- お役立ち記事
- Precision and Excellence: The Role of Calibration in Japanese Manufacturing Innovation
Precision and Excellence: The Role of Calibration in Japanese Manufacturing Innovation
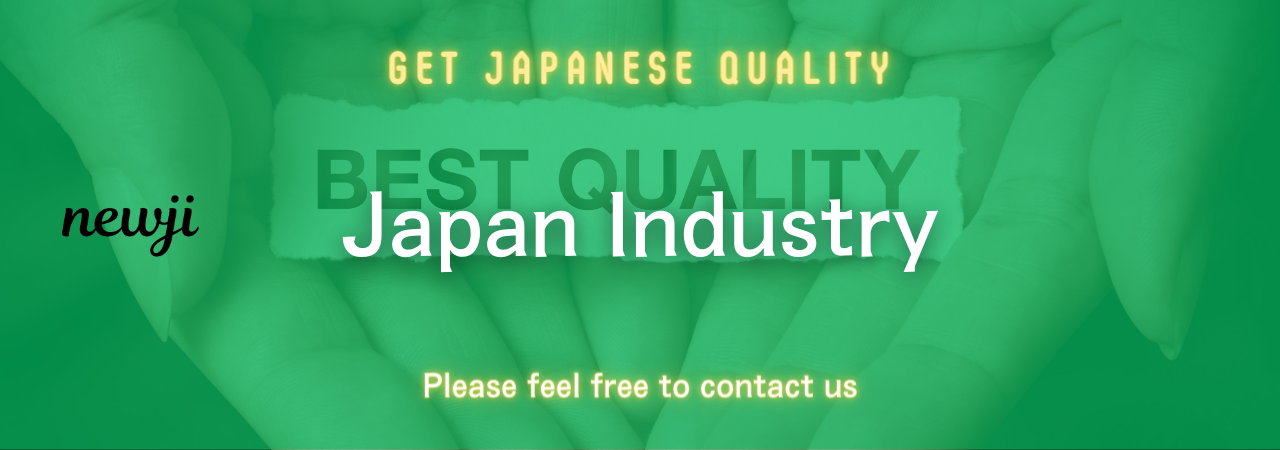
目次
Introduction to Calibration in Japanese Manufacturing
Calibration plays a pivotal role in the success and innovation of Japanese manufacturing. Renowned for their precision and quality, Japanese manufacturers have integrated calibration into their core processes to ensure that every product meets the highest standards. This dedication to accuracy not only enhances product performance but also fosters trust and reliability among consumers and business partners worldwide.
The Importance of Calibration in Manufacturing
Calibration involves adjusting and verifying the accuracy of measurement instruments and equipment used in manufacturing. In Japanese manufacturing, precision is not just a goal but a fundamental principle that drives excellence. Proper calibration ensures that all components and systems operate within specified tolerances, minimizing errors and defects. This meticulous attention to detail leads to:
Enhanced Product Quality
Consistent calibration ensures that every product maintains uniform quality, reducing variability and defects. This commitment to quality control is a cornerstone of Japanese manufacturing, allowing companies to produce reliable and durable products that meet stringent international standards.
Increased Efficiency and Productivity
Calibrated equipment operates more efficiently, reducing downtime and maintenance costs. By ensuring that machinery functions optimally, manufacturers can streamline production processes, increase output, and maintain high productivity levels without compromising on quality.
Cost Reduction
Accurate calibration minimizes waste by reducing the number of defective products and rework required. This not only lowers production costs but also enhances profitability by optimizing the use of materials and resources.
Advantages of Calibration in Japanese Manufacturing
Japanese manufacturing leverages calibration to gain a competitive edge in the global market. The advantages of this approach include:
Global Reputation for Excellence
Japanese manufacturers are globally recognized for their precision and quality. Consistent calibration practices contribute to this reputation, making Japanese products highly sought after in various industries, including automotive, electronics, and machinery.
Innovation and Continuous Improvement
Calibration is integral to the Japanese philosophy of Kaizen, or continuous improvement. Regularly calibrated equipment allows for the fine-tuning of production processes, fostering innovation and the development of new technologies and products.
