- お役立ち記事
- Practical Quality Assurance
Practical Quality Assurance
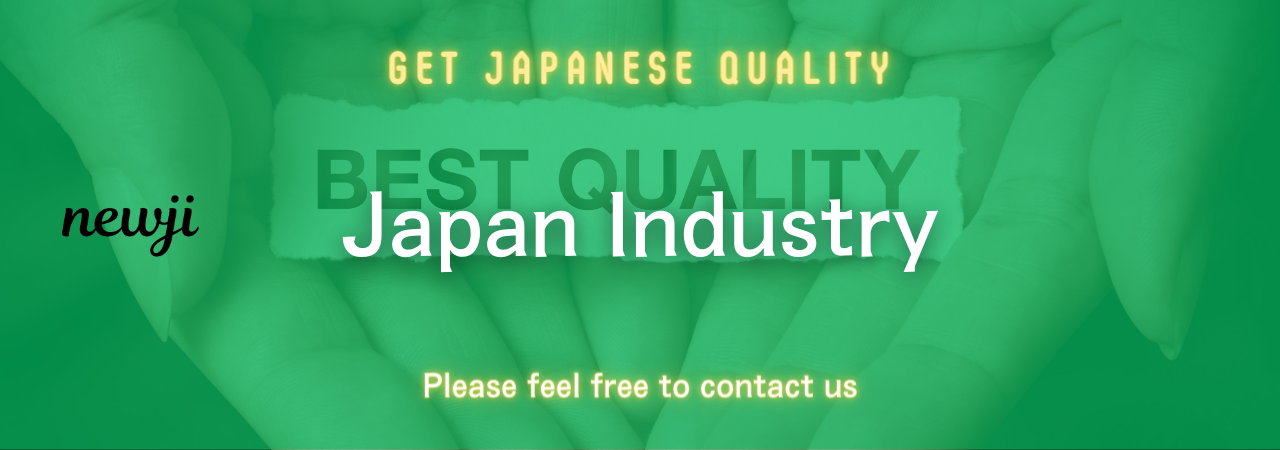
Quality assurance (QA) plays a vital role in any business, aiming to deliver high-quality products and services that meet customer expectations.
The concept of QA spans various industries and ensures that the final output is reliable, safe, and free from defects.
In this article, we will delve into practical ways to implement quality assurance effectively.
目次
Understanding Quality Assurance
Quality assurance is different from quality control.
While quality control focuses on identifying defects in the final product, quality assurance is a proactive process that aims to prevent defects from occurring in the first place.
QA encompasses the entire production process, including planning, designing, developing, and manufacturing.
The primary objective is to enhance customer satisfaction and build a reputable brand.
Key Principles of Quality Assurance
Customer Focus
Everything starts with the customer.
Understanding your customer’s needs and expectations is paramount.
Collect customer feedback regularly and use this information to improve your products and services.
Employee Involvement
Quality assurance is a team effort.
Involve all employees in the QA process by offering training and creating a culture of quality within the organization.
Encourage employees to take ownership of their work and contribute to quality improvement initiatives.
Continuous Improvement
One of the core principles of QA is continuous improvement.
Implementing regular audits and reviews helps identify areas for enhancement.
Adopt methodologies like Six Sigma or Kaizen to foster a culture of ongoing improvement.
Practical Steps to Implement Quality Assurance
Define Quality Standards
Start by establishing clear quality standards for your products or services.
These standards should be aligned with customer expectations and industry benchmarks.
Document these standards and communicate them effectively across the organization.
Develop a QA Plan
A comprehensive QA plan outlines the procedures, resources, and responsibilities required to achieve the set quality standards.
This plan should include detailed steps for quality checks at each stage of the production process.
Define roles and responsibilities so that every team member knows what is expected of them.
Conduct Regular Training
Training is crucial to ensure that employees are aware of the quality standards and procedures.
Offer regular training sessions on QA best practices, tools, and techniques.
Encourage employees to stay updated with the latest industry developments and trends.
Utilize Quality Management Systems (QMS)
Implementing a robust Quality Management System (QMS) can streamline your QA processes.
A QMS provides a structured framework for documenting, tracking, and analyzing quality data.
Popular QMS software includes ISO 9001, Six Sigma, and Total Quality Management (TQM).
Perform Regular Audits
Regular audits are essential to ensure compliance with the defined quality standards.
