- お役立ち記事
- Practical methods of material cost analysis and purchasing cost management that mid-level employees should know
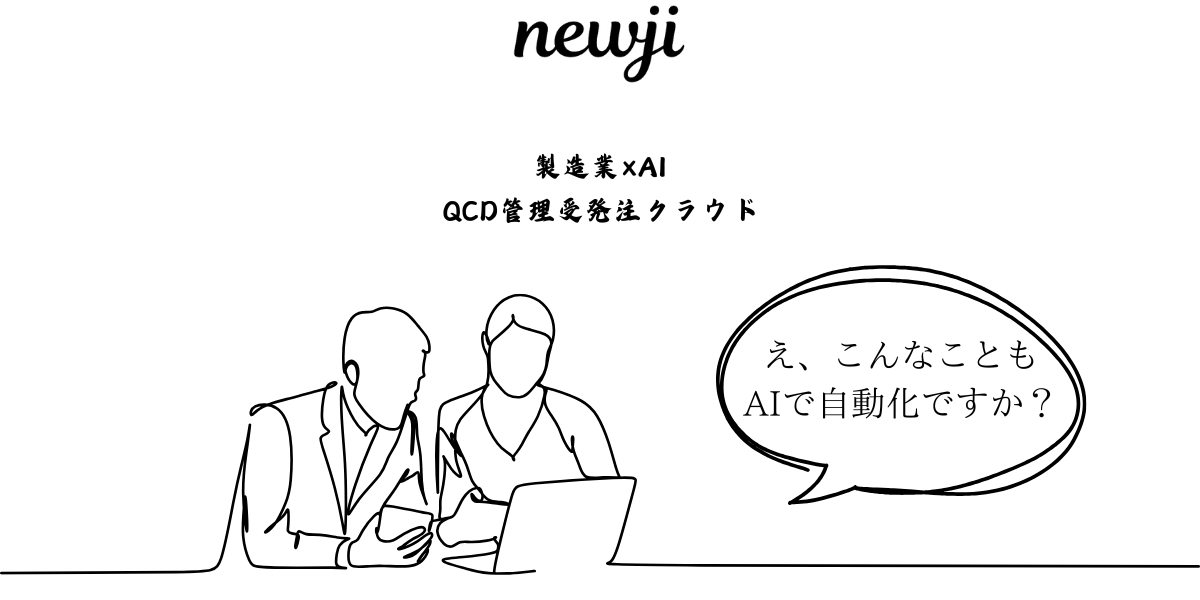
Practical methods of material cost analysis and purchasing cost management that mid-level employees should know
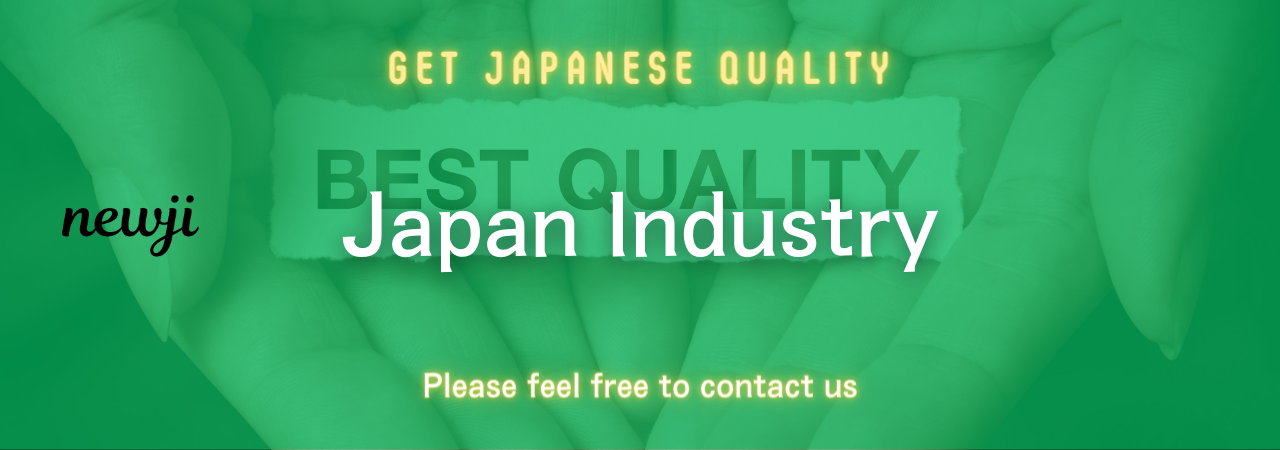
目次
Understanding Material Cost Analysis
Material cost analysis is a crucial aspect of managing expenses for any company that deals with production, manufacturing, or any form of goods creation.
It involves the detailed examination and evaluation of the costs associated with raw materials and other inputs necessary for production.
This process helps organizations to understand the composition of their material costs, identify areas where they can potentially reduce expenses, and improve overall cost efficiency.
