- お役立ち記事
- Practical Methods for Workplace Organization and Productivity Improvement through 5S Activities
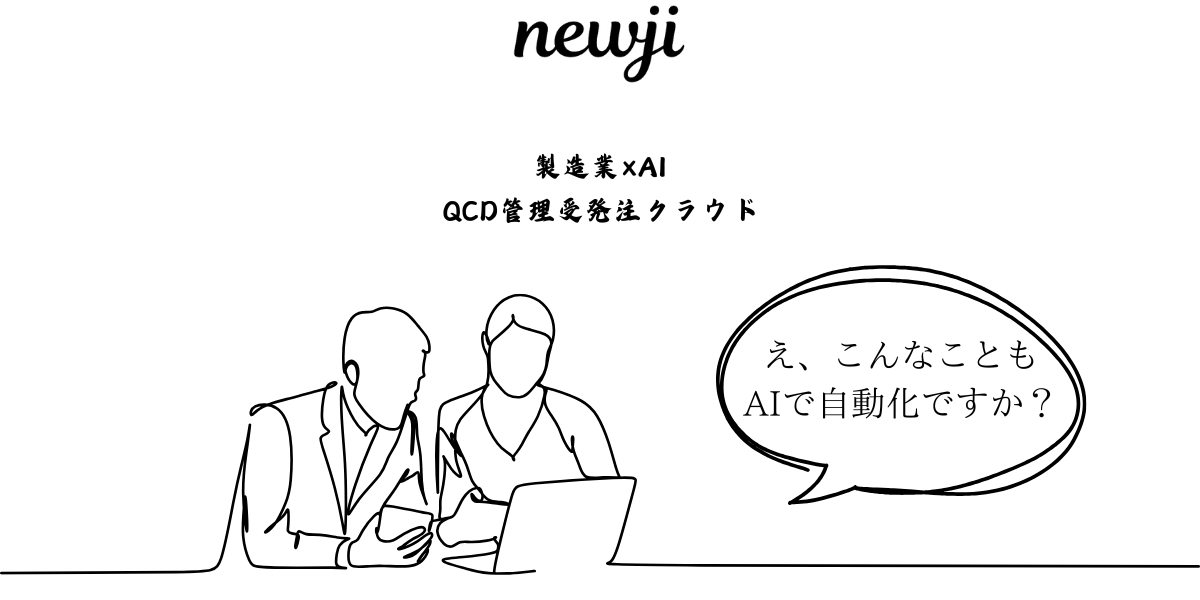
Practical Methods for Workplace Organization and Productivity Improvement through 5S Activities
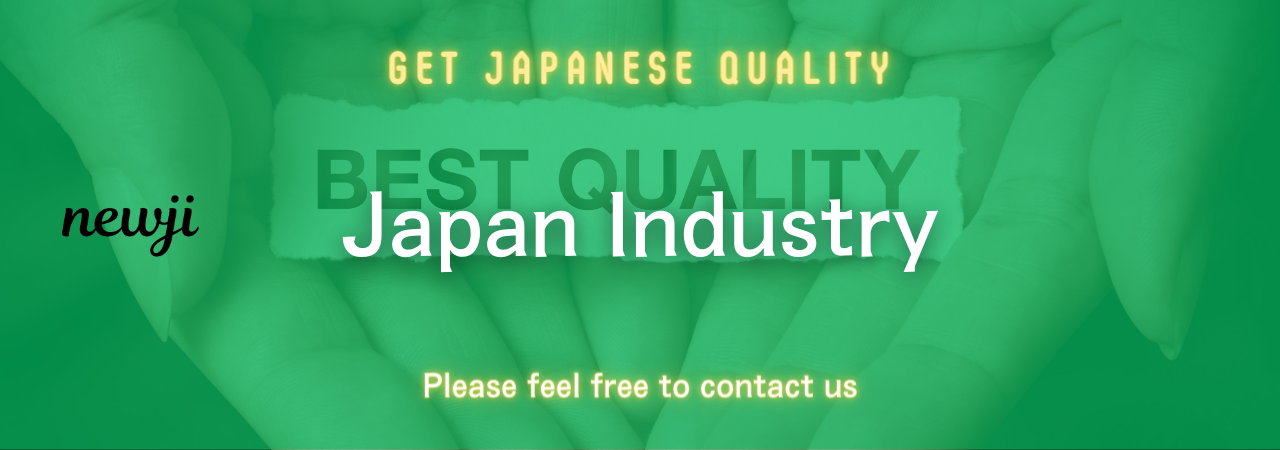
目次
Understanding the 5S Methodology
The 5S methodology is an innovative system aimed at improving workplace organization and productivity.
Its origins trace back to Japan, specifically in the manufacturing industry, but it is now widely adopted across various sectors worldwide.
The name “5S” represents five Japanese words that embody five critical steps in the workplace organization: Seiri, Seiton, Seiso, Seiketsu, and Shitsuke, which respectively translate to Sort, Set in Order, Shine, Standardize, and Sustain.
Each of these steps plays a fundamental role in maintaining an organized, efficient, and safe working environment.
By adopting 5S activities, businesses can streamline operations, minimize waste, and enhance productivity, ultimately improving the overall work environment.
