- お役立ち記事
- Predictive maintenance using infrared thermography that managers of equipment management departments in the steel industry should know about
月間76,176名の
製造業ご担当者様が閲覧しています*
*2025年3月31日現在のGoogle Analyticsのデータより
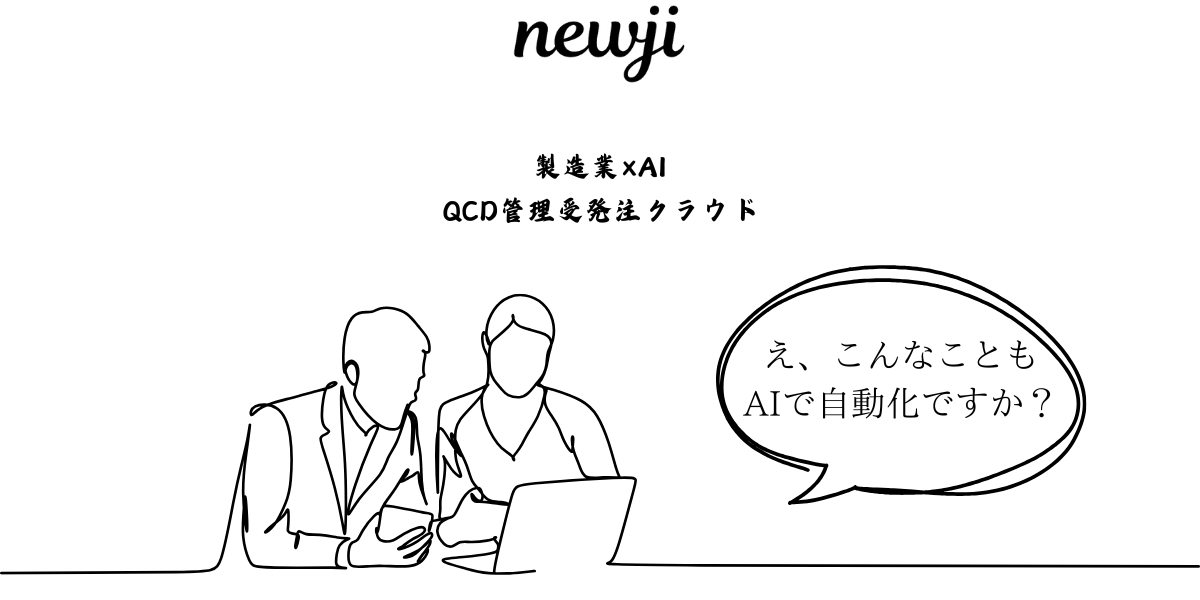
Predictive maintenance using infrared thermography that managers of equipment management departments in the steel industry should know about
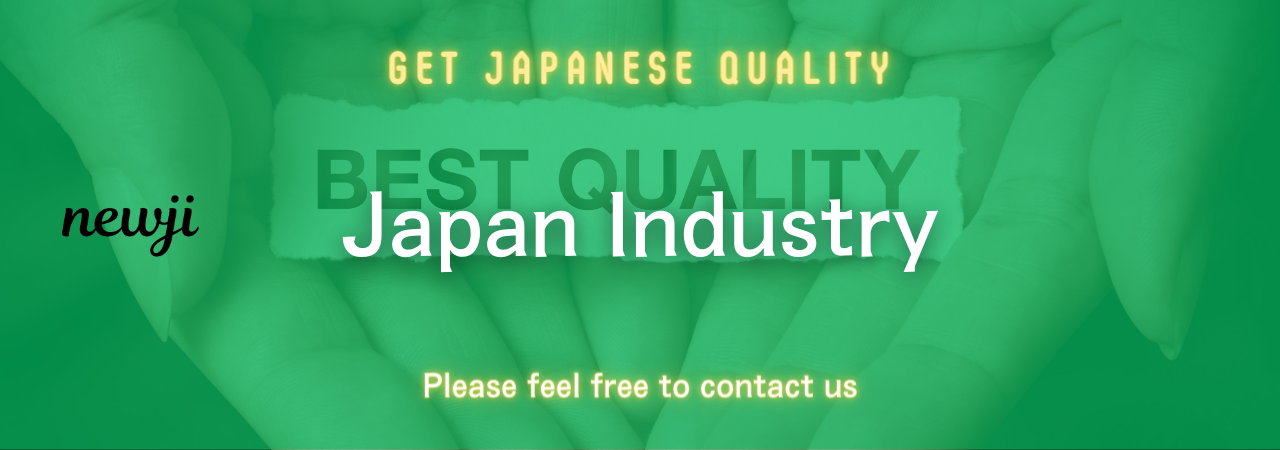
目次
Understanding Predictive Maintenance
Predictive maintenance is a proactive approach that allows equipment managers to anticipate and rectify potential problems before they lead to equipment failures.
It involves using data analysis tools and techniques to predict when machinery might fail, allowing maintenance to be performed just in time.
This method not only improves the lifespan of the equipment but also optimizes efficiency and reduces costs.
In the steel industry, where equipment is often run at full capacity and under severe conditions, maintaining optimal performance is crucial.
Integrating advanced technologies like infrared thermography can significantly enhance predictive maintenance strategies, providing an edge in equipment management.
The Role of Infrared Thermography in Predictive Maintenance
Infrared thermography is a non-contact and non-invasive technology that detects heat emitted from equipment surfaces.
