- お役立ち記事
- Practical Management for Production Department Managers
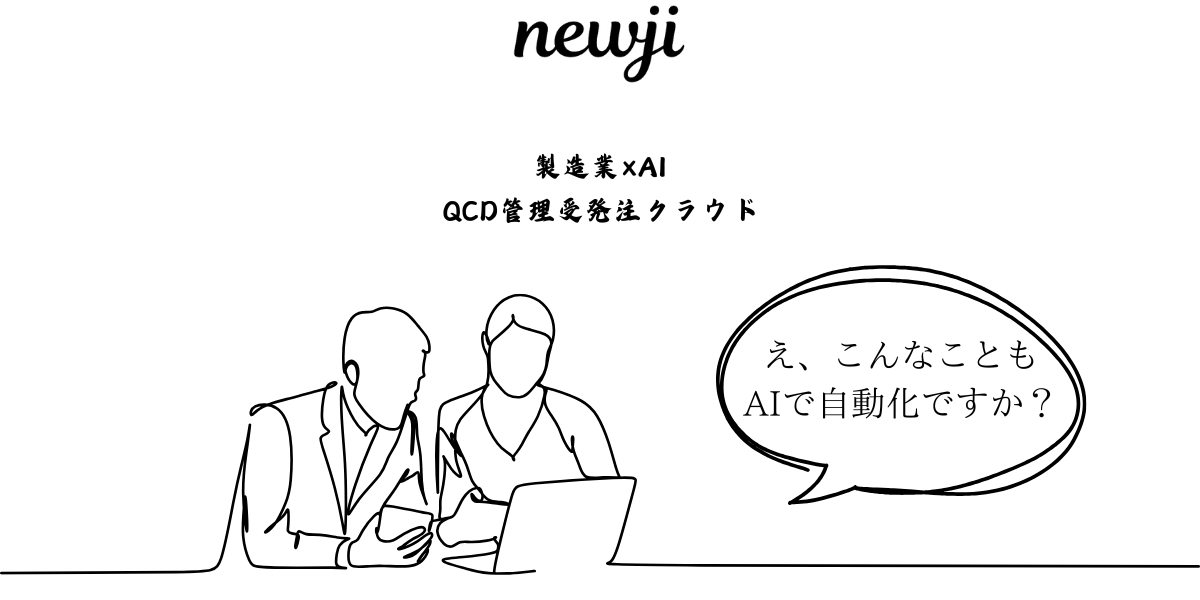
Practical Management for Production Department Managers
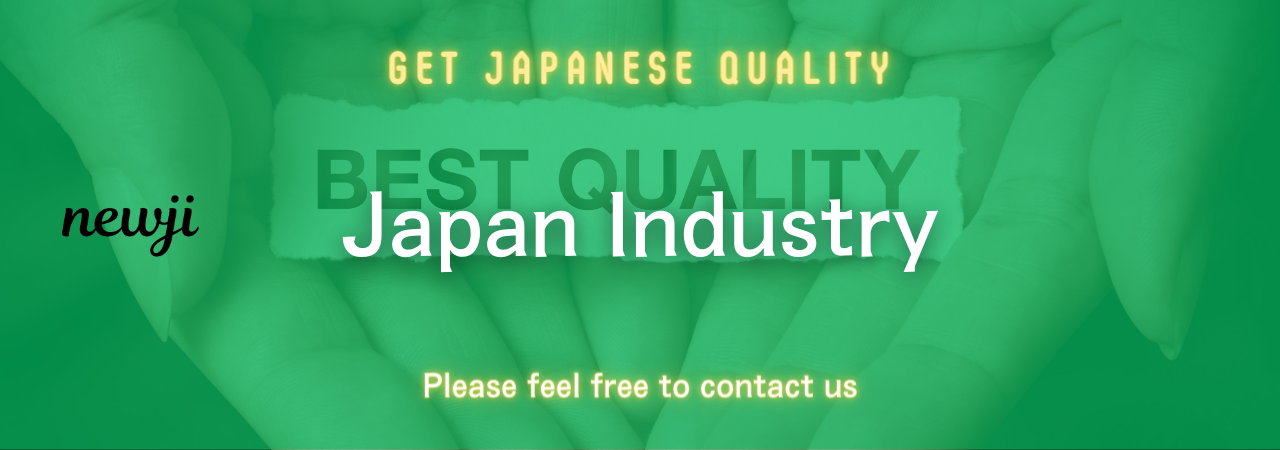
Effective management in a production department is crucial for maintaining smooth operations and ensuring that goals are met consistently. Understanding the roles, responsibilities, and best practices can help managers navigate the complexities of production management. This article delves into the practical aspects of managing a production department, highlighting essential strategies and tips for success.
