- お役立ち記事
- Practical know-how on quality engineering (Taguchi method) to improve product development efficiency and prevent complaints
月間77,185名の
製造業ご担当者様が閲覧しています*
*2025年2月28日現在のGoogle Analyticsのデータより
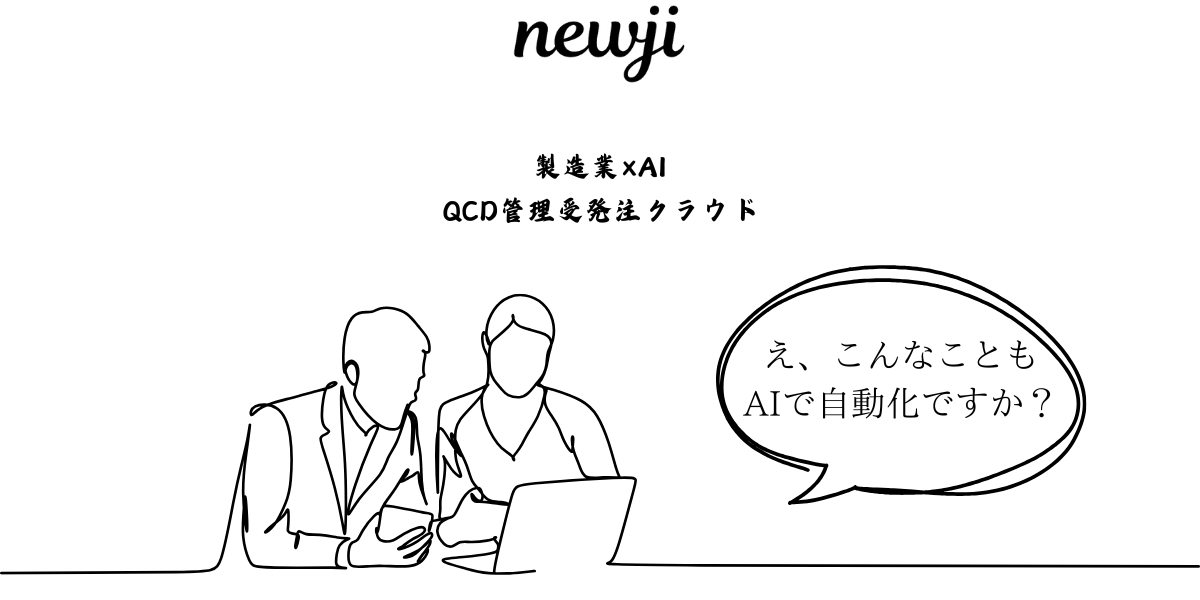
Practical know-how on quality engineering (Taguchi method) to improve product development efficiency and prevent complaints
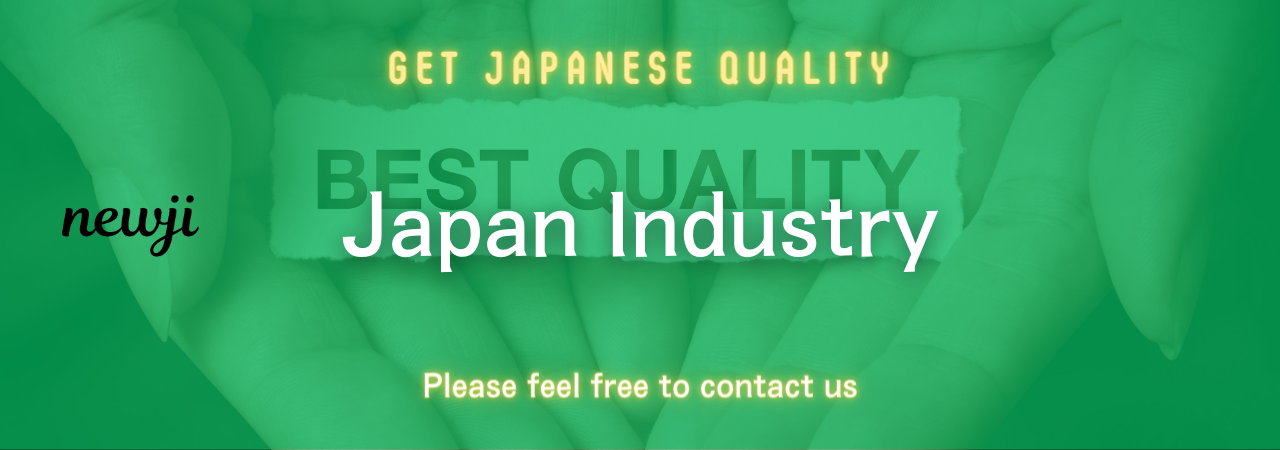
目次
Understanding Quality Engineering
Quality engineering plays a critical role in developing products that meet customer expectations and industry standards.
A key component of this field is the Taguchi method, which focuses on improving product quality and efficiency through robust design.
This approach emphasizes the importance of minimizing variance and focusing on the consistent performance of products, even in varying conditions.
The Taguchi method introduces a systematic approach to design and test experiments, making it easier to identify factors that affect product quality and performance.
