- お役立ち記事
- Practical Strategies for Enhancing Competitiveness by Shortening Molding Cycle Times
Practical Strategies for Enhancing Competitiveness by Shortening Molding Cycle Times
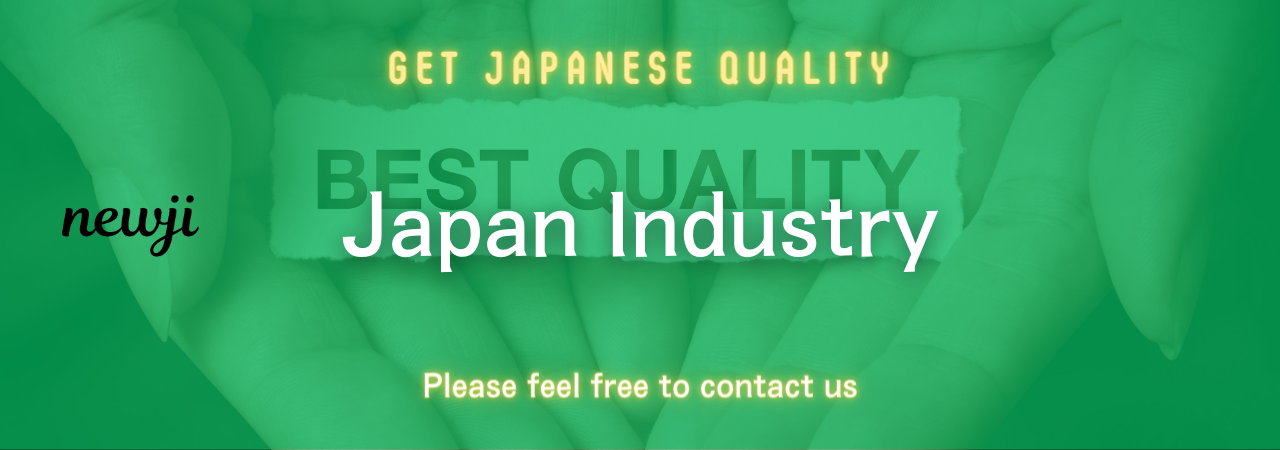
目次
Understanding Molding Cycle Times
In any manufacturing process, the efficiency and speed of production are crucial for maintaining competitiveness in the market.
Molding cycle time is a key component of this efficiency, especially in industries like plastics, where production rates impact profitability.
A molding cycle encompasses the entire process from when material enters the mold until the part is complete and ready for the next step.
Shortening this cycle without compromising quality can significantly enhance competitiveness.
To fully capitalize on this, manufacturers must understand each stage of the molding cycle and identify areas for improvement.
Identifying Key Stages in the Molding Cycle
The molding cycle consists of three primary stages: filling, packing, and cooling.
By examining these stages, manufacturers can pinpoint where time savings can be achieved.
Filling involves introducing molten material into the mold cavity.
During packing, pressure is applied to ensure the material fills all mold spaces and compensates for material shrinkage as it cools.
Finally, during cooling, the mold and its contents are prepared for ejection.
Each of these stages offers opportunities to reduce cycle time through process optimization.
Optimizing the Filling Stage
The filling stage is critical because it sets the tone for the rest of the cycle.
To optimize, manufacturers can focus on a few strategies.
First, adjusting the injection speed and pressure can help minimize the time required to fill the mold completely.
Using sensors to monitor and adjust these parameters in real-time can lead to significant improvements.
Additionally, the design of the mold plays a significant role.
Flow rates can be improved by minimizing flow length and complexity, allowing material to fill the mold more quickly.
Modern simulation software can help design engineers create efficient molds before production begins.
Refining the Packing Stage
Pack and hold times are pivotal in assuring quality and cycle time efficiency.
Again, real-time monitoring can bring significant advantages.
Manufacturers can adjust pack time based on part design, material viscosity, and mold temperature to ensure parts are fully packed without extending cycle time needlessly.
Experimenting with different waxes, fillers, and additives can also influence packing efficiency, leading to faster cycles while maintaining part integrity.
Think of it as customizing the process to fit the material’s behaviour, reducing unnecessary delays.