Internal audits help identify gaps and areas for improvement.
External audits, conducted by third-party organizations, lend credibility to your QA processes and reassure customers of your commitment to quality.
Gather and Analyze Data
Data analysis is a critical component of quality assurance.
Collect data on various parameters, such as defect rates, customer complaints, and process efficiency.
Use data analytics tools to identify patterns and trends that can inform quality improvement strategies.
Tools and Techniques for Quality Assurance
Statistical Process Control (SPC)
SPC involves using statistical methods to monitor and control production processes.
By analyzing data from the production line, SPC helps identify variations and deviations from the set quality standards, enabling timely corrective actions.
Root Cause Analysis (RCA)
RCA is a problem-solving technique used to identify the underlying causes of defects or issues.
By understanding the root cause, you can implement effective solutions to prevent recurrence.
Common RCA tools include the 5 Whys, Fishbone Diagram, and Fault Tree Analysis.
Failure Mode and Effects Analysis (FMEA)
FMEA is a systematic approach to identifying potential failure points in a process and assessing their impacts.
By prioritizing the highest risk areas, you can take preventative measures to mitigate potential issues before they occur.
Pareto Analysis
Pareto Analysis, based on the Pareto Principle (80/20 rule), helps identify the most significant factors contributing to quality problems.
By focusing on the vital few causes that account for the majority of defects, you can achieve substantial improvements with minimal resources.
Benefits of Effective Quality Assurance
Enhanced Customer Satisfaction
Implementing robust QA processes leads to higher-quality products and services, which, in turn, enhances customer satisfaction.
Satisfied customers are more likely to become repeat buyers and recommend your brand to others.
Improved Efficiency
QA helps streamline production processes by identifying and eliminating inefficiencies.
This leads to better resource utilization, reduced waste, and lower costs.
Regulatory Compliance
Many industries have stringent regulatory requirements.
Adhering to these regulations through effective QA practices ensures that your products meet legal standards, avoiding costly penalties and legal issues.
Competitive Advantage
A strong QA program sets you apart from competitors.
Consistently delivering high-quality products builds a positive reputation, attracting more customers and increasing market share.
Challenges in Quality Assurance
Cost Considerations
Implementing comprehensive QA processes can be expensive, particularly for small businesses.
Balancing quality improvement investments with budgetary constraints is a common challenge.
Resistance to Change
Employees may resist new QA procedures, especially if they are accustomed to existing workflows.
Overcoming resistance requires effective communication, training, and involvement of employees in QA initiatives.
Maintaining Consistency
Ensuring consistent quality across all production batches can be challenging.
Variations in materials, equipment, and human factors can impact product quality.
Regular monitoring and control measures are essential to maintain consistency.
In conclusion, practical quality assurance is an ongoing commitment to delivering superior products and services.
By understanding QA principles, implementing effective strategies, and utilizing the right tools, businesses can achieve significant improvements in quality and customer satisfaction.
Investing in quality assurance not only fosters customer loyalty but also drives operational efficiency and competitive advantage.
資料ダウンロード
QCD調達購買管理クラウド「newji」は、調達購買部門で必要なQCD管理全てを備えた、現場特化型兼クラウド型の今世紀最高の購買管理システムとなります。
ユーザー登録
調達購買業務の効率化だけでなく、システムを導入することで、コスト削減や製品・資材のステータス可視化のほか、属人化していた購買情報の共有化による内部不正防止や統制にも役立ちます。
NEWJI DX
製造業に特化したデジタルトランスフォーメーション(DX)の実現を目指す請負開発型のコンサルティングサービスです。AI、iPaaS、および先端の技術を駆使して、製造プロセスの効率化、業務効率化、チームワーク強化、コスト削減、品質向上を実現します。このサービスは、製造業の課題を深く理解し、それに対する最適なデジタルソリューションを提供することで、企業が持続的な成長とイノベーションを達成できるようサポートします。
オンライン講座
製造業、主に購買・調達部門にお勤めの方々に向けた情報を配信しております。
新任の方やベテランの方、管理職を対象とした幅広いコンテンツをご用意しております。
お問い合わせ
コストダウンが利益に直結する術だと理解していても、なかなか前に進めることができない状況。そんな時は、newjiのコストダウン自動化機能で大きく利益貢献しよう!
(Β版非公開)