Step 1: Sort (Seiri)
The first step, Sort (Seiri), focuses on removing unnecessary items from the workspace.
This process involves evaluating the tools, supplies, and materials within the area and distinguishing between what is essential and non-essential.
Items that are not required for daily operations should be removed to free up space and reduce potential clutter.
Employing the “Red Tag” technique can be beneficial here; items are labeled with a red tag and evaluated over a specific period to determine their necessity.
If they continue to remain unused, it’s a clear sign that these items should be discarded or relocated.
Step 2: Set in Order (Seiton)
The Set in Order (Seiton) step aims to organize and arrange the necessary items efficiently.
After sorting and removing unnecessary items, it’s time to assign designated locations for each tool, material, and supply.
The goal is to ensure that everything needed for a task is readily accessible, reducing the time spent searching and thereby enhancing productivity.
Visual management strategies like shadow boards or labeled shelving can be employed to help maintain organization and ensure items are returned to their proper place after use.
Step 3: Shine (Seiso)
Shine (Seiso) involves cleaning the workplace and maintaining it regularly.
Beyond mere tidiness, this step’s objective is to create a clean and safe environment that boosts morale and prevents hazards.
Regular cleaning and maintenance also help identify any defects in equipment or safety hazards early, allowing timely rectification and minimizing potential disruptions.
Involving everyone in the organization in the cleaning process fosters a sense of ownership and responsibility towards the work environment.
Step 4: Standardize (Seiketsu)
Standardize (Seiketsu) is about creating a consistent, organized approach to each day’s tasks.
Here, procedures and schedules are developed to ensure that the first three steps are repeated regularly and become second nature to everyone involved.
This is where checklists, documentation, and visual reminders play a pivotal role.
By establishing consistent methods for maintaining order and cleanliness, employees know what is expected, leading to fewer mistakes and a more efficient workflow.
Step 5: Sustain (Shitsuke)
Sustain (Shitsuke) is the final step that focuses on maintaining and improving the established 5S processes.
It’s about fostering a long-term culture of discipline and continuous improvement within the workplace.
Training sessions, audits, and feedback systems should be in place to reinforce the habits evolved from the 5S principles.
Leadership plays a critical role here; management’s commitment to supporting and developing these processes encourages employees to engage and participate willingly.
Benefits of Implementing 5S
By implementing 5S, organizations reap numerous benefits that extend beyond simple tidiness.
One primary advantage is increased efficiency.
Employees spend less time looking for tools and materials when everything is organized and in its place, which enhances productivity.
Another benefit is improved safety, as a clean and orderly workplace reduces the risks of accidents and injuries.
Employees naturally develop a sense of pride and accountability when working in an organized environment, contributing to higher job satisfaction and morale.
Additionally, 5S can positively impact a company’s bottom line.
Reduced waste, improved workflow, and lower inventory costs can lead to significant savings.
Enhanced efficiency and productivity translate into higher-quality outputs, giving the company a competitive edge.
Challenges and Solutions
Despite its many benefits, implementing 5S can pose challenges, particularly in changing the mindset and culture of an organization.
Resistance to change and a lack of commitment from staff are common obstacles.
To tackle these challenges, leadership must be committed to the process and willing to communicate its benefits effectively.
Providing training and continuous support can help ease the transition and ensure alignment across all levels of the organization.
Regular audits and feedback loops can identify areas of improvement and keep the process dynamic and engaging.
Conclusion
5S is a powerful tool for any business looking to enhance workplace organization and productivity.
By following its structured methodology, organizations can create a more efficient, safe, and pleasant work environment.
Investing time and resources into implementing 5S principles can lead to significant improvements in productivity, quality, safety, and employee satisfaction.
With a strong commitment from both management and employees, 5S can be a cornerstone of a company’s continuous improvement efforts towards achieving operational excellence.
資料ダウンロード
QCD調達購買管理クラウド「newji」は、調達購買部門で必要なQCD管理全てを備えた、現場特化型兼クラウド型の今世紀最高の購買管理システムとなります。
ユーザー登録
調達購買業務の効率化だけでなく、システムを導入することで、コスト削減や製品・資材のステータス可視化のほか、属人化していた購買情報の共有化による内部不正防止や統制にも役立ちます。
NEWJI DX
製造業に特化したデジタルトランスフォーメーション(DX)の実現を目指す請負開発型のコンサルティングサービスです。AI、iPaaS、および先端の技術を駆使して、製造プロセスの効率化、業務効率化、チームワーク強化、コスト削減、品質向上を実現します。このサービスは、製造業の課題を深く理解し、それに対する最適なデジタルソリューションを提供することで、企業が持続的な成長とイノベーションを達成できるようサポートします。
オンライン講座
製造業、主に購買・調達部門にお勤めの方々に向けた情報を配信しております。
新任の方やベテランの方、管理職を対象とした幅広いコンテンツをご用意しております。
お問い合わせ
コストダウンが利益に直結する術だと理解していても、なかなか前に進めることができない状況。そんな時は、newjiのコストダウン自動化機能で大きく利益貢献しよう!
(Β版非公開)