- お役立ち記事
- Practical techniques in the manufacturing industry learned from successful cases of trouble prevention
Practical techniques in the manufacturing industry learned from successful cases of trouble prevention
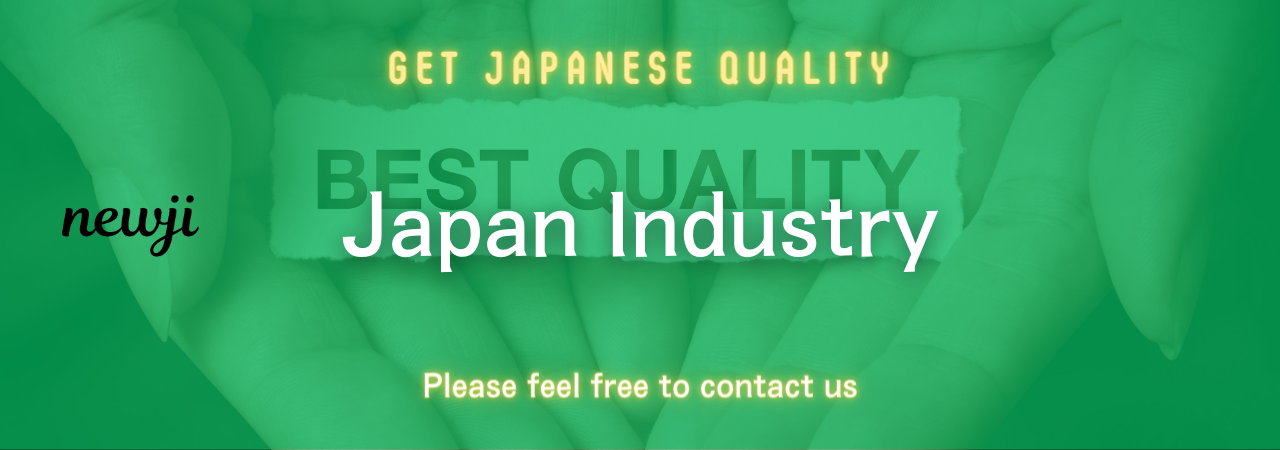
目次
Understanding the Importance of Trouble Prevention in Manufacturing
In the manufacturing industry, trouble prevention is a crucial aspect that ensures operations run smoothly without unexpected interruptions.
While minor issues may seem insignificant, they can escalate, leading to severe losses in time, resources, and revenue.
Successful companies have realized that implementing strategic measures can minimize these risks significantly.
This article delves into practical techniques drawn from successful cases that have effectively prevented troubles in the manufacturing sector.
Emphasizing Regular Maintenance
One of the simplest yet most effective techniques in preventing manufacturing troubles is regular maintenance.
Ensuring machines and equipment are routinely checked and serviced helps identify potential issues before they become significant problems.
Companies like Toyota have mastered the art of preventive maintenance, leading to increased efficiency and reduced downtime.
Incorporating a detailed maintenance schedule involves setting specific intervals for inspections, part replacements, and software updates.
This approach not only saves time but also optimizes the life cycle of equipment, ensuring they operate efficiently in the long term.
Implementing Risk Management Strategies
Risk management is another critical aspect of trouble prevention.
By identifying, assessing, and addressing potential risks ahead of time, manufacturing firms can dodge issues before they materialize.
A comprehensive risk management plan includes a clear understanding of both internal and external factors that can hinder operations.
For instance, companies like Siemens have taken proactive measures to evaluate risks involving supply chain disruptions, mechanical failures, and market fluctuations.
Utilizing advanced data analytics tools can enhance risk assessment by predicting trends and anticipating changes in demand.
Adopting Lean Manufacturing Principles
Lean manufacturing is a methodology focused on reducing waste within production systems while maximizing productivity.
This approach aids in trouble prevention by refining current processes and eliminating unnecessary steps that could lead to complications.
Pioneered by companies such as Toyota, lean manufacturing emphasizes continuous improvement (Kaizen) and just-in-time production.