Heat can be a key indicator of equipment health, as excessive temperatures often signal potential issues such as friction, misalignment, or electrical overloads.
This technique allows managers to monitor the thermal profile of equipment, identifying abnormal patterns that might suggest impending malfunction.
By employing infrared thermography, equipment managers in the steel industry can ensure that maintenance is performed precisely when needed, avoiding both under-maintenance and over-maintenance.
This targeted approach leads to better allocation of resources and minimizes unexpected downtimes.
Advantages of Using Infrared Thermography
Infrared thermography offers several advantages in predictive maintenance:
1. **Early Problem Detection**: It helps in identifying issues at an early stage before they escalate into significant problems, allowing timely interventions.
2. **Non-Invasive Monitoring**: Equipment can be inspected and monitored without interrupting operations, maintaining continuous production flow.
3. **Comprehensive Diagnostics**: Thermal imaging provides detailed insights into various equipment components, from motors and electrical systems to conveyor belts and furnaces.
4. **Safety Enhancements**: Identifying overheating components that might lead to fires or equipment damage protects both the infrastructure and workers.
5. **Cost Efficiency**: By preventing unexpected breakdowns and extending the lifespan of machinery, it reduces maintenance costs significantly.
Implementing Infrared Thermography in Steel Industry Maintenance
To effectively integrate infrared thermography into predictive maintenance, an organized approach is essential.
Preparation involves choosing the right equipment and training maintenance staff in infrared imaging techniques.
Many companies in the steel industry have opted for handheld thermal cameras for flexibility, while others have employed stationary systems for continuous monitoring.
Steps to Integrate Infrared Thermography
1. **Assessment and Planning**: Examine the existing maintenance program and identify areas where infrared thermography can provide the most insight.
Focus on critical machinery that has a high risk of failure.
2. **Equipment Selection**: Choose thermal cameras with the proper specifications for your needs, such as resolution and temperature range.
Advanced cameras with wireless connectivity and cloud integration can further streamline the monitoring process.
3. **Training and Skill Development**: Train maintenance personnel on how to interpret thermal images accurately.
Understanding anomalies and normal variations in temperature patterns is crucial for making informed decisions.
4. **Routine Monitoring**: Establish a schedule for regular thermal imaging scans of essential equipment.
Consistency in monitoring allows for the effective tracking of temperature trends over time.
5. **Data Analysis and Action**: Use analytics software to assess the collected thermal data.
Develop routine reports that highlight potential issues and recommend maintenance actions.
Address anomalies swiftly to prevent the development of more severe issues.
Challenges and Considerations
While infrared thermography is a powerful tool, certain challenges need consideration:
1. **Initial Investment**: The cost of high-quality thermal imaging equipment and training can be substantial.
However, the long-term savings from reduced downtime and maintenance costs frequently justify the initial expenditure.
2. **Data Interpretation**: Misinterpretation of thermal images can lead to inaccurate diagnoses.
Continual training and consultation with experienced professionals can help mitigate this issue.
3. **Environmental Factors**: External factors such as ambient temperature, sunlight, and wind can affect thermal readings.
Proper technique and timing of measurements are necessary to ensure reliability.
The Future of Predictive Maintenance in the Steel Industry
As technology evolves, predictive maintenance will increasingly incorporate advanced technologies like artificial intelligence and machine learning.
These technologies can enhance the analysis of thermal data, providing deeper insights into equipment behavior.
The Internet of Things (IoT) will play a significant role in connecting thermal imaging devices, allowing for real-time monitoring and automated alerts.
This integrated approach will further empower equipment managers in the steel industry to make data-driven decisions, improve efficiency, and enhance safety standards.
Transforming Maintenance Strategies
The integration of infrared thermography in predictive maintenance strategies is transforming how the steel industry manages equipment.
By embracing these technologies, equipment managers can expect increased reliability, safety, and service life of their machinery.
A commitment to proactive maintenance not only optimizes operations but also positions the industry for a more competitive and sustainable future.
This is a leap forward in ensuring consistent production quality and meeting global steel demand with minimized interruptions.
資料ダウンロード
QCD管理受発注クラウド「newji」は、受発注部門で必要なQCD管理全てを備えた、現場特化型兼クラウド型の今世紀最高の受発注管理システムとなります。
ユーザー登録
受発注業務の効率化だけでなく、システムを導入することで、コスト削減や製品・資材のステータス可視化のほか、属人化していた受発注情報の共有化による内部不正防止や統制にも役立ちます。
NEWJI DX
製造業に特化したデジタルトランスフォーメーション(DX)の実現を目指す請負開発型のコンサルティングサービスです。AI、iPaaS、および先端の技術を駆使して、製造プロセスの効率化、業務効率化、チームワーク強化、コスト削減、品質向上を実現します。このサービスは、製造業の課題を深く理解し、それに対する最適なデジタルソリューションを提供することで、企業が持続的な成長とイノベーションを達成できるようサポートします。
製造業ニュース解説
製造業、主に購買・調達部門にお勤めの方々に向けた情報を配信しております。
新任の方やベテランの方、管理職を対象とした幅広いコンテンツをご用意しております。
お問い合わせ
コストダウンが利益に直結する術だと理解していても、なかなか前に進めることができない状況。そんな時は、newjiのコストダウン自動化機能で大きく利益貢献しよう!
(β版非公開)