- お役立ち記事
- Precision 3D scanning technology for wood and optimization of automatic processing control
月間76,176名の
製造業ご担当者様が閲覧しています*
*2025年3月31日現在のGoogle Analyticsのデータより
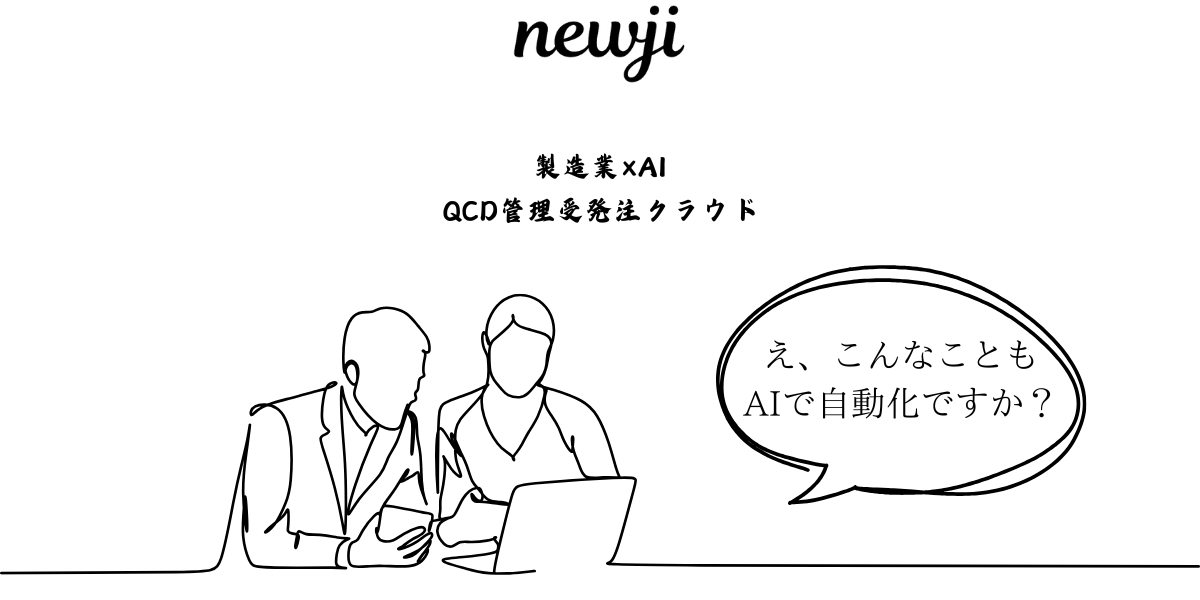
Precision 3D scanning technology for wood and optimization of automatic processing control
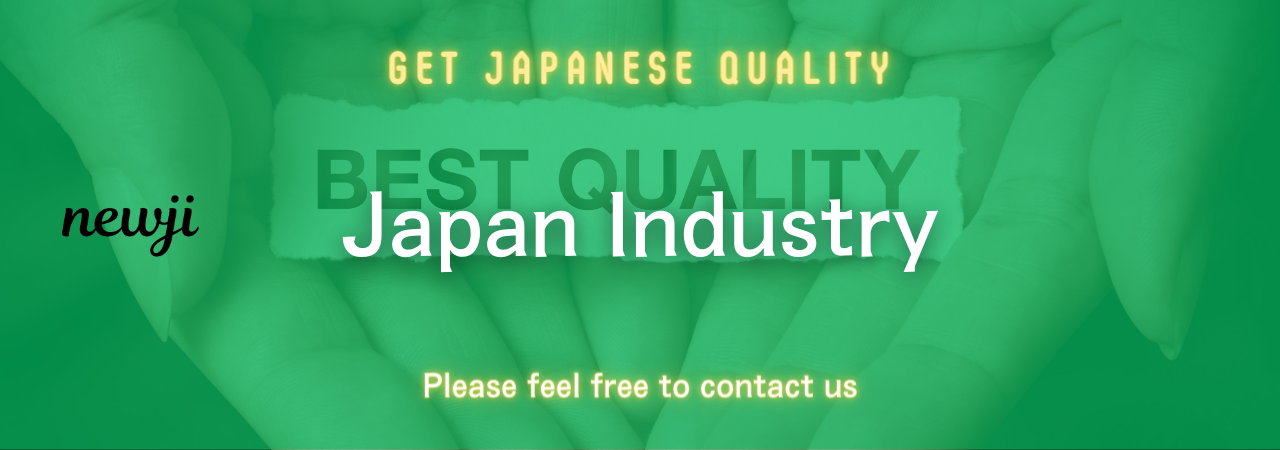
目次
Introduction to Precision 3D Scanning Technology
The realm of woodworking has seen a remarkable transformation with the advent of precision 3D scanning technology.
This innovative approach is reshaping the way woodworkers, manufacturers, and designers approach their craft.
At its core, 3D scanning for wood involves capturing the precise dimensions and intricate details of wooden materials.
This data is then used to optimize various processes, ensuring enhanced quality and efficiency.
