- お役立ち記事
- Practical Training Programs to Improve On-Site Capabilities of New and Young Employees in Manufacturing
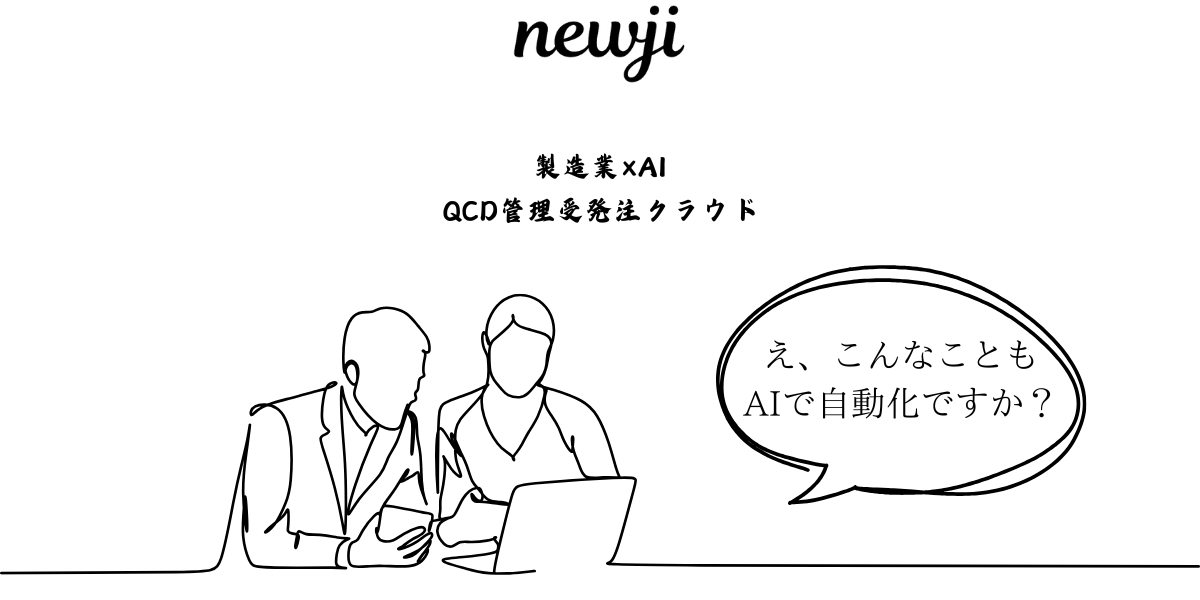
Practical Training Programs to Improve On-Site Capabilities of New and Young Employees in Manufacturing
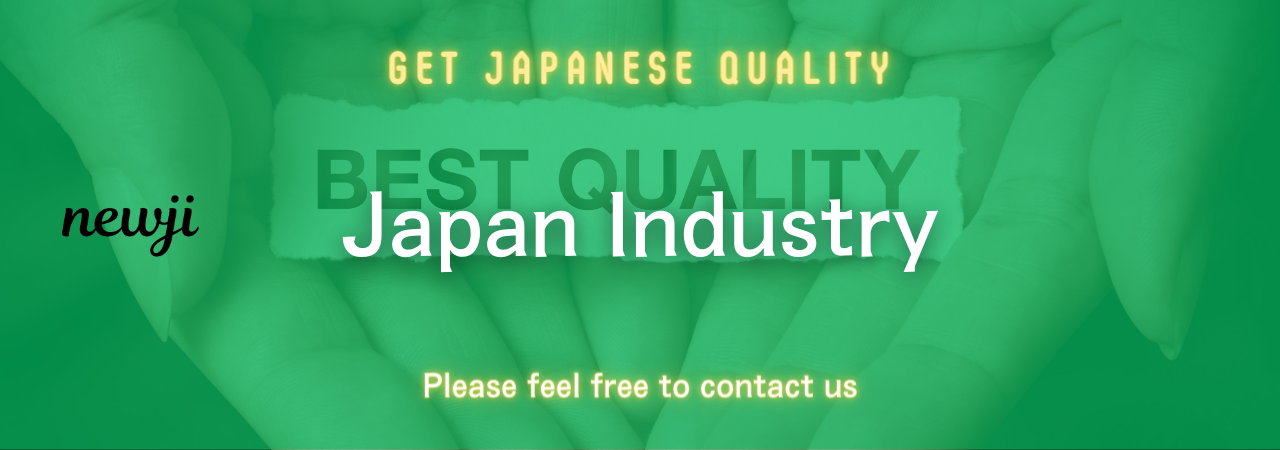
In today’s fast-paced manufacturing industry, it is crucial for new and young employees to possess strong on-site capabilities.
The ability to adapt to rapidly changing environments, solve complex problems, and operate machinery with precision are just a few of the necessary skills.
Practical training programs can significantly improve these capabilities, ensuring that the workforce is not only competent but also confident in their roles.
This article explores effective training methods that can help new and young employees excel in the manufacturing sector.
目次
Understanding On-Site Capabilities
On-site capabilities refer to the skills and competencies required to perform tasks efficiently in a manufacturing environment.
These include technical skills, problem-solving abilities, time management, and safety awareness.
