- お役立ち記事
- Preventive Maintenance in Japanese Manufacturing: Ensuring Efficiency and Longevity
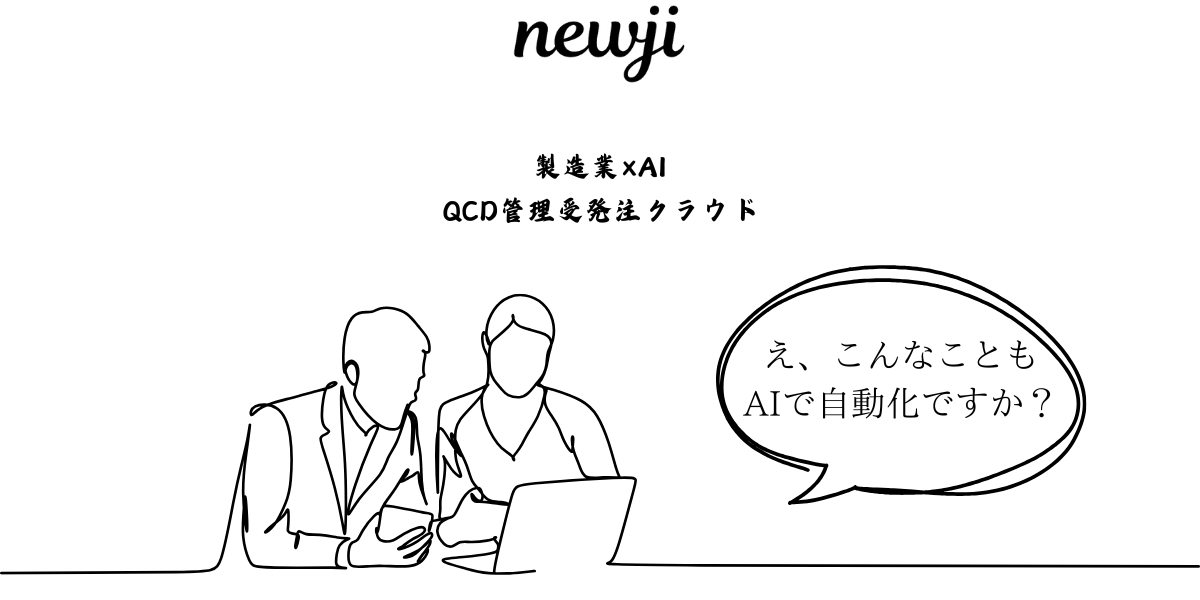
Preventive Maintenance in Japanese Manufacturing: Ensuring Efficiency and Longevity
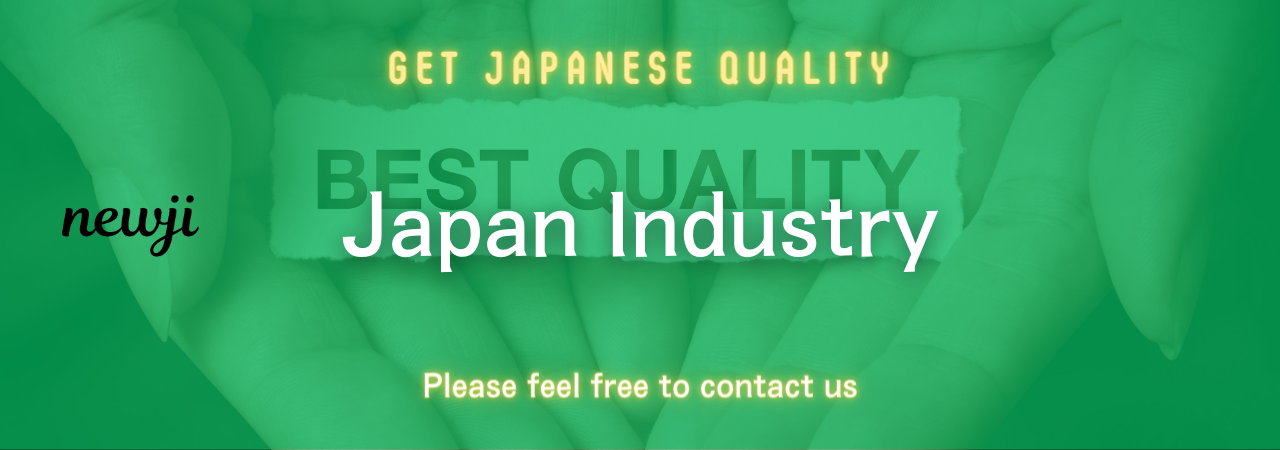
目次
Understanding Preventive Maintenance in Japanese Manufacturing
Preventive maintenance is a proactive approach that aims to ensure machinery and equipment operate efficiently and effectively, minimizing the risk of unexpected breakdowns and maximizing longevity.