目次
Understanding the Role of a Production Department Manager
A production department manager is responsible for overseeing the manufacturing processes within a company. They ensure that production runs efficiently, deadlines are met, and that the final products meet quality standards. This role is multi-faceted and demands excellent organizational and leadership skills.
Key Responsibilities
The primary responsibilities of a production department manager include:
– **Planning and Scheduling**: Developing production schedules and ensuring that they align with customer demands and company goals.
– **Resource Management**: Making sure that the necessary resources, including materials, labor, and equipment, are available to meet production targets.
– **Quality Control**: Implementing and maintaining processes that ensure the production of high-quality products.
– **Team Management**: Leading and motivating the production team, including hiring, training, and evaluating staff.
– **Problem Solving**: Addressing any issues that arise during production to prevent delays and maintain efficiency.
– **Budgeting**: Managing the production budget to keep costs within established limits.
Effective Planning and Scheduling
One of the cornerstone responsibilities of a production manager is effective planning and scheduling. This involves creating a detailed production plan that outlines what needs to be produced, how much, and by when.
Developing a Production Plan
A solid production plan should include:
– **Detailed Timelines**: Clear timelines for each stage of production.
– **Resource Allocation**: Information on where and when resources will be deployed.
– **Risk Management**: Strategies to handle potential disruptions or delays.
– **Communication Plan**: Ensuring all stakeholders are informed of their roles and timelines.
Tools for Scheduling
Leveraging various tools and technologies can make scheduling more efficient:
– **Project Management Software**: Tools like Asana, Trello, or Microsoft Project can help in creating and tracking schedules.
– **Production Planning Software**: Specific software designed for manufacturing industries, such as SAP, Oracle, or MRP systems, can optimize resource allocation and workflow.
– **Gantt Charts**: Visual representations of the production schedule can help in understanding the timeline and dependencies.
Resource Management
Efficient use of resources is critical for maintaining productivity and reducing costs. A production manager must balance resources against production demands.
Optimizing Material Use
Strategies for optimizing material use include:
– **Just-in-Time Inventory**: Reducing waste by having materials arrive just as they are needed in the production process.
– **Supplier Relationships**: Building strong relationships with suppliers to ensure reliable and efficient material deliveries.
– **Inventory Management**: Implementing robust inventory management practices to avoid overstocking and stockouts.
Labor Management
Effective labor management involves:
– **Staff Training**: Ensuring that all employees are adequately trained to perform their tasks efficiently.
– **Shift Planning**: Creating shifts that maximize productivity while considering employee well-being.
– **Performance Monitoring**: Keeping track of employee performance and providing feedback and support as needed.
Maintaining Quality Control
Quality control is essential for producing products that meet customer expectations and regulatory standards.
Implementing Quality Assurance Processes
Quality assurance processes might include:
– **Standard Operating Procedures (SOPs)**: Detailed documents that outline how tasks should be performed to maintain quality.
– **Regular Audits**: Conducting periodic audits to ensure compliance with SOPs.
– **Continuous Improvement**: Adopting practices such as Six Sigma or Lean Manufacturing to continuously improve quality.
Employee Involvement in Quality Control
Engaging employees in maintaining quality can be achieved by:
– **Training Sessions**: Regular training on quality standards and procedures.