Unlike traditional methods, which often rely on trial and error, the Taguchi method uses a more structured methodology that helps teams design experiments with fewer runs.
As a result, businesses can save time and resources while achieving higher quality standards.
The Core Principles of the Taguchi Method
At its heart, the Taguchi method is about improving product development processes by focusing on design robustness.
Robust design means creating products that deliver consistent performance under a variety of conditions.
This is achieved by understanding and controlling the factors that affect a product’s performance.
The method hinges on three essential concepts:
1. **Quality Loss Function**: The idea that any deviation from the target quality level results in a loss to society.
This principle encourages designers to aim for the target value rather than just meeting specifications.
By doing so, companies can reduce costs associated with defects and rework.
2. **Signal-to-Noise Ratio**: Taguchi developed this concept to measure how well a product can perform in different conditions.
A higher signal-to-noise ratio indicates a more robust product.
Designers use this ratio to assess the impact of variables and to fine-tune their designs for better performance.
3. **Orthogonal Arrays**: These are structured designs of experiments that allow teams to evaluate multiple variables simultaneously.
By using orthogonal arrays, companies can identify key factors that affect product quality, leading to more informed decisions during development.
Implementing the Taguchi Method in Product Development
To successfully implement the Taguchi method, teams need to follow a systematic approach.
Here is a step-by-step guide to integrating this methodology into your product development process:
1. Define the Problem
The first step in applying the Taguchi method is to clearly define the problem.
This involves identifying the critical characteristics of the product that must be optimized for performance.
It is crucial to involve key stakeholders to ensure everyone’s needs and expectations are considered.
2. Identify Factors and Levels
Next, list all the factors that could potentially impact product quality.
These factors can include materials, design parameters, environmental conditions, and more.
Once identified, assign levels to these factors to test their effects on the product.
3. Design the Experiment
Using orthogonal arrays, plan your experiments to test the combinations of factors and levels.
This structured approach reduces the number of experiments while ensuring comprehensive coverage of possibilities.
Consider the use of control and noise factors to simulate real-world conditions.
4. Conduct the Experiment
Carry out the experiments as per the plan, and carefully record the results.
Ensure that the tests are conducted in a controlled environment to maintain consistency.
The data collected should reflect how different factor combinations affect product quality and performance.
5. Analyze the Results
After experiments, analyze the data to determine the impact of each factor on the product’s performance.
Calculate the signal-to-noise ratio to identify which factors are significant and how they interact.
This analysis will guide you in making informed decisions on improving product design.
6. Optimize the Design
Based on the analysis, make adjustments to optimize the design for better quality and efficiency.
This may involve changing materials, adjusting parameters, or modifying design elements.
The goal is to achieve a robust design that consistently delivers high-quality products.
7. Verify the Improvements
Finally, conduct further testing to verify the improvements made.
Ensure that the product meets quality standards and performs consistently in different conditions.
Reiterate the process if necessary to fine-tune the product further.
Benefits of the Taguchi Method
The Taguchi method offers numerous benefits for product development teams:
– **Increased Efficiency**: By focusing on critical factors and reducing the number of experiments, the Taguchi method helps teams develop products faster and at a lower cost.
– **Improved Quality**: By minimizing variability and achieving robust designs, products meet higher quality standards, leading to greater customer satisfaction and fewer complaints.
– **Cost Savings**: Better quality results in fewer defects, reduced rework, and lower warranty costs, contributing positively to the bottom line.
– **Enhanced Innovation**: The structured approach provides insights into the behavior of products, leading to innovative solutions and competitive advantages.
Conclusion
In today’s competitive market, quality engineering is not just a luxury but a necessity.
The Taguchi method offers a practical approach to improving product quality and development efficiency.
By implementing this methodology, businesses can create robust designs that deliver consistent performance, satisfy customers, and reduce costs.
Whether you’re an established company or a startup, leveraging the Taguchi method can give you the edge needed to succeed in the marketplace.
資料ダウンロード
QCD管理受発注クラウド「newji」は、受発注部門で必要なQCD管理全てを備えた、現場特化型兼クラウド型の今世紀最高の受発注管理システムとなります。
ユーザー登録
受発注業務の効率化だけでなく、システムを導入することで、コスト削減や製品・資材のステータス可視化のほか、属人化していた受発注情報の共有化による内部不正防止や統制にも役立ちます。
NEWJI DX
製造業に特化したデジタルトランスフォーメーション(DX)の実現を目指す請負開発型のコンサルティングサービスです。AI、iPaaS、および先端の技術を駆使して、製造プロセスの効率化、業務効率化、チームワーク強化、コスト削減、品質向上を実現します。このサービスは、製造業の課題を深く理解し、それに対する最適なデジタルソリューションを提供することで、企業が持続的な成長とイノベーションを達成できるようサポートします。
製造業ニュース解説
製造業、主に購買・調達部門にお勤めの方々に向けた情報を配信しております。
新任の方やベテランの方、管理職を対象とした幅広いコンテンツをご用意しております。
お問い合わせ
コストダウンが利益に直結する術だと理解していても、なかなか前に進めることができない状況。そんな時は、newjiのコストダウン自動化機能で大きく利益貢献しよう!
(β版非公開)