- お役立ち記事
- Practical process for supplier audits in the pharmaceutical manufacturing industry
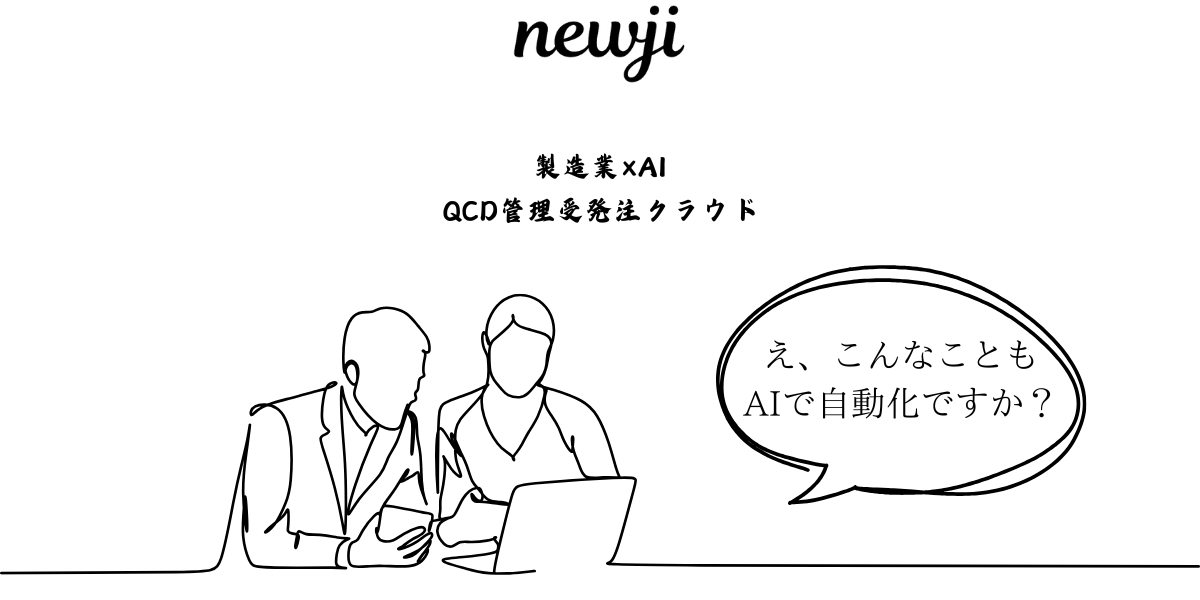
Practical process for supplier audits in the pharmaceutical manufacturing industry
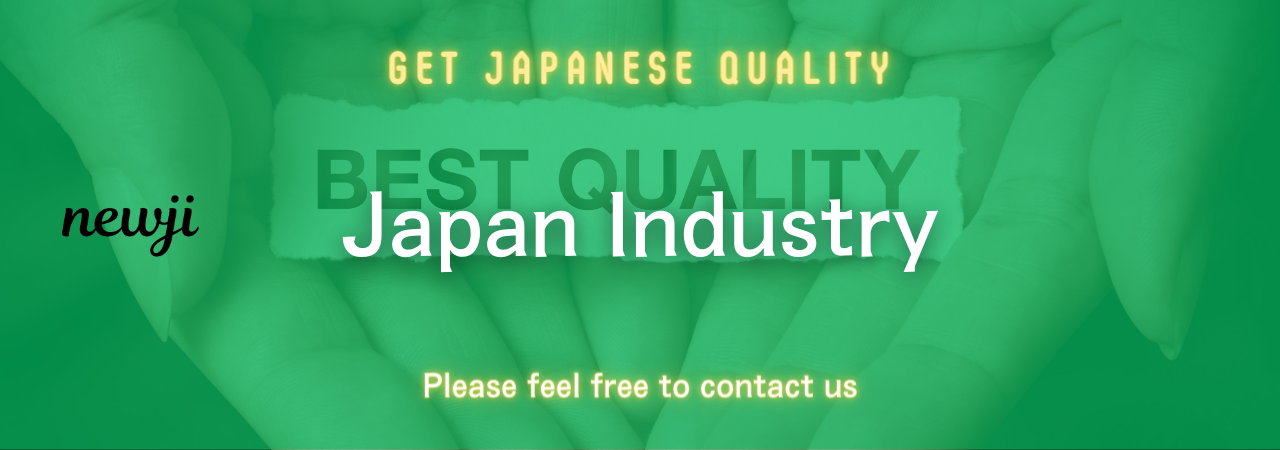
目次
Understanding the Importance of Supplier Audits
In the pharmaceutical manufacturing industry, supplier audits play a crucial role in ensuring product quality and compliance with regulatory standards.
These audits are systematic evaluations of a supplier’s quality management systems and processes.
Conducting thorough supplier audits helps pharmaceutical companies to verify that their suppliers can meet the required standards for raw materials, components, and services used in drug production.
This not only safeguards the quality and safety of pharmaceutical products but also mitigates risks associated with supply chain failures.
Supplier audits are essential for maintaining compliance with regulations set by authorities like the FDA and EMA.
Non-compliance can lead to significant penalties and damage a company’s reputation.
Therefore, engaging in a robust supplier audit program is a proactive strategy to manage quality and operational risks.
