- お役立ち記事
- Precision part modeling methods using 3D-CAD that design department leaders in the electronic parts manufacturing industry should know
Precision part modeling methods using 3D-CAD that design department leaders in the electronic parts manufacturing industry should know
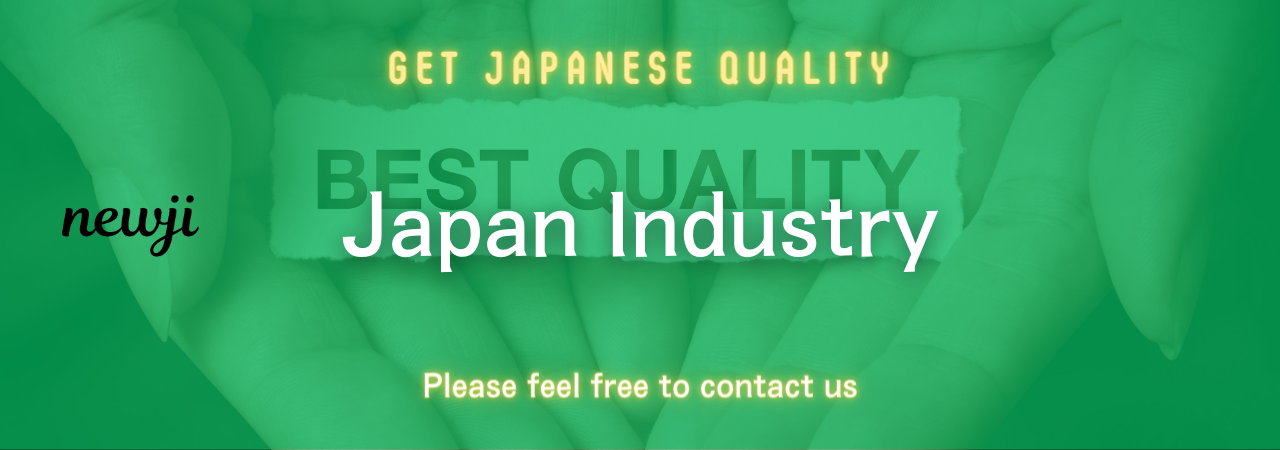
In today’s rapidly evolving electronic parts manufacturing industry, precision is paramount.
As a leader in the design department, it is crucial to stay updated with the latest technologies and methods that can enhance the accuracy and efficiency of your designs.
3D-CAD, or three-dimensional computer-aided design, has become an indispensable tool for creating precise digital models of parts and assemblies.
This article explores the essential methods of precision part modeling using 3D-CAD that design department leaders should know.
目次
Understanding the Basics of 3D-CAD
3D-CAD technology allows engineers and designers to create detailed digital models of physical objects.
These models can be viewed, manipulated, and analyzed on a computer, significantly enhancing the design process.
Understanding the basics of 3D-CAD is the first step toward mastering precision modeling.
Components of 3D-CAD Software
3D-CAD software typically consists of several core components: the user interface, sketching tools, part modeling tools, and assembly modeling capabilities.
The user interface provides access to various features and functions, enabling users to interact with the software easily.
Sketching tools allow designers to create 2D representations that can be transformed into 3D models.
Part modeling tools help in constructing detailed components, while assembly modeling capabilities enable the integration of various parts into a complete system.
Key Methods for Precision Part Modeling
Precision in part modeling can be achieved through a combination of techniques and features available in 3D-CAD software.
Let’s delve into some of the crucial methods that every design department leader should know.
Parametric Modeling
Parametric modeling is a method that involves defining parameters, such as dimensions and constraints, to control the shape and features of a model.
In this method, changes to the parameters automatically update the model, ensuring consistency and precision.
This approach is incredibly useful when designing parts that require strict adherence to specifications, as it minimizes errors and reduces the need for extensive manual adjustments.
Feature-Based Modeling
Feature-based modeling involves constructing models by defining various features, such as holes, extrusions, and fillets.
This method allows designers to conceptualize parts based on their geometric features, simplifying the design process.
By breaking down a model into its fundamental features, designers can easily modify specific parts without affecting the overall structure.
