- お役立ち記事
- Precision grinding and its know-how learned from the basics
月間77,185名の
製造業ご担当者様が閲覧しています*
*2025年2月28日現在のGoogle Analyticsのデータより
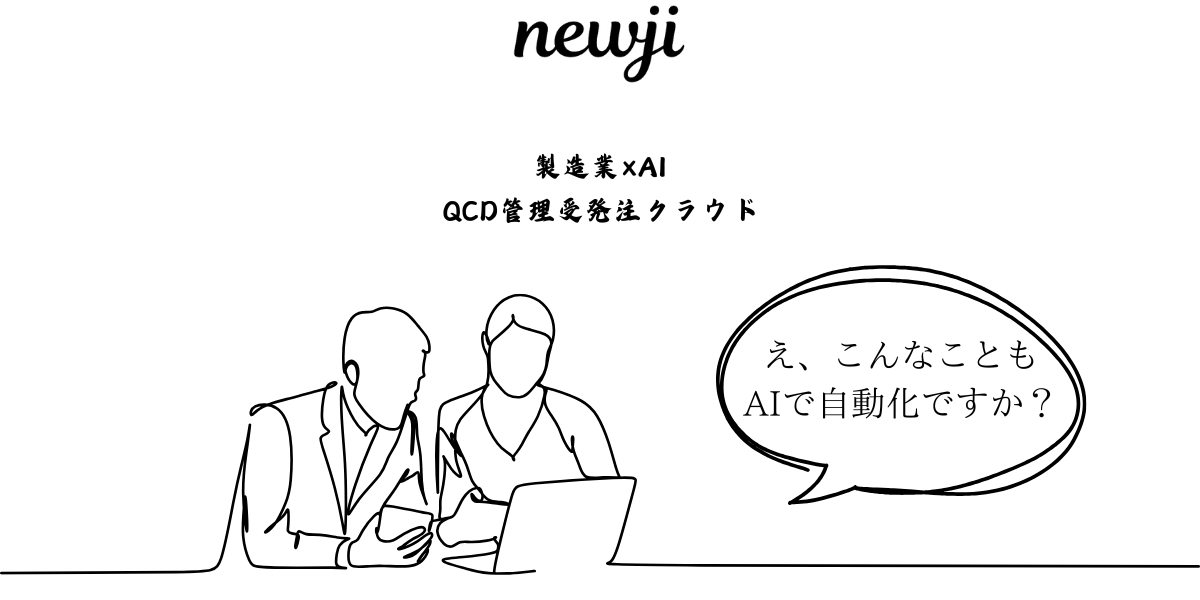
Precision grinding and its know-how learned from the basics
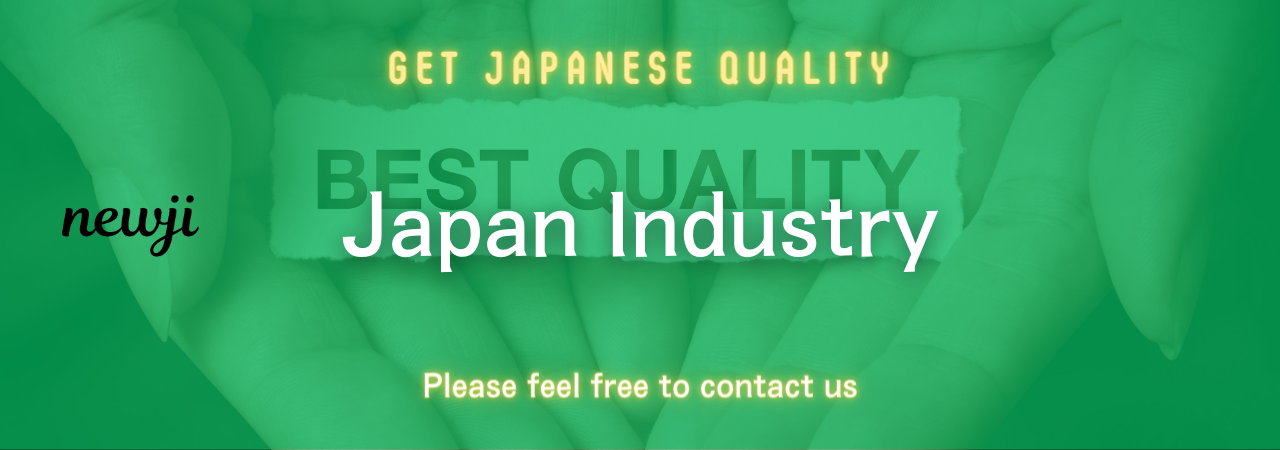
Precision grinding is a critical process in the manufacturing industry, providing the ability to create smooth, accurate, and complex parts. Understanding the basics of precision grinding is essential for anyone involved in manufacturing or interested in learning about this essential technique.
目次
What is Precision Grinding?
Precision grinding is a machining process that involves the removal of material from a workpiece using abrasive tools or machines. It is used to achieve high levels of accuracy and smooth finishes, making it ideal for parts that require tight tolerances. The process can be applied to a variety of materials, including metals, ceramics, and composites.
