- お役立ち記事
- Prevention and improvement points of printing process defects in printed electronics and device development applications
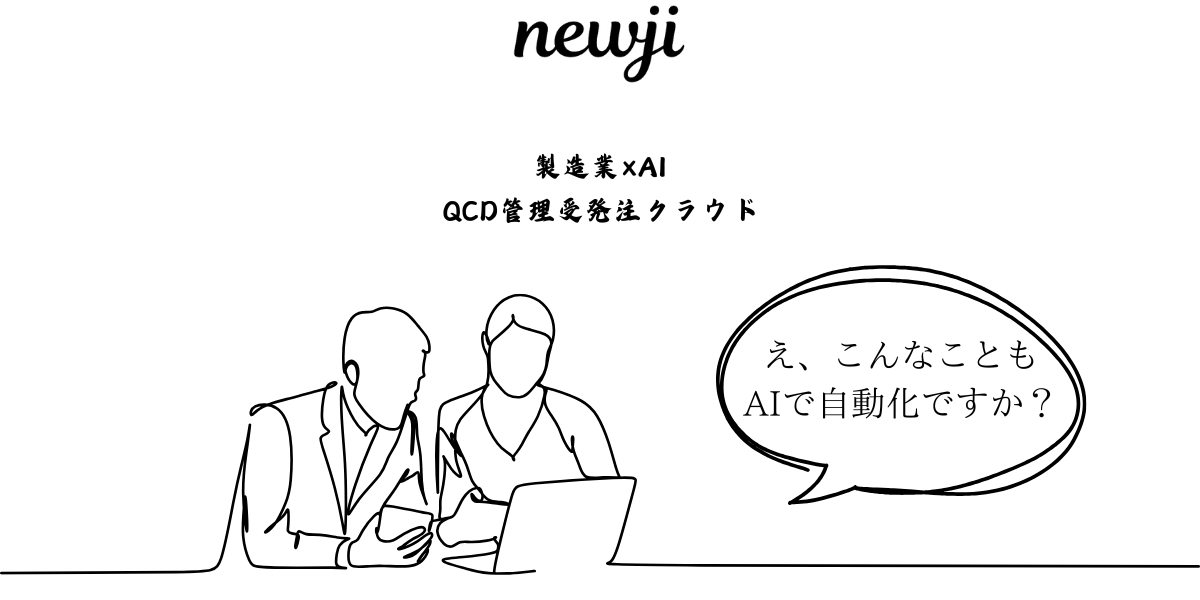
Prevention and improvement points of printing process defects in printed electronics and device development applications
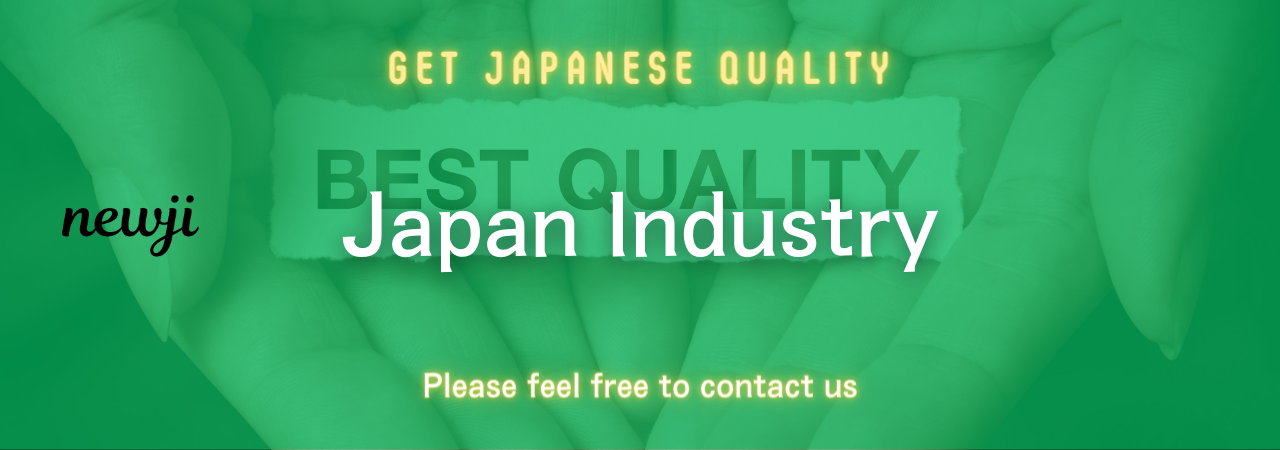
目次
Understanding Printed Electronics
Printed electronics are revolutionizing the way electronic devices are manufactured.
By using advanced printing technologies, it seamlessly integrates components onto flexible substrates, reducing costs and allowing for innovative designs.
While this method offers a myriad of benefits, it also presents challenges, especially in the printing process where defects can occur.
