- お役立ち記事
- Prevention measures for functionality and safety in product design: Basics of FMEA/FTA and effective practice points
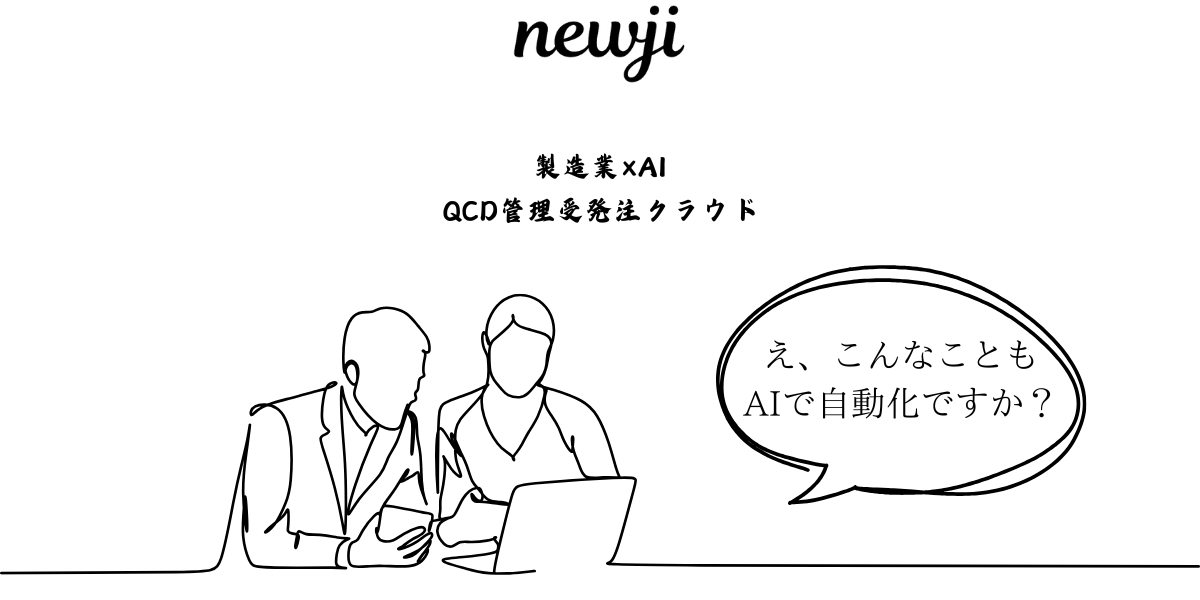
Prevention measures for functionality and safety in product design: Basics of FMEA/FTA and effective practice points
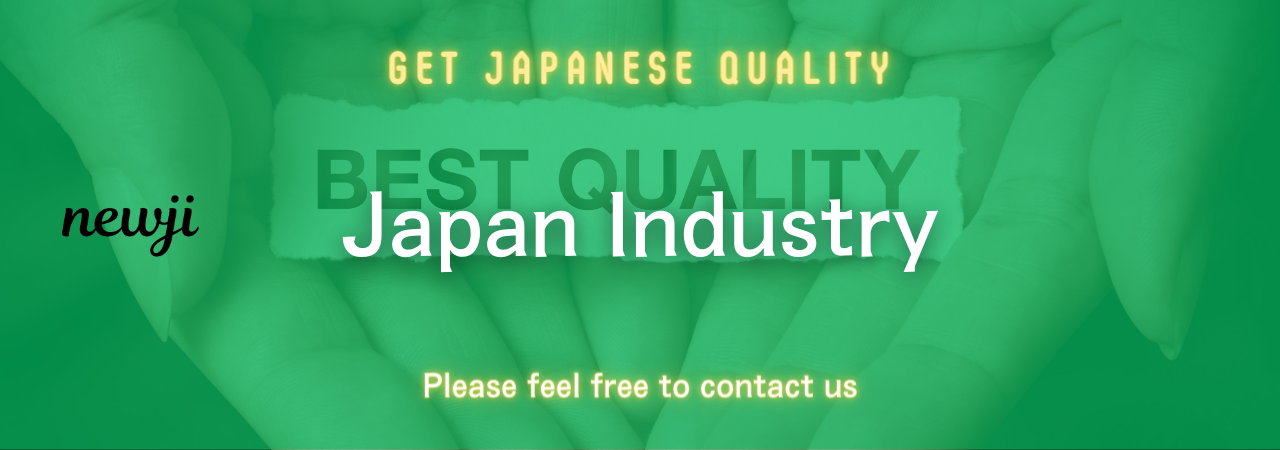
When designing a product, ensuring functionality and safety are critical components that must not be overlooked.
Among the many tools available to designers and engineers, Failure Mode and Effects Analysis (FMEA) and Fault Tree Analysis (FTA) stand out as essential methodologies.
They help identify potential failures and assess their impacts, thereby enhancing product reliability and safety.
This article will delve into the basic concepts of FMEA and FTA, highlight their benefits, and offer practical tips for their effective implementation.
目次
Understanding FMEA: Principles and Process
The Basics of FMEA
Failure Mode and Effects Analysis (FMEA) is a systematic approach to identifying all possible failures in a design, manufacturing, or assembly process.
