- お役立ち記事
- Practical Techniques and Tips to Prevent Weld Line Formation
Practical Techniques and Tips to Prevent Weld Line Formation
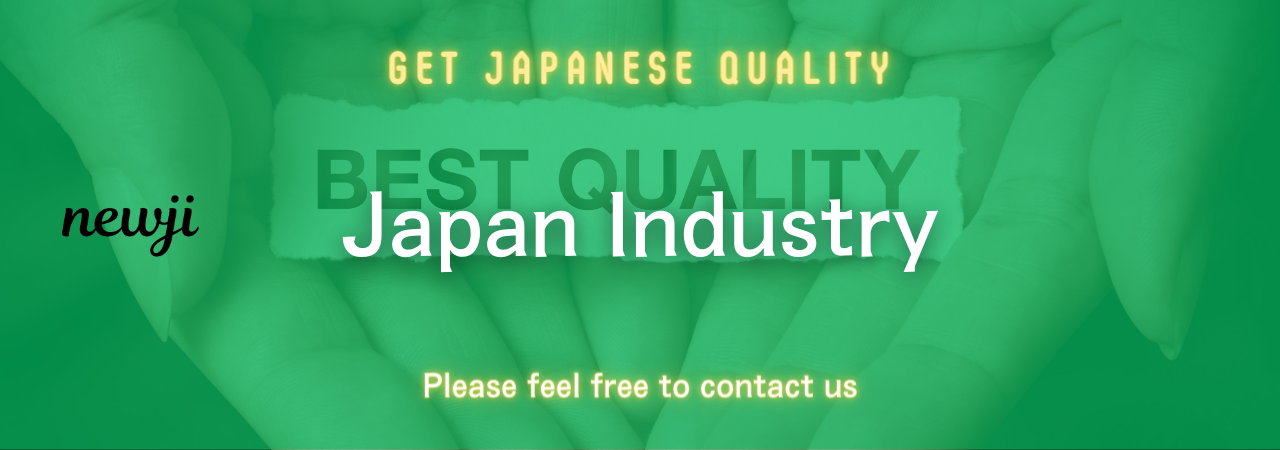
目次
Understanding Weld Lines
Weld lines, often referred to as knit lines, are a common issue in the manufacturing process, especially in injection molding.
They occur when two or more flow fronts of molten material meet and solidify before they fully integrate.
This results in a visible line or blemish on the surface of the molded part, potentially weakening the final product.
Understanding the science behind weld lines is the first step toward preventing their formation.
It’s crucial for manufacturers to recognize the impact these lines can have on the structural integrity and aesthetic value of a product.
The Causes of Weld Lines
To effectively minimize weld line formation, one must first understand their primary causes.
Several factors contribute to the development of these lines:
Material Factors
The type of polymer used in the injection molding process greatly influences the likelihood of weld line formation.
Viscosity and melting temperature play crucial roles.
Materials that do not flow easily or require high temperatures may tend to form poor welds, leading to visible lines.
Design Factors
The design of the mold, particularly in complex shapes with thin walls or varying thicknesses, can lead to multiple flow fronts.
Sharp corners, intersecting walls, or sudden changes in wall thickness can all encourage the formation of weld lines as the material struggles to fill the mold evenly.
Processing Factors
The processing conditions, such as injection speed, pressure, and temperature, are significant contributors.
If the injection speed is too slow, the molten material can cool and solidify, making it difficult for the flow fronts to meld seamlessly.
Additionally, if the temperature is not adequately controlled, it may lead to cool spots where weld lines are more likely to appear.
Practical Techniques to Prevent Weld Lines
Preventing weld lines is not just about altering one aspect of the process but requires a comprehensive approach, involving material selection, design adjustments, and process optimization.
Material Selection and Optimization
Choosing the right material is fundamental.
Opt for materials with better flow characteristics and lower melting temperatures to facilitate smoother melding of flow fronts.
Blends or additives can also be used to enhance material flow and reduce the likelihood of weld line formation.
Conducting thorough testing with pilot molds can help in selecting the best material for the specific requirements of a product.
Design Improvements
Engage in smarter mold design to minimize areas where weld lines are prone to form.
Incorporate fillets to reduce sharp corners, and ensure uniform wall thickness wherever possible.
Reducing intricate details in the mold can also help as these often necessitate multiple flow fronts.
Additionally, positioning gates strategically can improve the flow path and reduce potential weld line areas.
Processing Adjustments
Adjusting processing conditions can have a significant impact on weld line reduction.
Increasing the injection speed allows for the material to fill the mold before solidifying excessively.
Moreover, controlling the mold temperature ensures the molten polymer remains at an optimal temperature for longer periods, helping the flow fronts to merge seamlessly.
Holding pressure should also be optimized to push the material into the mold uniformly, minimizing weld line impact.
Advanced Techniques
Incorporating advanced techniques can further enhance weld line prevention strategies.
Improved Vents and Air Release
Proper venting in the mold design can aid in the movement of material, allowing air trapped between flow fronts to escape.
This prevents the formation of weak points where weld lines commonly develop.
Mold Surface Modification
Utilizing textured surfaces within the mold can also mask weld lines, making them less visible.
This is more applicable for parts where the aesthetic impact of weld lines is a concern.
Computer Simulation
Adapting computer-aided engineering (CAE) tools enables manufacturers to simulate the injection molding process and envisage where weld lines are likely to form.
With this insight, adjustments can be made preemptively in the design or process methodologies to counter potential issues.
Conclusion
Preventing weld line formation involves an integrated approach combining material choice, design considerations, and precise control over the injection molding process.
Understanding the underlying causes and utilizing practical and advanced techniques can greatly enhance the quality of the molded products.
Strategies such as optimizing material flow, enhancing mold design, and refining processing parameters contribute significantly to reducing the occurrence of weld lines.
Embracing technological advancements like computer simulations offers manufacturers a predictive edge, enabling them to address potential issues before they manifest physically.
By applying these strategies, the detrimental impact of weld lines on the structural integrity and aesthetic appeal of injection-molded products can be effectively mitigated.
資料ダウンロード
QCD調達購買管理クラウド「newji」は、調達購買部門で必要なQCD管理全てを備えた、現場特化型兼クラウド型の今世紀最高の購買管理システムとなります。
ユーザー登録
調達購買業務の効率化だけでなく、システムを導入することで、コスト削減や製品・資材のステータス可視化のほか、属人化していた購買情報の共有化による内部不正防止や統制にも役立ちます。
NEWJI DX
製造業に特化したデジタルトランスフォーメーション(DX)の実現を目指す請負開発型のコンサルティングサービスです。AI、iPaaS、および先端の技術を駆使して、製造プロセスの効率化、業務効率化、チームワーク強化、コスト削減、品質向上を実現します。このサービスは、製造業の課題を深く理解し、それに対する最適なデジタルソリューションを提供することで、企業が持続的な成長とイノベーションを達成できるようサポートします。
オンライン講座
製造業、主に購買・調達部門にお勤めの方々に向けた情報を配信しております。
新任の方やベテランの方、管理職を対象とした幅広いコンテンツをご用意しております。
お問い合わせ
コストダウンが利益に直結する術だと理解していても、なかなか前に進めることができない状況。そんな時は、newjiのコストダウン自動化機能で大きく利益貢献しよう!
(Β版非公開)