- お役立ち記事
- Practical Steps for Kaizen in In-House Logistics Using a 3-Step Approach
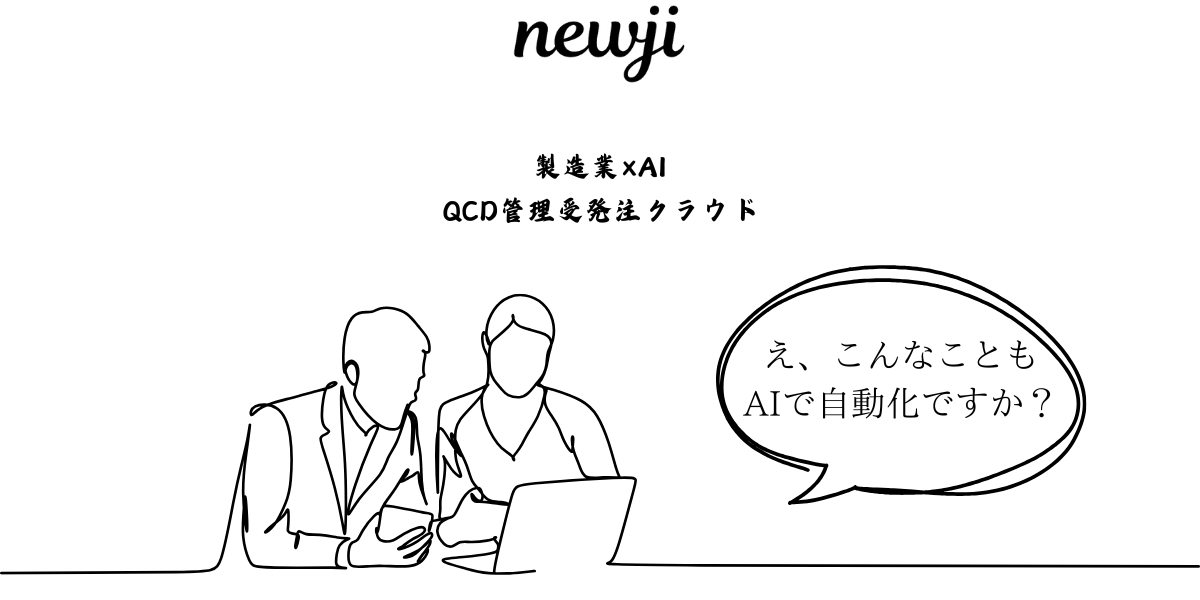
Practical Steps for Kaizen in In-House Logistics Using a 3-Step Approach
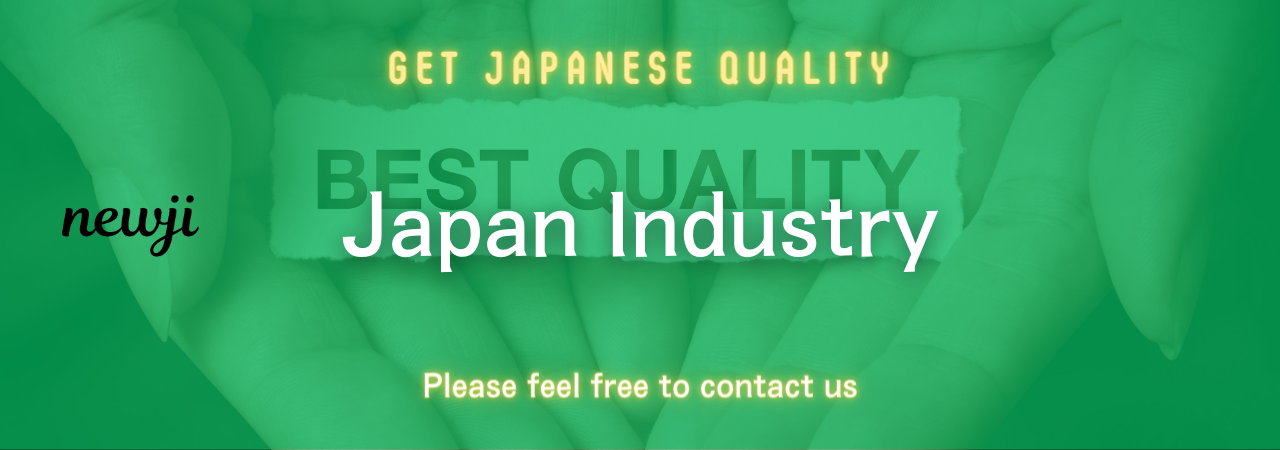
Kaizen, a Japanese term meaning “change for better” or “continuous improvement,” is an effective strategy for enhancing in-house logistics.
Kaizen involves making small, incremental changes to processes, aiming for long-term improvements in efficiency, productivity, and quality.
Adopting a Kaizen mindset can significantly streamline your logistics operations.
Here’s how you can implement Kaizen in in-house logistics using a simple 3-step approach.