Understanding these defects and knowing how to prevent them is crucial for smoother manufacturing and optimal device performance.
Common Defects in the Printing Process
In the world of printed electronics, there are several common defects that manufacturers might encounter.
The first is conductivity issues.
This occurs when the printed ink fails to conduct electricity as expected.
It can be caused by inadequate curing, improper ink formulation, or uneven printing layers.
Another common defect is delamination.
This is when layers of the printed material start to peel away from each other, potentially compromising the structural integrity of the device.
This can result from poor adhesion between layers or incompatible material choices.
Misalignment is another defect, where patterns do not align as they should.
It’s often due to mechanical errors or inaccurate software settings.
This defect can cause operational problems in the finished device.
Preventing Defects in Printed Electronics
To minimize defects in printed electronics, manufacturers must adopt a proactive approach.
The first step is ensuring optimal material selection.
Materials must be compatible and suitable for the intended application to avoid issues like delamination and conductivity failures.
Testing new materials beforehand can help spot potential problems early on.
Optimizing the printing process itself is equally important.
Regular maintenance of printing equipment ensures high precision and accuracy, reducing the chances of misalignment and uneven layers.
Adjusting machine settings to match the specific requirements of each job can also prevent common errors.
Another key strategy is to implement real-time monitoring during printing.
By keeping a close eye on the process, operators can catch errors as they arise, offering a chance to correct them quickly.
Incorporating automated systems with AI capabilities can greatly enhance defect detection, providing more consistent outcomes.
Role of Quality Control
Quality control is a cornerstone in preventing and identifying defects in printed electronics.
By establishing rigorous testing protocols, manufacturers can ensure each product meets the required standards before progressing to the next stage.
Non-destructive testing methods are particularly beneficial in this field.
Techniques such as X-ray imaging and electrical conductivity tests can detect hidden flaws without damaging the product.
Investing in sophisticated quality control systems is vital for maintaining the integrity and functionality of printed electronic devices.
Improving Device Development Applications
Enhancing device development applications goes hand-in-hand with minimizing defects.
For optimal results, it’s important to foster collaboration between design and manufacturing teams.
This ensures design specifications consider the practicalities and limitations of the printing process, reducing the likelihood of errors during production.
Rapid prototyping is another key area for improvements.
By quickly turning designs into tangible models, manufacturers can test the practicality and functionality of a design before full-scale production.
This step helps identify potential issues early, allowing for adjustments to be made.
Additionally, ongoing education and training for staff involved in printed electronics can make a significant difference.
A well-informed team is more adept at identifying potential defects and suggesting improvements, thereby optimizing the entire process.
Future Trends in Printed Electronics
As technology advances, the field of printed electronics is expected to evolve considerably.
One future trend is the increasing use of nanomaterials, which promise to enhance conductivity and flexibility in devices.
While these materials present new opportunities, they also come with specific handling and processing requirements to avoid defects.
Another forthcoming trend is the integration of IoT (Internet of Things) and smart manufacturing protocols.
These systems offer real-time insights into the manufacturing process, enabling better control and fewer defects.
By embracing these technologies, manufacturers can push the boundaries of printed electronics even further.
Conclusion
The prevention and improvement of defects in printed electronics are essential for the advancement of device development applications.
By focusing on quality control, optimizing material usage, and leveraging cutting-edge technologies, manufacturers can enhance production efficiency and product reliability.
As demand for innovative electronic devices continues to grow, addressing and mitigating defects will remain a central priority for the industry.
With careful attention to detail and a commitment to best practices, the future of printed electronics is bright and full of potential.
資料ダウンロード
QCD調達購買管理クラウド「newji」は、調達購買部門で必要なQCD管理全てを備えた、現場特化型兼クラウド型の今世紀最高の購買管理システムとなります。
ユーザー登録
調達購買業務の効率化だけでなく、システムを導入することで、コスト削減や製品・資材のステータス可視化のほか、属人化していた購買情報の共有化による内部不正防止や統制にも役立ちます。
NEWJI DX
製造業に特化したデジタルトランスフォーメーション(DX)の実現を目指す請負開発型のコンサルティングサービスです。AI、iPaaS、および先端の技術を駆使して、製造プロセスの効率化、業務効率化、チームワーク強化、コスト削減、品質向上を実現します。このサービスは、製造業の課題を深く理解し、それに対する最適なデジタルソリューションを提供することで、企業が持続的な成長とイノベーションを達成できるようサポートします。
オンライン講座
製造業、主に購買・調達部門にお勤めの方々に向けた情報を配信しております。
新任の方やベテランの方、管理職を対象とした幅広いコンテンツをご用意しております。
お問い合わせ
コストダウンが利益に直結する術だと理解していても、なかなか前に進めることができない状況。そんな時は、newjiのコストダウン自動化機能で大きく利益貢献しよう!
(Β版非公開)