- お役立ち記事
- Precision Parts with Dry Etching OEM
Precision Parts with Dry Etching OEM
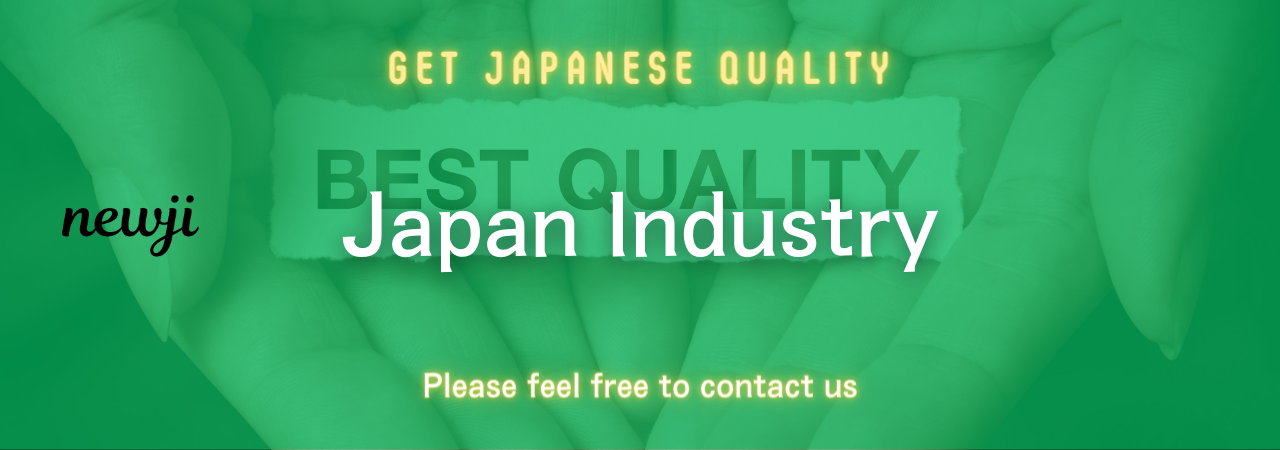
目次
Understanding Dry Etching in Precision Parts Manufacturing
Precision parts are crucial components in a wide range of industries, from aerospace to electronics.
Manufacturers often seek methods to produce these parts with high accuracy and repeatability.
One such method that has gained prominence is dry etching.
In this article, we’ll explore the role of dry etching in precision parts manufacturing and why OEMs (Original Equipment Manufacturers) prefer using this technique.
What is Dry Etching?
Dry etching is a highly controlled process used to remove specific layers from the surface of a material.
Unlike wet etching, which uses liquid chemicals to dissolve materials, dry etching involves gaseous chemicals or plasmas to achieve precise material removal.
This process offers greater control over etching parameters, making it ideal for intricate designs and delicate components.
Why Use Dry Etching for Precision Parts?
Dry etching is favored in precision manufacturing due to its ability to produce highly detailed and accurate features.
Here are some reasons why OEMs prefer dry etching for precision parts:
– **Precision and Accuracy:** Dry etching yields precise control over the removal of material, allowing manufacturers to achieve tight tolerances.
This is essential in industries like semiconductor manufacturing where the margin for error is minimal.
– **Cleanliness:** It offers a cleaner process compared to wet etching, minimizing the risk of contamination.
This is crucial for applications where even the slightest contamination can impact performance, such as in medical devices or microelectronics.
– **Versatility:** The flexibility of dry etching allows it to be used on various materials, including metals, semiconductors, and ceramics.
This versatility is essential as OEMs often work with diverse materials in precision parts production.
– **Efficiency:** Dry etching processes can be more efficient than traditional methods, often reducing time and resource consumption.
This efficiency directly translates to cost savings and higher throughput in manufacturing operations.
The Dry Etching Process Explained
To better understand how dry etching contributes to precision parts manufacturing, let’s break down the dry etching process:
– **Substrate Preparation:** The process begins with preparing the substrate, which involves cleaning and coating the material with a photoresist layer.