Planning the Supplier Audit
The first step in conducting a supplier audit is meticulous planning.
A well-structured audit plan sets the foundation for an effective evaluation.
Begin by identifying the scope of the audit.
Determine which processes, activities, and standards will be reviewed.
This will involve understanding the regulatory requirements relevant to the supplier’s role in the supply chain.
Next, assemble a capable audit team.
Choose individuals with expertise in areas pertinent to the supplier’s processes.
The team should include personnel with auditing competencies and experience in pharmaceutical manufacturing.
It’s also beneficial to train the audit team in specific regulatory guidelines such as Good Manufacturing Practices (GMP).
Develop an audit agenda listing the specific tasks and timeline for the audit process.
This agenda should be shared with the supplier well in advance of the audit date to ensure transparency and collaboration.
Conducting the On-site Audit
On the day of the audit, begin with an opening meeting.
Use this time to introduce the audit team, restate the objectives, and confirm the agenda with the supplier’s representatives.
Effective communication in this initial phase is key to setting a cooperative tone for the audit.
During the on-site inspection, assess the supplier’s quality management system.
Examine documentation, processes, and product facilities.
Verify that procedures align with regulatory requirements and company specifications.
It’s important to engage with the supplier’s staff to gather insights into their understanding and implementation of quality standards.
Take detailed notes throughout the inspection and note any discrepancies between the supplier’s processes and the required standards.
Photographic evidence can be useful for documenting observations, but ensure that it does not compromise sensitive or proprietary information.
Evaluating Documentation and Records
A significant component of the audit involves the examination of documentation.
Review the supplier’s quality manuals, standard operating procedures (SOPs), and training records.
Verify that these documents are up-to-date and accurately reflect the processes being practiced.
Assess the completeness and accuracy of batch records and trace them back to verify that raw materials meet specifications.
Ensure that there is adequate traceability for raw materials through to the finished product.
Inspecting Quality Control Systems
Inspect the supplier’s quality control systems to ensure they are effectively monitoring and managing product quality.
Evaluate the execution of testing protocols and analytical methods.
Verify calibration records for testing equipment to confirm that instruments are maintained and function accurately.
The supplier’s deviation management process should be scrutinized to understand how deviations are documented, investigated, and resolved.
This process is critical for ensuring that any issues encountered are thoroughly evaluated and do not affect product quality.
Preparing the Audit Report
Following the on-site audit, compile an audit report.
The report should provide a clear and concise summary of the findings, including both positive highlights and areas of non-conformance.
Include specific details about any deviations noted during the audit.
Develop action items for the supplier to address each non-conformance.
It’s vital that these actions have clearly defined timelines and responsibilities.
Conducting the Closing Meeting
Hold a closing meeting with the supplier’s representatives to discuss the audit findings.
This meeting is an opportunity to clarify observations, discuss potential corrective actions, and set expectations for follow-up.
Engage in open dialogue with the supplier, encouraging feedback and ensuring they understand the findings.
Post-Audit Follow-Up
Effective follow-up is crucial for ensuring that the supplier takes corrective actions seriously.
Monitor the implementation of corrective actions through regular communication and, if necessary, additional audits.
It is recommended to establish a timeline to verify the effectiveness of these actions.
A periodic review of the supplier’s performance is an important aspect of a dynamic supplier management program.
Regularly schedule audits and assessments to verify ongoing compliance and continuous improvement.
Conclusion
In conclusion, supplier audits in the pharmaceutical manufacturing industry are essential for maintaining quality and compliance standards.
Through careful planning, thorough execution, and proactive follow-up, these audits help mitigate risks associated with the supply chain.
By adhering to a structured audit process, pharmaceutical companies can build strong relationships with their suppliers, ensuring a reliable source of high-quality raw materials and components.
Committing to a rigorous supplier audit program is not only a regulatory requirement, but also a strategic business practice that supports the delivery of safe and effective pharmaceutical products.
資料ダウンロード
QCD調達購買管理クラウド「newji」は、調達購買部門で必要なQCD管理全てを備えた、現場特化型兼クラウド型の今世紀最高の購買管理システムとなります。
ユーザー登録
調達購買業務の効率化だけでなく、システムを導入することで、コスト削減や製品・資材のステータス可視化のほか、属人化していた購買情報の共有化による内部不正防止や統制にも役立ちます。
NEWJI DX
製造業に特化したデジタルトランスフォーメーション(DX)の実現を目指す請負開発型のコンサルティングサービスです。AI、iPaaS、および先端の技術を駆使して、製造プロセスの効率化、業務効率化、チームワーク強化、コスト削減、品質向上を実現します。このサービスは、製造業の課題を深く理解し、それに対する最適なデジタルソリューションを提供することで、企業が持続的な成長とイノベーションを達成できるようサポートします。
オンライン講座
製造業、主に購買・調達部門にお勤めの方々に向けた情報を配信しております。
新任の方やベテランの方、管理職を対象とした幅広いコンテンツをご用意しております。
お問い合わせ
コストダウンが利益に直結する術だと理解していても、なかなか前に進めることができない状況。そんな時は、newjiのコストダウン自動化機能で大きく利益貢献しよう!
(Β版非公開)