Incorporating lean practices involves streamlining workflows, improving process layouts, and enhancing worker communication.
Companies can achieve a more efficient production line, fewer defects, and a more responsive manufacturing environment by adopting these principles.
Utilizing Predictive Maintenance Technologies
The advent of technology in manufacturing has introduced predictive maintenance as a viable solution for trouble prevention.
Predictive maintenance involves using data analysis and real-time monitoring to predict equipment failures before they occur.
This method goes beyond traditional maintenance by leveraging technological tools such as sensors and IoT devices.
Industry leaders like General Electric use predictive maintenance to monitor equipment conditions, identify wear patterns, and forecast potential breakdowns.
These insights allow for timely interventions, reducing the risk of unscheduled repairs and extending the lifespan of machinery.
Establishing a Robust Quality Control System
A reliable quality control system is imperative for preventing manufacturing troubles.
Quality control ensures that every product meets a specific standard before reaching the consumer, reducing the likelihood of defects and recalls.
Manufacturers such as Ford implement stringent quality control measures across their production lines to maintain high product standards.
A thorough quality control system involves consistent testing, inspection at various stages of production, and adhering to industry standards.
By ensuring that defects are caught early, manufacturers can avoid costly rework and safeguard their brand reputation.
Investing in Employee Training and Development
Skilled employees are the backbone of any successful manufacturing operation.
Adequate training and development programs ensure that workers are well-equipped to handle the technologies and processes used in modern manufacturing.
Training initiatives should focus on technical skills, safety procedures, and problem-solving techniques to empower employees.
Companies like BMW have invested heavily in employee training, resulting in a workforce that can identify and address potential issues effectively.
Ongoing training promotes a culture of vigilance and problem-solving, significantly reducing error rates and enhancing productivity.
Fostering Open Communication and Collaboration
Encouraging open communication and collaboration between departments plays a pivotal role in trouble prevention.
When teams work closely together, they can identify bottlenecks and brainstorm solutions more efficiently.
Collaborative efforts lead to improved processes and a unified approach to tackling challenges.
Companies like Procter & Gamble encourage cross-departmental teamwork, enabling a free exchange of ideas and fostering innovation.
Such an environment reduces silos, promotes transparency, and allows the organization to respond swiftly to potential disruptions.
Conclusion: A Proactive Approach to Trouble Prevention
Effective trouble prevention in manufacturing requires a proactive approach involving various strategies and techniques.
By learning from successful cases, manufacturers can implement practical measures like regular maintenance, risk management, and quality control systems.
Incorporating technology, lean principles, and investing in employee development also play a significant role in maintaining seamless operations.
Ultimately, adopting these techniques fosters a culture of continuous improvement and vigilance, ensuring long-term success in the ever-evolving manufacturing landscape.
資料ダウンロード
QCD調達購買管理クラウド「newji」は、調達購買部門で必要なQCD管理全てを備えた、現場特化型兼クラウド型の今世紀最高の購買管理システムとなります。
ユーザー登録
調達購買業務の効率化だけでなく、システムを導入することで、コスト削減や製品・資材のステータス可視化のほか、属人化していた購買情報の共有化による内部不正防止や統制にも役立ちます。
NEWJI DX
製造業に特化したデジタルトランスフォーメーション(DX)の実現を目指す請負開発型のコンサルティングサービスです。AI、iPaaS、および先端の技術を駆使して、製造プロセスの効率化、業務効率化、チームワーク強化、コスト削減、品質向上を実現します。このサービスは、製造業の課題を深く理解し、それに対する最適なデジタルソリューションを提供することで、企業が持続的な成長とイノベーションを達成できるようサポートします。
オンライン講座
製造業、主に購買・調達部門にお勤めの方々に向けた情報を配信しております。
新任の方やベテランの方、管理職を対象とした幅広いコンテンツをご用意しております。
お問い合わせ
コストダウンが利益に直結する術だと理解していても、なかなか前に進めることができない状況。そんな時は、newjiのコストダウン自動化機能で大きく利益貢献しよう!
(Β版非公開)