- お役立ち記事
- Precision Parts with Wet Etching OEM Manufacturing
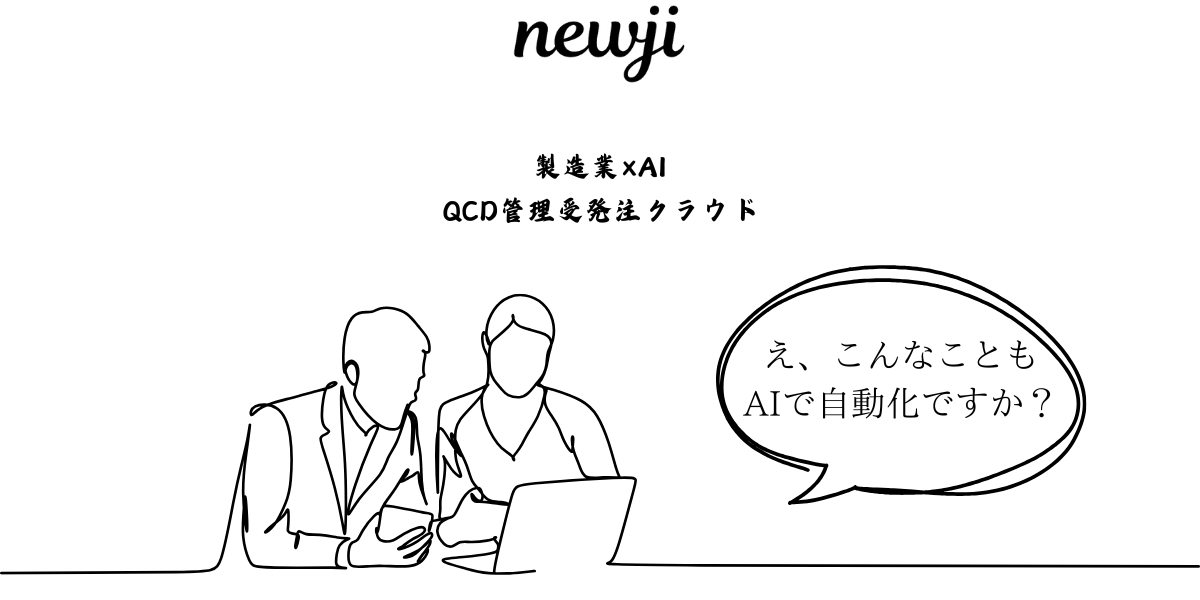
Precision Parts with Wet Etching OEM Manufacturing
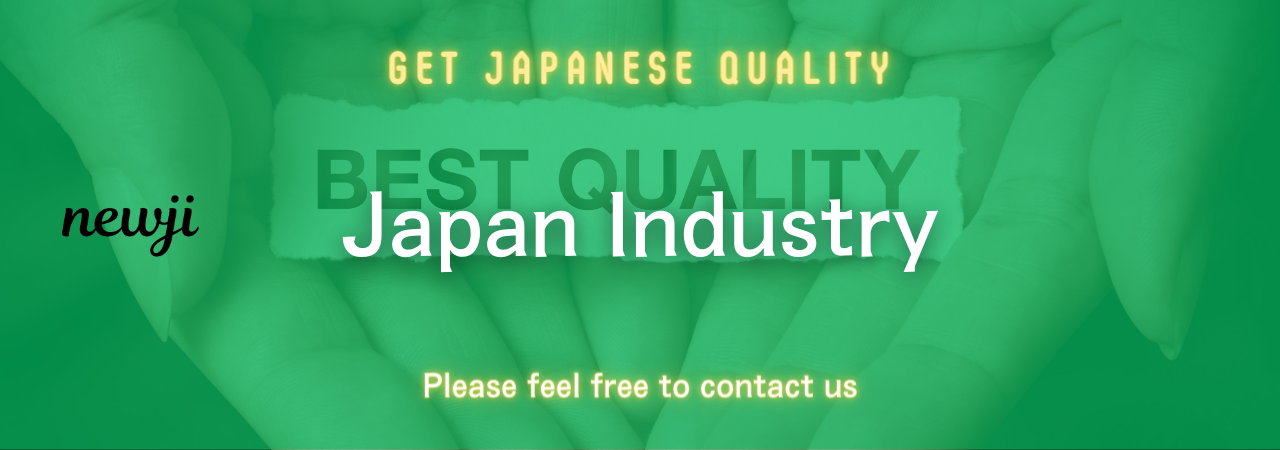
Wet etching is a fascinating process that involves removing material from a substrate to create intricate designs and patterns.
This method is widely used in many industries, particularly in the manufacturing of precision parts.
OEM (Original Equipment Manufacturer) companies often rely on wet etching to produce high-quality components that meet specific requirements.
Let’s dive deeper into the world of wet etching and OEM manufacturing to understand how they work together to create precision parts.
目次
Understanding Wet Etching
Wet etching is a chemical process used to remove layers of material from a substrate.
The substrate can be made of various materials, such as metals, semiconductors, or glass.
In this process, the substrate is immersed in a chemical solution that reacts with the exposed material, dissolving it away.
The areas that need to be protected from the etching process are covered with a resistant material called a “mask.”
One of the key benefits of wet etching is its ability to create highly detailed and precise patterns.
This is especially important in industries where minute deviations can lead to significant problems.
The chemical reactions involved in wet etching are predictable and controllable, allowing manufacturers to achieve the desired level of precision.
