- お役立ち記事
- Pressure Control Technologies in General Machinery: Differences Between Hydraulic and Pneumatic Systems
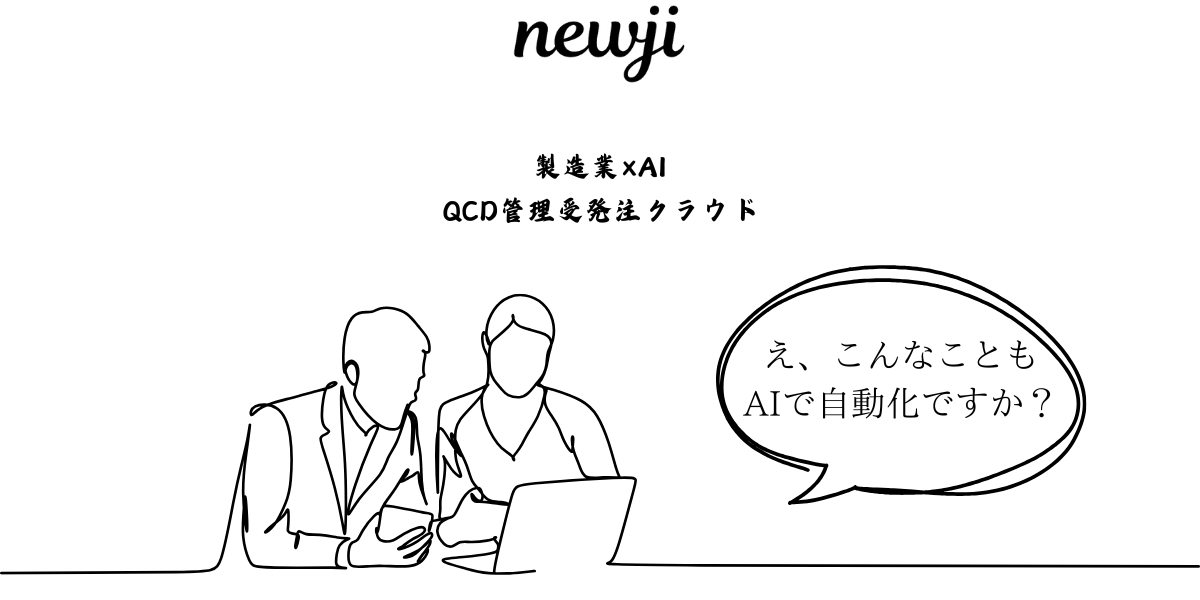
Pressure Control Technologies in General Machinery: Differences Between Hydraulic and Pneumatic Systems
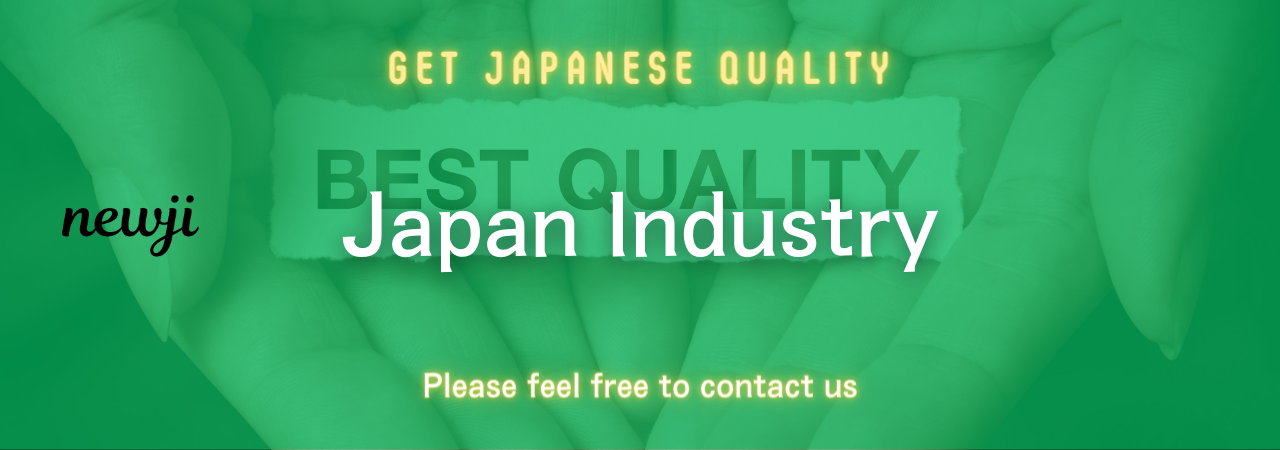
目次
Understanding Pressure Control Technologies
Pressure control technologies play a pivotal role in the operation of general machinery.
These technologies ensure the efficient and precise handling of equipment by managing the flow and pressure of liquids and gases.
Among the most popular pressure control systems used in industrial applications are hydraulic and pneumatic systems.
While they serve similar purposes, each system operates differently, with unique advantages and challenges.
What Are Hydraulic Systems?
Hydraulic systems are based on the principle that liquids, due to their incompressible nature, can be used to transmit power efficiently.
These systems use a pressurized fluid to drive machinery and perform tasks requiring significant force.
The fluid, typically oil, is pumped through hoses to various components, transferring energy to perform work.
Hydraulic systems are favored in situations where powerful, precise movements are necessary.
They are commonly used in construction equipment, such as excavators and cranes, due to their ability to lift heavy loads with great accuracy.
They also play a crucial role in automotive braking systems and industrial machines.