Compliance with International Standards
Adhering to international calibration standards ensures that Japanese manufacturers meet global regulatory requirements. This compliance is essential for exporting products to different markets, ensuring that they meet the necessary quality and safety standards.
Customer Satisfaction and Loyalty
High-quality, reliable products lead to increased customer satisfaction and loyalty. By maintaining stringent calibration practices, Japanese manufacturers can consistently deliver products that meet or exceed customer expectations, fostering long-term relationships and repeat business.
Challenges and Disadvantages of Calibration
While calibration offers numerous benefits, it also presents certain challenges that Japanese manufacturers must address.
High Initial Investment
Implementing comprehensive calibration systems requires significant upfront investment in calibration equipment, training, and infrastructure. This can be a barrier for smaller manufacturers or those with limited financial resources.
Ongoing Maintenance and Costs
Calibration is not a one-time process but requires regular maintenance and re-calibration. This ongoing commitment can lead to increased operational costs and logistical challenges, particularly for companies with extensive manufacturing operations.
Technical Expertise Required
Effective calibration demands specialized knowledge and skills. Japanese manufacturers must invest in training their workforce or hiring experts to ensure that calibration processes are accurately performed and maintained.
Supplier Negotiation Techniques for Calibration Services
Effective supplier negotiation is crucial for securing reliable calibration services and equipment. Japanese manufacturers employ several negotiation techniques to achieve favorable terms and ensure quality.
Building Long-Term Relationships
Japanese business culture emphasizes long-term relationships and mutual trust. By fostering strong relationships with calibration service providers, manufacturers can secure better terms, priority service, and consistent quality.
Clear Specification and Standards
Clearly defining calibration requirements and standards is essential. Japanese manufacturers meticulously outline their specifications to ensure that suppliers understand and can meet their precise needs, reducing the risk of errors and misunderstandings.
Competitive Bidding and Supplier Evaluation
Japanese manufacturers often engage in competitive bidding to identify the best suppliers. Comprehensive evaluation criteria, including quality, reliability, cost, and service capabilities, are used to select suppliers that align with the company’s standards and objectives.
Collaborative Approach
Adopting a collaborative approach helps in negotiating terms that are beneficial for both parties. By working together with suppliers to solve problems and improve processes, manufacturers can achieve better outcomes and stronger partnerships.
Market Conditions Impacting Calibration in Japan
Understanding the market conditions is crucial for Japanese manufacturers to navigate the calibration landscape effectively.
Technological Advancements
Rapid advancements in technology require continuous updates to calibration equipment and processes. Japanese manufacturers must stay abreast of the latest developments to maintain their competitive edge and ensure that their calibration practices remain state-of-the-art.
Global Supply Chain Dynamics
Global supply chain disruptions can impact the availability and cost of calibration services and equipment. Japanese manufacturers need to develop resilient supply chains and diversify their supplier base to mitigate risks associated with geopolitical tensions, natural disasters, and other unforeseen events.
Regulatory Environment
Changing international regulations can affect calibration standards and requirements. Japanese manufacturers must stay informed about regulatory changes in their target markets and adjust their calibration practices accordingly to ensure compliance and avoid penalties.
Economic Factors
Economic fluctuations can influence the cost and demand for calibration services. In times of economic downturn, manufacturers may seek cost-effective calibration solutions, while during periods of growth, there may be increased investment in advanced calibration technologies.
Best Practices in Calibration for Japanese Manufacturers
Adopting best practices in calibration is essential for maintaining high standards and driving innovation in Japanese manufacturing.
Implementing a Calibration Management System
A robust calibration management system ensures that all calibration activities are systematically planned, executed, and documented. This includes scheduling regular calibrations, maintaining records of calibration results, and ensuring traceability to international standards.
Training and Skill Development
Continuous training and skill development for employees involved in calibration processes are critical. Japanese manufacturers invest in training programs to enhance the technical expertise of their workforce, ensuring that calibration activities are performed accurately and efficiently.
