- お役立ち記事
- Practical Strategies for Balancing Injection Speed and Molding Cycles
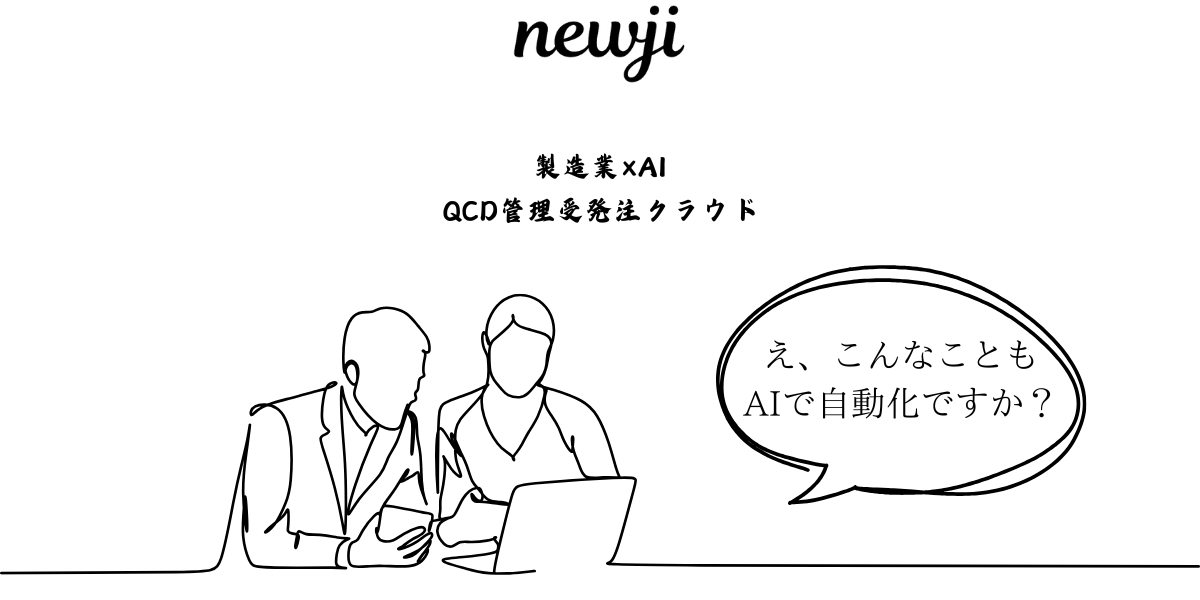
Practical Strategies for Balancing Injection Speed and Molding Cycles
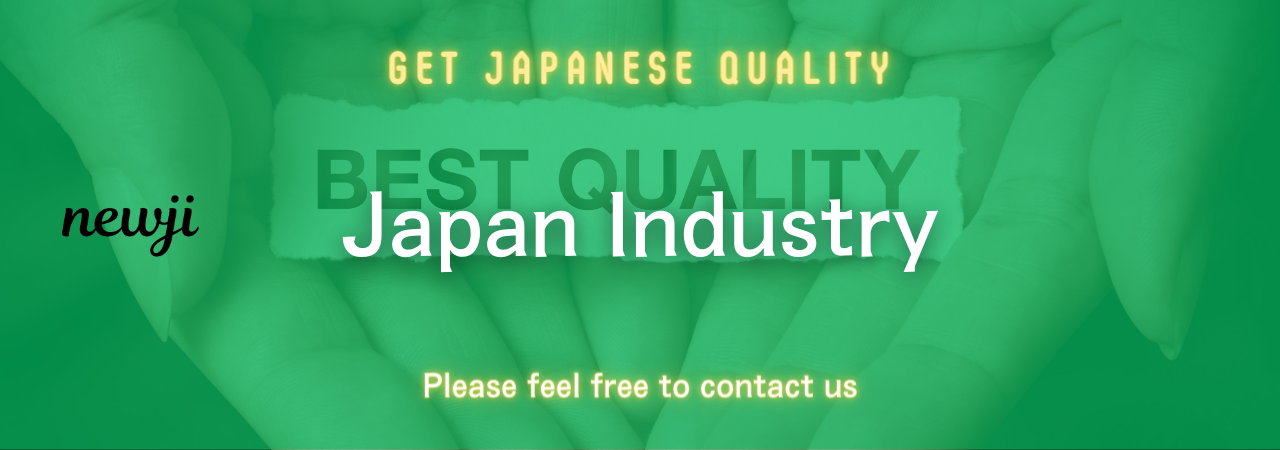
目次
Understanding Injection Molding Basics
Injection molding is a manufacturing process that involves injecting molten material into a mold cavity.
Typically used for producing plastic parts, it can also be applied to metals, glasses, and other materials.
The cycle begins when the desired material, often thermoplastic, is heated until it becomes pliable.