This flexibility is crucial for precision, as it enables quick iterations and fine-tuning of designs.
Advanced Surface Modeling
For designs requiring complex surfaces, such as aerodynamic components, advanced surface modeling is essential.
This method involves creating intricate surface geometries that are not easily achievable through basic solid modeling.
By utilizing tools like lofting, sweeping, and freeform surface creation, designers can achieve highly detailed and precise surface models.
Advanced surface modeling is particularly beneficial in industries where aesthetics and aerodynamics are critical considerations.
Leveraging Simulation and Analysis Tools
In addition to modeling capabilities, 3D-CAD software often includes powerful simulation and analysis tools.
These tools allow designers to test and validate their models before physical prototypes are manufactured, saving time and resources.
Finite Element Analysis (FEA)
Finite Element Analysis is a simulation method that evaluates how a design will react to external forces, such as stress, heat, and vibrations.
By breaking down a model into smaller, manageable elements, FEA provides detailed insights into the structural integrity and performance of a design.
Implementing FEA in the design process helps in identifying potential weaknesses or failure points, enabling designers to enhance the precision and reliability of the final product.
Computational Fluid Dynamics (CFD)
Computational Fluid Dynamics is a tool used to analyze fluid flow and its interaction with a model.
In the electronics manufacturing industry, CFD can be crucial for optimizing heat dissipation, airflow, and cooling systems.
By simulating fluid behavior, designers can predict and correct any issues that may affect the performance and efficiency of electronic components.
Incorporating CFD into the design process ensures that parts function as intended, further contributing to precision and innovation.
The Importance of Collaboration and Revision
While precision part modeling using 3D-CAD involves sophisticated techniques and tools, collaboration and revision remain vital components of the design process.
Encouraging open communication between team members fosters idea sharing and facilitates collective problem-solving.
Feedback and Iteration
Constructive feedback and iterative improvements are essential for achieving precision.
By regularly reviewing models and incorporating feedback from team members and other departments, designers can identify areas for enhancement and implement necessary changes.
This collaborative approach ensures that the final product meets all specifications and quality standards.
Version Control and Documentation
Maintaining version control and thorough documentation of design changes is crucial for tracking progress and ensuring consistency.
Organized records of revisions allow teams to reference previous iterations, understand design decisions, and prevent redundant work.
Efficient version control streamlines the design process and supports the maintenance of precision throughout the project lifecycle.
In conclusion, mastering precision part modeling using 3D-CAD is essential for leaders in the electronic parts manufacturing industry.
By understanding fundamental components, implementing key modeling techniques, leveraging simulation tools, and fostering collaboration, design department leaders can enhance the precision, efficiency, and quality of their designs.
Staying current with the latest advancements in 3D-CAD technology is crucial for maintaining a competitive edge in this dynamic and innovative field.
資料ダウンロード
QCD調達購買管理クラウド「newji」は、調達購買部門で必要なQCD管理全てを備えた、現場特化型兼クラウド型の今世紀最高の購買管理システムとなります。
ユーザー登録
調達購買業務の効率化だけでなく、システムを導入することで、コスト削減や製品・資材のステータス可視化のほか、属人化していた購買情報の共有化による内部不正防止や統制にも役立ちます。
NEWJI DX
製造業に特化したデジタルトランスフォーメーション(DX)の実現を目指す請負開発型のコンサルティングサービスです。AI、iPaaS、および先端の技術を駆使して、製造プロセスの効率化、業務効率化、チームワーク強化、コスト削減、品質向上を実現します。このサービスは、製造業の課題を深く理解し、それに対する最適なデジタルソリューションを提供することで、企業が持続的な成長とイノベーションを達成できるようサポートします。
オンライン講座
製造業、主に購買・調達部門にお勤めの方々に向けた情報を配信しております。
新任の方やベテランの方、管理職を対象とした幅広いコンテンツをご用意しております。
お問い合わせ
コストダウンが利益に直結する術だと理解していても、なかなか前に進めることができない状況。そんな時は、newjiのコストダウン自動化機能で大きく利益貢献しよう!
(Β版非公開)