- お役立ち記事
- Preventing Production Issues Through Process Simulation
月間76,176名の
製造業ご担当者様が閲覧しています*
*2025年3月31日現在のGoogle Analyticsのデータより
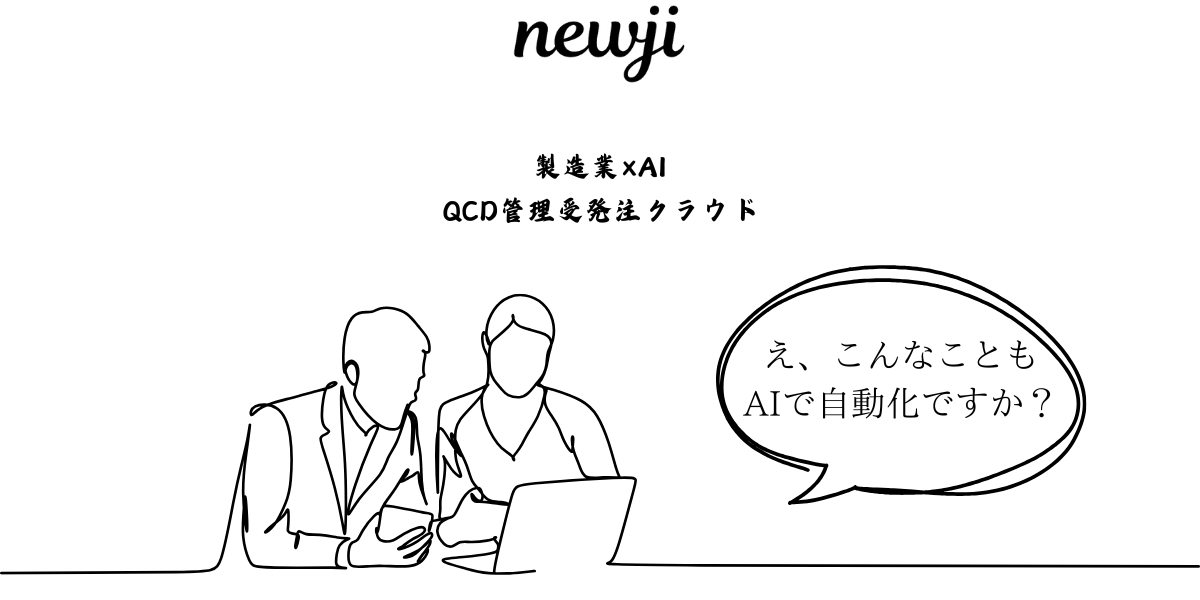
Preventing Production Issues Through Process Simulation
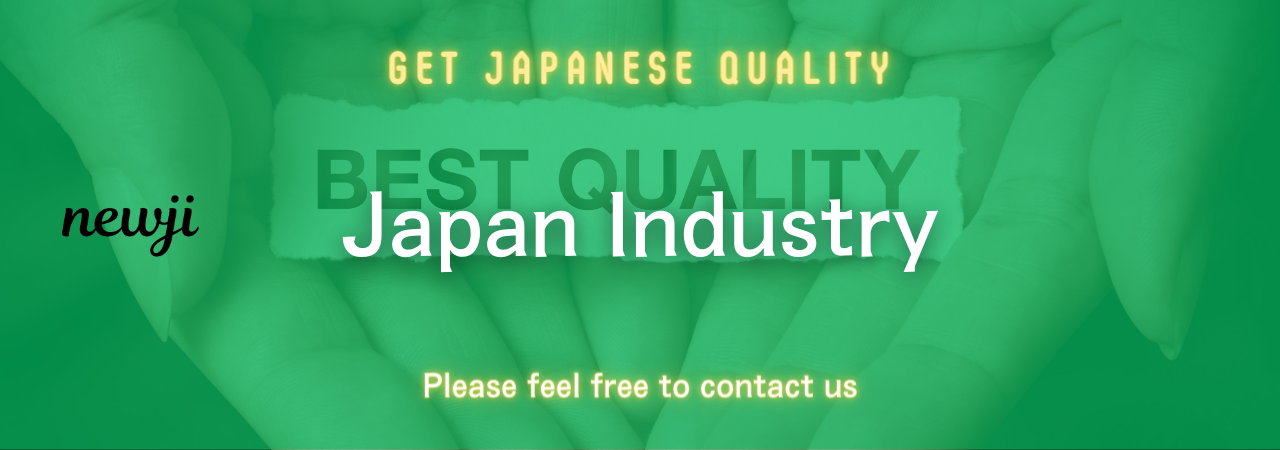
In the competitive world of manufacturing, ensuring the efficiency and reliability of production processes is crucial.
One of the most effective ways to achieve this is through process simulation.
By simulating production scenarios, manufacturers can foresee potential problems and optimize workflows before they even begin.
目次
What is Process Simulation?
Process simulation involves creating a computer-based model of a manufacturing process.
This allows engineers and managers to visualize how different variables interact in a controlled environment.
The model uses mathematical equations and data to replicate real-world processes, allowing for detailed observation and analysis.
Advantages of Process Simulation
Using process simulation provides numerous benefits:
1. **Cost Savings**: By identifying and solving issues in a virtual environment, companies can avoid costly real-world errors.
2. **Efficiency Improvement**: Simulations help find the most efficient pathways and reduce waste.
