- お役立ち記事
- Predictive maintenance technology using IoT and its application to system construction
月間77,185名の
製造業ご担当者様が閲覧しています*
*2025年2月28日現在のGoogle Analyticsのデータより
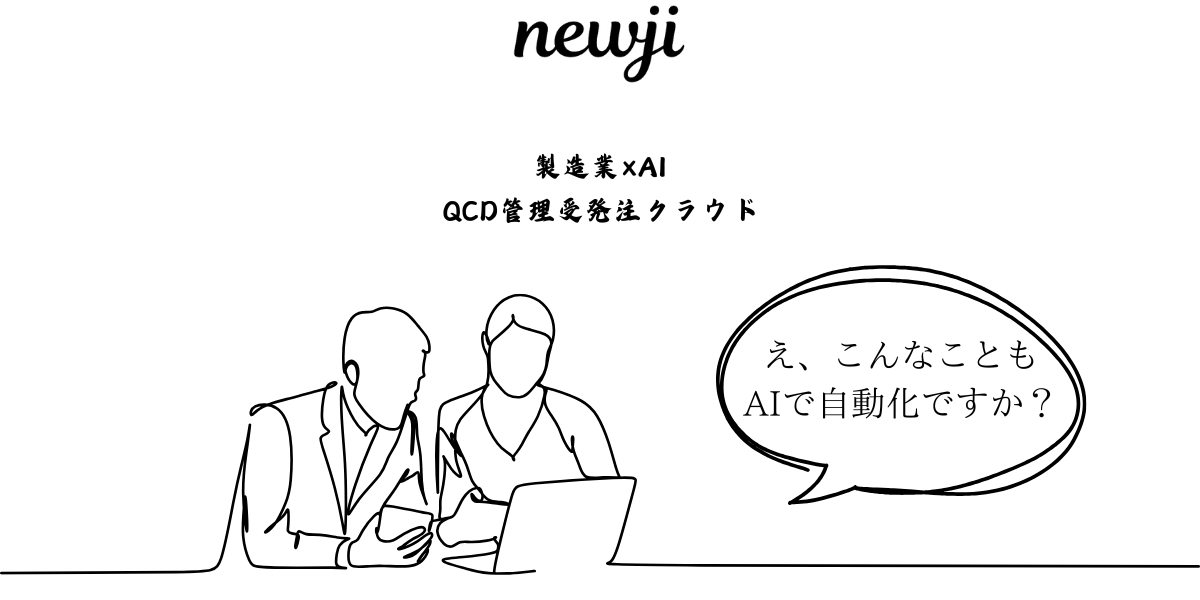
Predictive maintenance technology using IoT and its application to system construction
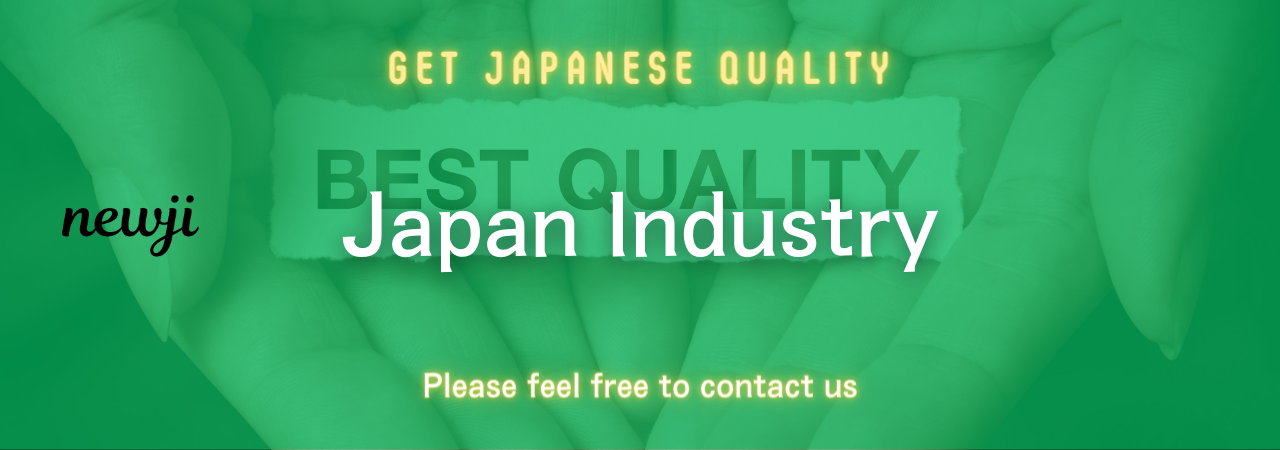
目次
Introduction to Predictive Maintenance and IoT
Predictive maintenance is a modern approach that utilizes advanced technologies to foresee potential system failures before they occur.
By leveraging the Internet of Things (IoT), companies can gather real-time data to predict when maintenance should be performed.
This prevents unexpected downtimes and saves on repair costs.
IoT plays a critical role in predictive maintenance by providing the necessary data from connected devices.