Next, it is injected at high pressure into a precision-designed mold, which cools and hardens the material into the desired shape.
This process is favored for its ability to produce complex, high-quality components rapidly and cost-effectively.
The Role of Injection Speed
Injection speed is a pivotal factor in the molding process.
It refers to the rate at which the molten material is injected into the mold.
A well-calibrated injection speed is crucial for ensuring part quality and optimizing production efficiency.
If the speed is too slow, the material may solidify prematurely, leading to defects such as flow lines or short shots.
Conversely, if it’s too fast, issues like flash, burn marks, or increased stress in the material could occur.
Thus, finding the appropriate injection speed is key to producing defect-free parts while maintaining a smooth and quick cycle.
The Impact of Molding Cycles on Production
A molding cycle encompasses the entire process from mold closure to part ejection.
It includes stages such as injection, cooling, and ejection.
The time required to complete each cycle directly affects production rates and costs.
Shorter cycles increase production capacity but may compromise part quality when improperly managed.
On the other hand, excessively lengthy cycles can decrease production efficiency, leading to increased operational costs.
Hence, balancing molding cycle duration is vital to achieve high-quality output while maintaining cost-effectiveness.
Strategies for Balancing Injection Speed and Molding Cycles
1. Optimize Material Selection
Choosing the right material significantly impacts both injection speed and cycle time.
Different materials have varying flow characteristics and thermal properties.
For example, materials with low viscosity can be injected more rapidly, possibly shortening the injection time.
However, it’s important to consider how quickly the material cools and solidifies.
Selecting a material that provides the optimal balance of flowability and cooling time ensures that cycle times remain competitive without sacrificing quality.
2. Precise Mold Design
The mold design has a profound impact on cycle times and injection speed.
Complex molds with intricate geometries may require slower injection speeds to ensure that the material fills all crevices properly.
Using flow simulation software during the design phase can help predict and optimize flow characteristics.
Additionally, ensuring that mold design incorporates adequate cooling channels can significantly reduce cooling times, thus shortening the overall cycle time.
3. Temperature Control
Maintaining precise control over the temperature of both the material and the mold can enhance part quality and reduce cycle times.
Properly heated molds, in tandem with the material’s optimal processing temperature, allow for smoother and faster injection.
Efficient cooling systems rebalance mold temperature quickly, allowing for shorter cooling phases and hence faster cycle times.
4. Fine-Tuning Machine Parameters
Advanced injection molding machines allow for significant customization of operation parameters such as injection pressure, speed, and hold time.
It’s crucial to fine-tune these settings according to the specific material being used and the part being produced.
This customization helps to balance speed and precision, minimizing manufacturing defects and optimizing cycle times.
5. Implement Automation Solutions
Integrating automation into the injection molding process can substantially enhance efficiency.
Robotic systems can be employed for activities such as part removal, thereby decreasing cycle time and improving throughput.
Automation also reduces human error, ensuring consistent speed and quality throughout production runs.
6. Regular Maintenance and Upkeep
Regular maintenance of molding equipment ensures optimal operation and prevents part defects caused by wear or misalignment.
Routine checks and timely maintenance minimize downtime, often caused by unexpected machine failures, and ensure that the equipment performs at peak efficiency.
Conclusion
Balancing injection speed and molding cycles is a complex but essential aspect of efficient production in injection molding.
Understanding the interplay between the different parameters and employing practical strategies such as optimizing material selection, mold design, and machine maintenance can significantly improve production outcomes.
Ultimately, a well-balanced manufacturing process will yield high-quality parts, reduce costs, and enhance overall production efficiency.
資料ダウンロード
QCD調達購買管理クラウド「newji」は、調達購買部門で必要なQCD管理全てを備えた、現場特化型兼クラウド型の今世紀最高の購買管理システムとなります。
ユーザー登録
調達購買業務の効率化だけでなく、システムを導入することで、コスト削減や製品・資材のステータス可視化のほか、属人化していた購買情報の共有化による内部不正防止や統制にも役立ちます。
NEWJI DX
製造業に特化したデジタルトランスフォーメーション(DX)の実現を目指す請負開発型のコンサルティングサービスです。AI、iPaaS、および先端の技術を駆使して、製造プロセスの効率化、業務効率化、チームワーク強化、コスト削減、品質向上を実現します。このサービスは、製造業の課題を深く理解し、それに対する最適なデジタルソリューションを提供することで、企業が持続的な成長とイノベーションを達成できるようサポートします。
オンライン講座
製造業、主に購買・調達部門にお勤めの方々に向けた情報を配信しております。
新任の方やベテランの方、管理職を対象とした幅広いコンテンツをご用意しております。
お問い合わせ
コストダウンが利益に直結する術だと理解していても、なかなか前に進めることができない状況。そんな時は、newjiのコストダウン自動化機能で大きく利益貢献しよう!
(Β版非公開)