– **Feedback Mechanisms**: Encouraging employees to provide feedback on quality issues and potential improvements.
– **Recognition Programs**: Recognizing and rewarding employees who consistently contribute to high-quality production.
Effective Team Management
Leading a production team requires strong leadership skills and the ability to foster a collaborative working environment.
Building a Strong Team
Creating a strong team involves:
– **Hiring the Right People**: Recruiting individuals with the necessary skills and a good cultural fit for the team.
– **Team Building Activities**: Organizing activities that promote team cohesion and collaboration.
– **Clear Communication**: Ensuring that team members understand their roles, responsibilities, and the importance of their work.
Motivating the Team
Keeping the team motivated can be managed by:
– **Setting Clear Goals**: Providing clear, achievable goals can give employees a sense of purpose and direction.
– **Providing Support**: Offering the necessary resources and support to help employees succeed.
– **Recognition and Rewards**: Acknowledging hard work and achievements can boost morale and motivation.
Problem Solving and Decision Making
Challenges are inevitable in any production environment. Effective problem-solving and decision-making skills are crucial for keeping production on track.
Identifying Problems Early
Early identification of problems involves:
– **Regular Monitoring**: Keeping a close watch on production processes to spot issues as they arise.
– **Open Communication**: Encouraging employees to report problems immediately.
– **Data Analysis**: Using data analytics to identify trends and potential issues before they become major problems.
Effective Decision-Making Strategies
Making effective decisions requires:
– **Gathering Information**: Collecting all relevant information to understand the problem fully.
– **Considering Options**: Evaluating different solutions and their potential impacts.
– **Making Timely Decisions**: Acting quickly to implement the best solution.
Budget Management
Maintaining a balanced budget is vital for the sustainability of the production department.
Creating a Budget
Creating a production budget involves:
– **Assessing Costs**: Identifying all costs associated with production, including labor, materials, and overhead.
– **Forecasting Demand**: Estimating future demand to allocate resources effectively.
– **Setting Financial Targets**: Establishing clear financial goals to guide spending.
Monitoring and Adjusting the Budget
Regular monitoring and adjusting the budget as needed ensures financial health:
– **Tracking Expenses**: Keeping detailed records of all expenditures.
– **Identifying Deviations**: Noticing when spending deviates from the budget and understanding why.
– **Making Adjustments**: Modifying the budget to address any discrepancies or changes in production needs.
In conclusion, managing a production department involves a combination of strategic planning, resource management, quality control, team leadership, problem-solving, and budgeting. By understanding and implementing these principles, production department managers can ensure that their operations run smoothly and efficiently, meeting both company goals and customer expectations.
資料ダウンロード
QCD調達購買管理クラウド「newji」は、調達購買部門で必要なQCD管理全てを備えた、現場特化型兼クラウド型の今世紀最高の購買管理システムとなります。
ユーザー登録
調達購買業務の効率化だけでなく、システムを導入することで、コスト削減や製品・資材のステータス可視化のほか、属人化していた購買情報の共有化による内部不正防止や統制にも役立ちます。
NEWJI DX
製造業に特化したデジタルトランスフォーメーション(DX)の実現を目指す請負開発型のコンサルティングサービスです。AI、iPaaS、および先端の技術を駆使して、製造プロセスの効率化、業務効率化、チームワーク強化、コスト削減、品質向上を実現します。このサービスは、製造業の課題を深く理解し、それに対する最適なデジタルソリューションを提供することで、企業が持続的な成長とイノベーションを達成できるようサポートします。
オンライン講座
製造業、主に購買・調達部門にお勤めの方々に向けた情報を配信しております。
新任の方やベテランの方、管理職を対象とした幅広いコンテンツをご用意しております。
お問い合わせ
コストダウンが利益に直結する術だと理解していても、なかなか前に進めることができない状況。そんな時は、newjiのコストダウン自動化機能で大きく利益貢献しよう!
(Β版非公開)