- お役立ち記事
- Practical Methods for Quality Improvement and Cost Reduction with the QC Seven Tools
月間76,176名の
製造業ご担当者様が閲覧しています*
*2025年3月31日現在のGoogle Analyticsのデータより
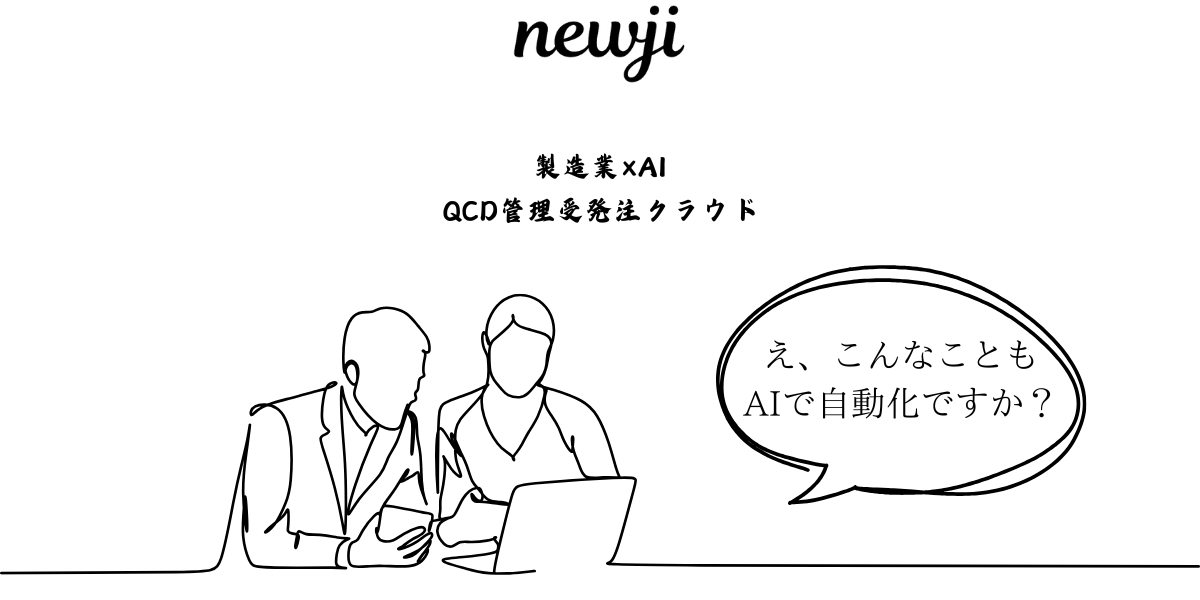
Practical Methods for Quality Improvement and Cost Reduction with the QC Seven Tools
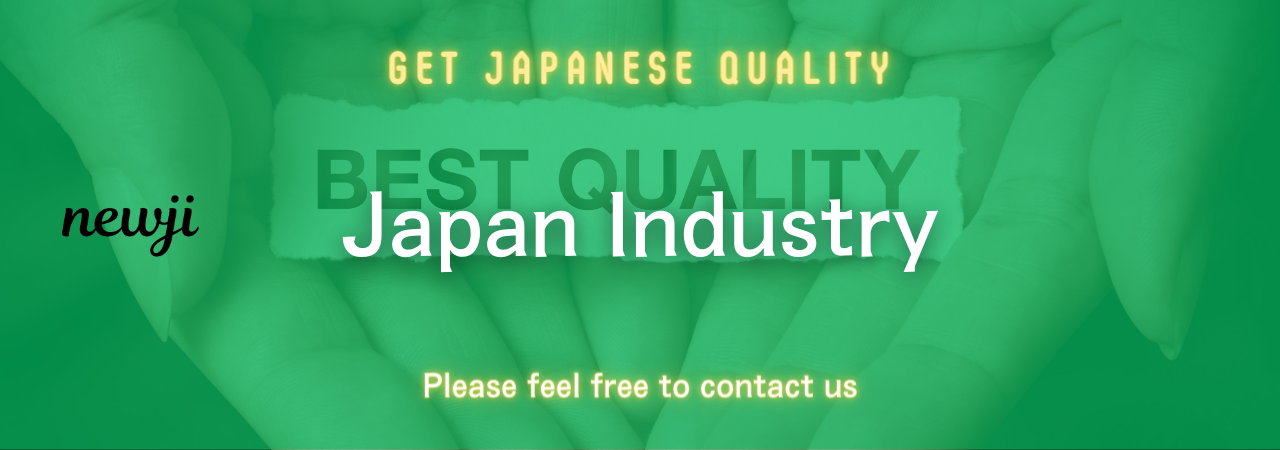
目次
Understanding the QC Seven Tools
Before diving into practical methods for quality improvement and cost reduction, it’s essential to understand what the QC Seven Tools are.
These tools are a set of techniques used in quality management for addressing and solving problems.
Initially developed in Japan during the 1950s, the QC Seven Tools are widely recognized for their efficiency in various industries.
The seven tools include the Cause-and-Effect Diagram, Control Charts, Check Sheets, Pareto Chart, Histogram, Scatter Diagram, and Flow Chart.
Each tool has a specific application and can be used independently or in tandem, depending on the situation.
By applying these tools, companies can systematically identify defects, improve processes, and reduce unnecessary costs.
Cause-and-Effect Diagram: Identifying Root Causes
Also known as the Fishbone or Ishikawa diagram, the Cause-and-Effect Diagram helps teams track down the root causes of problems.
It visually lays out potential causes under broad categories like manpower, materials, machines, and methods.