These failures are evaluated on their severity, potential causes, and the likelihood of occurrence.
Primarily used during the design phase, FMEA helps teams anticipate issues early, saving time and costs associated with later modifications.
How FMEA Works
FMEA involves identifying failure modes, which are ways that a process could fail.
For each failure mode, the possible effects on the end product are analyzed and assessed for severity.
Next, potential causes of each failure are examined, focusing on their likelihood of occurrence and detectability.
Finally, these factors are combined to calculate a Risk Priority Number (RPN), which ranks the risk associated with the failure mode.
Benefits of FMEA
One of the primary benefits of FMEA is the ability to prevent potential failures and mitigate risks before they occur.
This proactive measure aids in the design of more reliable and safe products.
Additionally, FMEA encourages team collaboration, pooling insights from various experts to improve the overall quality and dependability of a product.
Moreover, it assists in compliance with industry standards and customer requirements.
Exploring FTA: A Complementary Approach
Introducing Fault Tree Analysis
Fault Tree Analysis (FTA) is another vital tool for assessing reliability in product design.
Unlike FMEA, which is a bottom-up approach, FTA is a top-down technique.
It focuses on identifying and analyzing the various failure paths that could lead to a system fault, essentially providing a visual representation of the potential causes.
The FTA Process
The FTA process begins by defining the top-level undesired event or system failure.
This event is placed at the top of the fault tree diagram.
The next step involves breaking down this top event into its immediate causes, which are then further divided into more fundamental causes.
Boolean logic gates, such as AND and OR gates, are used to illustrate the relationships between these causes.
Advantages of FTA
Fault Tree Analysis provides a systematic method for identifying root causes of system failures.
By focusing on the logical relationships of failure paths, FTA offers clear visualization that aids in understanding how different failures are interconnected.
This clarity facilitates effective risk management, enabling teams to prioritize corrective actions.
Furthermore, FTA’s structured approach is particularly useful in complex systems where multiple failure sequences might lead to a single fault.
Integrating FMEA and FTA for Optimal Product Design
Complementary Nature of FMEA and FTA
While FMEA and FTA each offer unique perspectives on failure analysis, their integration can yield comprehensive insights into product design reliability.
FMEA’s detailed analysis of each failure mode complements FTA’s holistic view of overall system faults.
Together, they provide a robust framework for understanding and mitigating risks in both component and system levels.
Best Practices for Implementation
To effectively integrate FMEA and FTA, start by assembling a cross-functional team that includes individuals from design, engineering, quality assurance, and manufacturing departments.
Diverse perspectives enhance the completeness of the analysis, uncovering potential issues that may not be apparent from a single vantage point.
Next, clearly define the scope of the analysis.
This involves specifying the purpose, system boundaries, and the detail level required for the analysis.
A well-defined scope ensures that resources are focused and that relevant failure modes and causes are thoroughly examined.
As you conduct FMEA and FTA, maintain detailed documentation of each step taken, including assumptions and justifications.
This record acts as a valuable reference for future analyses and audits.
Lastly, ensure continuous improvement by regularly updating FMEA and FTA.
Product designs evolve, and so should your failure analysis processes.
As new information becomes available or as modifications are made to the product, revisit and revise your analyses to keep them relevant and effective.
Conclusion: Leveraging FMEA and FTA for Safer Products
Incorporating both Failure Mode and Effects Analysis (FMEA) and Fault Tree Analysis (FTA) into your product design process is a critical step towards ensuring functionality and safety.
These methodologies not only help identify potential issues but also guide the design of robust and reliable products.
By employing the practical points discussed, teams can maximize the effectiveness of FMEA and FTA, ultimately leading to safer, high-quality products that meet and exceed stakeholder expectations.
In the competitive market, the ability to preemptively tackle potential safety risks offers a significant edge, enhancing customer trust and brand reputation.
By adopting these analyses proactively, companies can pave the way for innovations that are not only cutting-edge but also secure and dependable.
資料ダウンロード
QCD調達購買管理クラウド「newji」は、調達購買部門で必要なQCD管理全てを備えた、現場特化型兼クラウド型の今世紀最高の購買管理システムとなります。
ユーザー登録
調達購買業務の効率化だけでなく、システムを導入することで、コスト削減や製品・資材のステータス可視化のほか、属人化していた購買情報の共有化による内部不正防止や統制にも役立ちます。
NEWJI DX
製造業に特化したデジタルトランスフォーメーション(DX)の実現を目指す請負開発型のコンサルティングサービスです。AI、iPaaS、および先端の技術を駆使して、製造プロセスの効率化、業務効率化、チームワーク強化、コスト削減、品質向上を実現します。このサービスは、製造業の課題を深く理解し、それに対する最適なデジタルソリューションを提供することで、企業が持続的な成長とイノベーションを達成できるようサポートします。
オンライン講座
製造業、主に購買・調達部門にお勤めの方々に向けた情報を配信しております。
新任の方やベテランの方、管理職を対象とした幅広いコンテンツをご用意しております。
お問い合わせ
コストダウンが利益に直結する術だと理解していても、なかなか前に進めることができない状況。そんな時は、newjiのコストダウン自動化機能で大きく利益貢献しよう!
(Β版非公開)