- お役立ち記事
- Practical methods of lead time management and emergency procurement to prevent material shortages
月間76,176名の
製造業ご担当者様が閲覧しています*
*2025年3月31日現在のGoogle Analyticsのデータより
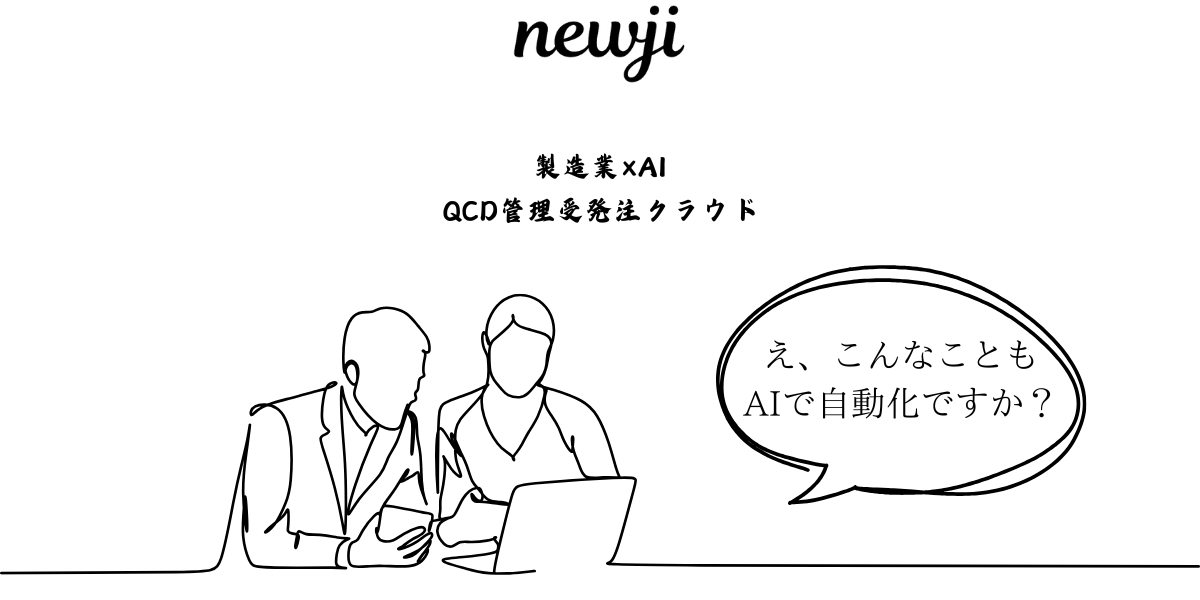
Practical methods of lead time management and emergency procurement to prevent material shortages
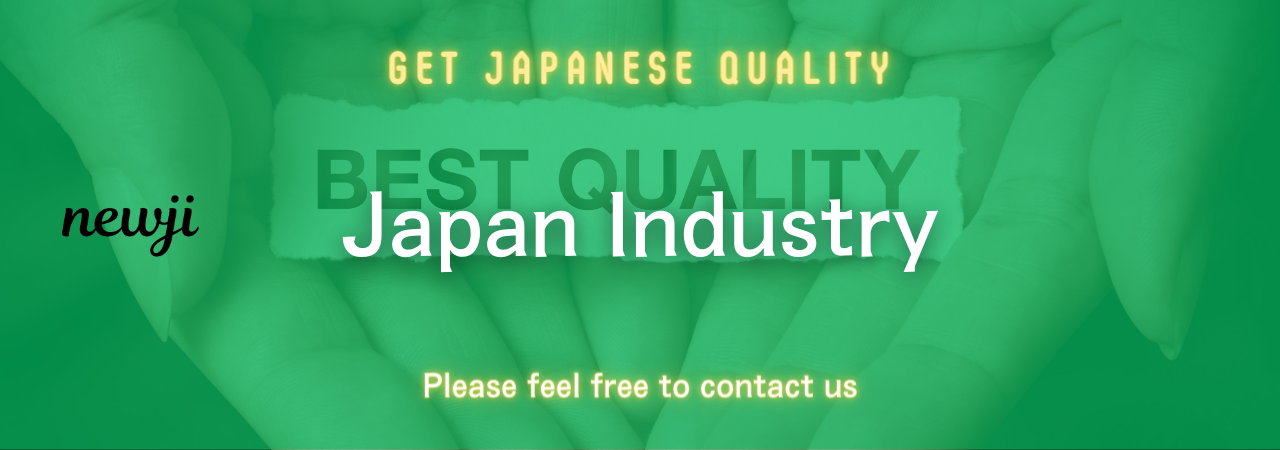
目次
Understanding Lead Time Management
Managing lead times effectively is crucial for businesses to maintain a steady flow of materials and prevent shortages.
