは、製造業の課題を深く理解し、それに対する最適なデジタルソリューションを提供することで、企業が持続的な成長とイノベーションを達成できるようサポートします。
製造業ニュース解説
製造業、主に購買・調達部門にお勤めの方々に向けた情報を配信しております。
新任の方やベテランの方、管理職を対象とした幅広いコンテンツをご用意しております。
お問い合わせ
コストダウンが利益に直結する術だと理解していても、なかなか前に進めることができない状況。そんな時は、newjiのコストダウン自動化機能で大きく利益貢献しよう!
(β版非公開)