This data forms the basis for predictive algorithms to accurately diagnose potential issues.
With sensors continuously monitoring equipment, the IoT ensures that critical information about performance and wear is collected and analyzed.
The Role of IoT in Predictive Maintenance
IoT devices are instrumental in enhancing predictive maintenance functionalities.
They collect vast amounts of data from equipment in various conditions.
These devices help in monitoring temperature, vibrations, pressure, humidity, and other parameters critical for equipment functionality.
The integration of IoT devices with maintenance systems allows for real-time data analysis.
Such integration ensures that maintenance decisions are data-driven and more accurate.
By analyzing this data over time, patterns and anomalies can be identified, pointing towards the potential for failure.
Benefits of Predictive Maintenance with IoT
Enhanced Equipment Reliability
Predictive maintenance increases equipment reliability by ensuring issues are dealt with before they lead to significant failures.
By continuously monitoring equipment health, organizations can maintain optimal performance levels.
Reduced Maintenance Costs
One of the most significant advantages of predictive maintenance is cost savings.
By anticipating failures and addressing them before they escalate, companies can reduce the frequency and cost of repairs.
Avoiding unplanned downtimes not only saves money but also boosts productivity.
Improved Safety
Ensuring the proper functioning of equipment contributes to a safer working environment.
Predictive maintenance identifies potential mechanical failures that could lead to accidents.
Therefore, maintaining equipment in its best condition reduces risks and enhances safety for operators.
Challenges in Implementing Predictive Maintenance
Despite its benefits, implementing predictive maintenance using IoT comes with its set of challenges.
Data Management
The sheer volume of data generated by IoT devices can be overwhelming.
Managing this data effectively involves data storage, processing, and analysis, which require robust systems.
Organizations must invest in data management solutions to make sense of and benefit from the data collected.
Integration of Systems
Integrating IoT devices with existing maintenance management systems can be complex.
Ensuring compatibility and seamless data flow between systems is essential for effective predictive maintenance.
Existing infrastructure might need upgrades or adjustments to accommodate the new technology.
Security Concerns
With increased connectivity, there is a higher risk of cybersecurity threats.
Ensuring that data from IoT devices is protected from unauthorized access requires robust security protocols.
Organizations must prioritize cybersecurity to safeguard sensitive equipment information.
Applications of Predictive Maintenance in Various Industries
Predictive maintenance is revolutionizing maintenance strategies across different industries.
Manufacturing
In manufacturing, predictive maintenance helps optimize production line efficiency.
By detecting potential machine failures, manufacturers can schedule timely interventions, avoiding costly production halts.
This approach maximizes uptime and enhances overall operational efficiency.
Energy Sector
Predictive maintenance is crucial in the energy sector, where equipment like turbines and generators must operate flawlessly.
Remote condition monitoring powered by IoT can forewarn maintenance teams about potential equipment failures, ensuring uninterrupted energy supply and reducing operational risks.
Transportation
In the transportation industry, predictive maintenance helps keep vehicles and infrastructure in top condition.
Real-time data on vehicle performance aids in timely maintenance, reducing breakdowns and increasing the lifespan of the fleet.
Airlines, railways, and logistics companies benefit significantly from IoT-enhanced predictive maintenance routines.
Conclusion
Predictive maintenance, powered by IoT, represents a futuristic approach to maintaining industrial and commercial systems.
While the challenges in implementing such systems are real, the benefits in terms of cost savings, reliability, and safety far outweigh these hurdles.
As IoT technology continues to advance, predictive maintenance strategies will become ever more sophisticated and accessible.
For organizations, adopting predictive maintenance is not merely an option but a necessity for staying competitive in today’s tech-driven environment.
資料ダウンロード
QCD管理受発注クラウド「newji」は、受発注部門で必要なQCD管理全てを備えた、現場特化型兼クラウド型の今世紀最高の受発注管理システムとなります。
ユーザー登録
受発注業務の効率化だけでなく、システムを導入することで、コスト削減や製品・資材のステータス可視化のほか、属人化していた受発注情報の共有化による内部不正防止や統制にも役立ちます。
NEWJI DX
製造業に特化したデジタルトランスフォーメーション(DX)の実現を目指す請負開発型のコンサルティングサービスです。AI、iPaaS、および先端の技術を駆使して、製造プロセスの効率化、業務効率化、チームワーク強化、コスト削減、品質向上を実現します。このサービスは、製造業の課題を深く理解し、それに対する最適なデジタルソリューションを提供することで、企業が持続的な成長とイノベーションを達成できるようサポートします。
製造業ニュース解説
製造業、主に購買・調達部門にお勤めの方々に向けた情報を配信しております。
新任の方やベテランの方、管理職を対象とした幅広いコンテンツをご用意しております。
お問い合わせ
コストダウンが利益に直結する術だと理解していても、なかなか前に進めることができない状況。そんな時は、newjiのコストダウン自動化機能で大きく利益貢献しよう!
(β版非公開)