- お役立ち記事
- Preventing quality problems and practical points through DRBFM, past test utilization, and design verification
Preventing quality problems and practical points through DRBFM, past test utilization, and design verification
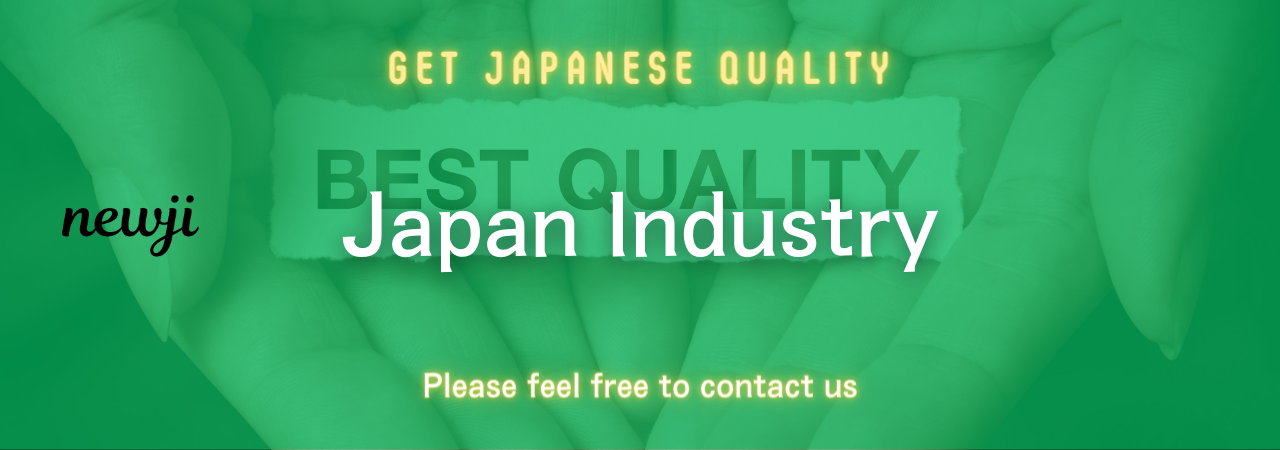
目次
Understanding DRBFM for Quality Assurance
Design Review Based on Failure Mode (DRBFM) is a proven methodology used to minimize quality issues in product development and manufacturing.
It focuses on identifying potential failure modes and addressing them during the design phase.
This proactive approach ensures that products are equipped to meet quality standards and reduce the likelihood of defects.
DRBFM involves a detailed examination of design changes and their impact on product functionality.
By engaging in structured discussions, design teams can uncover weaknesses before they manifest as real-world problems.
Implementing DRBFM requires collaboration across various departments to ensure comprehensive reviews and the successful resolution of potential issues.
The Benefits of DRBFM in Preventing Quality Problems
One of the primary benefits of DRBFM is its ability to enhance product reliability.
By identifying and addressing potential failures early in the design process, companies can avoid costly recalls and enhance customer satisfaction.
This not only improves brand reputation but also reduces the financial burden associated with fixing post-production problems.
Moreover, DRBFM encourages continuous improvement within organizations.
It fosters an environment where team members are motivated to think critically about design changes and their effects, leading to smarter innovation.
This methodological focus drives increased quality, efficiency, and productivity over time.
Leveraging Past Test Data for Improvement
Past test data serves as a crucial resource for preventing quality issues in new product designs.
By analyzing historical data, manufacturers can uncover patterns and insights that guide future projects.
This valuable information helps in anticipating potential problems and implementing effective solutions.
With past test data, teams have access to a wealth of knowledge on how products perform under various conditions.
Identifying stress points, weaknesses, and areas exceeding expectations provides an opportunity to replicate successful elements and improve on shortcomings.
Creating Feedback Loops with Test Data
To make the most of past test data, establishing feedback loops is essential.
These loops involve consistently integrating test findings into the design process.
By ensuring that lessons learned from past experiences inform future projects, companies can cultivate a virtuous cycle of improvement.
Feedback loops also help in aligning the goals of diverse teams.
When engineers, designers, and production staff work with shared insights, they can better coordinate to achieve common quality objectives.
This synergy is pivotal in creating more robust and reliable products.
Design Verification as a Cornerstone of Quality Control
Design verification is a critical phase in the product development process.
It involves rigorous testing to ensure that a design meets all specified requirements and functions as intended.
The goal of design verification is to confirm that a product’s design aligns with its desired performance, safety standards, and regulatory requirements.
By employing design verification, companies can catch design flaws or misalignments before production begins.
This not only saves time and resources but also minimizes the risk of customer dissatisfaction or liability issues stemming from defective products.
Implementing Effective Design Verification Techniques
There are several techniques that companies can employ to ensure robust design verification.
Simulation tools allow designers to model complex scenarios and predict product behavior under various conditions.
This reduces the need for physical prototypes and accelerates the verification process.
Additionally, physical testing remains a vital strategy.
Real-world trials can uncover unanticipated issues that simulations may miss, offering a more comprehensive view of a product’s reliability.
Combining simulations with physical testing creates a balanced approach that maximizes the effectiveness of design verification.
Integrating DRBFM, Past Tests, and Design Verification
To prevent quality problems effectively, integrating DRBFM, past test utilization, and design verification is key.
Each element plays a complementary role in building a robust quality assurance framework.
Applying DRBFM ensures that potential issues are considered early on, while historical test data provides evidence-based insights for design improvements.
Design verification then acts as the final check to validate that the design meets all necessary criteria.
This integrated approach enables organizations to adopt a holistic view of quality assurance.
By focusing on prevention, learning, and validation throughout the design process, companies can substantially reduce the risk of product failures and uphold high quality standards.
Promoting a Culture of Quality
Ultimately, the success of any quality prevention strategy hinges on fostering a culture of quality across all levels of the organization.
Encouraging open communication, continuous learning, and a commitment to excellence ensures that quality considerations are embedded in every decision.
Training and empowering team members to think critically about potential design issues create a proactive mindset.
When quality is ingrained as a core value, it catalyzes innovation and drives sustainable growth.
In conclusion, preventing quality problems requires a multi-faceted approach that combines proven methodologies like DRBFM, the careful analysis of past test data, and meticulous design verification.
Through strategic integration and a focus on fostering a quality-centric culture, companies can meet and exceed customer expectations with reliable, high-quality products.
資料ダウンロード
QCD調達購買管理クラウド「newji」は、調達購買部門で必要なQCD管理全てを備えた、現場特化型兼クラウド型の今世紀最高の購買管理システムとなります。
ユーザー登録
調達購買業務の効率化だけでなく、システムを導入することで、コスト削減や製品・資材のステータス可視化のほか、属人化していた購買情報の共有化による内部不正防止や統制にも役立ちます。
NEWJI DX
製造業に特化したデジタルトランスフォーメーション(DX)の実現を目指す請負開発型のコンサルティングサービスです。AI、iPaaS、および先端の技術を駆使して、製造プロセスの効率化、業務効率化、チームワーク強化、コスト削減、品質向上を実現します。このサービスは、製造業の課題を深く理解し、それに対する最適なデジタルソリューションを提供することで、企業が持続的な成長とイノベーションを達成できるようサポートします。
オンライン講座
製造業、主に購買・調達部門にお勤めの方々に向けた情報を配信しております。
新任の方やベテランの方、管理職を対象とした幅広いコンテンツをご用意しております。
お問い合わせ
コストダウンが利益に直結する術だと理解していても、なかなか前に進めることができない状況。そんな時は、newjiのコストダウン自動化機能で大きく利益貢献しよう!
(Β版非公開)