This strategy has been a hallmark of Japanese manufacturing, renowned for its focus on quality and operational excellence.
Understanding preventive maintenance within the context of Japanese manufacturing allows companies to adopt best practices and enjoy long-term benefits.
Advantages of Preventive Maintenance
Minimized Downtime
One of the key benefits of preventive maintenance is the significant reduction in machinery downtime.
By regularly inspecting and maintaining equipment, Japanese manufacturers can identify potential issues before they become problematic.
This proactive approach ensures that machinery runs smoothly, minimizing interruptions to production schedules.
Enhanced Equipment Longevity
Preventive maintenance ensures that machinery and equipment are kept in optimal condition.
Regular servicing and replacement of worn-out parts help prevent failures and extend the life of equipment.
Japanese manufacturers often operate with a long-term perspective, understanding that investing in regular maintenance can save significant costs in the long run.
Increased Operational Efficiency
When equipment operates at peak performance, productivity levels improve.
Preventive maintenance helps avoid the inefficiencies caused by machinery breakdowns or suboptimal performance.
This focus on efficiency is integral to the Japanese approach to manufacturing, where continuous improvement and lean production principles are deeply ingrained.
Cost Savings
While preventive maintenance requires an initial investment, it can lead to substantial cost savings over time.
Unexpected equipment failures can result in expensive repairs, production losses, and potential damage to other machinery.
By avoiding these scenarios through proactive maintenance, companies can manage their budgets more effectively.
Safety and Compliance
Regular maintenance ensures that machinery operates safely, reducing the risk of accidents and ensuring compliance with safety regulations.
Japanese manufacturers prioritize workplace safety, recognizing that a safe working environment contributes to overall productivity and employee well-being.
Challenges and Disadvantages
Initial Investment Costs
Implementing a preventive maintenance program requires an initial investment in terms of labor, equipment, and training.
For some companies, especially smaller ones, this can be a significant financial burden.
However, it’s essential to view this as a strategic investment in the long-term health and efficiency of the manufacturing process.
Time-Consuming
Scheduling regular maintenance can be time-consuming and may require temporary production halts.
This can be challenging for companies operating with tight production timelines.
Effective planning and scheduling are crucial to mitigate the impact on production.
Resource Management
Preventive maintenance necessitates proper management of resources, including skilled personnel and spare parts inventory.
Ensuring that these resources are available when needed requires efficient planning and coordination, which can be complex.
Over-Maintenance Risk
There is a possibility of over-maintaining equipment, leading to unnecessary costs and labor.
Finding the right balance between adequate maintenance and over-maintenance is crucial, and this requires careful monitoring and data analysis.
Best Practices for Implementing Preventive Maintenance
Comprehensive Training
Properly training maintenance staff is essential for the success of a preventive maintenance program.
Employees should be equipped with the knowledge and skills to perform inspections, identify issues, and carry out repairs efficiently.
Japanese manufacturers often prioritize continuous training and development to ensure their workforce is well-prepared.
Regular Scheduled Inspections
Establishing a routine schedule for inspections and maintenance tasks is fundamental.
This ensures that potential issues are identified and addressed in a timely manner, preventing unexpected breakdowns.
Utilizing software and digital tools can help streamline scheduling and record-keeping.
Data-Driven Approach
Leveraging data and analytics can significantly enhance preventive maintenance efforts.
By collecting and analyzing data on equipment performance, manufacturers can identify patterns and trends that indicate potential issues.
This allows for more targeted and effective maintenance interventions.
Effective Communication
Effective communication between different departments is critical.
Production, maintenance, and procurement teams must collaborate closely to ensure that maintenance activities are well-coordinated and do not disrupt production schedules.
Clear communication channels help in addressing issues promptly and efficiently.
Utilizing Quality Parts
Using high-quality replacement parts is essential for maintaining equipment performance and longevity.
Japanese manufacturers often have stringent procurement standards, ensuring that spare parts meet rigorous quality criteria.
This minimizes the risk of failures and extends the lifespan of the machinery.
Supplier Negotiation Techniques for Preventive Maintenance
Establish Long-Term Relationships
Building long-term relationships with suppliers can lead to better terms and conditions.
Japanese manufacturers often work closely with their suppliers, fostering robust partnerships that benefit both parties.
