- お役立ち記事
- Pressure management technology and efficiency improvement during molding of rubber products [for manufacturing industry]
月間77,185名の
製造業ご担当者様が閲覧しています*
*2025年2月28日現在のGoogle Analyticsのデータより
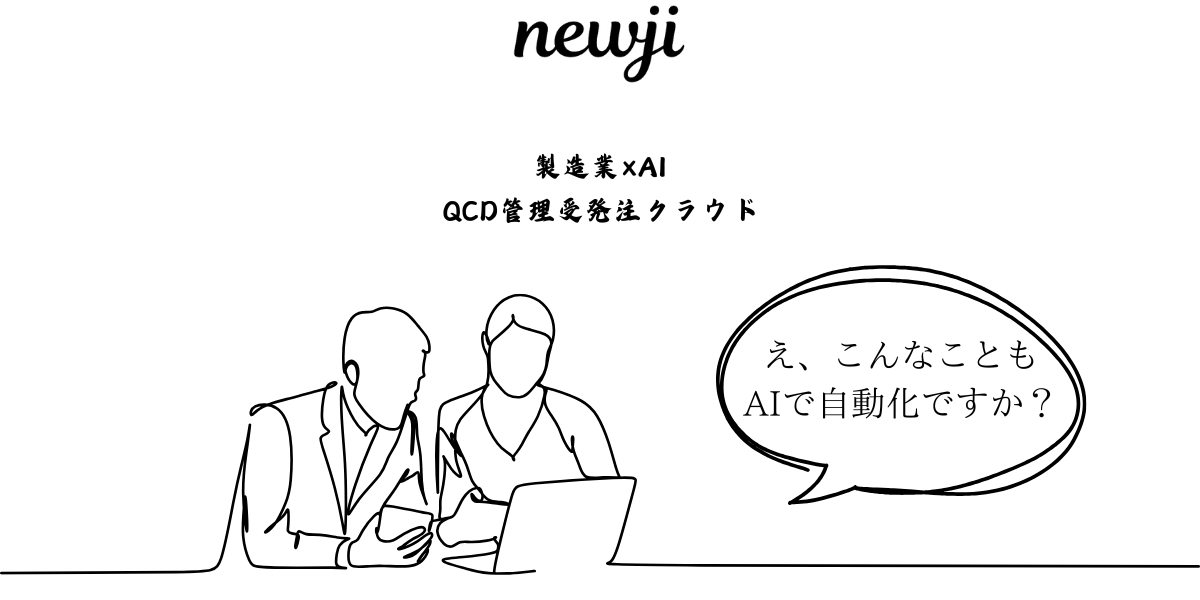
Pressure management technology and efficiency improvement during molding of rubber products [for manufacturing industry]
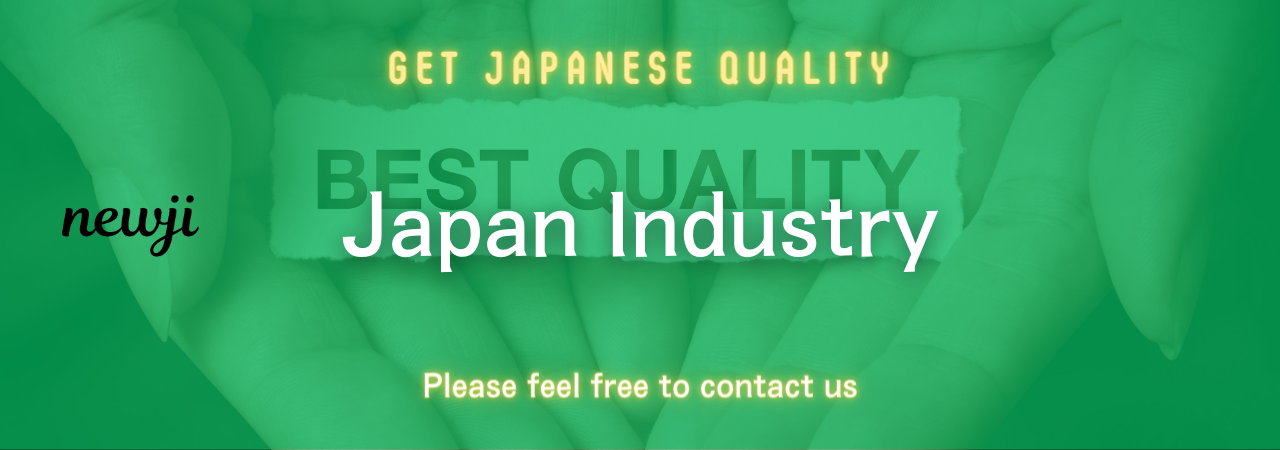
目次
Understanding Pressure Management in Rubber Molding
Molding rubber products is a key process in the manufacturing industry, requiring precision and control to ensure quality and efficiency.
One of the crucial aspects of this process is pressure management.
Proper handling of pressure during the molding process not only guarantees the durability and performance of the rubber products but also enhances production efficiency.
During the molding process, rubber is transformed from raw material into various shapes and designs using molds.
Applying the correct amount of pressure is essential to ensure the rubber fills the mold perfectly, eliminating any voids or defects.
Incorrect pressure can lead to issues such as under-filling, over-filling, or even damage to the mold itself.
