- お役立ち記事
- Preparation of Defective Measures Instructions and Effective Response Procedures in Manufacturing
月間76,176名の
製造業ご担当者様が閲覧しています*
*2025年3月31日現在のGoogle Analyticsのデータより
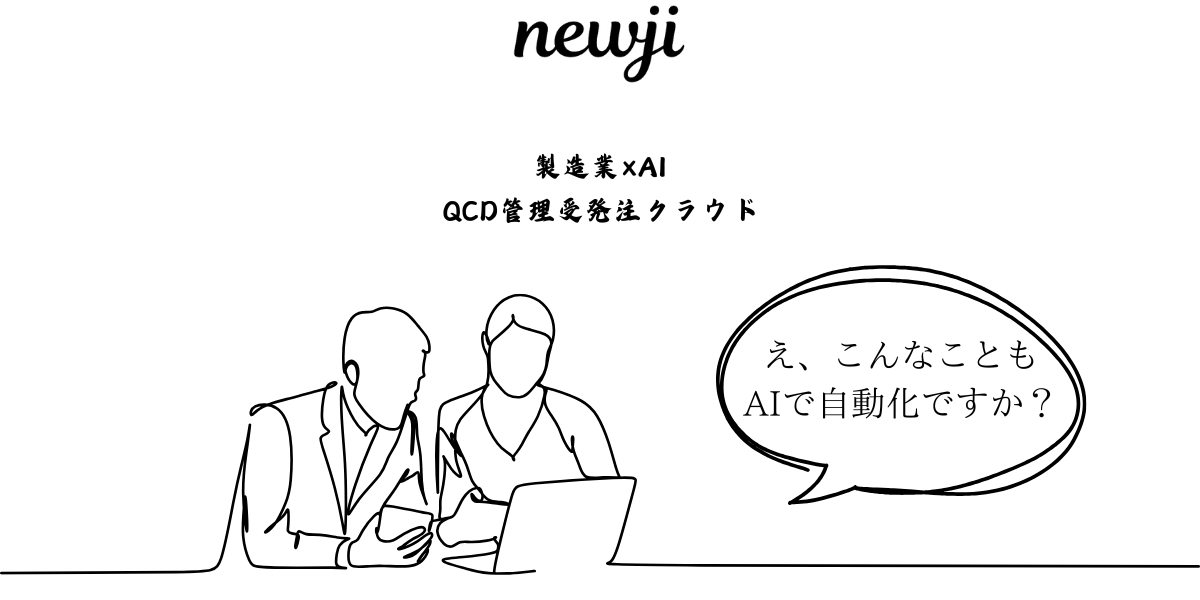
Preparation of Defective Measures Instructions and Effective Response Procedures in Manufacturing
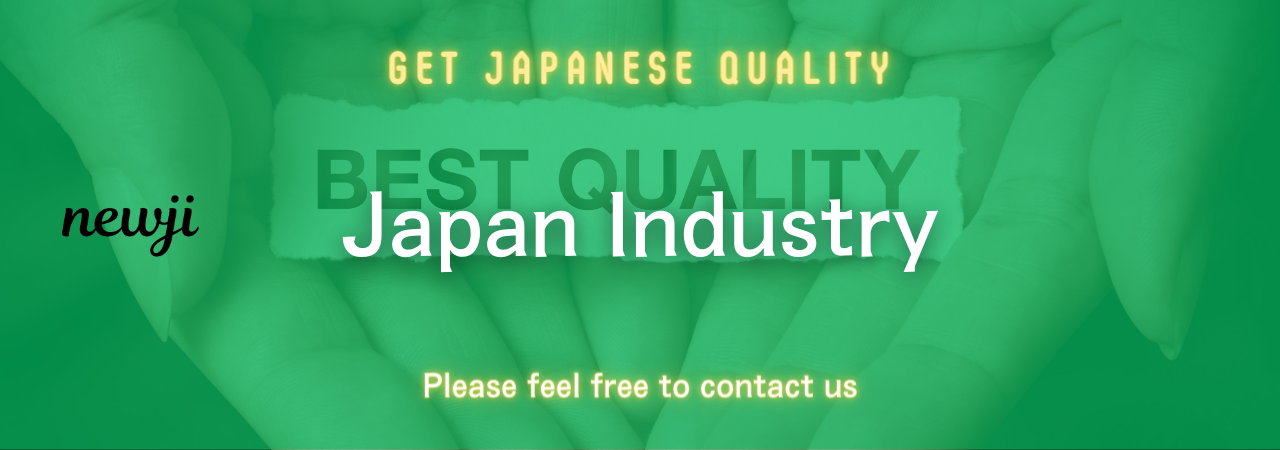
Manufacturing is the backbone of many industries, providing products that range from everyday items to complex machinery. Ensuring that these products meet quality standards is crucial. However, defects can and do occur. It’s essential for manufacturing companies to have well-prepared instructions and effective response procedures in place to handle these issues promptly and efficiently. This not only helps in maintaining product quality but also enhances the overall efficiency of the production process.
Understanding the Importance of Defective Measures
Defective measures refer to the steps and procedures enacted to identify, analyze, and correct defects in the manufacturing process. These measures are crucial for several reasons:
1. Cost Reduction:
– Reducing defects can significantly cut costs associated with rework, scrap, and customer returns.
