- お役立ち記事
- Practical Plastic Product Design: Understanding the Process from Order to Design and Mass Production, Along with Quality Knowledge
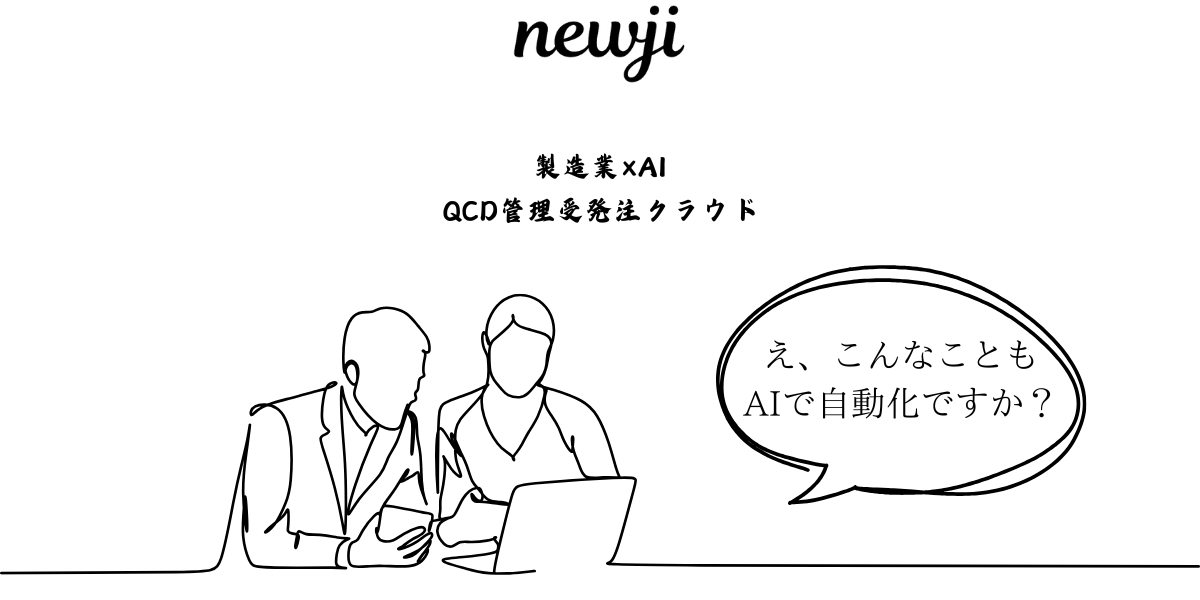
Practical Plastic Product Design: Understanding the Process from Order to Design and Mass Production, Along with Quality Knowledge
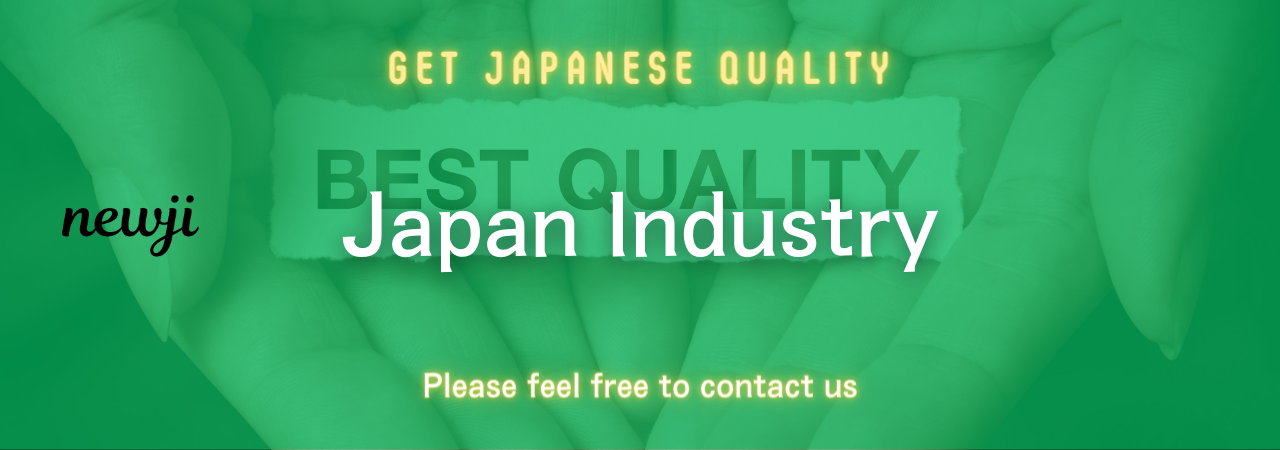
目次
Understanding the Basics of Plastic Product Design
When it comes to creating plastic products, the journey from concept to mass production is both intricate and fascinating.
It involves several steps that ensure the final product is not only functional but also of high quality.
Understanding this process can be beneficial for anyone involved in product design, manufacturing, or even as a consumer interested in knowing how things are made.