To achieve optimal results, understanding the dynamics of pressure management can play a pivotal role in improving both the quality and cost-effectiveness of manufacturing operations.
Importance of Pressure in Rubber Molding
Pressure plays a significant role in determining the outcome of the rubber molding process.
The correct pressure ensures that the rubber material flows well and fills the mold cavity adequately.
Approximately 80-140 psi is usually required for most types of rubber.
However, this can vary based on the type of rubber and the complexity of the mold.
Inadequate pressure may result in incomplete mold filling, leading to products with defects such as air pockets or weak spots.
These defects compromise the integrity and strength of the final product.
Conversely, excessive pressure can cause flash, where material seeps out of the mold, wasting resources and requiring additional trimming labor.
Effective pressure management, therefore, not only improves the quality of molded products but also reduces material waste and operational costs.
Techniques for Pressure Management
Several techniques can be employed to effectively manage pressure during rubber molding.
These techniques ensure that the process remains efficient, minimizing defects and enhancing product quality.
1. Mold Design and Maintenance
A well-designed and maintained mold significantly impacts pressure management.
Proper mold matching and alignment ensure that pressure is evenly distributed, allowing for uniform filling.
Regular maintenance checks and timely repairs can prevent pressure-related issues caused by wear and tear or faulty mold components.
2. Use of Advanced Molding Machines
Modern molding machines come equipped with pressure sensors and controllers, allowing operators to adjust pressure levels accurately.
These machines can maintain consistent pressure throughout the molding cycle, compensating for any variations in material viscosity or other external conditions.
3. Pressure Calibration
Regular calibration of the molding equipment ensures that pressure readings are accurate.
Calibration involves comparing and adjusting equipment to meet industry standards, thus preventing potential deviations that might affect product quality.
4. Use of Pressure Curves
Implementing pressure curves, where the pressure is gradually increased or decreased during the molding cycle, can enhance the process.
This technique helps to optimize material flow and avoid sudden spikes in pressure, which can lead to defects.
Improving Efficiency Through Pressure Management
Improving efficiency in rubber molding is crucial for manufacturers looking to stay competitive.
By focusing on pressure management, businesses can achieve significant productivity gains.
1. Reduction in Scrap Rates
Effective pressure management reduces the likelihood of producing defective products.
This minimizes scrap rates and lowers material costs, contributing to more efficient operations and a healthier bottom line.
2. Enhanced Production Speeds
With the correct pressure settings, the molding cycle time can be optimized, allowing for faster turnaround.
This increase in production speed enables manufacturers to meet higher demand without compromising quality.
3. Energy Savings
Controlled pressure application leads to less strain on machinery, reducing energy consumption.
In the long run, this not only cuts down on utility costs but also extends the lifespan of the equipment.
4. Consistent Product Quality
Achieving a consistent application of pressure results in uniformity across all products, ensuring that each meets quality standards.
This consistency is vital for building strong brand reputation and customer loyalty.
Implementing Technology for Better Pressure Management
Modern technology offers numerous solutions that can enhance pressure management in rubber molding.
1. Automation and Controls
Automation can significantly improve pressure management by standardizing the process.
Automated systems efficiently monitor pressure settings and make real-time adjustments to maintain optimal conditions.
This minimizes human error and enhances overall efficiency.
2. Real-time Monitoring Systems
Implementing real-time monitoring allows manufacturers to oversee the molding process closely.
Advanced sensors and software track pressure levels, providing valuable data that can be used for process improvement and troubleshooting.
3. Data Analytics
Analyzing data collected from the molding process can uncover trends and patterns that inform better pressure management strategies.
Data analytics can help in predicting potential issues and adjusting processes proactively.
Conclusion
Pressure management is a critical aspect of rubber molding that directly influences product quality and manufacturing efficiency.
By employing best practices and leveraging modern technology, manufacturers can ensure that their processes are optimized, leading to reduced waste, faster production times, and enhanced product reliability.
Ultimately, mastering pressure management sets a high standard for excellence in rubber product manufacturing, enabling businesses to thrive in a competitive market.
資料ダウンロード
QCD管理受発注クラウド「newji」は、受発注部門で必要なQCD管理全てを備えた、現場特化型兼クラウド型の今世紀最高の受発注管理システムとなります。
ユーザー登録
受発注業務の効率化だけでなく、システムを導入することで、コスト削減や製品・資材のステータス可視化のほか、属人化していた受発注情報の共有化による内部不正防止や統制にも役立ちます。
NEWJI DX
製造業に特化したデジタルトランスフォーメーション(DX)の実現を目指す請負開発型のコンサルティングサービスです。AI、iPaaS、および先端の技術を駆使して、製造プロセスの効率化、業務効率化、チームワーク強化、コスト削減、品質向上を実現します。このサービスは、製造業の課題を深く理解し、それに対する最適なデジタルソリューションを提供することで、企業が持続的な成長とイノベーションを達成できるようサポートします。
製造業ニュース解説
製造業、主に購買・調達部門にお勤めの方々に向けた情報を配信しております。
新任の方やベテランの方、管理職を対象とした幅広いコンテンツをご用意しております。
お問い合わせ
コストダウンが利益に直結する術だと理解していても、なかなか前に進めることができない状況。そんな時は、newjiのコストダウン自動化機能で大きく利益貢献しよう!
(β版非公開)