The Importance of Precision in Manufacturing
In many industries, precision manufacturing is crucial for the functionality and reliability of the final product.
Take the electronics industry, for example.
Microchips and integrated circuits require incredibly precise patterns to function correctly.
Any deviation from the intended design can lead to malfunction or lower performance.
Similarly, the medical industry relies on precision parts for various devices and instruments.
Surgical tools, diagnostic equipment, and implants all need to be manufactured with a high degree of accuracy.
Wet etching ensures that these components meet the stringent standards required for medical applications.
OEM Manufacturing and Wet Etching
OEM manufacturing involves producing components or products that are then sold by another company under their own brand name.
This practice is common in many industries, including automotive, aerospace, electronics, and medical devices.
OEM companies often turn to wet etching to create precision parts that meet their exact specifications.
Advantages of Using OEM Manufacturers
One of the main advantages of working with an OEM manufacturer is the ability to leverage their expertise and specialized equipment.
These manufacturers have the experience and know-how to produce high-quality components efficiently.
By partnering with an OEM, companies can focus on their core business activities while leaving the manufacturing process to the experts.
Additionally, OEM manufacturers can produce parts at scale, which helps reduce costs.
They have established relationships with suppliers and access to bulk materials, making the production process more cost-effective.
This means that companies can obtain precision parts without needing to invest in expensive equipment or facilities.
Quality Assurance and Compliance
Quality assurance is a critical aspect of manufacturing precision parts.
OEM manufacturers have stringent quality control processes in place to ensure that every component meets the required standards.
This includes rigorous testing and inspection procedures to detect any defects or deviations from the specifications.
In industries like medical devices and aerospace, compliance with industry regulations is essential.
OEM manufacturers are well-versed in these regulations and ensure that their products adhere to the necessary guidelines.
This provides peace of mind to companies, knowing that the components they receive are reliable and compliant with industry standards.
Applications of Precision Parts with Wet Etching
Electronics Industry
In the electronics industry, wet etching is used to create microchips, printed circuit boards (PCBs), and various other components.
The ability to produce intricate patterns with high precision is essential for the functionality of electronic devices.
Wet etching allows for the creation of fine features and tight tolerances required for advanced electronic applications.
Medical Devices
For medical devices, precision is paramount.
Wet etching is used to manufacture components such as surgical instruments, needles, and microfluidic devices.
These parts need to be made with exceptional accuracy to ensure they function correctly in medical procedures.
The use of wet etching allows for the creation of smooth surfaces and fine details necessary for these applications.
Aerospace Industry
In the aerospace industry, wet etching is employed to create components that must withstand extreme conditions.
Turbine blades, engine parts, and structural components all require high precision and reliability.
Wet etching helps achieve the necessary specifications, ensuring the safety and performance of aerospace systems.
Automotive Industry
The automotive industry also benefits from precision parts manufactured using wet etching.
Components such as sensors, fuel injectors, and engine control units require accurate designs to function properly.
Wet etching enables the production of these parts with the necessary precision, contributing to the overall performance and efficiency of vehicles.
Challenges in Wet Etching
While wet etching offers many benefits, it also comes with its own set of challenges.
One of the main challenges is the control of the etching process.
The chemical reactions involved can be influenced by various factors such as temperature, concentration, and agitation.
Maintaining consistent conditions is crucial to achieving uniform etching and avoiding defects.
Another challenge is the handling of hazardous chemicals used in the etching process.
Proper safety measures must be in place to protect workers and the environment.
This includes appropriate storage, handling, and disposal of chemicals to prevent accidents and contamination.
Advancements in Technology
Advancements in technology are continuously improving the wet etching process.
Innovations such as automated etching systems and advanced masking techniques are enhancing the precision and efficiency of the process.
These advancements are helping to overcome some of the challenges associated with wet etching and are driving the industry forward.
Conclusion
Wet etching is a crucial technology in the world of precision manufacturing.
The ability to create detailed and accurate patterns makes it indispensable in industries such as electronics, medical devices, aerospace, and automotive.
By partnering with OEM manufacturers, companies can leverage their expertise and equipment to produce high-quality precision parts.
While challenges exist, ongoing advancements in technology are making wet etching more efficient and reliable.
As industries continue to demand higher precision, wet etching will remain a vital process in the production of complex and intricate components.
資料ダウンロード
QCD調達購買管理クラウド「newji」は、調達購買部門で必要なQCD管理全てを備えた、現場特化型兼クラウド型の今世紀最高の購買管理システムとなります。
ユーザー登録
調達購買業務の効率化だけでなく、システムを導入することで、コスト削減や製品・資材のステータス可視化のほか、属人化していた購買情報の共有化による内部不正防止や統制にも役立ちます。
NEWJI DX
製造業に特化したデジタルトランスフォーメーション(DX)の実現を目指す請負開発型のコンサルティングサービスです。AI、iPaaS、および先端の技術を駆使して、製造プロセスの効率化、業務効率化、チームワーク強化、コスト削減、品質向上を実現します。このサービスは、製造業の課題を深く理解し、それに対する最適なデジタルソリューションを提供することで、企業が持続的な成長とイノベーションを達成できるようサポートします。
オンライン講座
製造業、主に購買・調達部門にお勤めの方々に向けた情報を配信しております。
新任の方やベテランの方、管理職を対象とした幅広いコンテンツをご用意しております。
お問い合わせ
コストダウンが利益に直結する術だと理解していても、なかなか前に進めることができない状況。そんな時は、newjiのコストダウン自動化機能で大きく利益貢献しよう!
(Β版非公開)