- お役立ち記事
- Prediction and evaluation method of rolling fatigue life and technology to extend the life of rolling bearings
月間77,185名の
製造業ご担当者様が閲覧しています*
*2025年2月28日現在のGoogle Analyticsのデータより
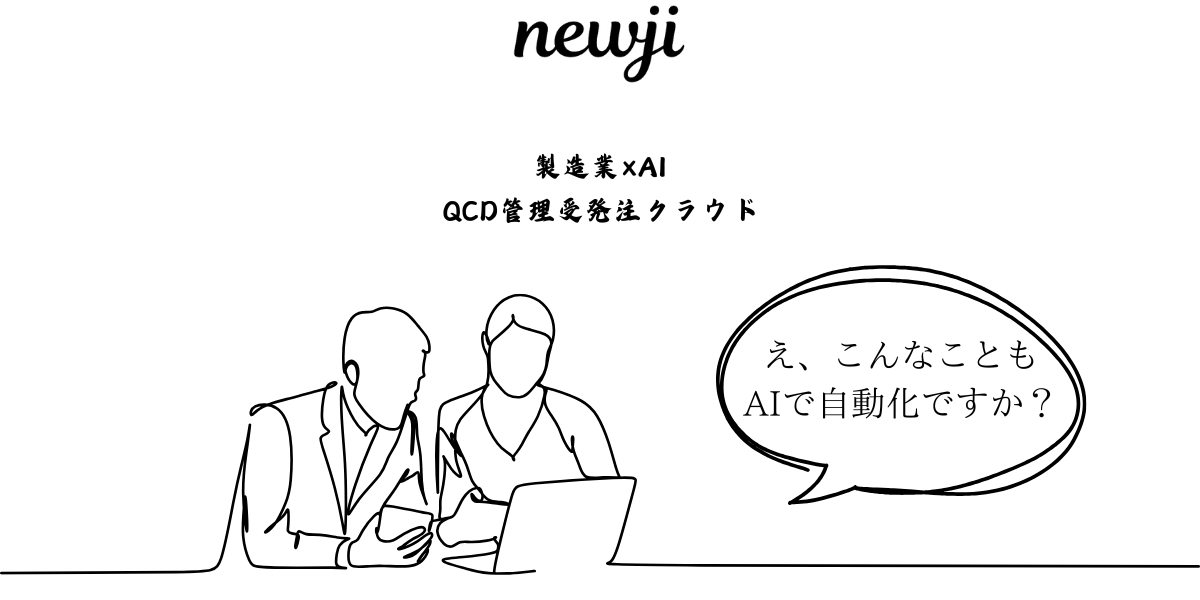
Prediction and evaluation method of rolling fatigue life and technology to extend the life of rolling bearings
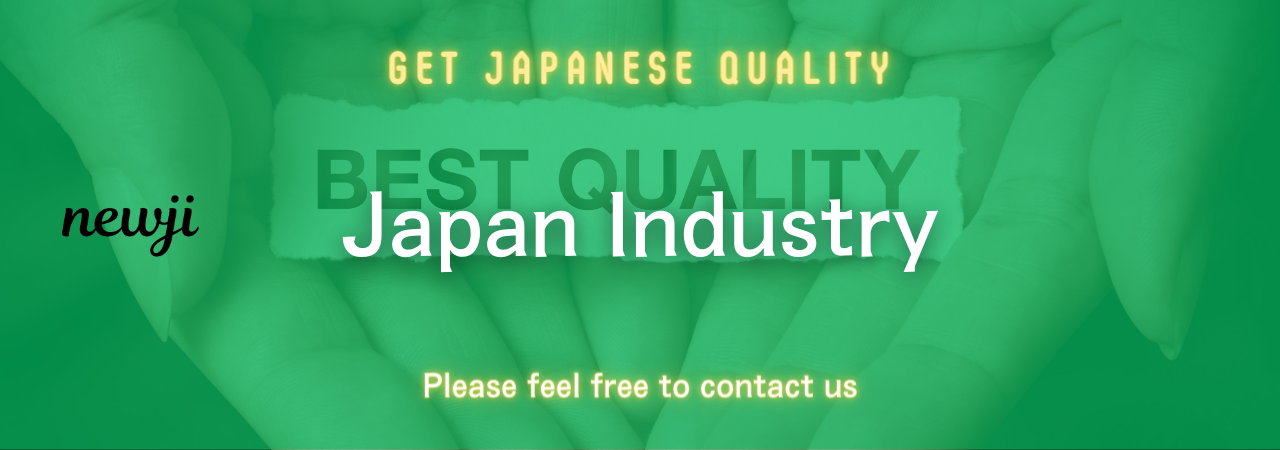
目次
Understanding Rolling Fatigue in Bearings
Rolling bearings are critical components in various mechanical systems, playing a pivotal role in reducing friction and supporting radial and axial loads.