3. **Time Savings**: Developing physical prototypes and undergoing trial-and-error processes can be time-consuming. Simulation streamlines this by addressing issues beforehand.
4. **Risk Mitigation**: Companies can assess risks and implement necessary changes without any physical danger or loss.
5. **Better Decision Making**: Having detailed data and visual models lead to more informed decisions.
The Role of Process Simulation in Preventing Production Issues
Process simulation serves as a powerful tool for anticipating and preventing production issues.
Identifying Bottlenecks
One of the major advantages of process simulation is its ability to identify bottlenecks.
These are points in the production process where the flow is restricted, leading to delays and inefficiencies.
By pinpointing these bottlenecks, businesses can address them proactively.
Optimizing Resource Allocation
Effective resource allocation is critical for smooth operations.
Simulations help determine the optimal distribution of resources like labor, machinery, and materials.
This ensures that no resources are underutilized or overburdened, leading to a balanced and efficient production line.
Testing Various Scenarios
What would happen if there was an unexpected surge in demand?
How would a new piece of equipment affect the overall process?
With process simulation, different scenarios can be tested without any real-world implications.
This allows companies to prepare for any eventuality.
Reducing Downtime
Unexpected downtime can be costly.
By simulating the production process, maintenance schedules can be optimized to reduce the chances of unforeseen breaks.
This keeps the production line running smoothly and minimizes lost revenue.
Quality Control
Ensuring product quality is essential.
Simulations can analyze the impact of various factors on product quality, helping identify any deviations before they occur.
This results in higher quality outputs and greater customer satisfaction.
Implementing Process Simulation
Understanding the benefits is one thing, but successfully implementing process simulation requires a strategic approach.
Data Collection
The first step is gathering accurate data.
This includes information on all variables involved in the production process, such as machinery specifications, labor input, material properties, and environmental conditions.
The more detailed the data, the more accurate the simulations will be.
Choosing the Right Software
There is a range of process simulation software available, each with its strengths.
Companies need to choose software that best fits their specific needs.
Factors to consider include the complexity of processes, user-friendliness, compatibility with existing systems, and the level of technical support provided.
Building the Model
Once the data is collected and the software is chosen, the next step is building the model.
This involves inputting data to create a virtual representation of the production process.
The model should be as detailed as needed to accurately reflect real-world conditions.
Running Simulations
With the model in place, simulations can begin.
It’s important to run multiple simulations to cover various scenarios and variables.
This can include changes in demand, operational disruptions, new equipment installations, or shifts in labor force.
Analyzing Results
The final step is analyzing the results of the simulations.
This involves looking at the data generated to identify patterns, bottlenecks, inefficiencies, and potential issues.
Based on the analysis, strategic decisions can be made to improve the production process.
Real-World Applications of Process Simulation
Process simulation has a proven track record across various industries.
Automotive Industry
In the automotive industry, simulations help in the design and production of vehicles.
By simulating assembly lines, manufacturers can optimize the production process, leading to faster and more cost-effective manufacturing.
Pharmaceuticals
In pharmaceuticals, process simulation ensures that drugs are produced efficiently while maintaining the highest standards of quality and compliance.
It helps in scaling up from laboratory to full-scale production and in maintaining consistent output.
Food and Beverage
Food and beverage companies use simulations to optimize packaging lines, ingredient mixing processes, and overall production workflows.
This helps in reducing waste and ensuring consistent product quality.
Aerospace
In the aerospace industry, process simulation is crucial for manufacturing high-precision components.
Simulations ensure that the production process meets stringent quality and safety standards.
Future of Process Simulation
As technology advances, the potential for process simulation continues to grow.
With the advent of artificial intelligence and machine learning, simulations are becoming more accurate and predictive.
They can adapt and learn from new data, providing even more valuable insights.
The integration of the Internet of Things (IoT) allows for real-time data collection and analysis, making simulations more dynamic.
This leads to a more responsive and flexible production process.
In summary, process simulation is an invaluable tool for any manufacturing firm.
By anticipating and mitigating potential issues, it ensures efficiency, cost savings, and high-quality outputs.
As the technology continues to evolve, its impact on production processes will only become more profound.
Embracing process simulation today sets the foundation for a more efficient and competitive future.
資料ダウンロード
QCD管理受発注クラウド「newji」は、受発注部門で必要なQCD管理全てを備えた、現場特化型兼クラウド型の今世紀最高の受発注管理システムとなります。
ユーザー登録
受発注業務の効率化だけでなく、システムを導入することで、コスト削減や製品・資材のステータス可視化のほか、属人化していた受発注情報の共有化による内部不正防止や統制にも役立ちます。
NEWJI DX
製造業に特化したデジタルトランスフォーメーション(DX)の実現を目指す請負開発型のコンサルティングサービスです。AI、iPaaS、および先端の技術を駆使して、製造プロセスの効率化、業務効率化、チームワーク強化、コスト削減、品質向上を実現します。このサービスは、製造業の課題を深く理解し、それに対する最適なデジタルソリューションを提供することで、企業が持続的な成長とイノベーションを達成できるようサポートします。
製造業ニュース解説
製造業、主に購買・調達部門にお勤めの方々に向けた情報を配信しております。
新任の方やベテランの方、管理職を対象とした幅広いコンテンツをご用意しております。
お問い合わせ
コストダウンが利益に直結する術だと理解していても、なかなか前に進めることができない状況。そんな時は、newjiのコストダウン自動化機能で大きく利益貢献しよう!
(β版非公開)