- お役立ち記事
- Practical points of “Toyota-style why-why analysis” and its application to trouble prevention
Practical points of “Toyota-style why-why analysis” and its application to trouble prevention
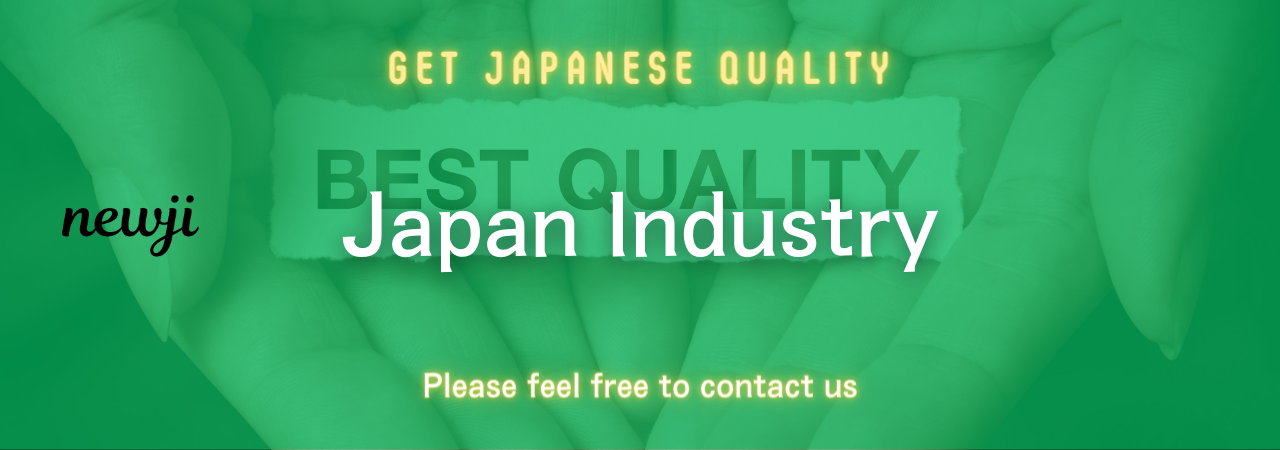
目次
Understanding the “Toyota-Style Why-Why Analysis”
The “Toyota-style why-why analysis,” often referred to as the “5 Whys,” is a simple, yet effective technique used for root cause analysis.
Developed by Sakichi Toyoda, a Japanese inventor, the process is quintessential to Toyota’s problem-solving approach.
By repeatedly asking “why” to a problem or challenge, this method aims to peel away the layers of symptoms and uncover the core issue.
Normally, five iterations of asking “why” are sufficient to delve deep into the problem.
However, there may be times when more than five questions are necessary to reach the root cause.
This analysis goes beyond just finding a quick fix and focuses on preventing the problem from recurring.
The Basic Steps of Why-Why Analysis
The why-why analysis typically involves several steps:
1. **Identify the Problem**: Clearly define what the problem is.
The more specific, the better.
2. **Ask “Why?”**: Begin by asking why the problem happened.
Write down the answer, which often leads to symptoms of the problem.
3. **Continue Asking “Why?”**: With each answer, ask “why” again.
Repeat this process until you reach the root cause.
4. **Develop a Solution**: Once the root cause is identified, brainstorm possible solutions and implement the most feasible one to ensure the issue does not reoccur.
5. **Monitor the Solution**: After implementing the solution, monitor it to ensure the problem is effectively solved and does not resurface.
Applying Why-Why Analysis to Trouble Prevention
While the why-why analysis is excellent for troubleshooting existing issues, it also has significant preventive applications.
1. Proactive Problem Prevention
By encouraging teams to use this analysis proactively, issues can be spotted and addressed before they escalate.
Whether it’s a manufacturing defect, a service issue, or a logistical bottleneck, identifying potential issues early can save time and resources.
2. Enhancing Team Collaboration
The why-why analysis naturally encourages team collaboration.
When teams work together to dive deep into problems, diverse perspectives can offer unique insights, leading to innovative solutions.
Thus, it strengthens teamwork and communication, which are critical components of effective problem-solving and prevention.