Despite their robust design, these bearings are subject to rolling fatigue, a common failure mode that occurs due to repeated stress over time.
The Basics of Rolling Fatigue
Rolling fatigue is a type of fatigue failure that originates from the repeated stress cycles experienced by the bearing’s rolling elements and the raceway.
This repetitive loading leads to micro-cracks within the material structure, eventually resulting in surface spalling or complete failure.
The life of a rolling bearing is significantly influenced by factors such as load, speed, lubrication quality, and operating conditions.
Predicting Rolling Fatigue Life
Accurately predicting the rolling fatigue life of bearings is essential for planning maintenance, avoiding unexpected failures, and improving system reliability.
Factors Influencing Bearing Life
Several factors come into play when estimating bearing life, including:
– **Load and Speed**: Bearings subjected to higher loads and speeds tend to experience accelerated wear and reduced operational life.
– **Material Quality**: The type and quality of material used in manufacturing the bearings can greatly influence their durability.
– **Lubrication**: Adequate lubrication minimizes friction and wear, thus prolonging the life of bearings.
– **Environmental Conditions**: Extreme temperatures, contamination, and moisture can affect the bearing’s longevity.
L10 Life and Its Calculations
The L10 life, a common measure in the industry, represents the estimated lifespan during which 90% of a group of identical bearings will still be operational without showing any signs of fatigue failure.
This measure is calculated using the Basic Rating Life Formula:
\[ L_{10} = \left(\frac{C}{P}\right)^3 \times 10^6 \]
Where:
– \( L_{10} \) is the basic rating life in million revolutions
– \( C \) is the dynamic load rating
– \( P \) is the equivalent dynamic bearing load
Refinements to this formula include adjustments for varying lubrication conditions, stress concentrations, and operating temperature, often leading to the development of more advanced models.
Technologies for Extending Bearing Life
Various technologies and techniques have been devised to extend the fatigue life of rolling bearings and enhance their performance.
Advanced Materials
The use of advanced materials such as high-grade steel, ceramics, and composite materials can significantly enhance the lifespan of bearings.
These materials offer improved wear resistance, greater hardness, and better resistance to adverse environmental conditions.
Improved Surface Treatments
Surface treatments like coatings, heat treatments, and shot peening can enhance the bearing’s surface properties, reducing stress concentrations and delaying the onset of fatigue cracks.
Coatings such as diamond-like carbon (DLC) and chromium nitride (CrN) are excellent for improving wear resistance.
Optimized Lubrication Systems
Proper lubrication is critical in maximizing bearing life.
Developments in lubrication technology, including the use of synthetic oils, solid-film lubricants, and advanced grease formulations, help reduce friction and metal-to-metal contact, thus extending bearing service life.
Condition Monitoring Solutions
Incorporating condition monitoring systems allows for the early detection of potential failures.
Vibration analysis, temperature monitoring, and acoustic emission analysis are some methods used to assess the condition of bearings and predict failures before they occur.
Conclusion
Understanding and effectively managing the rolling fatigue life of bearings is crucial for the reliability and efficiency of mechanical systems.
Through advanced prediction methods and technologies aimed at extending bearing life, it is possible to reduce maintenance costs, prevent unexpected downtimes, and improve overall system performance.
By focusing on the various factors that influence bearing life and implementing the latest technological advancements, industries can ensure that their systems remain operational at peak efficiency for extended periods.
資料ダウンロード
QCD管理受発注クラウド「newji」は、受発注部門で必要なQCD管理全てを備えた、現場特化型兼クラウド型の今世紀最高の受発注管理システムとなります。
ユーザー登録
受発注業務の効率化だけでなく、システムを導入することで、コスト削減や製品・資材のステータス可視化のほか、属人化していた受発注情報の共有化による内部不正防止や統制にも役立ちます。
NEWJI DX
製造業に特化したデジタルトランスフォーメーション(DX)の実現を目指す請負開発型のコンサルティングサービスです。AI、iPaaS、および先端の技術を駆使して、製造プロセスの効率化、業務効率化、チームワーク強化、コスト削減、品質向上を実現します。このサービスは、製造業の課題を深く理解し、それに対する最適なデジタルソリューションを提供することで、企業が持続的な成長とイノベーションを達成できるようサポートします。
製造業ニュース解説
製造業、主に購買・調達部門にお勤めの方々に向けた情報を配信しております。
新任の方やベテランの方、管理職を対象とした幅広いコンテンツをご用意しております。
お問い合わせ
コストダウンが利益に直結する術だと理解していても、なかなか前に進めることができない状況。そんな時は、newjiのコストダウン自動化機能で大きく利益貢献しよう!
(β版非公開)