- お役立ち記事
- Preventing defective products by establishing a quality inspection system at the time of import Checkpoints that the purchasing department should perform
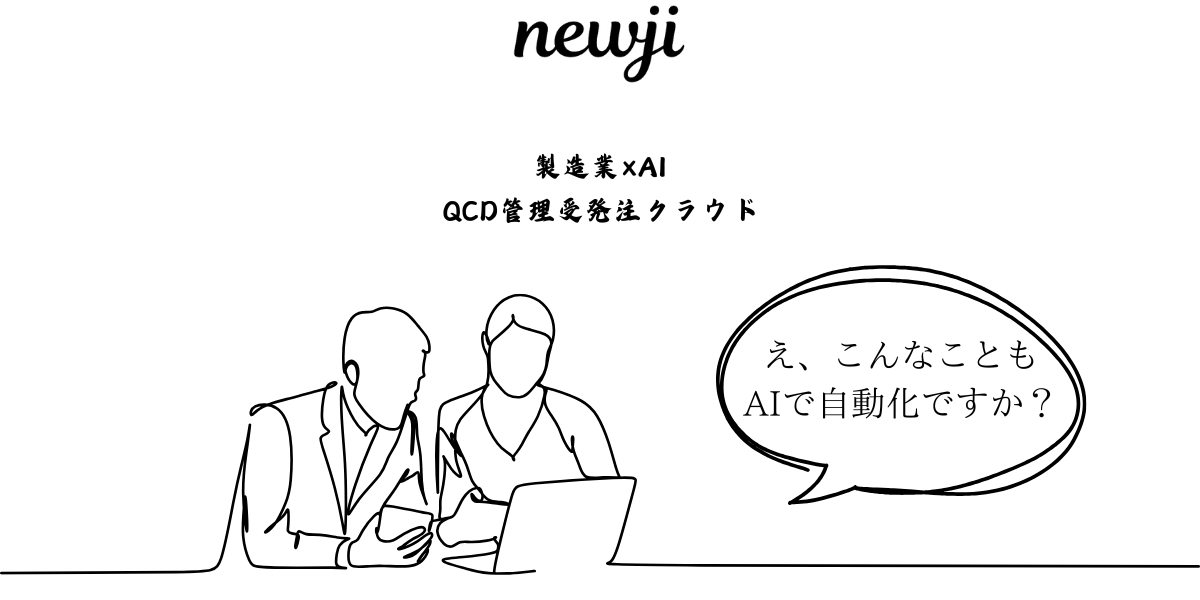
Preventing defective products by establishing a quality inspection system at the time of import Checkpoints that the purchasing department should perform
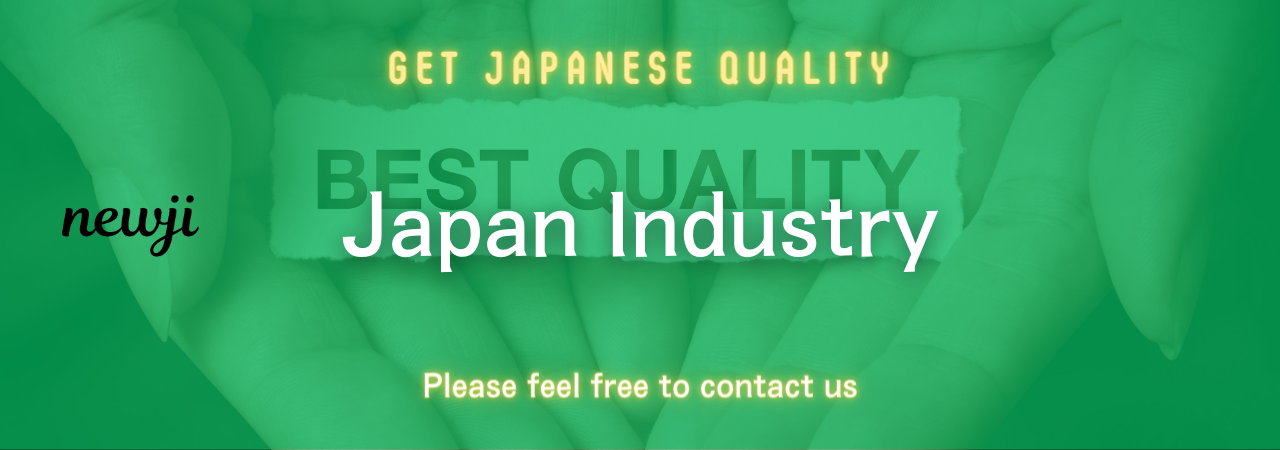
目次
Understanding the Importance of Quality Inspection Systems
In today’s global market, ensuring the quality of imported products is crucial for maintaining brand reputation and customer satisfaction.
A robust quality inspection system can be the line of defense against defective products reaching consumers.
Such systems are particularly vital for the purchasing departments of companies, as they bear the responsibility of acquiring goods that meet the company’s standards.
Establishing a quality inspection system can not only prevent defects but also boost operational efficiency and reduce costs associated with product returns and recalls.
Key Elements of a Quality Inspection System
A well-established quality inspection system must incorporate several key elements to ensure its effectiveness.
These include setting clear standards, conducting thorough inspections, and continuous improvement.
Setting Clear Quality Standards
Before any product is imported, the purchasing department must have well-defined quality standards.
