- お役立ち記事
- Practical Strategies for Balancing Shot Size and Molding Cycles
月間76,176名の
製造業ご担当者様が閲覧しています*
*2025年3月31日現在のGoogle Analyticsのデータより
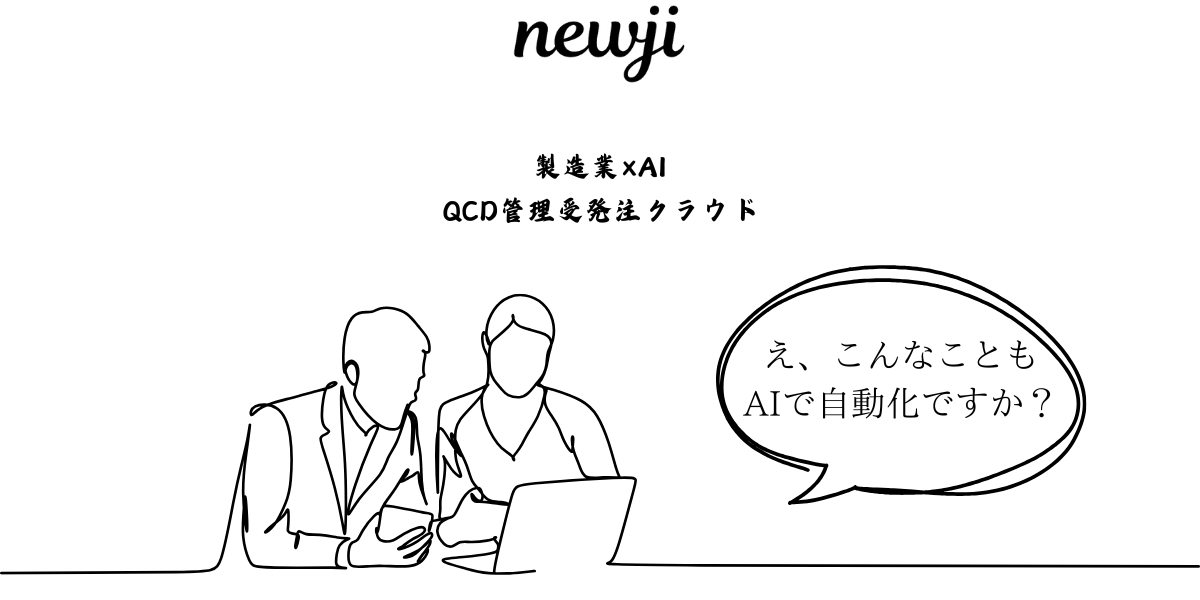
Practical Strategies for Balancing Shot Size and Molding Cycles
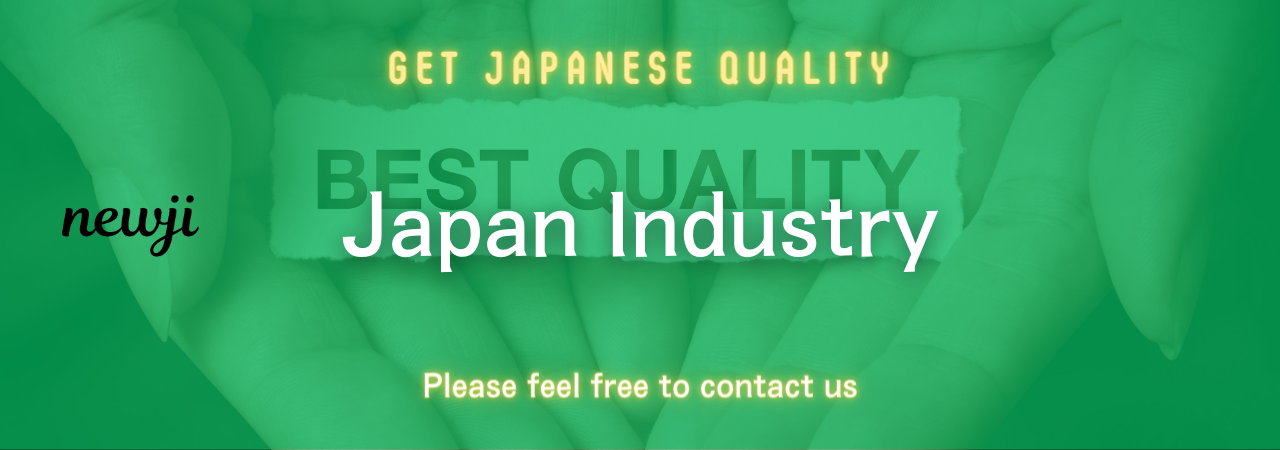
Balancing shot size and molding cycles is crucial in the plastic injection molding industry.
Achieving the right balance can significantly impact production efficiency, product quality, and cost management.
This article will explore practical strategies to optimize shot size and molding cycles to enhance overall performance.
目次
Understanding Shot Size and Molding Cycles
Before diving into strategies, it’s essential to grasp what shot size and molding cycles mean in the context of injection molding.