Step 1: Receiving and Understanding the Order
The first step in plastic product design is receiving and understanding the client’s order.
This stage is crucial as it sets the foundation for the entire project.
A clear and detailed order will include specifications like product dimensions, functionalities, materials to be used, and any specific requirements from the client.
At this point, communication between the client and the design team is vital.
Discussing expectations, timelines, and budget constraints will help avoid confusion later.
Step 2: Conceptualizing the Design
After understanding the order, the design team begins to conceptualize the product.
This phase involves brainstorming and sketching out initial ideas.
Designers often use CAD (Computer-Aided Design) software to create precise digital models.
These models help in visualizing the product, making necessary adjustments, and ensuring that the design meets the client’s requirements.
Conceptualizing also allows the team to foresee potential issues and address them early in the process.
Step 3: Detailed Design and Prototyping
Once the concept is finalized, designers move to the detailed design phase.
In this stage, every aspect of the product is fine-tuned.
This includes determining the exact dimensions, selecting appropriate materials, and finalizing the product’s aesthetics.
Prototyping is an essential part of this phase.
A prototype is a physical representation of the design that allows for practical testing and evaluation.
Prototypes can be made using various materials, but 3D printing is a common method used in this stage.
Testing the prototype helps identify any flaws or areas for improvement before moving to mass production.
The Production Process
Step 4: Preparing for Mass Production
After a successful prototype evaluation, preparations for mass production begin.
This involves setting up the production line, which includes making or sourcing the necessary molds and selecting the right machinery.
Molds are critical in plastic product production as they determine the shape and precision of the final product.
High-quality molds ensure consistency and efficiency in the production process.
Step 5: Production
Production can begin once everything is set up.
Plastic products are typically manufactured using methods like injection molding, blow molding, or extrusion.
Injection molding involves injecting molten plastic into a mold where it cools and hardens into the desired shape.
Blow molding is used for hollow products like bottles and containers.
Extrusion pushes plastic through a die to create long shapes like pipes or sheets.
Each method is chosen based on the specific requirements of the product being made.
Throughout the production phase, consistent quality checks are performed to ensure that every item meets the established standards.
Ensuring Quality in Plastic Products
Maintaining Quality Standards
Quality is a critical aspect of plastic product design and production.
To maintain high standards, a company must implement rigorous quality control measures.
This includes regular inspections, testing, and adhering to industry standards and regulations.
Quality control helps in identifying defects early, reducing waste, and ensuring customer satisfaction.
Material Selection
Selecting the right material is integral to the quality of the final product.
Different plastics have various properties, and choosing the wrong one can affect the product’s strength, durability, and cost.
For example, ABS plastic is known for its robustness and is commonly used in automotive and toy industries.
On the other hand, PET plastic is lightweight and often used for packaging, especially in the food industry.
Understanding the characteristics of different materials helps in making informed decisions that enhance the product’s functionality and longevity.
Testing and Certification
Before a plastic product reaches the market, it must undergo thorough testing to ensure safety and performance.
These tests check for factors like durability, heat resistance, and chemical stability.
Some industries require specific certifications to validate that the product meets all regulatory requirements.
These certifications are crucial for building consumer trust and opening up markets, especially in sectors like healthcare and food packaging where safety standards are stringent.
Conclusion
The process of plastic product design, from the initial order to mass production, is a meticulously planned journey.
Each step, from conceptualizing the design to ensuring the highest quality standards, plays a vital role in creating a successful product.
By understanding this process, businesses can better manage their projects, avoid common pitfalls, and ultimately deliver products that meet both their needs and their customers’ expectations.
Whether you are a budding designer, a manufacturer, or just curious, knowing these steps enriches your appreciation of the endless possibilities in plastic product design.
資料ダウンロード
QCD調達購買管理クラウド「newji」は、調達購買部門で必要なQCD管理全てを備えた、現場特化型兼クラウド型の今世紀最高の購買管理システムとなります。
ユーザー登録
調達購買業務の効率化だけでなく、システムを導入することで、コスト削減や製品・資材のステータス可視化のほか、属人化していた購買情報の共有化による内部不正防止や統制にも役立ちます。
NEWJI DX
製造業に特化したデジタルトランスフォーメーション(DX)の実現を目指す請負開発型のコンサルティングサービスです。AI、iPaaS、および先端の技術を駆使して、製造プロセスの効率化、業務効率化、チームワーク強化、コスト削減、品質向上を実現します。このサービスは、製造業の課題を深く理解し、それに対する最適なデジタルソリューションを提供することで、企業が持続的な成長とイノベーションを達成できるようサポートします。
オンライン講座
製造業、主に購買・調達部門にお勤めの方々に向けた情報を配信しております。
新任の方やベテランの方、管理職を対象とした幅広いコンテンツをご用意しております。
お問い合わせ
コストダウンが利益に直結する術だと理解していても、なかなか前に進めることができない状況。そんな時は、newjiのコストダウン自動化機能で大きく利益貢献しよう!
(Β版非公開)