Leveraging Automation and Advanced Technologies
Integrating automation and advanced technologies, such as IoT and AI, can enhance calibration processes. Automated calibration systems can increase precision, reduce human error, and provide real-time monitoring and data analysis, leading to more effective calibration management.
Regular Audits and Assessments
Conducting regular audits and assessments of calibration processes helps identify areas for improvement and ensure compliance with standards. Japanese manufacturers use these assessments to maintain the integrity of their calibration practices and continuously enhance their manufacturing processes.
Collaborating with Suppliers and Partners
Collaboration with suppliers and partners is key to optimizing calibration processes. By working closely with calibration service providers and equipment manufacturers, Japanese manufacturers can ensure that they have access to the latest technologies and best practices, fostering innovation and maintaining high quality.
The Future of Calibration in Japanese Manufacturing
As Japanese manufacturers continue to lead in precision and quality, the role of calibration will evolve to meet emerging challenges and opportunities.
Integration with Industry 4.0
Industry 4.0 technologies, such as smart factories, connected devices, and big data analytics, offer new possibilities for calibration. Integrating calibration into these advanced manufacturing systems can enhance real-time monitoring, predictive maintenance, and process optimization.
Sustainability and Green Manufacturing
Sustainable manufacturing practices are becoming increasingly important. Calibration can contribute to sustainability by optimizing resource usage, reducing waste, and improving energy efficiency. Japanese manufacturers are likely to focus on environmentally friendly calibration practices as part of their broader sustainability initiatives.
Global Expansion and Localization
As Japanese manufacturers expand globally, they will need to adapt their calibration practices to diverse regional standards and requirements. Localization of calibration processes can help in meeting specific market demands and regulatory standards, ensuring seamless integration into new markets.
Enhanced Data Analytics and AI
Advancements in data analytics and artificial intelligence will further enhance calibration processes. Predictive analytics can anticipate calibration needs, reduce downtime, and improve overall efficiency. AI-driven calibration systems can continuously learn and adapt, providing more accurate and reliable results.
Conclusion
Calibration is a cornerstone of Japanese manufacturing excellence, underpinning the precision, quality, and reliability that define the industry. By implementing rigorous calibration practices, Japanese manufacturers achieve superior product quality, operational efficiency, and customer satisfaction. Despite the challenges, the benefits of calibration – including enhanced reputation, innovation, and compliance – make it an indispensable element of manufacturing success.
As the industry evolves, Japanese manufacturers continue to adapt their calibration strategies, integrating advanced technologies and sustainable practices to maintain their leadership in global markets. Through continuous improvement and a commitment to precision, calibration will remain a vital driver of innovation and excellence in Japanese manufacturing for years to come.
資料ダウンロード
QCD調達購買管理クラウド「newji」は、調達購買部門で必要なQCD管理全てを備えた、現場特化型兼クラウド型の今世紀最高の購買管理システムとなります。
ユーザー登録
調達購買業務の効率化だけでなく、システムを導入することで、コスト削減や製品・資材のステータス可視化のほか、属人化していた購買情報の共有化による内部不正防止や統制にも役立ちます。
NEWJI DX
製造業に特化したデジタルトランスフォーメーション(DX)の実現を目指す請負開発型のコンサルティングサービスです。AI、iPaaS、および先端の技術を駆使して、製造プロセスの効率化、業務効率化、チームワーク強化、コスト削減、品質向上を実現します。このサービスは、製造業の課題を深く理解し、それに対する最適なデジタルソリューションを提供することで、企業が持続的な成長とイノベーションを達成できるようサポートします。
オンライン講座
製造業、主に購買・調達部門にお勤めの方々に向けた情報を配信しております。
新任の方やベテランの方、管理職を対象とした幅広いコンテンツをご用意しております。
お問い合わせ
コストダウンが利益に直結する術だと理解していても、なかなか前に進めることができない状況。そんな時は、newjiのコストダウン自動化機能で大きく利益貢献しよう!
(Β版非公開)