3. Continuous Improvement Culture
Implementing the Toyota-style why-why analysis fosters a culture of continuous improvement.
By regularly examining why mistakes or near-misses occur, organizations can systematically reduce risk and improve their processes, leading to ongoing enhancements and efficiencies.
Advantages of Why-Why Analysis
There are several notable benefits of employing the why-why analysis in an organization.
Identifying Root Causes
Many organizations apply quick fixes or make assumptions about problems without understanding their root causes.
The why-why analysis digs deep, ensuring that solutions address the actual source of the issue, reducing the likelihood of recurrence.
Simplicity and Cost-Effectiveness
Unlike complex analytical methods that require significant resources and expertise, the why-why analysis is simple to conduct.
It can be implemented without the need for expensive or sophisticated tools, making it accessible and cost-effective for businesses of any size.
Improved Decision-Making
As the analysis often involves a team, it naturally boosts collective understanding and decision-making.
It turns abstract problems into concrete challenges that can be addressed more effectively.
This collaborative approach ensures that multiple facets of the problem are considered, leading to better-informed decisions.
Challenges in Implementing Why-Why Analysis
While the why-why analysis is powerful, it does come with its challenges.
Over-Simplification
One common issue is that teams might not ask enough “whys,” leading to an oversimplified view of the problem.
This might result in incorrect root cause identification.
Thus, it is crucial to ensure the process isn’t rushed and comprehensively addresses the issue.
Lack of Training
Effective implementation requires understanding the methodology.
Teams without adequate training might not execute the process effectively, leading to unreliable results.
Providing proper training ensures the analysis is conducted correctly and leads to accurate identification of root causes.
Resistance to Change
Some individuals or teams may resist the why-why analysis, especially if they are accustomed to traditional problem-solving methods.
To overcome this, emphasizing the benefits and demonstrating successful case studies can help in gaining buy-in.
Real-World Applications of Why-Why Analysis
Several industries leverage the why-why analysis for various benefits apart from problem-solving.
Manufacturing
In manufacturing, the analysis is used to prevent defects on production lines.
By identifying the root causes of defects and addressing them, manufacturers reduce waste and enhance product quality.
Healthcare
In healthcare, why-why analysis helps understand errors in patient care, leading to improved safety protocols and operational procedures to prevent similar mistakes in the future.
IT and Software Development
In IT, particularly in software development, this analysis can be employed to resolve bugs and prevent future software issues.
By addressing the fundamental problems, teams can ensure more reliable and efficient software solutions.
Conclusion
The Toyota-style why-why analysis is a robust tool that, while simple, can significantly enhance an organization’s problem-solving capabilities and cultivate a culture of continuous improvement.
As teams apply this method, they not only uncover critical issues but also develop a more profound understanding of their processes, leading to sustainable success.
By addressing challenges and leveraging the advantages of the why-why analysis, organizations can derive its full potential and maintain a consistent stride towards operational excellence.
資料ダウンロード
QCD調達購買管理クラウド「newji」は、調達購買部門で必要なQCD管理全てを備えた、現場特化型兼クラウド型の今世紀最高の購買管理システムとなります。
ユーザー登録
調達購買業務の効率化だけでなく、システムを導入することで、コスト削減や製品・資材のステータス可視化のほか、属人化していた購買情報の共有化による内部不正防止や統制にも役立ちます。
NEWJI DX
製造業に特化したデジタルトランスフォーメーション(DX)の実現を目指す請負開発型のコンサルティングサービスです。AI、iPaaS、および先端の技術を駆使して、製造プロセスの効率化、業務効率化、チームワーク強化、コスト削減、品質向上を実現します。このサービスは、製造業の課題を深く理解し、それに対する最適なデジタルソリューションを提供することで、企業が持続的な成長とイノベーションを達成できるようサポートします。
オンライン講座
製造業、主に購買・調達部門にお勤めの方々に向けた情報を配信しております。
新任の方やベテランの方、管理職を対象とした幅広いコンテンツをご用意しております。
お問い合わせ
コストダウンが利益に直結する術だと理解していても、なかなか前に進めることができない状況。そんな時は、newjiのコストダウン自動化機能で大きく利益貢献しよう!
(Β版非公開)