目次
Step 1: Identify and Analyze Current Processes
The first step in implementing Kaizen in your logistics operations is to thoroughly understand your current processes.
You cannot improve what you do not understand.
Start by mapping out all the logistics activities, from order processing to inventory management and delivery.
Mapping Your Processes
Use visual aids like flowcharts and diagrams to map out each step in your logistics chain.
Identify key touchpoints where delays, bottlenecks, or errors most often occur.
This visual representation helps you to see the entire process at a glance, making it easier to pinpoint problem areas.
Gathering Data
Once your processes are mapped, it’s time to gather relevant data.
Track key performance indicators (KPIs) such as order accuracy, delivery times, and inventory turnover rates.
Collecting this data gives you a baseline to measure improvements against later.
Root Cause Analysis
When you find an issue, it is critical to identify its root cause.
Tools such as the “5 Whys” technique can help you delve deeper into the problem.
Ask “Why?” five times, each time drilling down to uncover the fundamental reason behind the issue.
Addressing root causes, rather than just symptoms, leads to more sustainable improvements.
Step 2: Brainstorm and Implement Solutions
Once you understand the issues in your logistics processes, the next step is to generate and enact solutions.
In Kaizen, everyone in the organization is encouraged to contribute ideas for improvement.
Engaging Teams
Improvement ideas often come from those directly involved in the processes.
Encourage employees to suggest changes by creating open forums or suggestion boxes.
Regular team meetings can also be a great place to brainstorm collectively.
Prioritizing Solutions
Not all ideas can be implemented at once.
Prioritize solutions based on their impact and feasibility.
Quick wins — easy-to-implement changes that significantly improve processes — should be tackled first.
This creates immediate benefits and can build momentum for tackling more complex issues.
Implementing Changes
Once solutions are prioritized, start implementing them in manageable steps.
It’s important to keep track of these changes, documenting each modification and its impact on the process.
This can be done using simple spreadsheets or specialized project management software.
Monitoring and Feedback
After implementing changes, closely monitor their effects.
Compare the new data against your baseline to gauge the effectiveness of the improvements.
Encourage ongoing feedback from employees to further tweak and optimize the processes.
Continuous monitoring ensures that the changes provide lasting benefits.
Step 3: Review and Standardize Processes
The final step in the Kaizen approach is to review the changes and standardize successful improvements.
This ensures that the gains made are maintained and become part of the daily routine.
Conducting Reviews
Regularly scheduled reviews are essential to reflect on the changes made.
Assess the overall impact on logistics operations, and identify any further areas for improvement.
In these reviews, pay attention to both quantitative data (e.g., KPIs) and qualitative feedback from employees.
Standard Operating Procedures (SOPs)
When a process improvement proves to be successful, it’s crucial to document it in the form of Standard Operating Procedures (SOPs).
SOPs provide a step-by-step guide on how to execute tasks efficiently and correctly.
Ensure all employees are trained on newly established SOPs to maintain consistency.
Creating a Culture of Continuous Improvement
Kaizen is not a one-time effort but a continuous cycle of improvement.
Cultivate a culture where employees are always looking for ways to enhance processes.
Provide ongoing training and development opportunities to keep the team updated on new strategies and technologies.
Celebrate successes to reinforce the importance of constant improvement.
Conclusion
Implementing Kaizen in in-house logistics involves a systematic approach of identifying, analyzing, and improving processes.
By following this 3-step approach — understanding current processes, brainstorming and implementing solutions, and reviewing and standardizing improvements — you can achieve significant enhancements in efficiency and productivity.
Continuous improvement should become a core organizational principle to sustain long-term success.
Empower your team, standardize best practices, and maintain a keen focus on ongoing improvements.
These steps will ensure that your logistics operations remain efficient, effective, and always evolving for the better.
資料ダウンロード
QCD調達購買管理クラウド「newji」は、調達購買部門で必要なQCD管理全てを備えた、現場特化型兼クラウド型の今世紀最高の購買管理システムとなります。
ユーザー登録
調達購買業務の効率化だけでなく、システムを導入することで、コスト削減や製品・資材のステータス可視化のほか、属人化していた購買情報の共有化による内部不正防止や統制にも役立ちます。
NEWJI DX
製造業に特化したデジタルトランスフォーメーション(DX)の実現を目指す請負開発型のコンサルティングサービスです。AI、iPaaS、および先端の技術を駆使して、製造プロセスの効率化、業務効率化、チームワーク強化、コスト削減、品質向上を実現します。このサービスは、製造業の課題を深く理解し、それに対する最適なデジタルソリューションを提供することで、企業が持続的な成長とイノベーションを達成できるようサポートします。
オンライン講座
製造業、主に購買・調達部門にお勤めの方々に向けた情報を配信しております。
新任の方やベテランの方、管理職を対象とした幅広いコンテンツをご用意しております。
お問い合わせ
コストダウンが利益に直結する術だと理解していても、なかなか前に進めることができない状況。そんな時は、newjiのコストダウン自動化機能で大きく利益貢献しよう!
(Β版非公開)