What is Shot Size?
Shot size refers to the amount of molten material injected into the mold during the injection process.
It’s a critical variable in ensuring that the final product meets the required specifications and quality standards.
Too much or too little material can lead to defects, increased waste, or operational inefficiency.
What are Molding Cycles?
A molding cycle is the complete process of forming a part, starting from the injection of material to the ejection of the completed part.
It includes several stages: mold closing, injection, cooling, mold opening, and part ejection.
The length of the cycle can affect production speed and energy usage.
Strategies for Optimizing Shot Size
Optimizing shot size is vital for producing high-quality parts efficiently.
Here are some strategies to help achieve this goal:
1. Precise Material Calculation
One of the fundamental steps in optimizing shot size is calculating the exact amount of material required per shot.
Using computer software designed for this purpose can minimize human error and ensure that you use just the right amount of material needed for each product.
2. Adjust Machine Settings
Machine settings, such as temperature, pressure, and speed, should be regularly monitored and adjusted to match the required shot size.
Calibration of machines ensures that they operate within the optimal parameters, reducing variability and enhancing consistency in shot size.
3. Material Consideration
Different materials have unique properties and react differently under pressure and heat.
Understanding the specific characteristics of the materials you are working with can help you adjust the shot size effectively.
For example, semi-crystalline polymers may require different shot sizes compared to amorphous ones.
4. Regular Maintenance
Ensuring that all equipment is well-maintained reduces the risk of malfunctions that can affect shot size.
Regular checks and maintenance of machinery, including the injection unit and hydraulic system, are crucial for ongoing production efficiency.
Strategies for Optimizing Molding Cycles
Shortening molding cycles without compromising quality is a key factor in improving profitability.
1. Streamline Cooling Time
Cooling time is a significant part of the cycle and can often be optimized.
Implementing efficient cooling systems, such as conformal cooling channels, can help reduce the time needed.
Using materials and mold designs that conduct heat away from the part more effectively can also cut down cycle times.
2. Optimize Mold Design
The design and complexity of the mold can greatly impact the cycle time.
Simplifying the mold design, where possible, can lead to faster cycles.
Utilizing advanced simulation software can help identify the best design parameters to minimize cycle time.
3. Use Automation
Automating parts of the molding process can significantly reduce cycle times.
Robotic arms for part removal or advanced systems for mold closing and opening can increase the speed of production cycles while maintaining precision and safety.
4. Monitor and Analyze
Data monitoring and analysis are essential to identify bottlenecks in the molding cycle process.
Using sensors and data analytics tools can provide insights into where adjustments can be made to improve efficiency.
Continuous monitoring enables quick response to any deviations from the norm, maintaining optimal cycle times.
The Benefits of Balanced Shot Size and Molding Cycles
Achieving a harmonious balance between shot size and molding cycles can lead to various benefits.
Improved Product Quality
When shot size and cycle times are optimized, the consistency and appearance of the finished products improve.
This can lead to higher customer satisfaction and reduced waste due to defective products.
Increased Efficiency and Throughput
Optimizing these factors contributes to shorter production times, meaning more parts can be produced within the same timeframe, effectively increasing output and maximizing the use of resources.
Cost Reduction
Reducing cycle times and optimizing shot sizes minimize energy usage and material waste, lowering production costs.
Moreover, operational efficiency reduces downtime and potential costs associated with machine breakdowns or part defects.
Conclusion
Balancing shot size and molding cycles is a nuanced task requiring thorough understanding and strategic planning.
By employing precise material calculations, adjusting machine settings, and adopting efficient mold designs, manufacturers can optimize their processes.
This balance leads to higher quality products, increased production efficiency, and reduced costs, ultimately driving success in the competitive field of plastic injection molding.
資料ダウンロード
QCD管理受発注クラウド「newji」は、受発注部門で必要なQCD管理全てを備えた、現場特化型兼クラウド型の今世紀最高の受発注管理システムとなります。
ユーザー登録
受発注業務の効率化だけでなく、システムを導入することで、コスト削減や製品・資材のステータス可視化のほか、属人化していた受発注情報の共有化による内部不正防止や統制にも役立ちます。
NEWJI DX
製造業に特化したデジタルトランスフォーメーション(DX)の実現を目指す請負開発型のコンサルティングサービスです。AI、iPaaS、および先端の技術を駆使して、製造プロセスの効率化、業務効率化、チームワーク強化、コスト削減、品質向上を実現します。このサービスは、製造業の課題を深く理解し、それに対する最適なデジタルソリューションを提供することで、企業が持続的な成長とイノベーションを達成できるようサポートします。
製造業ニュース解説
製造業、主に購買・調達部門にお勤めの方々に向けた情報を配信しております。
新任の方やベテランの方、管理職を対象とした幅広いコンテンツをご用意しております。
お問い合わせ
コストダウンが利益に直結する術だと理解していても、なかなか前に進めることができない状況。そんな時は、newjiのコストダウン自動化機能で大きく利益貢献しよう!
(β版非公開)