Key Components of Hydraulic Systems
To understand how hydraulic systems function, it’s essential to know about their primary components:
1. **Pump** – The pump pressurizes the hydraulic fluid, sending it through the system.
2. **Valves** – Valves regulate fluid flow and direction, allowing for control over movement.
3. **Actuators** – Actuators, such as cylinders and motors, convert the hydraulic energy into mechanical energy, performing the actual work.
4. **Reservoir** – The reservoir stores the hydraulic fluid when not in use.
5. **Hoses and Seals** – These ensure the system is closed and fluid is contained, preventing leaks.
Advantages of Hydraulic Systems
Hydraulic systems offer several benefits:
– **High Power**: They can exert significant force, making them ideal for heavy-duty applications.
– **Precision**: The control over fluid flow allows for precise movements, crucial for specific industrial and construction tasks.
– **Durability**: When properly maintained, hydraulic systems are robust and can last a long time.
Challenges of Hydraulic Systems
Despite their benefits, hydraulic systems do come with challenges:
– **Maintenance**: Regular maintenance is crucial to prevent leaks and ensure reliable operation.
– **Environmental Concerns**: Spilled hydraulic fluid can be hazardous, necessitating careful handling and environmentally friendly practices.
– **Complexity**: These systems are often more complex and may require specialized knowledge to design, install, and troubleshoot.
What Are Pneumatic Systems?
Pneumatic systems use compressed air or gas to transmit power.
Contrary to hydraulic systems, which use liquids, pneumatic systems rely on compressible gases.
This characteristic provides them with unique applications and benefits.
Pneumatic systems are widely used in factory automation, dental drills, and air brakes in buses and trucks.
Their ability to provide quick, reliable responses makes them invaluable in manufacturing and automated assembly lines.
Key Components of Pneumatic Systems
Here are the primary components of pneumatic systems:
1. **Compressor** – Compressors draw in air and compress it, storing it for use in the system.
2. **Valves** – Valves control the flow and pressure of the air, managing the movement of the actuators.
3. **Actuators** – These could be pneumatic cylinders or motors that convert compressed air into mechanical motion.
4. **Tanks** – Tanks store compressed air for when it’s needed, acting as a buffer for system demands.
5. **Pipes and Fittings** – Pipes and fittings carry air throughout the system, connecting the compressor to the actuators.
Advantages of Pneumatic Systems
Pneumatic systems present various benefits:
– **Speed**: They offer rapid actuation, which is advantageous in systems requiring quick responses.
– **Safety**: Air is not hazardous, eliminating concerns related to fluid leaks.
– **Simplicity**: Generally easier to design and maintain compared to hydraulic systems.
– **Reliability**: Pneumatic systems can operate in a wide range of temperatures and environmental conditions.
Challenges of Pneumatic Systems
Despite their advantages, pneumatic systems have their challenges:
– **Energy Efficiency**: Compressing air requires energy, and the efficiencies of pneumatic systems can be lower compared to their hydraulic counterparts.
– **Limited Power**: Pneumatic systems are not as powerful as hydraulic systems, which makes them less suitable for heavy-duty applications.
– **Control Precision**: Achieving precision and consistency comparable to hydraulic systems can be challenging in pneumatics.
Comparing Hydraulic and Pneumatic Systems
Choosing between hydraulic and pneumatic systems depends heavily on the specific requirements of a project or application.
– **Power and Force**: Hydraulic systems are the go-to choice for tasks needing high force and power.
– **Speed and Response**: Pneumatic systems excel where rapid movements and quick actuation are essential.
– **Maintenance and Complexity**: Hydraulics require more maintenance and can be more complex, whereas pneumatics are simpler and easier to handle.
– **Environmental Impact**: Pneumatic systems are environmentally friendlier due to the absence of liquid leaks.
Conclusion
Pressure control technologies, through hydraulic and pneumatic systems, provide essential solutions for a wide array of industrial applications.
While they share the common purpose of transmitting power, their differences dictate their suitability for various tasks.
Understanding these technologies, their components, advantages, and challenges can help in making informed decisions to optimize machinery performance and ensure operational efficiency.
By analyzing the specific requirements and conditions, businesses can leverage the right system for their needs, driving productivity and innovation in their operations.
資料ダウンロード
QCD調達購買管理クラウド「newji」は、調達購買部門で必要なQCD管理全てを備えた、現場特化型兼クラウド型の今世紀最高の購買管理システムとなります。
ユーザー登録
調達購買業務の効率化だけでなく、システムを導入することで、コスト削減や製品・資材のステータス可視化のほか、属人化していた購買情報の共有化による内部不正防止や統制にも役立ちます。
NEWJI DX
製造業に特化したデジタルトランスフォーメーション(DX)の実現を目指す請負開発型のコンサルティングサービスです。AI、iPaaS、および先端の技術を駆使して、製造プロセスの効率化、業務効率化、チームワーク強化、コスト削減、品質向上を実現します。このサービスは、製造業の課題を深く理解し、それに対する最適なデジタルソリューションを提供することで、企業が持続的な成長とイノベーションを達成できるようサポートします。
オンライン講座
製造業、主に購買・調達部門にお勤めの方々に向けた情報を配信しております。
新任の方やベテランの方、管理職を対象とした幅広いコンテンツをご用意しております。
お問い合わせ
コストダウンが利益に直結する術だと理解していても、なかなか前に進めることができない状況。そんな時は、newjiのコストダウン自動化機能で大きく利益貢献しよう!
(Β版非公開)