By constructing a diagram for each issue, teams can systematically explore all possible causes.
This allows for a thorough investigation, ensuring that all angles are covered before deciding on a solution.
An effective way to use this tool is during brainstorming sessions.
Gather your team and identify all factors that could contribute to the problem.
This open dialogue can lead to insights that might not have been considered initially.
As a result, you can target the root cause directly rather than applying temporary fixes.
Control Charts: Monitoring Process Performance
Control Charts are instrumental in monitoring and maintaining consistent process performance.
They display variations over time, helping you to distinguish between common cause variations and special cause variations.
Common cause variations are inherent to a process, while special cause variations indicate an issue that needs attention.
With Control Charts, you can spot trends and outliers quickly, allowing for timely interventions.
For instance, if a process starts to drift out of control, you can investigate and correct it before it leads to significant defects or losses.
Regularly reviewing Control Charts enable continuous process improvements and keeps your operations efficient and cost-effective.
Check Sheets: Simple Data Collection
Check Sheets are among the simplest yet most powerful QC tools, tailored for data collection and analysis.
They are designed to gather quantitative or qualitative data, focusing on frequencies or patterns of specific event occurrences.
The key is to keep the Check Sheet straightforward and user-friendly.
When workers find recording data quick and easy, consistency in data collection improves.
This accurate data forms the basis for further analysis and decision-making.
For example, you might use a Check Sheet to document when and where defects occur in production.
By analyzing this data, you can identify patterns or trends that could indicate underlying issues.
Pareto Chart: Focusing on What Matters Most
The Pareto Chart is based on the Pareto Principle, often summarized as the “80/20 Rule” – 80% of problems are often due to 20% of causes.
This tool helps you identify the few areas where improvements will yield the most significant impact.
The Pareto Chart is a type of bar chart that includes a line graph; the bars represent the frequency of problems, while the line shows the cumulative totals.
This visualization makes it easy to determine which problems warrant closer attention and resources.
By addressing these critical areas first, you optimize the impact of your quality improvement efforts and consequently reduce costs associated with defects and inefficiencies.
Histogram: Understanding Data Distribution
Histograms illustrate the distribution of a set of data, offering insights into the variability of a process.
By constructing a Histogram, you can see how data is spread and identify patterns or irregularities.
For example, a Histogram showing a bell-shaped curve might indicate normal distribution, while a skewed pattern could reveal a bias in the process.
Understanding these variations is crucial for identifying process strengths and weaknesses.
This understanding allows you to standardize and refine processes, ensuring they are as efficient and cost-effective as possible.
Scatter Diagram: Revealing Relationships Between Variables
A Scatter Diagram explores potential relationships between two variables by plotting them on a graph.
The visual representation helps to determine if changes in one variable correlate with alterations in another.
For example, you might assess if different temperatures affect product quality.
By plotting temperature against quality data, the Scatter Diagram could reveal a positive, negative, or no correlation.
Identifying these relationships is vital for informed decision-making.
Understanding the factors that influence quality can lead to innovative solutions and adjustments in processes to enhance efficiency and reduce costs.
Flow Chart: Mapping Out Processes
Flow Charts are diagrams that breakdown processes into steps, providing an overview that can identify inefficiencies or issues needing improvement.
They help visualize each step in a process, simplifying complex sequences and enhancing understanding among team members.
By employing Flow Charts, you can pinpoint stages that cause bottlenecks, delays, or errors.
This map allows for clearer communication across different levels of your organization and aids in refining processes to be more efficient.
Identifying redundancies or unnecessary steps can significantly reduce costs and improve productivity.
Integrating the QC Seven Tools for Success
Integrating these tools into your quality control approach allows your organization to tackle quality improvement and cost reduction systematically.
Start by identifying current challenges or goals, and then select the most appropriate QC tools for your situation.
Combining tools can often provide broader insights—for instance, using a Check Sheet to collect data and then visualize it with a Control Chart.
By fostering a continuous improvement mindset, organizations can stay competitively agile and enhance their product quality and operational efficiency.
Commitment to using these tools can lead to higher customer satisfaction and loyalty, driving sustained business growth.
Achieving quality improvement and cost reduction is a reflection of a culture that values precision, efficiency, and proactive management.
Adapting these methodologies can yield significant advantages in any industry, paving the way for innovation and sustainable success.
資料ダウンロード
QCD管理受発注クラウド「newji」は、受発注部門で必要なQCD管理全てを備えた、現場特化型兼クラウド型の今世紀最高の受発注管理システムとなります。
ユーザー登録
受発注業務の効率化だけでなく、システムを導入することで、コスト削減や製品・資材のステータス可視化のほか、属人化していた受発注情報の共有化による内部不正防止や統制にも役立ちます。
NEWJI DX
製造業に特化したデジタルトランスフォーメーション(DX)の実現を目指す請負開発型のコンサルティングサービスです。AI、iPaaS、および先端の技術を駆使して、製造プロセスの効率化、業務効率化、チームワーク強化、コスト削減、品質向上を実現します。このサービスは、製造業の課題を深く理解し、それに対する最適なデジタルソリューションを提供することで、企業が持続的な成長とイノベーションを達成できるようサポートします。
製造業ニュース解説
製造業、主に購買・調達部門にお勤めの方々に向けた情報を配信しております。
新任の方やベテランの方、管理職を対象とした幅広いコンテンツをご用意しております。
お問い合わせ
コストダウンが利益に直結する術だと理解していても、なかなか前に進めることができない状況。そんな時は、newjiのコストダウン自動化機能で大きく利益貢献しよう!
(β版非公開)