- お役立ち記事
- Practical points for machine safety design methods and intrinsically safe design
月間76,176名の
製造業ご担当者様が閲覧しています*
*2025年3月31日現在のGoogle Analyticsのデータより
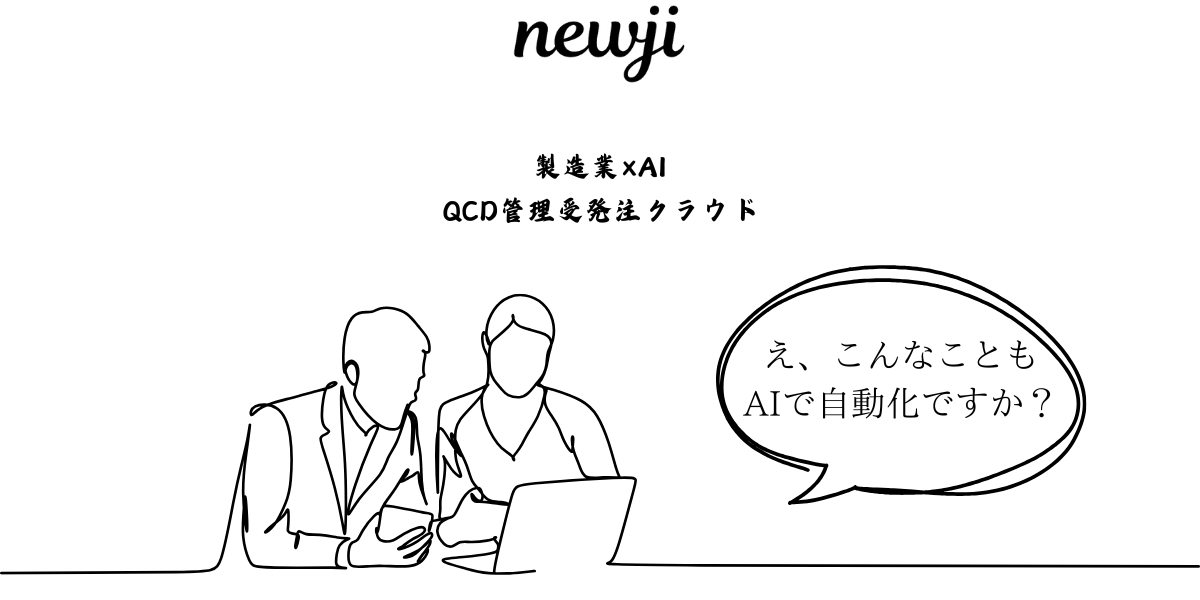
Practical points for machine safety design methods and intrinsically safe design
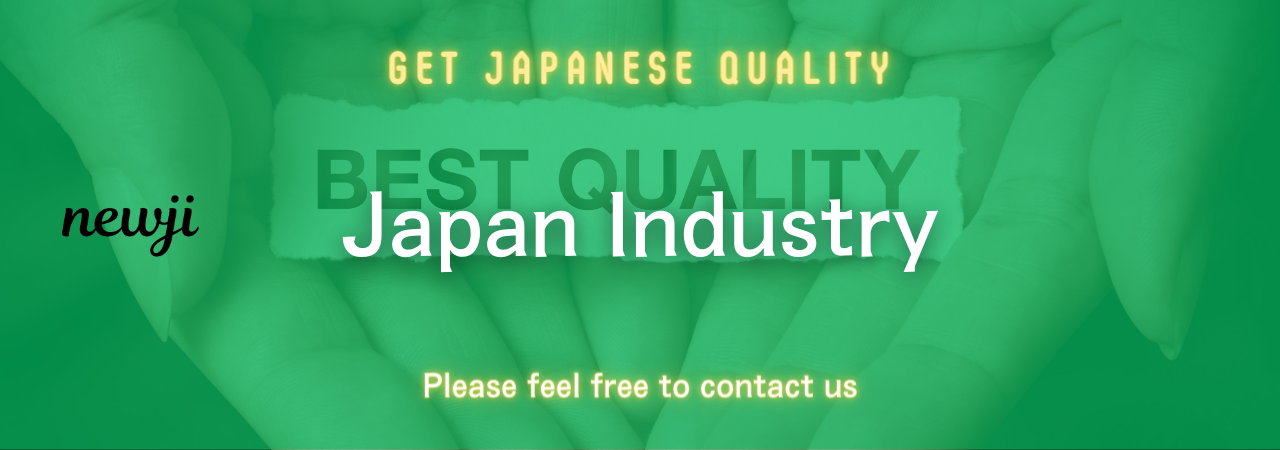
目次
Understanding Machine Safety Design
Machine safety design is a critical aspect of engineering that ensures the safe operation of equipment and machinery.
It involves the integration of safety principles and technologies into the design process to minimize risks to operators and the environment.
Designing for safety is not just about compliance with legal standards; it’s about creating a working environment that prioritizes the well-being of everyone involved.
The concept of machine safety encompasses several key areas, including risk assessment, hazard control, fail-safe design, and user training.
These areas work together to form a comprehensive safety system that can prevent accidents and injuries.
Key Principles of Machine Safety Design
At the core of machine safety design is the need to identify and assess potential hazards.