The photoresist layer serves as a mask to protect specific areas during etching.
– **Patterning:** A pattern is transferred onto the photoresist using photolithography, a technique that uses light to create a specific design.
This pattern dictates which areas will be etched and which will remain protected.
– **Etching:** Once the pattern is established, the substrate is exposed to a gaseous chemical or plasma.
The etching gas reacts with the unprotected areas, removing the material layer by layer.
Operators can finely control parameters like gas flow, pressure, and temperature to achieve the desired level of material removal.
– **Post-Etching:** After the etching process is complete, the remaining photoresist is removed.
The precision part now has the required features and dimensions as defined by the original pattern.
Applications of Dry Etching in Precision Parts Manufacturing
Dry etching finds applications across multiple industries where precision and detail are paramount:
– **Semiconductor Industry:** Dry etching is essential for creating micro-scale features on silicon wafers used in semiconductors.
It enables the fine patterning required in integrated circuits and other electronic components.
– **Aerospace Components:** In aerospace, precision parts are critical for safety and performance.
Dry etching ensures parts meet the stringent demands of this industry with high accuracy and consistency.
– **Medical Devices:** For medical devices that require intricate details, such as implantable devices and microfluidic chips, dry etching provides the precision needed for functionality and reliability.
– **Optical Instruments:** The optics industry benefits from dry etching for creating high-precision components like lenses and mirrors, which require meticulous craftsmanship.
Challenges in Dry Etching
Despite its advantages, dry etching comes with certain challenges that manufacturers need to address:
– **Equipment Costs:** The cost of equipment required for dry etching can be high.
Companies must balance the initial investment with the long-term benefits of improved quality and efficiency.
– **Complexity of Process:** The process requires skilled operators who can manage the intricate parameters involved.
Training and maintaining a high level of expertise can be resource-intensive.
– **Material Limitations:** Not all materials respond equally to dry etching.
Manufacturers need to understand the specific interactions between etching gases and materials to avoid unwanted side effects.
The Future of Precision Parts Manufacturing with Dry Etching
The demand for precision parts continues to grow as technology advances.
As a result, dry etching is poised to play an even more significant role in future manufacturing processes.
Innovations in etching equipment and the development of new etching gases promise to make the process more efficient and versatile.
Moreover, as OEMs seek to reduce their environmental impact, dry etching’s inherently cleaner process becomes an attractive option.
With continued research and development, dry etching will likely overcome its current limitations, expanding its reach across even more industries.
In conclusion, dry etching remains a cornerstone in the realm of precision parts manufacturing.
Its ability to deliver high-precision components with minimal contamination and resource usage makes it a preferred choice for OEMs across the globe.
As we look to the future, this technique will undoubtedly continue to evolve, driving innovation and quality in precision manufacturing.
資料ダウンロード
QCD調達購買管理クラウド「newji」は、調達購買部門で必要なQCD管理全てを備えた、現場特化型兼クラウド型の今世紀最高の購買管理システムとなります。
ユーザー登録
調達購買業務の効率化だけでなく、システムを導入することで、コスト削減や製品・資材のステータス可視化のほか、属人化していた購買情報の共有化による内部不正防止や統制にも役立ちます。
NEWJI DX
製造業に特化したデジタルトランスフォーメーション(DX)の実現を目指す請負開発型のコンサルティングサービスです。AI、iPaaS、および先端の技術を駆使して、製造プロセスの効率化、業務効率化、チームワーク強化、コスト削減、品質向上を実現します。このサービスは、製造業の課題を深く理解し、それに対する最適なデジタルソリューションを提供することで、企業が持続的な成長とイノベーションを達成できるようサポートします。
オンライン講座
製造業、主に購買・調達部門にお勤めの方々に向けた情報を配信しております。
新任の方やベテランの方、管理職を対象とした幅広いコンテンツをご用意しております。
お問い合わせ
コストダウンが利益に直結する術だと理解していても、なかなか前に進めることができない状況。そんな時は、newjiのコストダウン自動化機能で大きく利益貢献しよう!
(Β版非公開)