- お役立ち記事
- Practical Skill Transfer Techniques in Manufacturing Sites
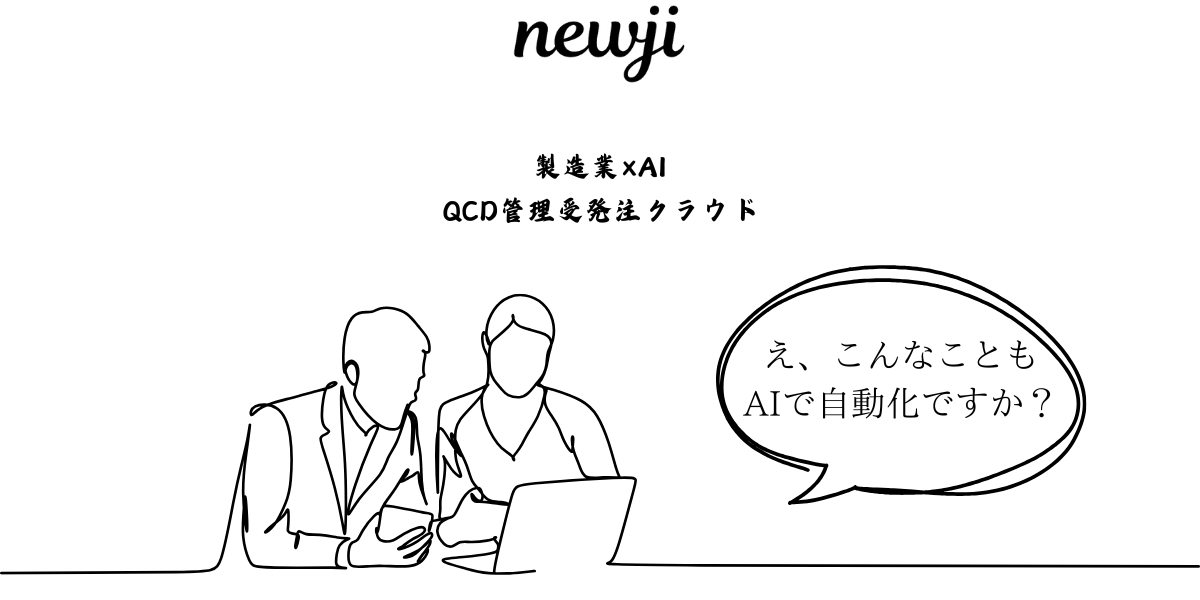
Practical Skill Transfer Techniques in Manufacturing Sites
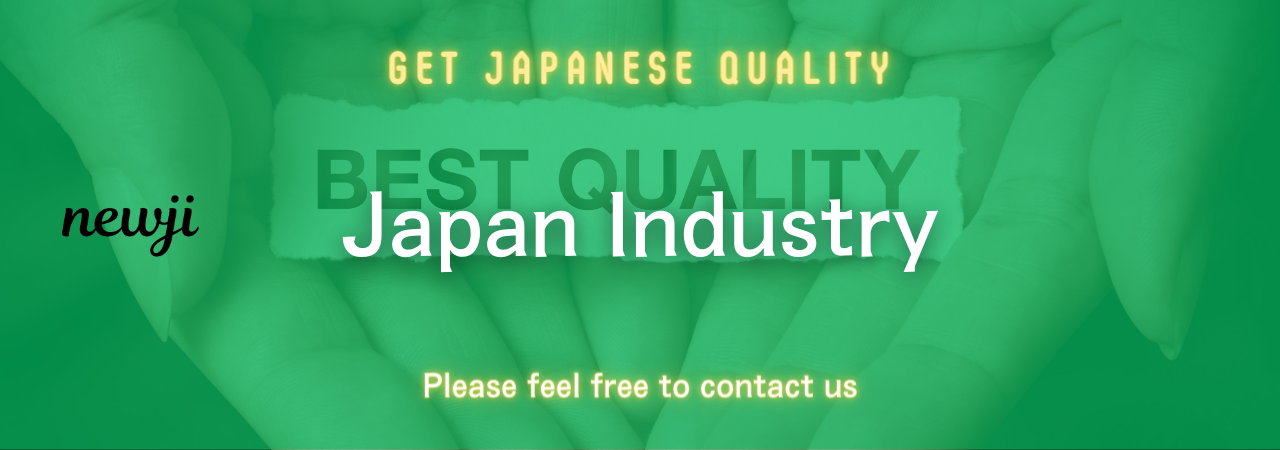
In the rapidly evolving landscape of manufacturing, transferring skills efficiently from seasoned professionals to newer team members is crucial for maintaining productivity and quality. Skill transfer ensures that knowledge is retained within the organization, reducing downtime and increasing overall efficiency. Whether on a factory floor or a production line, implementing practical skill transfer techniques can make a significant difference in a manufacturing site’s success.
目次
Understanding the Importance of Skill Transfer
Effective skill transfer is vital for several reasons.
First and foremost, it ensures continuity in operations.
Experienced workers possess valuable insights and nuanced understanding that cannot be easily captured in manuals.
Transferring these skills to newer employees minimizes the risk of operational disruptions when experienced workers retire or move on.
Additionally, a knowledgeable workforce is better equipped to troubleshoot issues, innovate solutions, and maintain high-quality standards, contributing to long-term success.
Methods for Effective Skill Transfer
There are several methods to facilitate skill transfer in manufacturing sites.
By integrating a combination of these techniques, businesses can build a resilient and capable workforce.
1. On-the-Job Training (OJT)
On-the-Job Training is an effective method where new employees learn by observing and performing tasks under the guidance of experienced workers.