Engineers begin by conducting a thorough risk assessment to pinpoint areas where dangers might arise.
This involves analyzing the machine’s intended use, understanding potential misuse, and considering the environment where it will operate.
Once hazards are identified, the next step is to control them.
This can be achieved through elimination, substitution, or engineering controls.
Eliminating a hazard is always the preferred method if possible.
When elimination isn’t feasible, substituting a less hazardous substance or process may be an option.
If neither elimination nor substitution is possible, engineering controls such as guards, barriers, or safety interlocks can be implemented.
Fail-safe design is another crucial element.
This means designing machines in a way that they will either shut down or default to a safe mode in case of a failure.
By incorporating these fail-safe mechanisms, machines can prevent accidents even when unexpected issues arise.
Integrating Safety into the Design Process
For effective machine safety, it’s important to integrate safety considerations from the very beginning of the design process.
This proactive approach is known as “safety by design” and is considered one of the best practices in the industry.
By incorporating safety features at the design stage, engineers can avoid costly modifications later and ensure a safer end product.
Early-stage safety integration involves collaboration between various stakeholders, including engineers, health, and safety professionals, and end-users.
This collaborative effort ensures that all perspectives are considered and that the final design meets safety requirements without compromising functionality.
Intrinsically Safe Design
Intrinsically safe design is a specialized approach within machine safety that focuses on preventing the ignition of flammable materials.
This is particularly important in industries such as oil and gas, chemical manufacturing, and mining, where explosive atmospheres are common.
By designing equipment that limits energy discharge, even in failure scenarios, intrinsically safe design minimizes the risk of explosions.
This involves ensuring that both the energy (electrical and thermal) and the surface temperature remain below levels that could ignite a hazardous atmosphere.
Components of Intrinsically Safe Design
There are several components involved in creating an intrinsically safe design.
Firstly, engineers must use components with energy limitations.
This means selecting equipment designed to operate at power levels below the ignition threshold of potentially explosive environments.
Additionally, circuits and systems must be carefully designed to prevent sparking or overheating.
This often involves incorporating protective components like fuses and resistors to control electrical currents.
Thermal management is also crucial, as excessive heat can serve as an ignition source.
Monitoring and maintenance are essential aspects too.
Regular inspections and maintenance help ensure that intrinsically safe systems remain effective over time.
Detecting wear and tear or malfunction can prevent failures that might compromise safety.
Challenges and Considerations
While intrinsically safe design offers substantial benefits, it does come with its own set of challenges.
Designing for intrinsically safe applications often requires additional certification and testing, which can be time-consuming and costly.
Moreover, creating a system that balances safety with functionality can be complex.
Engineers need to design solutions that do not overly limit their operational capabilities while still adhering to safety standards.
Furthermore, the rapid advancement of technology poses new challenges.
Emerging technologies like IoT and wireless communication require updated safety guidelines to ensure that they can be used safely in hazardous environments.
The Importance of Training and Awareness
Even the most well-designed safety systems can be undermined without proper training and awareness.
Operators and maintenance personnel must be educated on the potential hazards associated with the machinery they handle.
Training programs should cover safe operating procedures, emergency response protocols, and the proper use of personal protective equipment (PPE).
By ensuring workers are knowledgeable and equipped to handle potential safety issues, companies can significantly reduce the likelihood of accidents.
Creating a culture of safety is also vital.
Organizations should encourage open communication about safety concerns and foster an environment where employees feel comfortable reporting potential hazards without fear of reprisal.
Conclusion
Machine safety design, including inherently safe design practices, plays a crucial role in protecting workers and the environment.
By integrating safety considerations into the earliest stages of machine design and ensuring continued education and awareness, industries can reduce risks and create safer working conditions.
As technology continues to evolve, new challenges and solutions in machine safety will emerge.
The key is to remain proactive, adaptable, and committed to ongoing safety improvement.
Ultimately, investing in machine safety is not only a legal requirement but a moral obligation to protect lives and ensure the well-being of everyone involved in the operation and maintenance of machinery.
資料ダウンロード
QCD管理受発注クラウド「newji」は、受発注部門で必要なQCD管理全てを備えた、現場特化型兼クラウド型の今世紀最高の受発注管理システムとなります。
ユーザー登録
受発注業務の効率化だけでなく、システムを導入することで、コスト削減や製品・資材のステータス可視化のほか、属人化していた受発注情報の共有化による内部不正防止や統制にも役立ちます。
NEWJI DX
製造業に特化したデジタルトランスフォーメーション(DX)の実現を目指す請負開発型のコンサルティングサービスです。AI、iPaaS、および先端の技術を駆使して、製造プロセスの効率化、業務効率化、チームワーク強化、コスト削減、品質向上を実現します。このサービスは、製造業の課題を深く理解し、それに対する最適なデジタルソリューションを提供することで、企業が持続的な成長とイノベーションを達成できるようサポートします。
製造業ニュース解説
製造業、主に購買・調達部門にお勤めの方々に向けた情報を配信しております。
新任の方やベテランの方、管理職を対象とした幅広いコンテンツをご用意しております。
お問い合わせ
コストダウンが利益に直結する術だと理解していても、なかなか前に進めることができない状況。そんな時は、newjiのコストダウン自動化機能で大きく利益貢献しよう!
(β版非公開)