How 3D Scanning Works with Wood
3D scanning technology relies on advanced sensors and software to create detailed digital models of wooden objects.
The process begins with a scan of the surface of the wood, usually utilizing laser or structured light scanners.
These scanners map every contour of the wood, generating a highly accurate digital replica.
Once the scan is complete, specialized software processes the data to create a 3D model.
This model can be used for a variety of purposes, such as analyzing the quality of the wood, planning cuts, and ensuring that the final product meets precise specifications.
Benefits of 3D Scanning Technology in Woodworking
The integration of 3D scanning technology in woodworking offers several advantages.
Firstly, it significantly enhances precision.
Traditional methods of measurement can introduce errors, but 3D scanning eliminates these inaccuracies by providing exact measurements.
Moreover, the technology aids in optimizing material usage.
By understanding the precise dimensions and characteristics of each piece of wood, manufacturers can minimize waste and make more efficient use of their resources.
This leads to cost savings and a more sustainable approach to woodworking.
Another benefit is the facilitation of complex designs.
3D scanning allows designers to visualize and manipulate intricate patterns and structures that would be challenging to achieve manually.
This opens up new possibilities for creativity and innovation in woodworking.
Applications of 3D Scanning in the Wood Industry
3D scanning technology is utilized in various aspects of the wood industry.
In manufacturing, it plays a pivotal role in quality control.
By comparing the scanned model to the intended design, manufacturers can detect any deviations or defects early in the production process.
This ensures that only high-quality products reach the market.
In restoration and conservation projects, 3D scanning offers a non-invasive method to document and analyze historical wood artifacts.
This technology helps in creating precise reproductions or restorations while preserving the integrity of the original pieces.
It is also used in furniture design, where custom and ergonomic solutions are in demand.
Designers can scan existing pieces to modify or innovate upon them, ensuring that new designs are aesthetically pleasing and functionally superior.
Optimization of Automatic Processing Control
The pairing of 3D scanning technology with automatic processing control systems optimizes manufacturing operations.
Automated machinery equipped with precision 3D scanning capabilities can adjust in real-time, accommodating variations in the wood.
This ensures smoother operations and reduces the need for human intervention.
Impact on Production Efficiency
Automation driven by 3D scanning technology drastically improves production efficiency.
Machines can identify and adapt to imperfections or changes in the material, reducing downtime and speeding up the manufacturing process.
This adaptability allows for consistent production quality, even in large-scale operations.
Furthermore, the integration of 3D scanning in automated systems facilitates predictive maintenance.
By continuously scanning and analyzing the machinery’s operations, these systems can predict and address maintenance issues before they lead to significant disruptions.
Future of 3D Scanning and Automation in Woodworking
As technology advances, the capabilities of 3D scanning and automation in woodworking are expected to grow.
With ongoing developments in artificial intelligence and machine learning, these systems will become increasingly intelligent and autonomous.
The future might see the creation of smart factories where 3D scanning data is used to inform every step of the production process.
This will lead to even greater efficiencies and the ability to customize products on-demand, meeting specific customer requirements with precision.
In educational contexts, 3D scanning will likely become a standard tool for woodworking training programs.
Aspiring woodworkers will benefit from understanding how this technology can enhance their craft, preparing them for a technology-driven industry.
Conclusion
Precision 3D scanning technology is a transformative force in the woodworking industry.
Its ability to capture detailed digital representations of wood paves the way for enhanced precision, improved material utilization, and the creation of complex designs.
When coupled with automatic processing control, it leads to optimized manufacturing processes and significant production efficiencies.
As the technology continues to evolve, the wood industry stands on the brink of a new era of innovation and excellence.
Embracing these advancements will undoubtedly yield long-term benefits for manufacturers, designers, and consumers alike.
資料ダウンロード
QCD管理受発注クラウド「newji」は、受発注部門で必要なQCD管理全てを備えた、現場特化型兼クラウド型の今世紀最高の受発注管理システムとなります。
ユーザー登録
受発注業務の効率化だけでなく、システムを導入することで、コスト削減や製品・資材のステータス可視化のほか、属人化していた受発注情報の共有化による内部不正防止や統制にも役立ちます。
NEWJI DX
製造業に特化したデジタルトランスフォーメーション(DX)の実現を目指す請負開発型のコンサルティングサービスです。AI、iPaaS、および先端の技術を駆使して、製造プロセスの効率化、業務効率化、チームワーク強化、コスト削減、品質向上を実現します。このサービスは、製造業の課題を深く理解し、それに対する最適なデジタルソリューションを提供することで、企業が持続的な成長とイノベーションを達成できるようサポートします。
製造業ニュース解説
製造業、主に購買・調達部門にお勤めの方々に向けた情報を配信しております。
新任の方やベテランの方、管理職を対象とした幅広いコンテンツをご用意しております。
お問い合わせ
コストダウンが利益に直結する術だと理解していても、なかなか前に進めることができない状況。そんな時は、newjiのコストダウン自動化機能で大きく利益貢献しよう!
(β版非公開)