By developing these skills through practical training, employees can contribute more effectively to the production process.
Technical Skills
Technical skills are the foundational abilities that employees need to operate machinery, use tools, and follow production processes.
Training in these skills ensures that workers can perform their tasks accurately and efficiently.
Problem-Solving Abilities
Problem-solving is essential in manufacturing, where unforeseen issues can arise at any time.
Training programs that focus on critical thinking and troubleshooting can help employees address and resolve problems quickly.
Time Management
Effective time management is crucial in meeting production deadlines.
Training in this area helps employees prioritize tasks, manage their workload, and work more efficiently.
Safety Awareness
Safety is paramount in any manufacturing setting.
Training programs should emphasize the importance of safety protocols and procedures, ensuring that employees can work without risk.
Types of Practical Training Programs
Various training programs can be implemented to enhance the on-site capabilities of new and young employees in manufacturing.
These programs can be tailored to meet the specific needs of the workforce and the organization.
Hands-On Training
Hands-on training is one of the most effective ways to teach new employees the skills they need.
This type of training involves direct interaction with machinery and tools, allowing employees to gain practical experience.
Supervisors and experienced workers can provide guidance and support, ensuring that trainees learn the correct methods.
Simulation-Based Training
Simulation-based training uses computer programs to replicate real-world scenarios that employees might encounter on the job.
This method allows trainees to practice their skills in a controlled environment without the risk of real-world consequences.
Simulations can cover various aspects of manufacturing, from machine operation to emergency response.
Mentorship Programs
Mentorship programs pair new employees with experienced workers who can provide guidance, support, and knowledge.
Mentors can share their expertise, helping trainees develop their skills and navigate the complexities of the manufacturing industry.
Workshops and Seminars
Workshops and seminars offer opportunities for employees to learn new techniques and stay updated with industry trends.
These programs can cover a range of topics, from the latest technological advancements to best practices in manufacturing.
Interactive sessions encourage participation and engagement, making the learning process more effective.
Online Training Modules
Online training modules provide flexible learning options for employees.
These modules can be completed at the trainee’s convenience, making it easier to balance work and training.
Topics can range from basic skills to advanced manufacturing techniques, catering to various levels of expertise.
Implementing Effective Training Programs
Successful implementation of training programs requires careful planning and execution.
Here are some strategies to ensure that training programs are effective in improving on-site capabilities.
Assess Needs and Set Goals
Before implementing a training program, it is essential to assess the specific needs of the workforce.
Identify the skills and competencies that require improvement and set clear, achievable goals.
This ensures that the training program is targeted and relevant.
Develop a Comprehensive Curriculum
A well-structured curriculum is crucial to the success of any training program.
It should cover all necessary topics and provide a balanced mix of theoretical knowledge and practical experience.
Ensure that the curriculum is designed to meet the needs of the trainees and the organization.
Utilize Experienced Trainers
Trainers with extensive experience in the manufacturing industry can provide valuable insights and guidance.
They can share practical tips and real-world examples that enhance the learning experience.
Ensure that trainers are well-versed in the latest industry standards and practices.
Evaluate and Adjust
Regular evaluation of the training program is necessary to measure its effectiveness.
Collect feedback from trainees and trainers to identify areas for improvement.
Make necessary adjustments to the program to ensure that it remains relevant and effective.
Conclusion
Practical training programs are essential for improving the on-site capabilities of new and young employees in manufacturing.
By focusing on technical skills, problem-solving abilities, time management, and safety awareness, these programs ensure that employees are well-prepared for their roles.
Various training methods, including hands-on training, simulation-based training, mentorship programs, workshops, seminars, and online modules, can be tailored to meet the specific needs of the workforce.
Careful planning, a comprehensive curriculum, experienced trainers, and regular evaluation are key to the successful implementation of training programs.
By investing in practical training, manufacturing organizations can build a skilled, confident, and productive workforce.
資料ダウンロード
QCD調達購買管理クラウド「newji」は、調達購買部門で必要なQCD管理全てを備えた、現場特化型兼クラウド型の今世紀最高の購買管理システムとなります。
ユーザー登録
調達購買業務の効率化だけでなく、システムを導入することで、コスト削減や製品・資材のステータス可視化のほか、属人化していた購買情報の共有化による内部不正防止や統制にも役立ちます。
NEWJI DX
製造業に特化したデジタルトランスフォーメーション(DX)の実現を目指す請負開発型のコンサルティングサービスです。AI、iPaaS、および先端の技術を駆使して、製造プロセスの効率化、業務効率化、チームワーク強化、コスト削減、品質向上を実現します。このサービスは、製造業の課題を深く理解し、それに対する最適なデジタルソリューションを提供することで、企業が持続的な成長とイノベーションを達成できるようサポートします。
オンライン講座
製造業、主に購買・調達部門にお勤めの方々に向けた情報を配信しております。
新任の方やベテランの方、管理職を対象とした幅広いコンテンツをご用意しております。
お問い合わせ
コストダウンが利益に直結する術だと理解していても、なかなか前に進めることができない状況。そんな時は、newjiのコストダウン自動化機能で大きく利益貢献しよう!
(Β版非公開)