Enhancing the Cooling Stage
Cooling tends to be the longest part of the cycle, often making it the most substantial area for cycle time reduction.
The challenge is to ensure parts are firm enough to be ejected without warping.
One effective approach is improving the thermal management within the mold.
This can be achieved by advanced cooling channel design, facilitated by 3D printing technologies and conformal cooling inserts.
These technologies allow for even and rapid cooling throughout the part, significantly cutting down the time required.
Moreover, monitoring the temperature distribution using sensors can provide real-time insights and allow for adjustments on the fly.
Innovations in Material Science
Material selection is another area with profound implications for cycle time.
Emerging materials that have faster cooling times or less shrinkage can make significant contributions to efficiency.
By selecting materials that inherently require less energy and time to process, manufacturers can reduce cycle time without compromising quality.
Plastic and resin advancements, for example, continue to offer manufacturers opportunities to tweak the production process for quicker cycles.
Using materials with enhanced thermal conductivity reduces the cooling stage duration, thus shortening the entire cycle.
Automating the Production Process
Automation can greatly enhance the efficiency of the molding process.
From robotic arms to automated feed systems, employing advanced robotics can drastically reduce human error and increase production speed.
Automation ensures consistent cycle times and reduces downtime between cycles, thus enhancing competitiveness.
Furthermore, data analytics can be integrated with robotics to continually optimize the process.
Machine learning algorithms analyze real-time data to predict potential issues and suggest improvements, leading to continuous cycle time reductions.
Implementing Continuous Improvement Practices
Cycle time reduction is not a one-time event but a continuous commitment.
Adopting lean manufacturing principles and continuous improvement practices helps maintain a focus on efficiency.
Manufacturers should encourage a culture of innovation where employees are incentivized to identify inefficiencies and suggest improvements.
Regular training and workshops can keep teams updated with the latest techniques and technologies in the field.
Collaborative efforts across departments can yield creative solutions and foster a proactive improvement culture.
Measuring and Analyzing Results
The journey towards reduced molding cycle times should be measurable.
Establishing key performance indicators (KPIs) allows manufacturers to track progress and make data-driven decisions.
Cycle time analyses can benefit from real-time analytics to swiftly identify bottlenecks as they arise.
Starting with a clear baseline and regularly comparing performance metrics can ensure that improvements are quantifiable and persistent.
Incorporating feedback loops into the cycle review process ensures that adjustments are based on actual performance, not assumptions.
Staying Ahead in the Market
Shortening molding cycle times offers much more than just immediate cost savings.
It positions a company as agile and responsive—a critical asset for staying competitive in today’s fast-paced market.
The adaptability gained through cycle time reduction enables faster time-to-market for products, meeting customer demands promptly.
Furthermore, these efficiencies offer strategic capacity expansion without the need for significant additional investments.
By focusing on all aspects—process, materials, and people—manufacturers can continually enhance their competitive edge through optimized molding cycle times.
資料ダウンロード
QCD調達購買管理クラウド「newji」は、調達購買部門で必要なQCD管理全てを備えた、現場特化型兼クラウド型の今世紀最高の購買管理システムとなります。
ユーザー登録
調達購買業務の効率化だけでなく、システムを導入することで、コスト削減や製品・資材のステータス可視化のほか、属人化していた購買情報の共有化による内部不正防止や統制にも役立ちます。
NEWJI DX
製造業に特化したデジタルトランスフォーメーション(DX)の実現を目指す請負開発型のコンサルティングサービスです。AI、iPaaS、および先端の技術を駆使して、製造プロセスの効率化、業務効率化、チームワーク強化、コスト削減、品質向上を実現します。このサービスは、製造業の課題を深く理解し、それに対する最適なデジタルソリューションを提供することで、企業が持続的な成長とイノベーションを達成できるようサポートします。
オンライン講座
製造業、主に購買・調達部門にお勤めの方々に向けた情報を配信しております。
新任の方やベテランの方、管理職を対象とした幅広いコンテンツをご用意しております。
お問い合わせ
コストダウンが利益に直結する術だと理解していても、なかなか前に進めることができない状況。そんな時は、newjiのコストダウン自動化機能で大きく利益貢献しよう!
(Β版非公開)