This hands-on approach allows learners to gain practical experience and develop muscle memory for specific tasks.
OJT can be structured with checklists and standard operating procedures (SOPs) to ensure consistency and completeness in training.
2. Mentorship Programs
Implementing mentorship programs pairs less experienced workers with seasoned professionals who serve as mentors.
Mentors provide personalized guidance, share their expertise, and offer feedback on performance.
These relationships foster a supportive learning environment and ensure that critical knowledge is passed on effectively.
Regular check-ins and progress reviews can further enhance the mentorship experience.
3. Cross-Training
Cross-training involves training employees to perform multiple roles within the manufacturing site.
This practice not only enhances workforce flexibility but also facilitates skill transfer, as employees become proficient in various tasks.
Cross-training can help in identifying and bridging knowledge gaps, and it enables workforce redeployment in response to changing production needs or absenteeism.
4. Structured Training Programs
Structured training programs encompass formal education components such as classroom instruction, workshops, and e-learning modules.
These programs can be tailored to specific skills required in a manufacturing site and can include theoretical knowledge that complements hands-on experience.
Incorporating quizzes, practical assessments, and certifications can help gauge skill acquisition and ensure that learning objectives are met.
Tips for Successful Skill Transfer
Ensuring effective skill transfer requires thoughtful planning and execution.
Here are some tips to facilitate a smooth process:
1. Document Processes and Procedures
Creating detailed documentation of processes, procedures, and best practices is essential for consistent skill transfer.
Documents should include step-by-step instructions, visual aids, and troubleshooting tips.
Regular updates to documentation ensure that it remains relevant and accurate.
2. Use Visual Aids and Demonstrations
Visual aids such as diagrams, videos, and infographics can make complex processes easier to understand.
Live demonstrations by skilled workers allow learners to see techniques in action, bridging the gap between theory and practice.
Recording these demonstrations can create a valuable resource library for future training.
3. Encourage a Culture of Continuous Learning
Fostering a culture that values continuous learning and improvement encourages employees to seek out new knowledge and skills.
Providing opportunities for professional development, such as attending workshops or industry conferences, helps keep the workforce updated on the latest advancements and practices.
4. Utilize Technology
Modern technology offers various tools to enhance skill transfer.
Virtual reality (VR) and augmented reality (AR) can provide immersive training experiences, allowing employees to practice in a simulated environment.
Learning management systems (LMS) can track progress, provide resources, and facilitate communication between trainers and learners.
5. Create a Feedback Loop
Establishing a feedback loop ensures that training programs are effective and that any issues are addressed promptly.
Regularly soliciting feedback from both trainers and trainees helps identify areas for improvement and adapts training methods to better suit the needs of the workforce.
Encouraging open communication fosters a collaborative learning environment.
Challenges in Skill Transfer and How to Overcome Them
Despite its importance, skill transfer in manufacturing sites can face several challenges.
Addressing these challenges proactively can lead to more effective training outcomes.
1. Resistance to Change
Some employees may be resistant to adopting new methods or technologies.
To overcome this, involve them in the planning process, highlighting the benefits of skill transfer and addressing any concerns.
Providing incentives for participation and recognizing their contributions can also motivate them to embrace new learning opportunities.
2. Time Constraints
Finding time for training in a busy production schedule can be challenging.
Scheduling short, frequent training sessions can minimize disruptions and make it easier to integrate training into daily routines.
Alternatively, using shift overlaps or downtime effectively can ensure that training is conducted without significant impact on production.
3. Measuring Effectiveness
It can be difficult to measure the effectiveness of skill transfer initiatives.
Using clear metrics and key performance indicators (KPIs) allows for objective assessment of training outcomes.
Regular evaluations and adjustments to training programs based on these metrics can enhance their effectiveness.
The Future of Skill Transfer in Manufacturing
As technology continues to evolve, so too will the methods for skill transfer in manufacturing sites.
Embracing new tools and techniques will be crucial for staying competitive.
For example, artificial intelligence (AI) could personalize training programs based on individual learning styles and performance data.
Additionally, collaborations with educational institutions can provide access to cutting-edge research and methodologies.
The essence of manufacturing lies not only in the machinery and technology but in the skilled workforce that operates them.
By implementing practical skill transfer techniques, manufacturing sites can ensure that expertise is preserved and continuously built upon, paving the way for sustained growth and innovation.
資料ダウンロード
QCD調達購買管理クラウド「newji」は、調達購買部門で必要なQCD管理全てを備えた、現場特化型兼クラウド型の今世紀最高の購買管理システムとなります。
ユーザー登録
調達購買業務の効率化だけでなく、システムを導入することで、コスト削減や製品・資材のステータス可視化のほか、属人化していた購買情報の共有化による内部不正防止や統制にも役立ちます。
NEWJI DX
製造業に特化したデジタルトランスフォーメーション(DX)の実現を目指す請負開発型のコンサルティングサービスです。AI、iPaaS、および先端の技術を駆使して、製造プロセスの効率化、業務効率化、チームワーク強化、コスト削減、品質向上を実現します。このサービスは、製造業の課題を深く理解し、それに対する最適なデジタルソリューションを提供することで、企業が持続的な成長とイノベーションを達成できるようサポートします。
オンライン講座
製造業、主に購買・調達部門にお勤めの方々に向けた情報を配信しております。
新任の方やベテランの方、管理職を対象とした幅広いコンテンツをご用意しております。
お問い合わせ
コストダウンが利益に直結する術だと理解していても、なかなか前に進めることができない状況。そんな時は、newjiのコストダウン自動化機能で大きく利益貢献しよう!
(Β版非公開)