Lead time refers to the period between initiating a process and completing it.
In supply chain management, it is the time taken from placing an order to receiving the materials.
Several factors contribute to lead times, including supplier reliability, inventory management, and transportation logistics.
To manage these effectively, businesses need to analyze each aspect, identify bottlenecks, and streamline processes.
Understanding these components helps companies anticipate potential delays and develop strategies to minimize their impact.
Techniques for Lead Time Reduction
Reducing lead time can significantly impact a company’s efficiency and ability to meet customer demands.
Here are some practical methods for lead time reduction:
Strengthening Supplier Relationships
Building strong, reliable relationships with suppliers can help reduce lead times.
Regular communication ensures that suppliers understand your needs and priorities, allowing them to allocate resources effectively.
Negotiate contracts that include shorter lead times as a priority and hold suppliers accountable for delays.
Implementing Just-In-Time (JIT) Inventory
JIT inventory management minimizes lead time by ordering materials only when needed.
This strategy reduces excess inventory and storage costs, but requires precise coordination with suppliers.
Ensure that your suppliers can meet the quick turnaround times required by JIT systems.
Optimizing Transportation
Streamlining transportation logistics, such as choosing the best routes and carriers, can significantly reduce lead times.
Consider using air freight for critical materials when time is a key factor.
Digitize and automate logistics operations to minimize the risk of human error and delays.
Emergency Procurement Strategies
Despite the best lead time management efforts, unexpected material shortages can occur.
To address these, companies need effective emergency procurement strategies.
Establishing a Contingency Plan
A well-developed contingency plan is essential for managing emergencies.
Identify critical materials beforehand and establish alternate suppliers who can provide those items at short notice.
Make sure these suppliers understand your quality standards and deliver timelines, so they can act swiftly and effectively.
Maintaining a Safety Stock
Safety stock acts as a buffer against supply chain disruptions.
It involves keeping a minimum quantity of critical materials in reserve.
Calculate safety stock levels based on past demand fluctuations and lead time uncertainties.
Use data analytics to foresee periods where demand may exceed supply and adjust safety stock levels accordingly.
Leveraging Technology
Implement technology solutions like ERP (Enterprise Resource Planning) systems and AI-driven analytics tools to gain visibility into supply chain operations.
These tools can predict potential shortages and help formulate proactive measures.
Employ demand forecasting tools to understand consumption patterns and adjust procurement schedules in advance.
Benefits of Effective Lead Time and Emergency Procurement Management
By mastering lead time and emergency procurement management, businesses can reap numerous benefits.
Improved Customer Satisfaction
Timely delivery of products increases customer satisfaction and boosts loyalty.
When customers know that a company consistently meets their needs, they are more likely to return and order again.
Cost Efficiency
Effective management reduces excess inventory and storage costs.
It also minimizes the risk of rush fees due to last-minute procurement and shipping.
Competitive Advantage
Companies that deliver on time maintain a strong market reputation.
This reliability positions them as leaders within their industry, setting them apart from competitors who may not prioritize effective material management.
Conclusion
Practical methods of lead time management and emergency procurement are essential tools in preventing material shortages.
By optimizing supplier relationships, refining inventory strategies, and using advanced technologies, businesses can minimize disruptions and bolster their operations.
Adopting these practices not only facilitates smooth supply chain functioning but also enhances a company’s reliability and reputation.
This ensures long-term success and a steady growth trajectory, even in the face of potential supply chain challenges.
資料ダウンロード
QCD管理受発注クラウド「newji」は、受発注部門で必要なQCD管理全てを備えた、現場特化型兼クラウド型の今世紀最高の受発注管理システムとなります。
ユーザー登録
受発注業務の効率化だけでなく、システムを導入することで、コスト削減や製品・資材のステータス可視化のほか、属人化していた受発注情報の共有化による内部不正防止や統制にも役立ちます。
NEWJI DX
製造業に特化したデジタルトランスフォーメーション(DX)の実現を目指す請負開発型のコンサルティングサービスです。AI、iPaaS、および先端の技術を駆使して、製造プロセスの効率化、業務効率化、チームワーク強化、コスト削減、品質向上を実現します。このサービスは、製造業の課題を深く理解し、それに対する最適なデジタルソリューションを提供することで、企業が持続的な成長とイノベーションを達成できるようサポートします。
製造業ニュース解説
製造業、主に購買・調達部門にお勤めの方々に向けた情報を配信しております。
新任の方やベテランの方、管理職を対象とした幅広いコンテンツをご用意しております。
お問い合わせ
コストダウンが利益に直結する術だと理解していても、なかなか前に進めることができない状況。そんな時は、newjiのコストダウン自動化機能で大きく利益貢献しよう!
(β版非公開)