The Importance of Material Cost Analysis
By performing a thorough material cost analysis, companies can achieve several objectives.
Firstly, they can identify cost-saving opportunities by analyzing different components of their costs and finding less expensive alternatives.
Secondly, understanding the cost structure allows organizations to forecast expenses more accurately, aiding in better budgeting and financial planning.
Lastly, it helps in setting competitive prices for products by ensuring that all costs are considered and that pricing strategies reflect the actual expenses incurred.
Practical Methods for Conducting Material Cost Analysis
One effective approach to material cost analysis is the use of a cost breakdown structure.
This involves dissecting the total cost into different components, such as direct materials, labor, and overheads, to better understand each element’s contribution.
Such an analysis helps identify areas where costs exceed expectations and where adjustments are possible.
Another method is benchmarking, which involves comparing your company’s material costs against industry standards or competitors.
This can highlight discrepancies and opportunities for cost reduction by adopting best practices from others in the industry.
Utilizing Activity-Based Costing
Activity-Based Costing (ABC) is a more detailed method of analyzing material costs.
ABC assigns costs to products based on the activities required to produce them rather than a simple allocation based on volume or direct labor hours.
This method provides more accurate insights into how resources are consumed and highlights inefficiencies in the production process that might otherwise be overlooked.
Effective Purchasing Cost Management Strategies
Beyond analyzing material costs, effective purchasing cost management is vital for maintaining a company’s profitability.
This involves strategic planning and control of procurement activities to acquire goods and services at the best possible prices while ensuring quality and delivery timelines.
Building Strong Supplier Relationships
One of the most effective strategies in purchasing cost management is developing strong relationships with suppliers.
When suppliers and purchasers work as partners, rather than adversaries, companies can negotiate better terms, gain insights into market trends, and enjoy reliable supply chains.
Building trust with suppliers can lead to cost advantages, such as volume discounts, favorable credit terms, or priority access to materials during shortages.
Leveraging Technology in Procurement
The use of technology, such as e-procurement systems, can streamline purchasing processes and enhance cost management.
These systems automate routine tasks, provide real-time data on purchase orders and inventory levels, and enable better decision-making through data analytics.
By enhancing efficiency and improving visibility into procurement activities, companies can identify cost-saving opportunities and significantly reduce purchasing costs.
Incorporating Cost Control Measures
In addition to strategic purchasing, implementing cost control measures can further help manage material and purchasing costs.
Companies should regularly review and update their procurement policies to adapt to changes in market conditions and supplier capabilities.
Ensuring compliance with these policies minimizes risk and ensures that purchasing activities are aligned with organizational goals.
Implementing Just-In-Time Inventory Management
Adopting Just-In-Time (JIT) inventory management techniques can reduce costs associated with storage and inventory holding.
By coordinating with suppliers to receive materials and components only as they are needed for production, companies can minimize overstocking and reduce warehousing expenses.
However, it is crucial to have reliable suppliers and effective logistics systems in place to reap the benefits of JIT without risking production delays.
Conclusion
Mid-level employees involved in finance, procurement, or supply chain management should develop a robust understanding of material cost analysis and purchasing cost management.
These skills are invaluable in identifying cost-saving opportunities, optimizing production efficiency, and enhancing a company’s competitive position in the market.
By employing methods such as cost breakdown structures, activity-based costing, strategic supplier relationships, and leveraging technology, companies can effectively manage their material and purchasing costs and drive long-term profitability.
Staying informed about best practices and continuously seeking efficiencies in these areas can lead to significant improvements in overall business performance.
資料ダウンロード
QCD調達購買管理クラウド「newji」は、調達購買部門で必要なQCD管理全てを備えた、現場特化型兼クラウド型の今世紀最高の購買管理システムとなります。
ユーザー登録
調達購買業務の効率化だけでなく、システムを導入することで、コスト削減や製品・資材のステータス可視化のほか、属人化していた購買情報の共有化による内部不正防止や統制にも役立ちます。
NEWJI DX
製造業に特化したデジタルトランスフォーメーション(DX)の実現を目指す請負開発型のコンサルティングサービスです。AI、iPaaS、および先端の技術を駆使して、製造プロセスの効率化、業務効率化、チームワーク強化、コスト削減、品質向上を実現します。このサービスは、製造業の課題を深く理解し、それに対する最適なデジタルソリューションを提供することで、企業が持続的な成長とイノベーションを達成できるようサポートします。
オンライン講座
製造業、主に購買・調達部門にお勤めの方々に向けた情報を配信しております。
新任の方やベテランの方、管理職を対象とした幅広いコンテンツをご用意しております。
お問い合わせ
コストダウンが利益に直結する術だと理解していても、なかなか前に進めることができない状況。そんな時は、newjiのコストダウン自動化機能で大きく利益貢献しよう!
(Β版非公開)