- お役立ち記事
- Preventing quality problems and effective usage points using DRBFM
月間76,176名の
製造業ご担当者様が閲覧しています*
*2025年3月31日現在のGoogle Analyticsのデータより
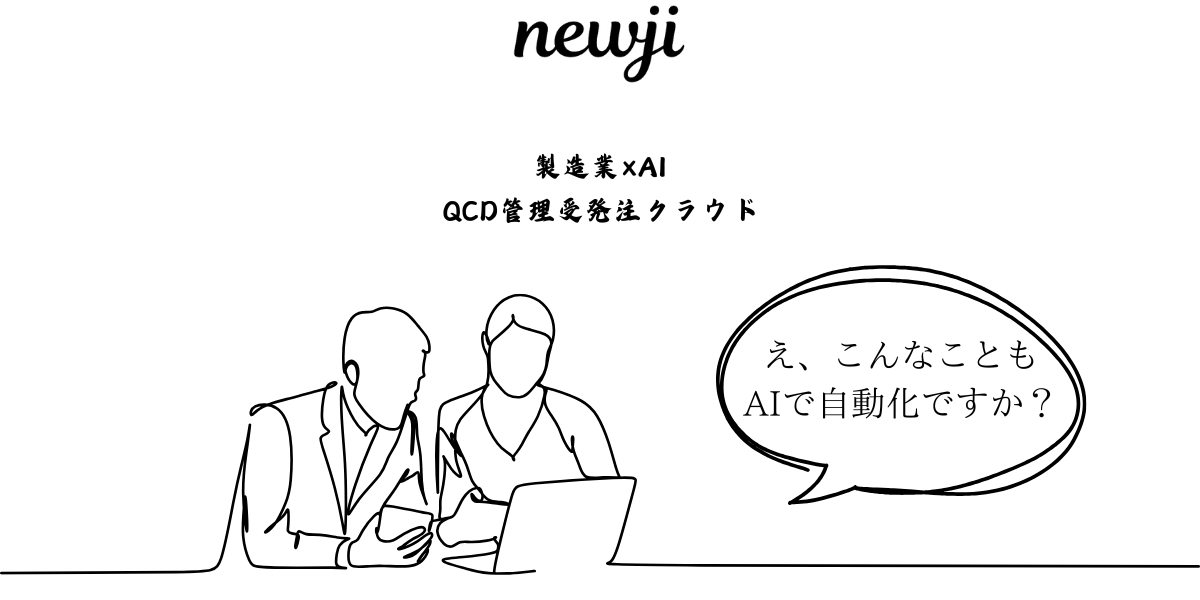
Preventing quality problems and effective usage points using DRBFM
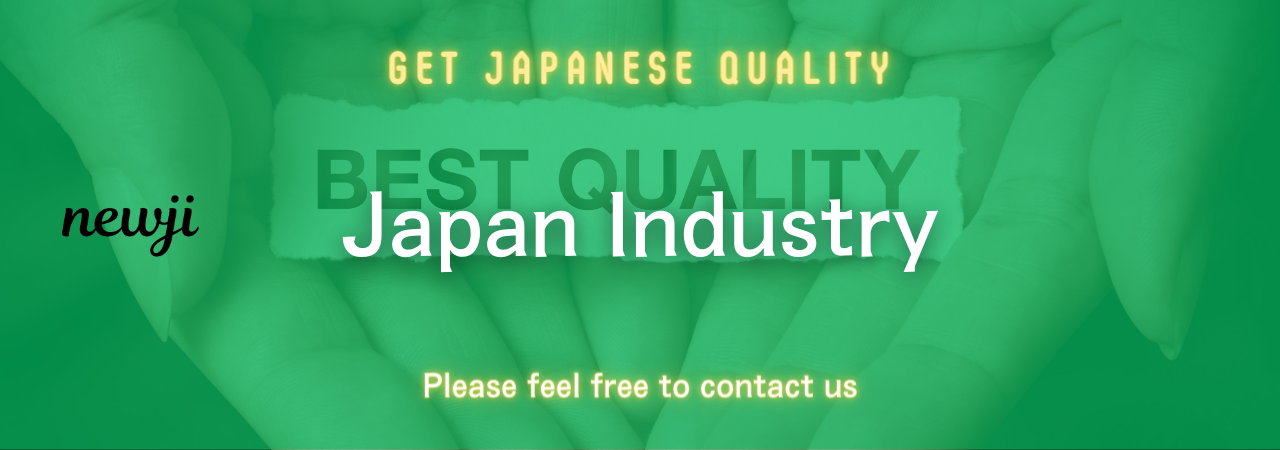
目次
Understanding DRBFM
Design Review Based on Failure Mode (DRBFM) is a structured methodology used in engineering to identify and prevent potential quality problems in the design and development of products.
It emphasizes the importance of focusing on changes or new elements in a design and proactively addressing potential failure modes that could arise.
This approach is crucial for ensuring that quality issues are minimized in the production stage, thus leading to more reliable and efficient products.
The Importance of DRBFM
Quality problems can lead to significant costs, both financially and in terms of brand reputation.