This collaborative approach ensures a steady supply of quality parts and services.
Volume Discounts and Bulk Purchases
Negotiating volume discounts and bulk purchase agreements can result in significant cost savings.
Japanese companies often leverage their purchasing power to negotiate favorable terms, ensuring they get the best value for their investment in maintenance supplies.
Benchmarking and Competitive Bidding
Regularly benchmarking supplier performance and engaging in competitive bidding can help ensure that you are getting the best possible deal.
By comparing offers from multiple suppliers, companies can negotiate better prices and terms for maintenance parts and services.
Supplier Performance Metrics
Setting clear performance metrics for suppliers helps ensure that they meet your expectations regarding quality, delivery times, and after-sales support.
Regularly reviewing these metrics allows for ongoing improvement and ensures that suppliers remain reliable partners.
Market Conditions Impacting Preventive Maintenance
Technological Advancements
Advancements in technology, such as the Industrial Internet of Things (IIoT) and predictive analytics, are transforming preventive maintenance.
These technologies allow for real-time monitoring and predictive maintenance, further enhancing efficiency and reducing downtime.
Global Supply Chain Disruptions
Disruptions in global supply chains can impact the availability of spare parts and maintenance supplies.
Japanese manufacturers are known for their resilience and adaptability, often having contingency plans and diversified supply chains to mitigate such risks.
Regulatory Changes
Changes in safety and environmental regulations can impact preventive maintenance practices.
Staying updated with regulatory requirements ensures compliance and helps in planning maintenance activities that meet new standards.
Economic Factors
Economic fluctuations can affect budget allocations for maintenance activities.
During economic downturns, companies may need to balance cost-cutting measures with the necessity of maintaining equipment performance and longevity.
Case Studies: Successful Implementation of Preventive Maintenance in Japanese Manufacturing
Toyota Production System (TPS)
The Toyota Production System (TPS) is a renowned example of effective preventive maintenance.
TPS emphasizes the importance of maintaining equipment to avoid production disruptions and ensure continuous improvement.
By integrating preventive maintenance into their lean manufacturing principles, Toyota has achieved high levels of efficiency and quality.
Hitachi Ltd.
Hitachi Ltd. utilizes predictive maintenance technologies to enhance their maintenance strategies.
By implementing IoT sensors and data analytics, Hitachi can predict equipment failures and schedule maintenance proactively.
This approach has resulted in reduced downtime and improved operational efficiency.
Panasonic Corporation
Panasonic Corporation focuses on comprehensive employee training and development as part of their preventive maintenance strategy.
By investing in their workforce, Panasonic ensures that maintenance tasks are performed accurately and efficiently.
This has led to improved equipment performance and prolonged machinery lifespan.
Conclusion
Preventive maintenance is a critical component of Japanese manufacturing, ensuring efficiency, longevity, and operational excellence.
By adopting best practices, investing in training, leveraging technology, and building strong supplier relationships, companies can achieve significant benefits.
Understanding the advantages and challenges of preventive maintenance allows for informed decision-making and strategic planning.
For companies looking to enhance their preventive maintenance programs, the lessons from Japanese manufacturing provide a valuable blueprint for success.
By embracing a proactive approach, businesses can maximize equipment performance, minimize downtime, and enjoy long-term cost savings.
資料ダウンロード
QCD調達購買管理クラウド「newji」は、調達購買部門で必要なQCD管理全てを備えた、現場特化型兼クラウド型の今世紀最高の購買管理システムとなります。
ユーザー登録
調達購買業務の効率化だけでなく、システムを導入することで、コスト削減や製品・資材のステータス可視化のほか、属人化していた購買情報の共有化による内部不正防止や統制にも役立ちます。
NEWJI DX
製造業に特化したデジタルトランスフォーメーション(DX)の実現を目指す請負開発型のコンサルティングサービスです。AI、iPaaS、および先端の技術を駆使して、製造プロセスの効率化、業務効率化、チームワーク強化、コスト削減、品質向上を実現します。このサービスは、製造業の課題を深く理解し、それに対する最適なデジタルソリューションを提供することで、企業が持続的な成長とイノベーションを達成できるようサポートします。
オンライン講座
製造業、主に購買・調達部門にお勤めの方々に向けた情報を配信しております。
新任の方やベテランの方、管理職を対象とした幅広いコンテンツをご用意しております。
お問い合わせ
コストダウンが利益に直結する術だと理解していても、なかなか前に進めることができない状況。そんな時は、newjiのコストダウン自動化機能で大きく利益貢献しよう!
(Β版非公開)