Types of Precision Grinding
There are several types of precision grinding, each with its own methods and applications.
Surface grinding is one of the most common types, and it involves grinding the surface of a workpiece to achieve a smooth and flat finish. This is typically done using a grinding wheel.
Cylindrical grinding is used to shape the outside of a workpiece. It is often used for parts that require precise diameters or finishes and can be applied to both the outside and inside of the part.
Centerless grinding is another popular method, used to remove material from the outside of a workpiece without the need for centering. This technique is useful for parts with complex geometries or requiring large batches to be processed quickly.
Internal grinding focuses on the inside surfaces of a workpiece, providing the ability to achieve precise holes and bores.
The Basics of Precision Grinding
To master precision grinding, it is crucial to understand the basic principles.
Abrasives
The choice of abrasive is fundamental to the grinding process. Abrasives are hard materials that wear down the surface of the workpiece. Common abrasives include aluminum oxide, silicon carbide, and diamond. Each type has its properties, benefits, and ideal applications, so selecting the right abrasive is essential for an efficient and effective grinding process.
Grinding Machines
Precision grinding requires specialized machinery designed to handle different grinding tasks. These machines vary in size, capability, and complexity. The most common types of grinding machines include:
– Surface grinders
– Cylindrical grinders
– Centerless grinders
– Internal grinders
Each machine type has its specific use, suited to different grinding tasks and requirements.
Grinding Wheel Selection
Critical to the success of the precision grinding process is the selection of the appropriate grinding wheel. Various factors must be considered, such as the type of abrasive, the size and shape of the wheel, and its bonding material. The choice depends on the workpiece material, desired finish, and the specific grinding machine being used.
Tolerances and Surface Finishes
Understanding tolerances and surface finishes is crucial in precision grinding. Tight tolerances are essential for parts to fit properly in assemblies, while surface finishes determine the smoothness of the part. Grinding operations must be carefully controlled to achieve the desired tolerances and finishes.
Advantages of Precision Grinding
Precision grinding offers several advantages over other machining processes.
High Accuracy
The main benefit of precision grinding is its ability to produce parts with extremely high accuracy. This is critical in industries where precision is mandatory, such as aerospace, automotive, and medical.
Excellent Surface Finish
Precision grinding provides superior surface finishes, which are often required in high-performance applications. This makes the parts not only functional but also aesthetically pleasing and free of sharp edges or burrs.
Versatility
Precision grinding can be applied to a wide range of materials and shapes, making it a versatile solution for complex parts. It also allows for the processing of large volumes of parts efficiently.
Challenges in Precision Grinding
While precision grinding offers numerous benefits, it also presents some challenges.
Complexity
The process requires a deep understanding of materials, tools, and machinery to be successful. Mastering the technique can take time and experience, making it a specialized skill.
Cost
Precision grinding generally involves higher costs due to the use of specialized equipment and tools. Additionally, the need for skilled operators can add to the overall expense.
Tool Wear and Maintenance
Grinding tools and machines require regular maintenance and replacement to ensure consistent performance. Tool wear must be monitored to maintain precision and avoid compromising the quality of the workpiece.
Conclusion
Precision grinding is indispensable in modern manufacturing, offering unmatched accuracy and finish quality. Understanding its basic principles, tools, and machines is crucial for producing high-quality components. Though the process presents some challenges, its advantages far outweigh the costs, making it a critical technique in various industries.
By mastering the intricacies of precision grinding, manufacturers can ensure that their products meet the highest standards of precision and quality. The ability to transform raw materials into intricate, precision-engineered parts is a testament to the importance of precision grinding in today’s manufacturing landscape.
資料ダウンロード
QCD管理受発注クラウド「newji」は、受発注部門で必要なQCD管理全てを備えた、現場特化型兼クラウド型の今世紀最高の受発注管理システムとなります。
ユーザー登録
受発注業務の効率化だけでなく、システムを導入することで、コスト削減や製品・資材のステータス可視化のほか、属人化していた受発注情報の共有化による内部不正防止や統制にも役立ちます。
NEWJI DX
製造業に特化したデジタルトランスフォーメーション(DX)の実現を目指す請負開発型のコンサルティングサービスです。AI、iPaaS、および先端の技術を駆使して、製造プロセスの効率化、業務効率化、チームワーク強化、コスト削減、品質向上を実現します。このサービスは、製造業の課題を深く理解し、それに対する最適なデジタルソリューションを提供することで、企業が持続的な成長とイノベーションを達成できるようサポートします。
製造業ニュース解説
製造業、主に購買・調達部門にお勤めの方々に向けた情報を配信しております。
新任の方やベテランの方、管理職を対象とした幅広いコンテンツをご用意しております。
お問い合わせ
コストダウンが利益に直結する術だと理解していても、なかなか前に進めることができない状況。そんな時は、newjiのコストダウン自動化機能で大きく利益貢献しよう!
(β版非公開)