Utilizing DRBFM helps mitigate these risks by embedding quality assurance directly into the design process.
By systematically examining changes in product design, teams are able to foresee and rectify flaws that might not be immediately obvious.
This proactive analysis allows for focused problem solving, reducing the likelihood of defects when the product hits the market.
Key Benefits of DRBFM
1. **Enhanced Product Reliability**: By addressing potential issues early in the design phase, DRBFM enhances the overall reliability of the product.
2. **Cost Savings**: Identifying potential problems early can save significant costs associated with recalls, repairs, and warranty claims.
3. **Improved Design Process**: The structured approach of DRBFM encourages a deeper understanding of design changes, ensuring robust and well-thought-out product designs.
4. **Risk Reduction**: With DRBFM, companies can lower the risk of product failures which might otherwise have been overlooked.
How DRBFM Works
The DRBFM process involves several critical steps.
Each step is designed to systematically guide teams through a thorough review of design changes and their potential impacts.
Identify Changes
The first step in DRBFM is to identify and document all changes made to the existing design.
These changes could be anything from new materials, altered dimensions, or different manufacturing processes.
Understanding these changes is essential as they form the basis for the entire DRBFM process.
Detail Out Possible Failure Modes
Once changes are identified, the next step is to detail potential failure modes associated with these changes.
A failure mode is any way in which the product might fail to meet its intended function.
By brainstorming possible issues, teams can develop a comprehensive list of potential failure modes for further analysis.
Conduct a Thorough Analysis
After detailing potential failure modes, a detailed analysis is conducted.
This involves assessing the severity, frequency, and detectability of each failure mode.
Teams use this information to determine the priority of each potential issue, which helps target resources effectively.
Develop Solutions
Once potential failure modes are prioritized, the next step is to develop solutions to address them.
This might involve design modifications, additional testing, or changes in manufacturing processes.
The aim is to resolve potential issues before they can impact product quality or performance.
Review, Implement, and Monitor
After developing solutions, they are implemented into the design and production process.
The effectiveness of these solutions is then monitored to ensure that they address the identified failure modes efficiently.
Ongoing monitoring helps ensure that no new defects arise and that the product maintains its quality throughout its lifecycle.
Effective Usage of DRBFM
DRBFM is most effective when used systematically and in an environment that promotes collaboration.
Commitment from All Levels
The successful use of DRBFM requires buy-in from all levels of an organization.
From upper management to production floor employees, each party must be committed to the process and its objectives.
Such commitment ensures that the necessary resources and support are available to carry out the reviews effectively.
Cross-Functional Teams
DRBFM should involve cross-functional teams to provide diverse perspectives and expertise.
Including members from design, manufacturing, quality assurance, and other relevant departments ensures that each potential failure mode is thoroughly investigated.
Regular Reviews
Conducting regular reviews is essential for DRBFM to be effective.
Regularly scheduled sessions allow for timely updates and ensure that all team members are on the same page regarding the status of the design and any arising concerns.
Documentation and Communication
Detailed documentation and clear communication are critical.
Documenting all changes, analyses, and solutions provides a reference that can be used for future design efforts and helps ensure continuity in production quality.
Effective communication throughout the project ensures that everyone is aware of their roles and responsibilities, facilitating a smoother implementation of DRBFM outcomes.
Conclusion
DRBFM is a robust and structured approach to improving product quality by identifying and addressing potential failures early in the design process.
By focusing on detailed analysis and proactive problem-solving, DRBFM helps companies save costs, enhance product reliability, and maintain brand reputation.
For the most effective implementation, it’s crucial for organizations to foster a culture of collaboration, commit to regular reviews, and maintain thorough documentation throughout the process.
Embracing DRBFM can lead to higher-quality products and more efficient production processes, benefiting both companies and consumers alike.
資料ダウンロード
QCD管理受発注クラウド「newji」は、受発注部門で必要なQCD管理全てを備えた、現場特化型兼クラウド型の今世紀最高の受発注管理システムとなります。
ユーザー登録
受発注業務の効率化だけでなく、システムを導入することで、コスト削減や製品・資材のステータス可視化のほか、属人化していた受発注情報の共有化による内部不正防止や統制にも役立ちます。
NEWJI DX
製造業に特化したデジタルトランスフォーメーション(DX)の実現を目指す請負開発型のコンサルティングサービスです。AI、iPaaS、および先端の技術を駆使して、製造プロセスの効率化、業務効率化、チームワーク強化、コスト削減、品質向上を実現します。このサービスは、製造業の課題を深く理解し、それに対する最適なデジタルソリューションを提供することで、企業が持続的な成長とイノベーションを達成できるようサポートします。
製造業ニュース解説
製造業、主に購買・調達部門にお勤めの方々に向けた情報を配信しております。
新任の方やベテランの方、管理職を対象とした幅広いコンテンツをご用意しております。
お問い合わせ
コストダウンが利益に直結する術だと理解していても、なかなか前に進めることができない状況。そんな時は、newjiのコストダウン自動化機能で大きく利益貢献しよう!
(β版非公開)