These standards serve as the benchmark against which products will be measured, ensuring consistency and reliability.
Clear quality standards must address various aspects, such as materials used, dimensions, functionality, and safety.
It is essential that these standards align with both international quality norms and the company’s specific requirements.
Conducting Thorough Inspections
The inspection process should be thorough, covering all aspects of the product to identify any potential defects.
Inspections can take place at various stages, such as pre-shipment, during production, and upon arrival.
Pre-shipment inspections help verify that products conform to standards before they leave the supplier.
During production inspections allow for the early detection and correction of defects.
Finally, arrival inspections ensure that products are still within standards after transport.
Continuous Improvement and Feedback Loops
A quality inspection system should not be static.
Continuous improvement is necessary to adapt to changing standards or product requirements.
Feedback loops are essential in this regard; they facilitate communication between different parts of the supply chain.
This communication can lead to improvements in product design, production methods, or inspection techniques.
A proactive approach to quality management will ultimately lead to fewer defects and improved product quality.
Checkpoints for the Purchasing Department
The purchasing department plays a pivotal role in the quality inspection process.
To prevent defective products, they should implement several checkpoints during the procurement process.
Supplier Evaluation and Selection
The first checkpoint is the evaluation and selection of suppliers.
A reliable supplier is the foundation of a quality product.
Purchasing departments must conduct comprehensive assessments of potential suppliers, looking at their production capabilities, reliability, and past performance regarding quality control.
Additionally, establishing long-term relationships with trustworthy suppliers can lead to better communication and improved quality outcomes.
Contractual Agreements and Quality Clauses
Contracts with suppliers should include specific quality clauses that outline the expected standards and consequences of non-compliance.
Such clauses ensure that suppliers are aware of their obligations and provide legal recourse should they fail to meet quality expectations.
Including clauses related to inspections and tests in contracts can also safeguard against defects.
Sample Testing and Prototyping
Before committing to large-scale purchases, the purchasing department should obtain samples or prototypes from the supplier.
Testing these samples can reveal defects that may not be apparent otherwise.
Sample testing allows the purchasing department to evaluate whether the products meet quality standards and address any concerns before full production or shipment commences.
Logistics and Handling Considerations
Defective products are not always due to manufacturing issues; sometimes, they arise from poor logistics and handling.
The purchasing department should work with logistics providers to ensure that products are transported under appropriate conditions.
This includes considering factors such as packaging, storage, and shipping methods to minimize the risk of damage during transit.
Implementing a Feedback Mechanism
Establishing a feedback mechanism with end-users or internal quality teams can provide valuable insights into any issues that arise post-purchase.
This feedback can then be used to address shortcomings in the current inspection process or supplier performance.
A responsive feedback system is an invaluable tool for maintaining and improving quality over time.
The Benefits of a Quality Inspection System
Implementing a comprehensive quality inspection system yields numerous benefits beyond preventing defective products.
Enhanced Customer Satisfaction
The primary benefit is enhanced customer satisfaction.
When customers receive products that meet or exceed their expectations, their trust in the brand increases.
This trust can translate into repeat business, positive reviews, and recommendations, which are invaluable in today’s competitive market.
Cost Reductions
While the initial setup of a quality inspection system might require investment, the cost savings over time can be significant.
By catching defects early in the supply chain, companies can avoid the higher costs associated with product recalls, repairs, or replacements.
Efficient quality control leads to less waste, both in terms of materials and financial resources.
Improved Brand Reputation
Consistently delivering high-quality products enhances brand reputation.
Companies known for their quality are more likely to attract new customers and retain existing ones.
A quality inspection system helps a company stand apart from competitors by demonstrating a commitment to excellence.
Conclusion
Establishing a robust quality inspection system at the time of import is crucial for preventing defective products.
With clear quality standards, thorough inspections, and continuous improvements, companies can mitigate risks and ensure superior product quality.
For the purchasing department, checkpoints such as supplier evaluation, contractual agreements, sample testing, logistics considerations, and feedback mechanisms are critical in the quality inspection process.
Ultimately, a dedication to quality not only protects a company’s bottom line but also builds a foundation for long-term success in the marketplace.
資料ダウンロード
QCD調達購買管理クラウド「newji」は、調達購買部門で必要なQCD管理全てを備えた、現場特化型兼クラウド型の今世紀最高の購買管理システムとなります。
ユーザー登録
調達購買業務の効率化だけでなく、システムを導入することで、コスト削減や製品・資材のステータス可視化のほか、属人化していた購買情報の共有化による内部不正防止や統制にも役立ちます。
NEWJI DX
製造業に特化したデジタルトランスフォーメーション(DX)の実現を目指す請負開発型のコンサルティングサービスです。AI、iPaaS、および先端の技術を駆使して、製造プロセスの効率化、業務効率化、チームワーク強化、コスト削減、品質向上を実現します。このサービスは、製造業の課題を深く理解し、それに対する最適なデジタルソリューションを提供することで、企業が持続的な成長とイノベーションを達成できるようサポートします。
オンライン講座
製造業、主に購買・調達部門にお勤めの方々に向けた情報を配信しております。
新任の方やベテランの方、管理職を対象とした幅広いコンテンツをご用意しております。
お問い合わせ
コストダウンが利益に直結する術だと理解していても、なかなか前に進めることができない状況。そんな時は、newjiのコストダウン自動化機能で大きく利益貢献しよう!
(Β版非公開)