2. Customer Satisfaction:
– Consistently delivering high-quality products builds customer trust and loyalty.
3. Regulatory Compliance:
– Adhering to industry standards and regulations is essential to avoid fines and maintain operating licenses.
Key Steps in Preparing Defective Measures Instructions
1. Identify Potential Defects:
– Use historical data and engineering analysis to identify common defects in the production process.
2. Set Quality Standards:
– Define acceptable quality levels and set measurable standards for each product.
3. Develop a Quality Control Plan:
– Establish procedures for inspecting and testing products at various stages of production.
4. Training and Awareness:
– Ensure that all employees are aware of the quality standards and are trained in inspection and defect identification.
5. Documentation:
– Maintain detailed records of inspections, defects identified, and corrective actions taken.
Effective Response Procedures
Having response procedures in place is critical for addressing defects swiftly and minimizing their impact. Here’s how to create effective response procedures:
1. Immediate Action Protocols:
– Define clear steps for immediate actions when a defect is identified, such as stopping the production line or isolating defective products.
2. Root Cause Analysis:
– Use tools like the 5 Whys, Fishbone Diagram, or Failure Mode and Effects Analysis (FMEA) to identify the root cause of the defect.
3. Corrective Actions:
– Develop corrective action plans to address the root cause and prevent recurrence. This may involve equipment adjustments, process modifications, or additional employee training.
4. Verification:
– After implementing corrective actions, verify their effectiveness by conducting follow-up inspections and tests.
5. Communication:
– Maintain clear communication channels to report defects, corrective actions, and outcomes to all relevant stakeholders.
Incorporating Technology
In the modern manufacturing environment, technology can play a significant role in defect management:
1. Automation and Robotics:
– Automated systems can improve precision and consistency, reducing the likelihood of defects.
2. Machine Learning and AI:
– Utilize machine learning algorithms to predict potential defects based on historical data and real-time monitoring.
3. Quality Management Software:
– Implement software solutions for tracking defects, managing documentation, and analyzing defect trends over time.
4. Internet of Things (IoT):
– IoT devices can provide real-time data on equipment performance and environmental conditions, helping to identify potential issues before they result in defects.
Continuous Improvement
Defect management is not a one-time task but an ongoing process. Adopt a culture of continuous improvement by:
1. Regular Audits and Reviews:
– Conduct regular quality audits and reviews to identify areas for improvement.
2. Employee Feedback:
– Encourage employees to provide feedback on quality issues and suggestions for improvement.
3. Lean Manufacturing Principles:
– Apply lean manufacturing principles like Six Sigma and Kaizen to reduce waste and improve process efficiency.
Case Study: Successful Implementation of Defective Measures
Consider the case of a manufacturing company that faced high levels of product returns due to defects. By implementing a comprehensive defective measures program, they achieved remarkable results:
Step 1: Identification
– The company analyzed historical data to identify the most common defects and their causes.
Step 2: Setting Standards
– They established new quality standards and retrained their workforce on these standards.
Step 3: Quality Control Plan
– A detailed quality control plan was developed, involving regular inspections at key stages of production.
Step 4: Immediate Action and Root Cause Analysis
– When defects were identified, immediate actions were taken to halt production and isolate defective products. Root cause analysis helped in pinpointing the source of defects.
Step 5: Corrective Actions and Verification
– Corrective actions, such as process adjustments and additional training, were implemented. Follow-up inspections confirmed the effectiveness of these actions.
Results:
– The defect rate decreased by 45%, resulting in significant cost savings and improved customer satisfaction.
Effective preparation of defective measures instructions and response procedures is essential for maintaining high quality in manufacturing. By identifying potential defects, setting quality standards, developing response procedures, incorporating technology, and fostering continuous improvement, manufacturing companies can significantly reduce defects, lower costs, and enhance customer satisfaction. Adopting these practices will not only improve product quality but also contribute to the overall efficiency and reliability of the manufacturing process. Through consistent effort and dedication to quality, companies can achieve a competitive edge in the market.
資料ダウンロード
QCD管理受発注クラウド「newji」は、受発注部門で必要なQCD管理全てを備えた、現場特化型兼クラウド型の今世紀最高の受発注管理システムとなります。
ユーザー登録
受発注業務の効率化だけでなく、システムを導入することで、コスト削減や製品・資材のステータス可視化のほか、属人化していた受発注情報の共有化による内部不正防止や統制にも役立ちます。
NEWJI DX
製造業に特化したデジタルトランスフォーメーション(DX)の実現を目指す請負開発型のコンサルティングサービスです。AI、iPaaS、および先端の技術を駆使して、製造プロセスの効率化、業務効率化、チームワーク強化、コスト削減、品質向上を実現します。このサービスは、製造業の課題を深く理解し、それに対する最適なデジタルソリューションを提供することで、企業が持続的な成長とイノベーションを達成できるようサポートします。
製造業ニュース解説
製造業、主に購買・調達部門にお勤めの方々に向けた情報を配信しております。
新任の方やベテランの方、管理職を対象とした幅広いコンテンツをご用意しております。
お問い合わせ
コストダウンが利益に直結する術だと理解していても、なかなか前に進めることができない状況。そんな時は、newjiのコストダウン自動化機能で大きく利益貢献しよう!
(β版非公開)